Garrett T.
Management Representative / Engineer at Dallas Avionics, Inc- Claim this Profile
Click to upgrade to our gold package
for the full feature experience.
-
English -
Topline Score
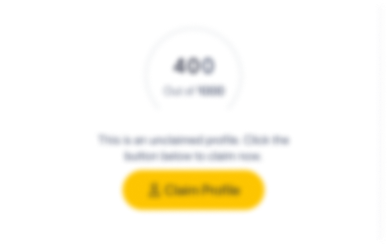
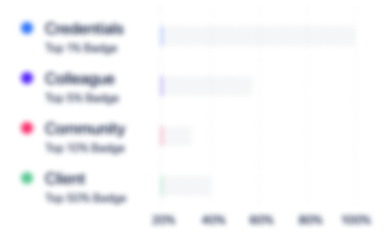
Bio

Jennifer Piazza
I had the pleasure of meeting Garrett Tuck in person recently at Dallas Avionics after their very successful certification audits for AS 9100. Garrett exemplifies what it means to comprehend and identify a company’s system requirements and organize them in a practical and straightforward structure. This leads to efficiency and ease of quality management for the work team, auditors and customer care. Garrett is always professional, and very personable, as well. He believes in customer service, and everyone is his customer. He practices continual improvement and added value through his leadership. I recommend Garrett for the design and implementation of any Quality Management System. Garrett is solution-oriented and his credentials speak for themselves.

David Lang
I worked with Gary for several years at Howell and on a number of projects for both military and commercial. He was always professional and willing to go that extra bit to insure that we produced the best possible product. Gary’s commitment to quality and customer satisfaction would be a great addition to any team.

Jennifer Piazza
I had the pleasure of meeting Garrett Tuck in person recently at Dallas Avionics after their very successful certification audits for AS 9100. Garrett exemplifies what it means to comprehend and identify a company’s system requirements and organize them in a practical and straightforward structure. This leads to efficiency and ease of quality management for the work team, auditors and customer care. Garrett is always professional, and very personable, as well. He believes in customer service, and everyone is his customer. He practices continual improvement and added value through his leadership. I recommend Garrett for the design and implementation of any Quality Management System. Garrett is solution-oriented and his credentials speak for themselves.

David Lang
I worked with Gary for several years at Howell and on a number of projects for both military and commercial. He was always professional and willing to go that extra bit to insure that we produced the best possible product. Gary’s commitment to quality and customer satisfaction would be a great addition to any team.

Jennifer Piazza
I had the pleasure of meeting Garrett Tuck in person recently at Dallas Avionics after their very successful certification audits for AS 9100. Garrett exemplifies what it means to comprehend and identify a company’s system requirements and organize them in a practical and straightforward structure. This leads to efficiency and ease of quality management for the work team, auditors and customer care. Garrett is always professional, and very personable, as well. He believes in customer service, and everyone is his customer. He practices continual improvement and added value through his leadership. I recommend Garrett for the design and implementation of any Quality Management System. Garrett is solution-oriented and his credentials speak for themselves.

David Lang
I worked with Gary for several years at Howell and on a number of projects for both military and commercial. He was always professional and willing to go that extra bit to insure that we produced the best possible product. Gary’s commitment to quality and customer satisfaction would be a great addition to any team.

Jennifer Piazza
I had the pleasure of meeting Garrett Tuck in person recently at Dallas Avionics after their very successful certification audits for AS 9100. Garrett exemplifies what it means to comprehend and identify a company’s system requirements and organize them in a practical and straightforward structure. This leads to efficiency and ease of quality management for the work team, auditors and customer care. Garrett is always professional, and very personable, as well. He believes in customer service, and everyone is his customer. He practices continual improvement and added value through his leadership. I recommend Garrett for the design and implementation of any Quality Management System. Garrett is solution-oriented and his credentials speak for themselves.

David Lang
I worked with Gary for several years at Howell and on a number of projects for both military and commercial. He was always professional and willing to go that extra bit to insure that we produced the best possible product. Gary’s commitment to quality and customer satisfaction would be a great addition to any team.

