Franklin Hunt
Production Supervisor (Manufacturing) at Logistic Services International, Inc.- Claim this Profile
Click to upgrade to our gold package
for the full feature experience.
Topline Score
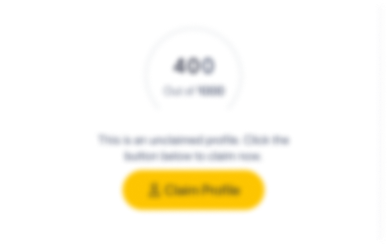
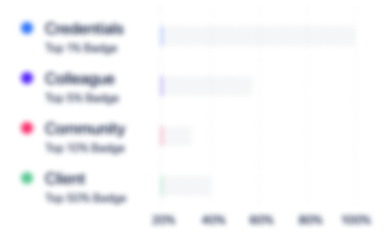
Bio


Experience
-
Logistic Services International, Inc.
-
United States
-
Defense and Space Manufacturing
-
300 - 400 Employee
-
Production Supervisor (Manufacturing)
-
Dec 2021 - Present
Jacksonville, Florida, United States LSI has over 475+ training and support experts, engineers, and craftsmen/artisans on staff who develop/manufacture/produce state-of-the-art high-fidelity training devices, complex computer-based, highly interactive distributed learning products, and comprehensive, dynamic technical publications. Oversee production operations, monitoring and tracking raw material usage and product line procedures to ensure requirements of active contracts are met and delivery work orders are fulfilled… Show more LSI has over 475+ training and support experts, engineers, and craftsmen/artisans on staff who develop/manufacture/produce state-of-the-art high-fidelity training devices, complex computer-based, highly interactive distributed learning products, and comprehensive, dynamic technical publications. Oversee production operations, monitoring and tracking raw material usage and product line procedures to ensure requirements of active contracts are met and delivery work orders are fulfilled. Maintains a Quality Matrix at 98% pass rate. Implement and monitor Preventative Maintenance System (PMS) program to prolong the lifespan of company assets and reduce manufacturing and production downtime. Acquired critical spare parts inventory for rapid repair of onsite machinery. Develop workflow policies and procedures that prioritize efficiency. effectiveness, and safety, while also participating in safety and quality management system (QMS) internal audits. Improved production processes achieving an increase in efficiency and while decreasing raw material waste. Manage and track labor and material cost for multiple programs, assessing impact on program cost and schedule and taking corrective action when necessary. Executes Root Cause Analysis routines on Quality Assurance major/minor defects and all non-compliance reports to determine applicable remedies/solutions and recommendations. Upholds the ISO 9001 Quality Management System (QMS) by forming, adhering to, and upholding organizational quality standards, safety, and quality programs. Promotes attainment of vision/plan by organizing/designating artisan workforce, establishing manufacturing objectives, formulating priorities, inspecting in-processes, altering schedules, rectifying issues, assessing outcomes, and detailing the progress of the processing flow on shift production summaries. Show less
-
-
-
Pegasus Technologies, Inc.
