Garvin Dane Moreno
Mechatronics Engineer at Antigua Distillery Ltd- Claim this Profile
Click to upgrade to our gold package
for the full feature experience.
-
French /Spanish learning Elementary proficiency
-
English Full professional proficiency
Topline Score
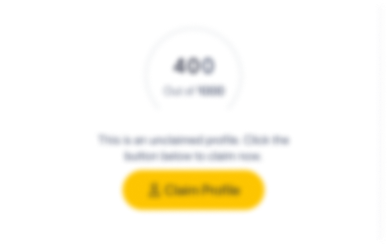
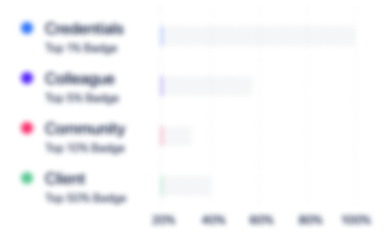
Bio

Anil Maharaj
Letter of Recommendation TO WHOM IT MAY CONCERN: This is to certify that I have known Mr. Garvin Moreno since July 2008 at Coca Cola Trinidad and Tobago, Caribbean Bottlers Trinidad and Tobago Limited and I am pleased to recommend him. I have worked with him in the Maintenance Department. His responsibilities include: 1. Carry out maintenance checks, inspections and repairs on mechanical and electrical equipment required to achieve maintenance work targets. 2. Troubleshoot and rectify mechanical and electrical plant equipment problems in accordance with established standards, specifications and procedures. 3. Install and test mechanical and electrical plant equipment. 4. Diagnose recurring mechanical and electrical system problems, recommend proper corrective action and carry out required repairs. 5. Calibrate process control equipment in accordance with approved specifications. 6. Participate in the design and modification of plant and equipment for the company’s operations. 7. Prepare maintenance reports and records in accordance with approved company procedures. 8. Carry out basic welding functions. 9. Troubleshoot Programmable Logic Control Systems. Garvin is a very enthusiastic worker and has demonstrated great competence in his duties. He is flexible and willing to work on any project that is assigned to him. I am impressed by his organizational skills and he has proven himself to be a very reliable individual. I strongly recommend him for any position in your company. Regards, ………………… Anil Maharaj, Adecco – Celestica Toronto, Cell: 1-416-919-1820.

Don Douglas
Garvin's character is defined by his ability to overcome challenges and reap success through hard work and sheer determination. His skills in machine operation and maintenace are complimented by his great personality. He is a winner and it is my priviledge to recommend him in the field of machine operation and maintenance.

Anil Maharaj
Letter of Recommendation TO WHOM IT MAY CONCERN: This is to certify that I have known Mr. Garvin Moreno since July 2008 at Coca Cola Trinidad and Tobago, Caribbean Bottlers Trinidad and Tobago Limited and I am pleased to recommend him. I have worked with him in the Maintenance Department. His responsibilities include: 1. Carry out maintenance checks, inspections and repairs on mechanical and electrical equipment required to achieve maintenance work targets. 2. Troubleshoot and rectify mechanical and electrical plant equipment problems in accordance with established standards, specifications and procedures. 3. Install and test mechanical and electrical plant equipment. 4. Diagnose recurring mechanical and electrical system problems, recommend proper corrective action and carry out required repairs. 5. Calibrate process control equipment in accordance with approved specifications. 6. Participate in the design and modification of plant and equipment for the company’s operations. 7. Prepare maintenance reports and records in accordance with approved company procedures. 8. Carry out basic welding functions. 9. Troubleshoot Programmable Logic Control Systems. Garvin is a very enthusiastic worker and has demonstrated great competence in his duties. He is flexible and willing to work on any project that is assigned to him. I am impressed by his organizational skills and he has proven himself to be a very reliable individual. I strongly recommend him for any position in your company. Regards, ………………… Anil Maharaj, Adecco – Celestica Toronto, Cell: 1-416-919-1820.