Credentials
-
AS9100 Rev D & ISO 9001:2015 Lead Auditor
Axeon.netJan, 2019- Nov, 2024 -
Certified Lead Auditor - AS9100:2009
AQS Management Systems, Inc.
Experience
-
Dallas Avionics, Inc
-
United States
-
Airlines and Aviation
-
1 - 100 Employee
-
Management Representative / Engineer
-
May 2014 - Present
I have many years experience as Director of Quality Assurance and Quality Assurance Manager. Currently I am the Management Representative at Dallas Avionics, Inc. I implemented AS9100 Rev C and Revision of AS9100 Rev D system at Dallas Avionics, Inc. I am very proud to say that our initial certification audit passed and we received a rating of 4 on all our PEARs and zero findings. No Minors and no Majors. Keep in mind that this was our Initial Certification Audit which is very rare for the initial certification. Dallas Avionics is a full service Aviation Parts Distributor. They are your One Stop Shop for Avionics parts. Dallas Avionics sells Avionics and Aviation approved Equipment and their two sister companies (Radio Masters and Cal Labs) can calibrate your equipment and as an FAA approved Repair Station, they can repair your equipment. True One Stop Shopping. I manage the Quality Management System including – AS9100 Rev C, Root Cause / Corrective Action, Preventive Actions, Continuous Improvements, Calibration program, Management Review, Turtle Diagrams, Forms, Documents, Procedures, charts - graphs, First Articles and the Management Review process, Customer feedback, key characteristics and a Quality Policy / Quality Objectives easy to read, understand and apply relationship chart. I have over 20 years of experience in certified Quality Management Systems beginning with: ISO 9001, 9002, 9003 thru today’s requirements ISO 9001:2015 / AS9100 Rev D and AS9120 for distributors. FAA MIDO, FSDO, DMIR, Repairman, PMA, TSO, STCs, and management of all applicable CFRs. I am also a AS9100 / ISO 9001 Lead Auditor. I am available to assist your company with any AS9100 or ISO issue you might have. Consulting includes assisting in getting your suspended certification lifted and re-instated, correction of any NCRs, training on any AS9100 / ISO subjects / concerns, GAP audits and Internal Auditing as a 3rd party. AS9100, AS9120 or ISO 9001.
-
-
-
Essner Manufacturing
-
United States
-
Aviation and Aerospace Component Manufacturing
-
1 - 100 Employee
-
Quality Assurance Manager
-
Nov 2012 - May 2014
Essner Manufacturing is a full sheet metal and CNC machining manufacturing company, NADCAP certified in heat treat and welding and small to mid-sized assemblies. Essner is an AS9100 certified company. As Quality Manager I have a multitude of duties which include management of: AS9100 Rev C., tool calibration, root cause - corrective action, quality escapes, customer complaints, dimensional inspection, in-process inspection, final inspection, AS9102 first article management, planning review and approval, and a host of other duties as assigned by company President. Experience with LEAN manufacturing, 5-S projects, Standard Work, Fishbone, 5-Whys, FMEA for production and design, FMEA for risk management. Customers I have worked with include Boeing, Bell Helicopter, Cobham Avionics, Lockheed Martin, Triumph-Vought, Cessna, Airbus, GKN, American Eurocopter, Sikorsky, Goodrich, L-3 and a host of others too numerous to mention them all. FAA, MIDO, FSDO, DMIR, TSO, PMA, STC, Certification, Repair Station, and Repairman cert. I work with all levels of management, promote a partnership relations management style, and always strive to make your flying experience safe.
-
-
-
Luminator Technology Group
-
United States
-
Appliances, Electrical, and Electronics Manufacturing
-
300 - 400 Employee
-
Director of Quality Assurance
-
May 2010 - Oct 2012
