Ganesh Salunke
Assistant Manager-EV Purchase at Kinetic Communication Ltd. Chinchwad,Pune- Claim this Profile
Click to upgrade to our gold package
for the full feature experience.
-
English Full professional proficiency
-
Hindi Full professional proficiency
-
Marathi Full professional proficiency
Topline Score
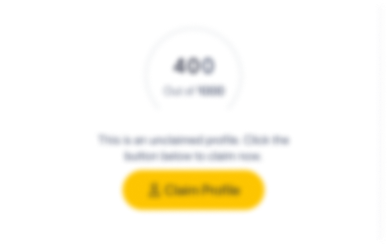
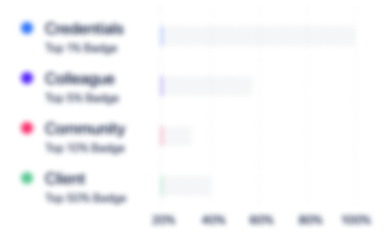
Bio


Credentials
-
Strategic Cost Management For Procurement & Supply
UdemyMay, 2020- Nov, 2024 -
Global Supply Chain Management
NPTELApr, 2020- Nov, 2024 -
Supply Chain Management Analytics
NPTELApr, 2020- Nov, 2024
Experience
-
Kinetic Communications Ltd. Chinchwad,Pune
-
Appliances, Electrical, and Electronics Manufacturing
-
1 - 100 Employee
-
Assistant Manager-EV Purchase
-
May 2022 - Present
1. New Part Development: - a) Feasibility study of new models b) Floating RFQ and sourcing decisions c) Management of ECN and APQP interpretation d) Part Cost Negotiation depending on ZBC. 2. Cost Improvement (Cost Reduction beyond inflation) Implementation of ideas, Value Addition / Value Engineering. 3. Identification and development of new resources, Multi-Sourcing / Alternative sourcing / Global Sourcing / Rationalization / Risk Management. 4. Tracking actual and PO release v / s budget. 5. Conduct Supplier Evaluation / fire and safety audit / green procurement management. Commodity Handles- Plastic, Fasteners, Casting, Forging, Sheetmetal, B/O Parts. Show less
-
-
-
Kinetic Communications Limited
-
Pune/Pimpri-Chinchwad Area
-
Sr.Purchase Engineer
-
Jun 2020 - May 2022
1) A result oriented professional with 3 years of experience in developing and maintaining sourcing vision, processes, and organization for selecting, managing, and developing the organizations strategic suppliers for Automobile. 2) Working knowledge of Oracle 9-i and Power Term, Tally. ERP 9, TCS System, MS Office Excel, MS Word. 3) Analyse all suppliers in order to select the most suitable suppliers who are able to deliver high quality products at competitive pricing. 4) Negotiate with suppliers on lead-time, cost & quality so as to obtain the maximum benefit for the company also calculate machining process time with the help of drawings. 5) Manage suppliers to meet objectives related to cost, delivery performance, schedule & quality. 6) Define and maintain documented category & supplier strategies using market & competitive data. 7) Develop, Implement and Drive the procurement strategies in order to meet cost savings targets. 8) Review and manage supplier base to ensure consistency with the sourcing strategy. 9) Coordinate with vendor on continuous quality improvement. 10) Responsible to control and monitor project total expenditure including verifying and checking of invoices and claims from suppliers, vendors and subcontractors to ensure that all project Expenditures are captured and properly recorded. 