Don Douglas
Garvin's character is defined by his ability to overcome challenges and reap success through hard work and sheer determination. His skills in machine operation and maintenace are complimented by his great personality. He is a winner and it is my priviledge to recommend him in the field of machine operation and maintenance.

Anil Maharaj
Letter of Recommendation TO WHOM IT MAY CONCERN: This is to certify that I have known Mr. Garvin Moreno since July 2008 at Coca Cola Trinidad and Tobago, Caribbean Bottlers Trinidad and Tobago Limited and I am pleased to recommend him. I have worked with him in the Maintenance Department. His responsibilities include: 1. Carry out maintenance checks, inspections and repairs on mechanical and electrical equipment required to achieve maintenance work targets. 2. Troubleshoot and rectify mechanical and electrical plant equipment problems in accordance with established standards, specifications and procedures. 3. Install and test mechanical and electrical plant equipment. 4. Diagnose recurring mechanical and electrical system problems, recommend proper corrective action and carry out required repairs. 5. Calibrate process control equipment in accordance with approved specifications. 6. Participate in the design and modification of plant and equipment for the company’s operations. 7. Prepare maintenance reports and records in accordance with approved company procedures. 8. Carry out basic welding functions. 9. Troubleshoot Programmable Logic Control Systems. Garvin is a very enthusiastic worker and has demonstrated great competence in his duties. He is flexible and willing to work on any project that is assigned to him. I am impressed by his organizational skills and he has proven himself to be a very reliable individual. I strongly recommend him for any position in your company. Regards, ………………… Anil Maharaj, Adecco – Celestica Toronto, Cell: 1-416-919-1820.

Don Douglas
Garvin's character is defined by his ability to overcome challenges and reap success through hard work and sheer determination. His skills in machine operation and maintenace are complimented by his great personality. He is a winner and it is my priviledge to recommend him in the field of machine operation and maintenance.

Anil Maharaj
Letter of Recommendation TO WHOM IT MAY CONCERN: This is to certify that I have known Mr. Garvin Moreno since July 2008 at Coca Cola Trinidad and Tobago, Caribbean Bottlers Trinidad and Tobago Limited and I am pleased to recommend him. I have worked with him in the Maintenance Department. His responsibilities include: 1. Carry out maintenance checks, inspections and repairs on mechanical and electrical equipment required to achieve maintenance work targets. 2. Troubleshoot and rectify mechanical and electrical plant equipment problems in accordance with established standards, specifications and procedures. 3. Install and test mechanical and electrical plant equipment. 4. Diagnose recurring mechanical and electrical system problems, recommend proper corrective action and carry out required repairs. 5. Calibrate process control equipment in accordance with approved specifications. 6. Participate in the design and modification of plant and equipment for the company’s operations. 7. Prepare maintenance reports and records in accordance with approved company procedures. 8. Carry out basic welding functions. 9. Troubleshoot Programmable Logic Control Systems. Garvin is a very enthusiastic worker and has demonstrated great competence in his duties. He is flexible and willing to work on any project that is assigned to him. I am impressed by his organizational skills and he has proven himself to be a very reliable individual. I strongly recommend him for any position in your company. Regards, ………………… Anil Maharaj, Adecco – Celestica Toronto, Cell: 1-416-919-1820.

Don Douglas
Garvin's character is defined by his ability to overcome challenges and reap success through hard work and sheer determination. His skills in machine operation and maintenace are complimented by his great personality. He is a winner and it is my priviledge to recommend him in the field of machine operation and maintenance.