-
United States
-
Appliances, Electrical, and Electronics Manufacturing
-
1 - 100 Employee
-
Director of Material Support
-
Jun 2018 - Oct 2021
Green Cove Springs, Florida Pegasus Technologies, Inc. (PTI) is a Federal Aviation Administration (FAA) Part 91 operator with extensive fixed-wing and rotor-wing experience, Part 23, 25, 27, and 29 aircraft. Tasked with leading, developing, and managing all aspects of the Logistics Department, including the acquisition of aeronautical equipment, Parts Material Requests, Request for Quotes, and Purchase Orders and Repair Purchase Orders. Moreover, Responsible for the procurement of raw materials, consumables… Show more Pegasus Technologies, Inc. (PTI) is a Federal Aviation Administration (FAA) Part 91 operator with extensive fixed-wing and rotor-wing experience, Part 23, 25, 27, and 29 aircraft. Tasked with leading, developing, and managing all aspects of the Logistics Department, including the acquisition of aeronautical equipment, Parts Material Requests, Request for Quotes, and Purchase Orders and Repair Purchase Orders. Moreover, Responsible for the procurement of raw materials, consumables, and support materials, as well as for overseeing Inventory Control Procedures, Distribution Operations, Property Control and Asset Management, and material management for both domestic and international locations. Additionally, had 6 CDL operators under my supervision and was managing the 5 company-owned commercial delivery vehicles and their respective trailers, to ensure compliance with all DOT/OSHA regulations and to track mileage/usage and the safety of the vehicles and trailers. Responsible for handling MHE Licensing and PMS programs. Responsible for negotiating B2B costs, terms, and conditions with vendors, suppliers, and external customers/clients related to the 44 fixed-wing and rotary-wing company-owned and managed aircraft. Critically analyzed all contractual terms and conditions, as well as indemnity clauses for clarity and conflict. Instrumental in vetting over 100 new vendors to enhance availability, lower costs, and increase customer return on investment. On a weekly basis, provided oral and written operational status briefings to the Board of Directors, Vice Presidents, and Directors regarding shipping and receiving, to ensure customer satisfaction and fiscal responsibility. Worked in conjunction with the Maintenance Department and Quality Assurance staff to create and maintain a range of processes intended to guarantee service compliance for all time-sensitive warehoused equipment. Show less
-
-
-
-
Employee
-
Dec 2017 - Jun 2018
Jacksonville, Florida Area Unison Industries Inc. (G.E. Aviation) is a supplier to nearly every engine and airframe program, providing the most advanced performance solutions for various markets, including aviation, space and defense, power, oil and gas, and transportation. Manufactures gas turbine ignition systems, including ignition exciters, igniters, leads, speed sensors, and other electronic components and repair and overhauls ignitions systems and speed sensors. (FAA Repair Center UILR299K).… Show more Unison Industries Inc. (G.E. Aviation) is a supplier to nearly every engine and airframe program, providing the most advanced performance solutions for various markets, including aviation, space and defense, power, oil and gas, and transportation. Manufactures gas turbine ignition systems, including ignition exciters, igniters, leads, speed sensors, and other electronic components and repair and overhauls ignitions systems and speed sensors. (FAA Repair Center UILR299K). Managed and monitored a Heat Treatment work center within an industrial manufacturing facility, including six industrial ovens, two vacuum parts dryers, and two vacuum/pressure chambers. Responded to incoming goods and shipments of OEM and Repair parts, using ERP knowledge to maintain stocking levels and ensure on-time delivery to customers. Participated in cross-functional teams to support production operations, troubleshoot issues, and develop corrective action and sustainable solutions. Assisted in process improvement projects, value stream mapping efforts, and Kaizen events/lean projects to increase efficiency and inventory accuracy. Administered appraisal and updating of 35 work orders (routers) to ensure technical clarity for industrial plant-assigned technicians. Verified comprehension of instructions provided in the work orders. Selected to collaborate with Quality Assurance and Material Engineers to investigate discrepancies, analyze causes of issues, recognize, and fix training mistakes, and eliminate unnecessary activities and rework. 5S Coordinator - Spearheaded, outlined, and conducted continual process enhancements (5S) within the work center, provided technicians with guidance, and monitored weekly adherence. Show less
-
-
-
M2 Services
-
United States
-
Aviation and Aerospace Component Manufacturing
-
1 - 100 Employee
-
Program Manager (Contractor) - Fleet Readiness Center Southeast
-
Feb 2015 - May 2017
