Gagan Kamble
Productivity Improvement Analyst at Gains5- Claim this Profile
Click to upgrade to our gold package
for the full feature experience.
-
English -
-
Kannada Native or bilingual proficiency
-
Hindi -
-
Marathi -
-
Telugu Elementary proficiency
Topline Score
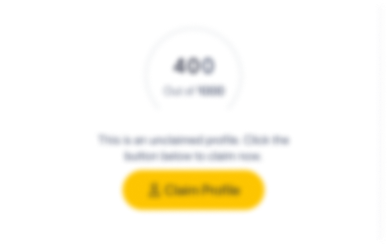
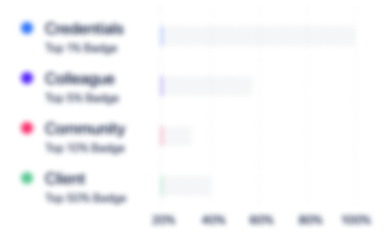
Bio

Viviana Pulido Cantor
I had the pleasure to work with Gagan in Woolworths Group in Sydney Australia, collaborating in projects for the National Productivity team. I was impressed by his ability to handle projects and be a team player. In addition to his professional qualifications, Gagan has the expertise and knowledge in MOST modelling as well as systems management. He is a person committed to progress and quality.

Viviana Pulido Cantor
I had the pleasure to work with Gagan in Woolworths Group in Sydney Australia, collaborating in projects for the National Productivity team. I was impressed by his ability to handle projects and be a team player. In addition to his professional qualifications, Gagan has the expertise and knowledge in MOST modelling as well as systems management. He is a person committed to progress and quality.

Viviana Pulido Cantor
I had the pleasure to work with Gagan in Woolworths Group in Sydney Australia, collaborating in projects for the National Productivity team. I was impressed by his ability to handle projects and be a team player. In addition to his professional qualifications, Gagan has the expertise and knowledge in MOST modelling as well as systems management. He is a person committed to progress and quality.

Viviana Pulido Cantor
I had the pleasure to work with Gagan in Woolworths Group in Sydney Australia, collaborating in projects for the National Productivity team. I was impressed by his ability to handle projects and be a team player. In addition to his professional qualifications, Gagan has the expertise and knowledge in MOST modelling as well as systems management. He is a person committed to progress and quality.