11) Develop purchasing & sourcing strategies based on portfolio analysis & supplier preferencing study. 12) Provide planning and cost controlling support for all projects which includes variation reporting, monitoring of milestone progress to the preparation of customer billing Processes, etc. 13) Perform and manage project activity scheduling and monitoring. 14) Materials Management, PO work under based on oracle and online Purchase Order is prepared in Oracle System 9-i, Reconciliation vendor Statement with Oracle System & Manual. Stock Verification, Analysis of Vendor Performance & Price Variance & Purchase related all responsibility. Show less
-
-
-
-
Purchase Engineer
-
Jan 2017 - May 2020
1) A result oriented professional with 3 years of experience in developing and maintaining sourcing vision, processes, and organization for selecting, managing, and developing the organizations strategic suppliers for Automobile. 2) Working knowledge of Oracle 9-i and Power Term, Tally. ERP 9, TCS System, MS Office Excel, MS Word. 3) Analyse all suppliers in order to select the most suitable suppliers who are able to deliver high quality products at competitive pricing. 4) Negotiate with suppliers on lead-time, cost & quality so as to obtain the maximum benefit for the company also calculate machining process time with the help of drawings. 5) Manage suppliers to meet objectives related to cost, delivery performance, schedule & quality. 6) Define and maintain documented category & supplier strategies using market & competitive data. 7) Develop, Implement and Drive the procurement strategies in order to meet cost savings targets. 8) Review and manage supplier base to ensure consistency with the sourcing strategy. 9) Coordinate with vendor on continuous quality improvement. 10) Responsible to control and monitor project total expenditure including verifying and checking of invoices and claims from suppliers, vendors and subcontractors to ensure that all project Expenditures are captured and properly recorded. 11) Develop purchasing & sourcing strategies based on portfolio analysis & supplier preferencing study. 12) Provide planning and cost controlling support for all projects which includes variation reporting, monitoring of milestone progress to the preparation of customer billing Processes, etc. 13) Perform and manage project activity scheduling and monitoring. 14) Materials Management, PO work under based on oracle and online Purchase Order is prepared in Oracle System 9-i, Reconciliation vendor Statement with Oracle System & Manual. Stock Verification, Analysis of Vendor Performance & Price Variance & Purchase related all responsibility. Show less
-
-
Education
-
Pune University
Bachelor of Engineering - BE, Mechanical Engineering
Community
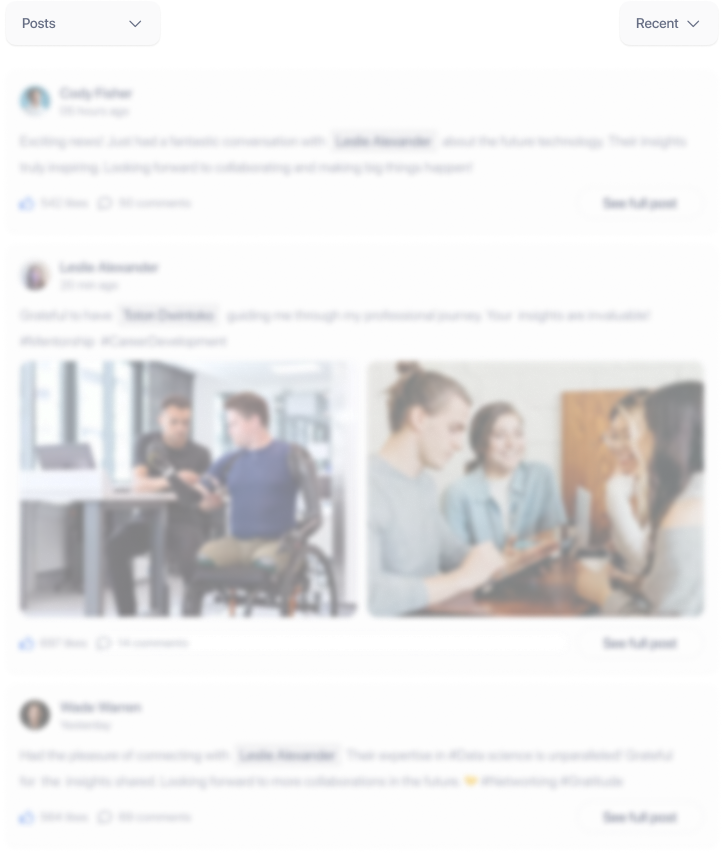