Fleet Readiness Center Southeast Naval Air Station Jacksonville Regulated all on-site touch-labor contractor functions daily and implemented executive decision-making in the process of aeronautical manufacturing, repair, and overhaul (MRO) operations, supervising a total of 440 subject matter expert (SME) artisan/technicians across facilities in Florida, South Carolina, and Virginia. Prioritized daily workloads, scheduled, and monitored production timeliness and quality assurance compliance for the secure delivery of F-18A/D, H-60, T-44, T-6… Show more Regulated all on-site touch-labor contractor functions daily and implemented executive decision-making in the process of aeronautical manufacturing, repair, and overhaul (MRO) operations, supervising a total of 440 subject matter expert (SME) artisan/technicians across facilities in Florida, South Carolina, and Virginia. Prioritized daily workloads, scheduled, and monitored production timeliness and quality assurance compliance for the secure delivery of F-18A/D, H-60, T-44, T-6, P-3/EP-3, E-6, and T-34 military aircraft. Sourced and enabled the recruitment and onboarding of more than 480+ new artisan/technicians within 30 months to meet government backfill and additional requirement demands. Implemented the Environmental, Health, and Safety (EHS) program which established specified targets and objectives. Worked towards sustaining a zero-incident EHS culture and succeeded in reducing the Recordable Injury Rate (RIR) by 65%. Established a mentor program focusing on QMS training and quality review progress which resulted in a reduction of Discrepancy Work Orders (DWO)/Material Review Board (MRB) efforts by 55%. Composed 85 Quality Management System (QMS) Instructions and 25 Local Safety Instructions (LSI) for the maintenance, quality assurance, and safety programs of the contract in compliance with OSHA and OPNAV/NAMP standards. Show less
-
-
-
-
E-2D and F-5 Flight Test Programs - Quality Assurance Specialist
-
Nov 2012 - Apr 2015
St Augustine, Florida Defense Contract Management Agency (DCMA) is a component of the United States Department of Defense (DoD) that works with defense contractors to ensure government services and supplies are delivered on time, come at the expected cost and satisfy all performance requirements. DCMA oversees the administration of origin inspection contracts, dispatches quality assurance (Q.A.) reports, and audits and monitors subcontracting plans. The primary goals of the DCMA include guaranteeing the… Show more Defense Contract Management Agency (DCMA) is a component of the United States Department of Defense (DoD) that works with defense contractors to ensure government services and supplies are delivered on time, come at the expected cost and satisfy all performance requirements. DCMA oversees the administration of origin inspection contracts, dispatches quality assurance (Q.A.) reports, and audits and monitors subcontracting plans. The primary goals of the DCMA include guaranteeing the quality of services, supplies, equipment, and support; ensuring services and supplies comply with all standards and regulations; and confirming that the contractor fulfills all requirements included in their contract. DCMA is necessary to ensure the U.S. government receives the services it needs and that the military is fully supported and ready to complete its mission objectives. Member of a multi-functional QA residential team assigned to Northrop Grumman Aerospace System's ISO 9001 and AS9100 manufacturing plant. Performed shareholder process/procedural reviews and critical safety inspections (CSI) during E-2D initial build, E-2D Inflight Refueling Probe development, and F-5 Phased Depot Maintenance I/II program. Full-charge responsibility for the hands-on control of an aviation parts inventory with an estimated value in the hundreds of millions of dollars; appointed to the Material Review Board (MRB); audited and approved Over & Above (O&A) expenditures, and ensured Safety of Flight (SOF) guidelines. Reviewed contracts and technical data packages to identify both the specification work order and professional requirements associated with detailed technical drawings. Established and maintained communications with contractor's management to ensure understanding exists for acceptable quality evidence for performance and critical process proofing/measurement and analysis. Show less
-
-
-
-
C-40A Contract Field Team (CFT) Site Leader
-
Jan 2012 - Oct 2012
Fleet Logistics Support Squadron Five Eight (VR-58) Strategic Technology Institute, Inc. (STi) is a minority-owned small, disadvantaged business (SDB) providing practical and innovative solutions in Maintenance, Repair, & Overhaul (MRO), Logistics, Safety, Reliability, Maintainability, & Quality Assurance (SRM&QA), I.T. & cybersecurity, and project management & control. STi, Inc is AS9100D-certified, ISO 14001:2015-certified, and ISO 9001:2015-certified concerning business management and program management, which profoundly influences… Show more Strategic Technology Institute, Inc. (STi) is a minority-owned small, disadvantaged business (SDB) providing practical and innovative solutions in Maintenance, Repair, & Overhaul (MRO), Logistics, Safety, Reliability, Maintainability, & Quality Assurance (SRM&QA), I.T. & cybersecurity, and project management & control. STi, Inc is AS9100D-certified, ISO 14001:2015-certified, and ISO 9001:2015-certified concerning business management and program management, which profoundly influences our consistent "Safety First, Quality Always" culture. Provided leadership, daily decision-making, and overall project direction for a highly skilled Contractor Field Team of 28 aviation maintenance technicians performing aircraft safe-for-flight and preventive maintenance routines for the Boeing C-40A Clipper. Orchestrated the talent acquisition, hiring, and onboarding of 5 A&P-licensed mechanics and several support personnel. Developed a focused workforce training program and set qualification requirements linked to the Performance Work Statement/Statement of Work. Show less
