Gabe Hernandez
Operations Director at ReviewMate- Claim this Profile
Click to upgrade to our gold package
for the full feature experience.
Topline Score
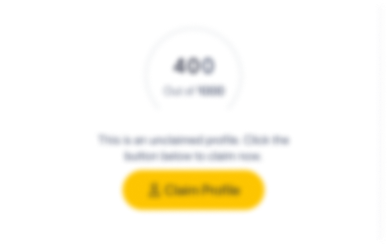
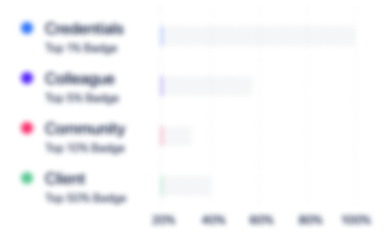
Bio


Experience
-
ReviewMate
-
Advertising Services
-
Operations Director
-
Sep 2018 - Present
The complete suite to inspect, organize, and manage medical coding audits with efficiency. Pickerson Solutions LLC was formed in 2013 when a question was asked, "In this day and age of technology, why is our industry still using spreadsheets?" This question launched the development of ReviewMate® by medical coding auditors for medical coding auditors. Pickerson Solutions' leadership team, with experience in middle revenue cycle management, software programming and development, is dedicated to working with our clients to advance quality of life for auditors by providing the most robust and innovative software in the revenue cycle market. Show less
-
-
-
-
North American Supply Chain Manager - Retired
-
Mar 2017 - Sep 2020
-
-
-
Toyota Motor Sales, Inc
-
United States
-
Retail
-
1 - 100 Employee
-
Parts Distribution Facility Manager
-
Nov 2012 - Feb 2017
Responsible for supporting the operations management team’s efforts to coordinate warehouse operations activities that relate to the receipt, storage and distribution of service parts and accessories. Ensures that customer service expectations for the facing dealers, regional partners, facility associates and other business partners are established, clearly communicated and achieved. Responsible for creating a positive safety culture within the facility that results in adherence to standards and continuous improvement through proactive abatement activities. Champion for creating a quality culture that addresses customer satisfaction with the dealers and promotes excellence in all of the work produced by the entire PDC staff. Champion’s the Toyota Way Culture by ensuring that all facility associates are afforded the opportunity to develop, grow and fully contribute to the success of the organization. Ensures the efficient use of resources by leading and leveraging strategic and tactical activities in support of North American Parts Operations Hoshin and financial plans. Show less
-
-
Part Center Operations Manager
-
Sep 2011 - Dec 2012
Oversaw a production staff of 177 team members and 8 leadership staff members in daily warehouse operations activities that relate to receipt, storage, kitting, and shipment of Japan and NA freight. Oversaw the completion and implementation of the 3 year Home Position Layout Reconfiguration Project. Completed in 8 months through strict project management processes and direction clarification.
-
-
-
Toyota Motor Sales
-
United States
-
Motor Vehicle Manufacturing
-
700 & Above Employee
-
Japan Sourced Parts Procurement Manager
-
Feb 2006 - Mar 2011
Exceed and maintain Procurement KPI’s by improving dealer and distributor fill rate, achieving low backorder levels, and identifying and implementing safety stock changes to support appropriate inventory levelsCreate, develop and implement an MS Access Db tool known as SIMS (Supply and Inventory Management System), a daily exception management database that is a One Stop Shop for managing deficit and excess supply and inventory conditions, demand and order management activities, as well as backorder recovery for PC's and PDC's, through team effortJapan Tsunami Recovery Activities in March 2011, including facilitation of activities for multiple supply departments, executive management report out, TMC negotiation and communication for supply recovery.Inventory Mgmt and Forecasting Improvement, resulting in 97% accuracy rate order to demand. Reduced air cost by $2.1mil annually through leadershipTook back responsibility of key blank sales from 3rd party, resulting in $2.4 mil in profit for TMS.Developed and implemented the Port Contingency Plan during the ILWU strikes while maintaining strong customer service Show less
-
-
Japan Source Procurement Supervisor
-
Apr 2004 - Sep 2006
Supervised the completion of daily, weekly, and monthly exception processing to meet key performance objectives.Created vision and led team to establish the Procurement Dojo Center through effective communication and progressive curriculumCo-led the Supply Chain Revolution project to identify and eliminate redundant work and non-standardized daily exception processes while improving efficiency.Facilitated the improvement of monthly training sessions for procurement administrators on monthly exception processes to ensure efficient procurement ordering.Led the Fixed Safety Stock Validation Project, a cross-functional project with Warehouse Operations, to validate a standard-based environmentLed and facilitated cross training between Parts Supply Procurement and warehouse operations team members in the daily, weekly, and monthly PSP functions and practices. Show less
-
-
-
-
Japan Source Procurement Administrator
-
2003 - 2004
Reduced approximately $1.1 million in inventory for Bumper Covers through the tracking process while achieving and exceeding 95% customer fill.Developed process to manage and reduce order variation of current model Bumper Covers ensuring strict Heijunka ordering to reduce supplier impact.Created and implemented desk related Hyperion Brio queries for tighter exception management controls
-
-
Parts Center Group Leader – Receiving and Cross dock Operations
-
Apr 2001 - Sep 2003
-
-
Parts Center Storage Senior Team Member
-
Aug 1996 - Sep 2001
-
-
Community
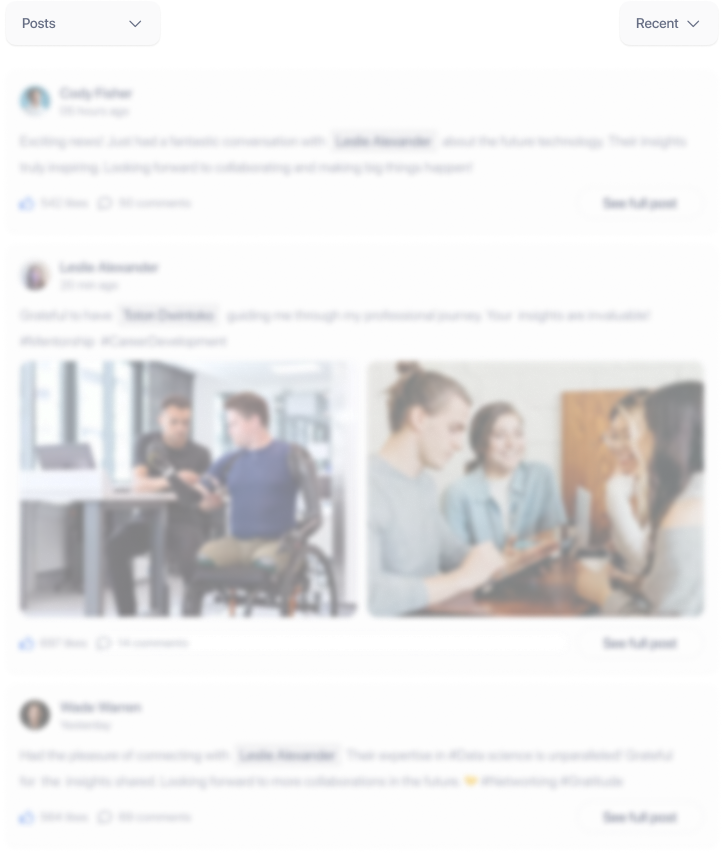