Experience
-
Gains5
-
Australia
-
Business Consulting and Services
-
1 - 100 Employee
-
Productivity Improvement Analyst
-
Oct 2019 - Present
BAU Activities:oManage supermarket store queries via E-mail and provided solutions on labour hours related inquiries.oManaging skill mix for renewal (refurbished stores) and new stores.oSetting up new stores in the Standards Management System (SMS), Customer Led Rostering (CLR) System, and various other productivity systems.oExtending on job training to the new recruits while their induction period and carrying on monthly training sessions to brush up all the concepts used internally in the business.oConstruct new processes and carry out productivity study to find out the impact on the business. Maintain the process documents of the same.oHave stand up daily to mark where all the team members stand in their assigned projects with the use of JIRA boards.Project Led:oProject Name: Impact Analysis on the Supermarket Business while using 2/3rd Pallets.Project Duration: April 2020-August 2020Description: Introduction of 2/3rd pallets which is in 2/3rd size of the normal pallet(2mtr*2mtr) which would eliminate the process of breaking the load on pallet and running the load to the trading area in roll cages (small trolleys).oProject Name: Process changes in Planogram changes.Project Description: July 2020-September 2020Description: Introduction of “Samsung Tab” replacing the hardcopies of the planogram. This eliminates the task of striping down the whole bay in the trading area while changing the planogram which in tun reduces the manhours required to complete the task. This project reduces the manhours thus saving AUD ($) 8.1 mil/year.Responsibilities:oDetermining labour efficiency standards for various processes in the supermarket space using M.O.S.T (Maynard Operation Sequence Technique) tool.oModelling shelf replenishment tasks that contributed 65% of labour spend in the department which included receiving fresh load and running pallets.Building impact assessment to identify the difference in current labour standards to proposed labour standards.
-
-
-
-
Team Member
-
Apr 2018 - Apr 2021
➢ Selling Woolworths brand with passion and enthusiasm by maintaining up-to-date knowledge of store policies regarding payments, returns and exchange.➢ Using awareness, attention to detail and integrity.➢ Maintaining stock, maximizing sales and organizing weekly sales report for the sales team to keep track.➢ Implementation of planogram updates, stacking, facing.➢ Providing customers with fast, efficient, friendly and knowledgeable service intron building relationships with the suppliers and customers.➢ Ensuring OH & S of all store associates and customers.
-
-
-
Jindal Steel & Power Ltd.
-
India
-
Mining
-
700 & Above Employee
-
Assistant Engineer-Pellet Plant Operations.
-
Apr 2015 - Nov 2016
• Responsibilities: o Promoted from Graduate Engineer Apprentice (GEA). o Responsibly performed duties concerning Operation, Purchase and Compliance of whole Pellet Plant in regular shifts. o Frequently appreciated by the senior management for managing a team of 13 people for operating pellet plant & handling Computer Control Room Operations which enhanced my team management skills. o Maintained very streamlined conversation with mechanical & Electrical In charges to plan shutdown during the lean period. o Managed administrative and operational work such as generating shift reports, data, reading of trends and daily/monthly reports (on MS Excel and MS PowerPoint). o Acknowledged for monitoring all the parameters for higher productivity without compromising the quality of the product. o Actively participated in the implementation of TPM (Total Productive Maintenance) & IMS (Integrated Management System) in the department. • Achievements: o Secured first position in presenting a case study on “Quality Optimization of Iron Ore Pellets” in a conference held by Aditya Birla Group titled “Manufacturing Today Reinventing the Future at Bhubaneswar” wherein the company could successfully save 3 Million AUD (per annum) in production of Iron Ore pellets. o Acknowledged with “Appreciation Certificate” for the support to “TPM Secretariat” during JIPM Audit, leaning to the achievement of JIPM-TPM Excellence Award Category ‘A’ (2015).
-
-
Graduate Engineering Apprentice
-
Apr 2014 - Apr 2015
• Responsibilities: o Built productive relationships at all levels within the company. o Developed a thorough understanding of safety procedures (OH&S). o Collaborated with managers to gain familiarity with existing production facilities. o Collaborated regularly with management for evaluations of individual market and production targets.
-
-
-
Thejo Engineering Ltd.
-
India
-
Mechanical Or Industrial Engineering
-
200 - 300 Employee
-
Graduate Engineer Trainee
-
Aug 2013 - Mar 2014
• Responsibilities: o Planning & implementing marketing activities across all online & offline channels. o Administered and maintained records consisting of employee information at Barbil site. (HR-related work) o Strategizing for new marking initiatives, generate sales leads and customer relations. o Coordinated company representation at relevant conferences and exhibitions o Supply Chain management exposure at plant level for the supply of material and supply of goods and materials. o Project management exposure to managing $700,000 (3.6 million INR) project. i. Site Inspection design the product, manufacture, procurement of raw materials, installation, and final handover of the project to the client. ii. Developed detailed work breakdown structures (WBS) and instilled shared accountability for achieving project milestones. iii. Achieved Project tracking, measurement, evaluation and reporting on all activities. iv. Resolved project issues with regards to scope creep, staffing problems and client needs. o Mobilization of man material & machines as per the requirement without compromising the quality of work.
-
-
-
Gearock Forge Pvt Ltd
-
India
-
Automotive
-
1 - 100 Employee
-
Project Intern
-
Feb 2013 - Jun 2013
Process Improvement, facilities planning Process Improvement, facilities planning
-
-
-
Toyota Kirloskar Motor
-
India
-
Motor Vehicle Manufacturing
-
700 & Above Employee
-
Internship
-
May 2012 - Jul 2012
Quality Control, checklist implementation, continuous improvement Quality Control, checklist implementation, continuous improvement
-
-
Education
-
University of Technology Sydney
Master of Business Administration (MBA), Project Management -
M.S. Ramaiah Institute Of Technology
Bachelor of Engineering (BEng), Industrial Engineering -
Kendriya Vidyalaya Kudremukh
10th
Community
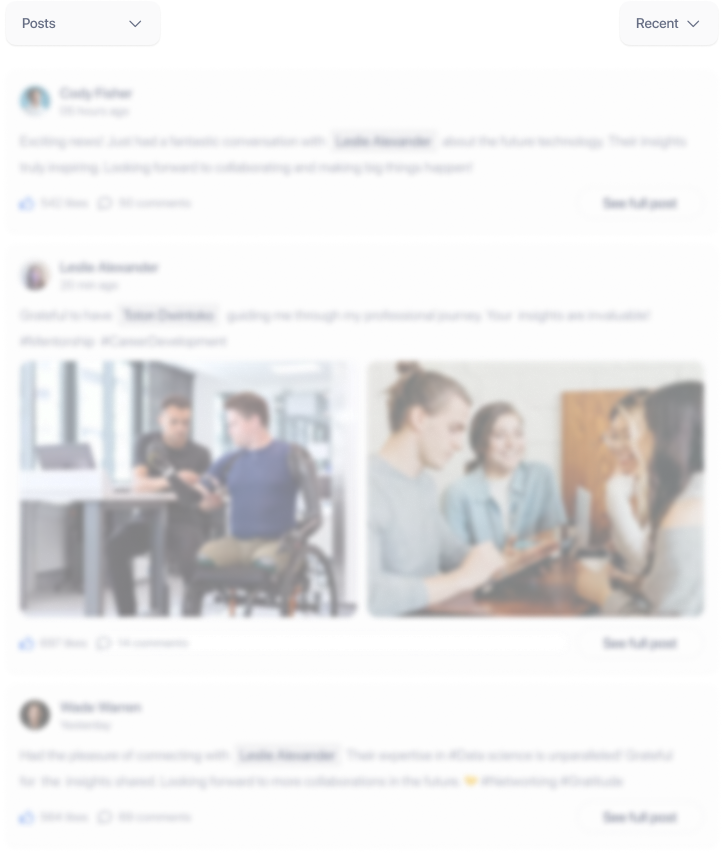