Credentials
-
Q pulse Awareness
The Coca-Cola CompanyMay, 2019- Sep, 2024 -
FIRE MARSHAL
-Sep, 2014- Sep, 2024 -
FIRST AIDER
Red Cross EU OfficeSep, 2014- Sep, 2024 -
Pallet Truck Safety Operations
D.G INSPECTION SERVICES LTDApr, 2018- Sep, 2024 -
Scissors lift
D.G INSPECTION SERVICES LTDApr, 2018- Sep, 2024
Experience
-
Antigua Distillery Ltd
-
Antigua and Barbuda
-
Beverage Manufacturing
-
1 - 100 Employee
-
Mechatronics Engineer
-
Mar 2023 - Present
-
-
-
-
Co-Founder
-
Mar 2019 - Present
-
-
-
-
Blow Moulding/Maintenance Supervisor
-
Aug 2019 - May 2023
All Blow Moulding Equipment and Engineering Work. All Blow Moulding Auxiliary Equipment. Pro-Active Engineering on all Blow Moulding and Auxiliary Equipment. Root Cause Analysis Systems. Instrumental Calibrations. Shift Logs/E-Mails. Blow Moulding Production and Engineering Trends. Equipment and Spare Parts sourcing. Collaborating with Outside Engineers and Suppliers. Standard Engineering Procedures and Practices. Robotics Engineering And… Show more All Blow Moulding Equipment and Engineering Work. All Blow Moulding Auxiliary Equipment. Pro-Active Engineering on all Blow Moulding and Auxiliary Equipment. Root Cause Analysis Systems. Instrumental Calibrations. Shift Logs/E-Mails. Blow Moulding Production and Engineering Trends. Equipment and Spare Parts sourcing. Collaborating with Outside Engineers and Suppliers. Standard Engineering Procedures and Practices. Robotics Engineering And Operation. Supervising of Employees. Blow Moulding Quality Control Monitoring. Projects. Blow Moulding Mechanical Efficiency. Blow Moulding Waste Reports. Preventative Maintenance Tracking system.
-
-
Blow Moulding Engineering Technician/ Assistant Supervisor
-
Nov 2016 - Jul 2019
All Blow Moulding Equipment and Engineering Work. All Blow Moulding Auxiliary Equipment. Pro-Active Engineering on all Blow Moulding and Auxiliary Equipment. Root Cause Analysis Systems. Instrumental Calibrations. Shift Logs/E-Mails. Blow Moulding Production and Engineering Trends. Equipment and Spare Parts sourcing. Collaborating with Outside Engineers and Suppliers. Standard Engineering Procedures and Practices. Robotics Engineering And… Show more All Blow Moulding Equipment and Engineering Work. All Blow Moulding Auxiliary Equipment. Pro-Active Engineering on all Blow Moulding and Auxiliary Equipment. Root Cause Analysis Systems. Instrumental Calibrations. Shift Logs/E-Mails. Blow Moulding Production and Engineering Trends. Equipment and Spare Parts sourcing. Collaborating with Outside Engineers and Suppliers. Standard Engineering Procedures and Practices. Robotics Engineering And Operation. Supervising of Employees. Blow Moulding Quality Control Monitoring. Projects. Blow Moulding Mechanical Efficiency. Blow Moulding Waste Reports. Preventative Maintenance Tracking system.