Manage and coordinate activities with Engineering, Operations, Purchasing, Sales & Marketing, Customer Service, and Quality Assurance in the Aircraft division, Bus division, and the Rail division. FAA, PMA, MIDO, and FSDO operations. Directly supervise Five (5) Quality Managers, (4) Quality Engineers, Quality Assurance Inspectors, Quality Specialist, and Quality Control activities. Maintains positive relationships with customers, vendors, and in-house personnel to promote understanding and open communication to provide the groundwork for a total quality environment based on ISO 9001 : 2008, AS9100 Rev C. Experience with LEAN manufacturing, 5-S projects, Standard Work, Fishbone, 5-Whys, FMEA for production and design, FMEA for risk management. Excellent 10,000 foot director that has the ability and knowledge to work in the trenches when necessary. Experience spans customers like: US Government, Boeing Aircraft Company, Lockheed Martin, DART Rail, Kawasaki Rail Car builders, and a host or others to numerous to mention them all. Very strong management skills, problem solving skills, root cause analysis skills, team player and partnership attitude, with ability to provide leadership and sound judgment in crisis and conflict resolution. As Director of Quality Assurance I am accountable to the President/CEO of Luminator.
-
-
-
S-TEC Corporation
-
Airlines and Aviation
-
1 - 100 Employee
-
Director of Quality Assurance
-
Aug 2007 - May 2010
Management of quality assurance activities including; FAA MIDO, FAA FSDO, TSO, PMA, STC, AS9100 certified quality management system, AS9100 audit manager, incoming inspection, in-process inspection, final inspection, material review board, supplier management, corrective action, preventive action (both using the 8D format), tool calibration, contract review, process/procedure writing and approval. Managed the following personnel: Quality Assurance Manager, Quality Assurance Engineer, Software Quality Engineer, three in-process inspectors, one final inspector, one administrative assistant, and five incoming inspectors. Projects: FAA self disclosure, update ISO system to AS9100, implement SPC, reduction of materials cost, quality inspections pushed back to suppliers, and reduced calibration cost by 25%,
-
-
-
Howell Instruments, Inc.
-
Fort Worth, TX
-
Quality Assurance Manager
-
Oct 1999 - Aug 2007
Management of quality assurance activities including; Incoming inspection, in-process inspection, final inspection, material review board, supplier management, training program (quality assurance and operations), calibration program, FAA MIDO, FAA FSDO, FAA TSO, PMA, acceptance test procedures, and acceptance / calibration of final products shipped. Managed the following personnel: Three in-process inspectors / final inspection, one incoming inspector. Projects: Calibration program redesign (reduced annual cost by 50%), FAA training program, training records, implemented electronic quality records, and monitored re-work.
-
-
-
-
Quality Assurance Manager
-
1996 - 1997
Directed day-to-day quality assurance operations with a primary focus on Customer issues, process improvement, in-process inspection, final inspection, statistics, and shipping inspection. Managed calibration program, corrective actions, preventive actions, material review board, supplier management, helped employees realize their potential, and cost savings. Directed day-to-day quality assurance operations with a primary focus on Customer issues, process improvement, in-process inspection, final inspection, statistics, and shipping inspection. Managed calibration program, corrective actions, preventive actions, material review board, supplier management, helped employees realize their potential, and cost savings.
-
-
Education
-
Wayland Baptist University
BS, Occupational Education Engineering -
Wayland Baptist University
Bachelor of Science (B.Sc.), Occupational Education
Community
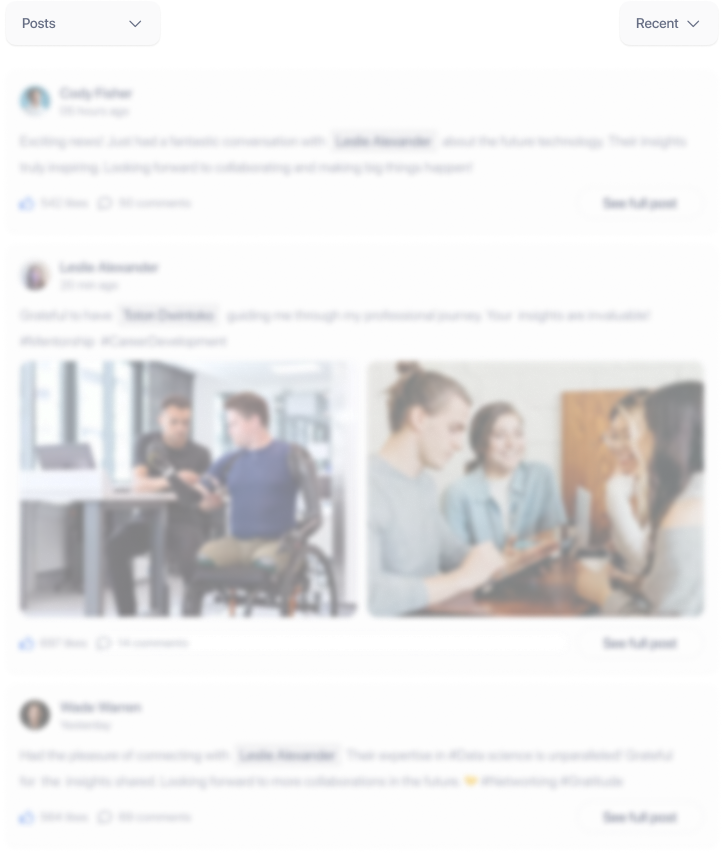