-
-
-
-
F-5N Aviation Maintenance Analysis / Liasion / Technical Advisor
-
Jan 2011 - Sep 2011
Northrop Grumman Aerospace - St Augustine Strategic Technology Institute, Inc. (STi) is a minority-owned small, disadvantaged business (SDB) providing practical and innovative solutions in Maintenance, Repair, & Overhaul (MRO), Logistics, Safety, Reliability, Maintainability, & Quality Assurance (SRM&QA), I.T. & cybersecurity, and project management & control. STi, Inc is AS9100D-certified, ISO 14001:2015-certified, and ISO 9001:2015-certified concerning business management and program management. Provided analytical… Show more Strategic Technology Institute, Inc. (STi) is a minority-owned small, disadvantaged business (SDB) providing practical and innovative solutions in Maintenance, Repair, & Overhaul (MRO), Logistics, Safety, Reliability, Maintainability, & Quality Assurance (SRM&QA), I.T. & cybersecurity, and project management & control. STi, Inc is AS9100D-certified, ISO 14001:2015-certified, and ISO 9001:2015-certified concerning business management and program management. Provided analytical and technical support as an aviation maintenance liaison between the Defense Contract Management Agency (DCMA) and Northrop Grumman Aerospace's F-5N/F Planned Depot Maintenance (PDM) program for the Commander Naval Air Force Reserves, Naval Air Systems Command, and USN/USMC Reserve Tactical Support Wing Maintenance management teams in Virginia, Florida, Texas, Arizona and Nevada. Provided technical guidance and surveillance on contractor’s performance and ensures compliance with appropriate Department of Defense guidelines, policies and status of work (SOW) procedure while providing program insight and analytical recommendations regarding cost-data scheduling and material conditions and internal/external constraints. Provided additional support in the application of the F-5 PDM In-Service Repair, Integrated Maintenance Program, Planning and Estimating, and special work maintenance actions. Reviewed all over-and-above documents presented and determined if contractor will perform additional work, no-work, or noted-but-not-corrected repair/rework action. Authors and distributed multiple data reporting resources via daily, weekly and monthly reports. Reduced PDM discrepancies 13 percent delivering aircraft on average 14-days early. Extensive familiarity with a wide variety of Information Systems including Manufacturing Execution System (MES); System Application & Product (SAP); Enterprise Resource Planning (ERP). Show less
-
-
-
US Navy
-
United States
-
Armed Forces
-
700 & Above Employee
-
LCDR - Assistant Officer In Charge
-
Sep 2008 - Oct 2010
Fleet Readiness Center Southeast Detachment Mayport Executive Consultant to CO/XO providing expert Senior Leadership in the efficient/effective application of the Naval Aviation Maintenance/Production and Material Control, Quality Assurance/Control, and Administrative/Human Resource Management Programs. Identified and develop strategic business plans to ensure organic capability to support workload projections and Ready-for-Tasking aircraft. Provided guidance in applying quality assurance methods, principles, and practices; and planning… Show more Executive Consultant to CO/XO providing expert Senior Leadership in the efficient/effective application of the Naval Aviation Maintenance/Production and Material Control, Quality Assurance/Control, and Administrative/Human Resource Management Programs. Identified and develop strategic business plans to ensure organic capability to support workload projections and Ready-for-Tasking aircraft. Provided guidance in applying quality assurance methods, principles, and practices; and planning, developing, and implementing risk management strategies designed to ensure compliance with established requirements for a variety of aviation-related maintenance applications. Expertly managed the Aviation Maintenance In-Service Training Program and Navy Total Force Manpower Programs within strict compliance with the COMNAVAIRFORINST 4790.2 and OPNAVINST 1000.16. Directed command programs relative to personnel and management support matter under the guidelines set forth in Department of Defense (DoD), Department of Navy (DoN), and Office of Personnel Management (OPM) regulations. Knowledgeable in the understanding and application of the principles of management system design to include methods of determining management requirements, system flow charting, and input/output analysis techniques as related to cost trade off considerations. Maintained familiarity with the concepts relating to the planning for and management of change, knowledge of the concepts relating to responsibility, effective two-way communication, and the delegation of authority. Hands-on familiarity with supply system fundamentals including the basic understanding of weapon systems acquisition, fleet introduction process, supply distribution system, repairable pipeline, allowance lists, logistic management codes, cross-reference lists, weapon equipment lists, Illustrated Parts Breakdown (IPB) and Technical Directives (TD) for aircraft and engines, and various other Technical Publication Library systems.