-
-
-
-
Maintenance Engineer Technician
-
Feb 2016 - Apr 2016
All Plant Equipment and Engineering Work. All Auxiliary Equipment. Pro-Active Engineering on all Plant and Auxiliary Equipment. Root Cause Analysis Systems. Instrumental Calibrations. Work Reports. Production and Engineering Trends. Equipment and Spare Parts sourcing. Collaborating with Outside Engineers and Suppliers. Standard Engineering Procedures and Practices. Robotics Engineering And Operations All Plant Equipment and Engineering Work. All Auxiliary Equipment. Pro-Active Engineering on all Plant and Auxiliary Equipment. Root Cause Analysis Systems. Instrumental Calibrations. Work Reports. Production and Engineering Trends. Equipment and Spare Parts sourcing. Collaborating with Outside Engineers and Suppliers. Standard Engineering Procedures and Practices. Robotics Engineering And Operations
-
-
-
EUROPEAN OAT MILLERS LIMITED
-
United Kingdom
-
Food and Beverage Manufacturing
-
1 - 100 Employee
-
Mill Process Operator
-
May 2015 - Jan 2016
- Inspection and Operation of Flour Grinders - Installation, Inspection and Operation of Sifters - Cleaning and Inspection of Magnets - Inspection and Operation of Screw Conveyors - Installation, Inspection and Operation of Inverters, Diverters and Rotary Seals - Inspection and Operation of Flour Outloading Equipment and Vehicles - Quality Control and Data Input - Preventative Maintenance of Flour Grinding Equipment - Inspection and Operation of Flour Grinders - Installation, Inspection and Operation of Sifters - Cleaning and Inspection of Magnets - Inspection and Operation of Screw Conveyors - Installation, Inspection and Operation of Inverters, Diverters and Rotary Seals - Inspection and Operation of Flour Outloading Equipment and Vehicles - Quality Control and Data Input - Preventative Maintenance of Flour Grinding Equipment
-
-
-
-
Lead Process Operator
-
Jan 2014 - May 2015
• Maintain all machinery operations. • Lead and supervise five (5) other operators in machinery operations. • Lead all technical services with shift engineer. • Assist with all fault finding problems. • Check all Quality logbooks daily. • Assign all cleaning schedules and recycled plastic. • Monitor all recycled materials and equipment. • Support all projects and upgrades within the company (mechanical, electrical, hydraulics and processing). • Assist in all trainee… Show more • Maintain all machinery operations. • Lead and supervise five (5) other operators in machinery operations. • Lead all technical services with shift engineer. • Assist with all fault finding problems. • Check all Quality logbooks daily. • Assign all cleaning schedules and recycled plastic. • Monitor all recycled materials and equipment. • Support all projects and upgrades within the company (mechanical, electrical, hydraulics and processing). • Assist in all trainee development Show less • Maintain all machinery operations. • Lead and supervise five (5) other operators in machinery operations. • Lead all technical services with shift engineer. • Assist with all fault finding problems. • Check all Quality logbooks daily. • Assign all cleaning schedules and recycled plastic. • Monitor all recycled materials and equipment. • Support all projects and upgrades within the company (mechanical, electrical, hydraulics and processing). • Assist in all trainee… Show more • Maintain all machinery operations. • Lead and supervise five (5) other operators in machinery operations. • Lead all technical services with shift engineer. • Assist with all fault finding problems. • Check all Quality logbooks daily. • Assign all cleaning schedules and recycled plastic. • Monitor all recycled materials and equipment. • Support all projects and upgrades within the company (mechanical, electrical, hydraulics and processing). • Assist in all trainee development Show less
-
-
-
-
Blow Moulding Technician
-
Nov 2006 - Feb 2013
Facilitated the production of quality bottles and maintenance of electrical and mechanical machinery Achievements Overhaul of the six main air compressors – Inspect and identify faults in line with procedural duties as required by the lifespan of the equipment. Changed major components of the rotary and screw type compressors. Overhaul of three main air conveyors – Twice yearly, after inspecting equipment using set guidelines for wear and tear, I was required to remove and… Show more Facilitated the production of quality bottles and maintenance of electrical and mechanical machinery Achievements Overhaul of the six main air compressors – Inspect and identify faults in line with procedural duties as required by the lifespan of the equipment. Changed major components of the rotary and screw type compressors. Overhaul of three main air conveyors – Twice yearly, after inspecting equipment using set guidelines for wear and tear, I was required to remove and service all blower motors as well as cleaning and maintenance of all moving parts. Installation of Vision Inspection System for HotFill Preforms – In order to install this major equipment, an air supply and electrical power outlets were installed which required the fabrication of components to give the machinery stability. Liaising, undergoing training from and working with external engineering specialists. Short Cap Conversion – In preparation of changing bottle caps from long caps to short caps, I was required to install new components on Sidel and Krones Blow Moulding machines. Rinser Overhaul – In keeping in line with the ISO 9000 quality management standards, it was a requirement that all rinser equipment was thoroughly inspected for faulty equipment and corrective measures were implemented. Carbonated Soft Drink Beverage Line Machinery Installation – This new line was an expansion of the factory and my role was to aid in the installation of air and water supply and electrical power. Hotfill Non-Carbonated Beverage Line Machinery Installation – Another new line in the expansion of the factory, I was required to participate in the installation of the air, water and electrical supply. Installation of utility equipment – Boilers, air compressors, condensors and cooling towers were some of the machinery that I had to install. Manufacturing of 400ml, 500ml and 1.75 litre bottles from standard preform – A new process had to be developed and tested for each new bottle size. Show less Facilitated the production of quality bottles and maintenance of electrical and mechanical machinery Achievements Overhaul of the six main air compressors – Inspect and identify faults in line with procedural duties as required by the lifespan of the equipment. Changed major components of the rotary and screw type compressors. Overhaul of three main air conveyors – Twice yearly, after inspecting equipment using set guidelines for wear and tear, I was required to remove and… Show more Facilitated the production of quality bottles and maintenance of electrical and mechanical machinery Achievements Overhaul of the six main air compressors – Inspect and identify faults in line with procedural duties as required by the lifespan of the equipment. Changed major components of the rotary and screw type compressors. Overhaul of three main air conveyors – Twice yearly, after inspecting equipment using set guidelines for wear and tear, I was required to remove and service all blower motors as well as cleaning and maintenance of all moving parts. Installation of Vision Inspection System for HotFill Preforms – In order to install this major equipment, an air supply and electrical power outlets were installed which required the fabrication of components to give the machinery stability. Liaising, undergoing training from and working with external engineering specialists. Short Cap Conversion – In preparation of changing bottle caps from long caps to short caps, I was required to install new components on Sidel and Krones Blow Moulding machines. Rinser Overhaul – In keeping in line with the ISO 9000 quality management standards, it was a requirement that all rinser equipment was thoroughly inspected for faulty equipment and corrective measures were implemented. Carbonated Soft Drink Beverage Line Machinery Installation – This new line was an expansion of the factory and my role was to aid in the installation of air and water supply and electrical power. Hotfill Non-Carbonated Beverage Line Machinery Installation – Another new line in the expansion of the factory, I was required to participate in the installation of the air, water and electrical supply. Installation of utility equipment – Boilers, air compressors, condensors and cooling towers were some of the machinery that I had to install. Manufacturing of 400ml, 500ml and 1.75 litre bottles from standard preform – A new process had to be developed and tested for each new bottle size. Show less
-
-
-
-
Blow Moulding Technician
-
Jan 2005 - Oct 2006
General Maintenance and Supervisory Role of New Bottling Department Achievements Installation of Blow Moulder - As part of the new bottling department, one of the main projects was the installation of the main blow moulder and accessories. Silo and Unscrambler Installation – In order to aid the new production line, it was necessary to prepare and install a new silo and unscrambling equipment. Installation of a new rinser and air conveyor – Used my electrical skills… Show more General Maintenance and Supervisory Role of New Bottling Department Achievements Installation of Blow Moulder - As part of the new bottling department, one of the main projects was the installation of the main blow moulder and accessories. Silo and Unscrambler Installation – In order to aid the new production line, it was necessary to prepare and install a new silo and unscrambling equipment. Installation of a new rinser and air conveyor – Used my electrical skills to supply air, water and electrical power to the new equipment. Responsibilities Undertake quality control checks including size, thickness, height and weight of each bottle made. Attending and repairing breakdowns on machines and equipment. Palletizing bottles, and transporting preforms using forklift equipment. Daily inspections of equipment and writing reports based on findings. Checking and calibrating instruments and machines. Completing tool surface cleaning and tool scrape downs. Forward planning of resource requirements. All general maintenance of blow moulding equipment. Show less General Maintenance and Supervisory Role of New Bottling Department Achievements Installation of Blow Moulder - As part of the new bottling department, one of the main projects was the installation of the main blow moulder and accessories. Silo and Unscrambler Installation – In order to aid the new production line, it was necessary to prepare and install a new silo and unscrambling equipment. Installation of a new rinser and air conveyor – Used my electrical skills… Show more General Maintenance and Supervisory Role of New Bottling Department Achievements Installation of Blow Moulder - As part of the new bottling department, one of the main projects was the installation of the main blow moulder and accessories. Silo and Unscrambler Installation – In order to aid the new production line, it was necessary to prepare and install a new silo and unscrambling equipment. Installation of a new rinser and air conveyor – Used my electrical skills to supply air, water and electrical power to the new equipment. Responsibilities Undertake quality control checks including size, thickness, height and weight of each bottle made. Attending and repairing breakdowns on machines and equipment. Palletizing bottles, and transporting preforms using forklift equipment. Daily inspections of equipment and writing reports based on findings. Checking and calibrating instruments and machines. Completing tool surface cleaning and tool scrape downs. Forward planning of resource requirements. All general maintenance of blow moulding equipment. Show less
-
-
-
-
Maintenance Technician
-
Nov 1998 - Jan 2005
Ensuring the efficient running of production lines and while maintaining and monitoring site Health and Safety practices Achievements Changeover of Quality Control Pipes in the Quality Control department – Based on inspection findings, faulty pipes needed to be changed. In order for this to be done, the process of fabricating, threading and welding had to be performed. Boiler Installation – As part of maintaining equipment to the highest standards, a new boiler was added to… Show more Ensuring the efficient running of production lines and while maintaining and monitoring site Health and Safety practices Achievements Changeover of Quality Control Pipes in the Quality Control department – Based on inspection findings, faulty pipes needed to be changed. In order for this to be done, the process of fabricating, threading and welding had to be performed. Boiler Installation – As part of maintaining equipment to the highest standards, a new boiler was added to the boiler system. This required new pipes to be run and a new water and electrical power supply installed. Air Compressor overhaul – the disassembly and re-assembly of new components with the consultation of external engineers. Responsibilities Welding and plumbing of pipes and sheet metal to facilitate various projects. Identifying and solving problems on all equipment including boilers, compressors, pumps, motors etc. Weekly checks on production equipment which resulted in the changing of bearings, seals, filters and other major components. Preparing and writing up of daily breakdown, loss of time and resource usage reports. Show less Ensuring the efficient running of production lines and while maintaining and monitoring site Health and Safety practices Achievements Changeover of Quality Control Pipes in the Quality Control department – Based on inspection findings, faulty pipes needed to be changed. In order for this to be done, the process of fabricating, threading and welding had to be performed. Boiler Installation – As part of maintaining equipment to the highest standards, a new boiler was added to… Show more Ensuring the efficient running of production lines and while maintaining and monitoring site Health and Safety practices Achievements Changeover of Quality Control Pipes in the Quality Control department – Based on inspection findings, faulty pipes needed to be changed. In order for this to be done, the process of fabricating, threading and welding had to be performed. Boiler Installation – As part of maintaining equipment to the highest standards, a new boiler was added to the boiler system. This required new pipes to be run and a new water and electrical power supply installed. Air Compressor overhaul – the disassembly and re-assembly of new components with the consultation of external engineers. Responsibilities Welding and plumbing of pipes and sheet metal to facilitate various projects. Identifying and solving problems on all equipment including boilers, compressors, pumps, motors etc. Weekly checks on production equipment which resulted in the changing of bearings, seals, filters and other major components. Preparing and writing up of daily breakdown, loss of time and resource usage reports. Show less
-
-
-
-
Trainee Electrical Technician
-
Nov 1997 - Nov 1998
Assisting in the installation and testing of electrical equipment Responsibilities Assisting in the installation and electrical testing of transformers, lights, switches and plugs etc. Electrical meter reading and troubleshooting. Preparation of daily reports on materials used. Wiring and conduit laying of commercial and industrial buildings. Assisting in the installation and testing of electrical equipment Responsibilities Assisting in the installation and electrical testing of transformers, lights, switches and plugs etc. Electrical meter reading and troubleshooting. Preparation of daily reports on materials used. Wiring and conduit laying of commercial and industrial buildings.
-
-
-
Tracmac Engineering Limited
-
Trinidad and Tobago
-
Industrial Machinery Manufacturing
-
Trainee Maintenance Technician
-
Nov 1996 - Nov 1997
Assisting in the repairs and maintenance of on and off site company equipment Responsibilities Repairing forklifts, compressors, cranes, tractors etc. Oil and filter changes. Gasket, seal making and changes. Assisting in identifying and repairing equipment off site. Assisting in the repairs and maintenance of on and off site company equipment Responsibilities Repairing forklifts, compressors, cranes, tractors etc. Oil and filter changes. Gasket, seal making and changes. Assisting in identifying and repairing equipment off site.
-
-
Education
-
University of London
Bachelor's degree, Operations Management and Supervision -
University of London
Bachelor of Applied Science - BASc, Engineering/Industrial Management -
EDEXCEL BTEC LEVEL 3
Dilpoma, Mechanical Engineering -
School of Computer and Business Science
Certificate in Project Management for Business Professionals, Project Management -
Metal Industries Company Limited
Certificate, Mechanical, Electrical/Electronics Technology, Welding and Industrial Maintenance Trades. -
toco composite
Mechanical Engineering Related Technologies/Technicians
Community
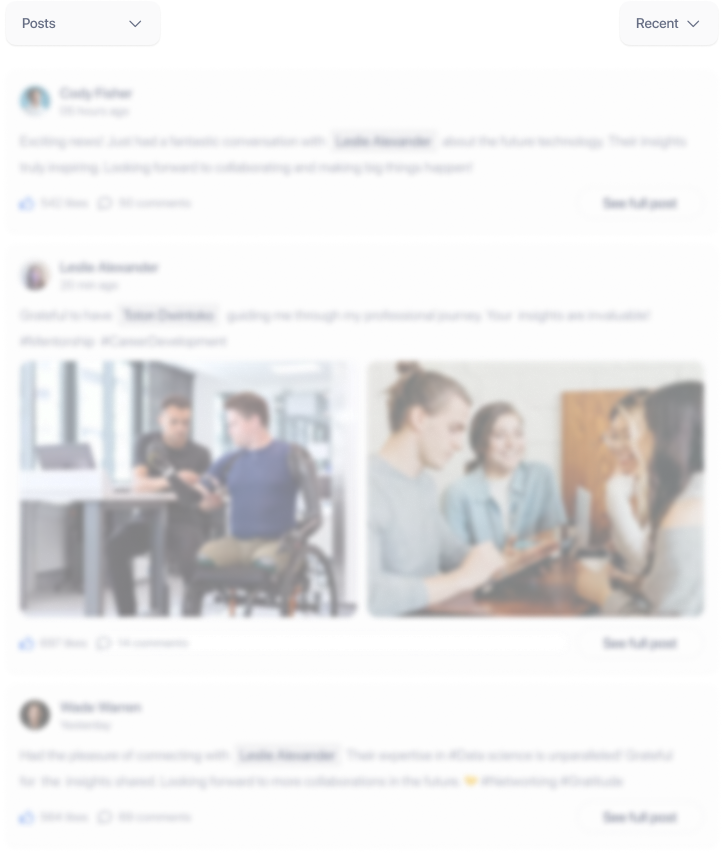