-
-
LT/LCDR - Assistant Maintenance Officer
-
Mar 2007 - Sep 2008
Jacksonville, Florida, United States Directed 190 personnel supporting S-3 aircraft and weapon systems. Developed short, medium and long term maintenance management and training plans, including aircraft inventory management, modifications, aircraft/engine depot rework, and aircraft bulletins. Coordinated, collected, identified and analyze data for Unscheduled/Scheduled Maintenance and Flying Hour Programs. Mastered Aviation Financial Analysis Tool (AFAST) charts monitor and control Aviation Fleet Maintenance (AFM) and AVDLR… Show more Directed 190 personnel supporting S-3 aircraft and weapon systems. Developed short, medium and long term maintenance management and training plans, including aircraft inventory management, modifications, aircraft/engine depot rework, and aircraft bulletins. Coordinated, collected, identified and analyze data for Unscheduled/Scheduled Maintenance and Flying Hour Programs. Mastered Aviation Financial Analysis Tool (AFAST) charts monitor and control Aviation Fleet Maintenance (AFM) and AVDLR cost data expenditures.
-
-
-
-
LT - AMO/MMCO
-
Nov 2004 - Mar 2007
Beaufort, South Carolina, United States Directed 225 personnel supporting F/A-18 aircraft and weapon systems. Developed short, medium and long term maintenance management and training plans, including aircraft inventory management, modifications, aircraft/engine depot rework, and aircraft bulletins. Coordinated, collected, identified and analyze data for Unscheduled/Scheduled Maintenance and Flying Hour Programs. Mastered Aviation Financial Analysis Tool (AFAST) charts monitor and control Aviation Fleet Maintenance (AFM) and… Show more Directed 225 personnel supporting F/A-18 aircraft and weapon systems. Developed short, medium and long term maintenance management and training plans, including aircraft inventory management, modifications, aircraft/engine depot rework, and aircraft bulletins. Coordinated, collected, identified and analyze data for Unscheduled/Scheduled Maintenance and Flying Hour Programs. Mastered Aviation Financial Analysis Tool (AFAST) charts monitor and control Aviation Fleet Maintenance (AFM) and AVDLR cost data expenditures. Show less
-
-
-
Pearl Harbor Naval Shipyard & IMF
-
United States
-
Defense and Space Manufacturing
-
700 & Above Employee
-
LT - Aviation Maintenance Division Officer
-
Oct 2001 - Oct 2004
Lead the day-to-day maintenance department administrative and maintenance operations. Coordinated efforts of 350 personnel providing Intermediate level support to P-3C/SH-60/HH-60/S-3 Fleet aviation activities, monitored/directed component level repair services for airframe/avionic platforms and support systems. Senior Legal Counsel (Non-Lawyer) for Commander, Sea Control Wing, U.S. Atlantic Fleet and for the Officer in Charge, Aircraft Intermediate Maintenance Detachment Jacksonville… Show more Lead the day-to-day maintenance department administrative and maintenance operations. Coordinated efforts of 350 personnel providing Intermediate level support to P-3C/SH-60/HH-60/S-3 Fleet aviation activities, monitored/directed component level repair services for airframe/avionic platforms and support systems. Senior Legal Counsel (Non-Lawyer) for Commander, Sea Control Wing, U.S. Atlantic Fleet and for the Officer in Charge, Aircraft Intermediate Maintenance Detachment Jacksonville. Coordinated, directed, assisted and advised senior military leaders in matters of military justice administration and provision of legal services. Provided administrative and technical assistance in courts martial, investigations, administrative boards and personal affairs. Initiated personnel investigations, administrative proceedings and disciplinary actions as directed. Maintained liaison with Naval Legal Service Office and Staff Judge Advocate's Office to obtain legal services in such fields as administrative law, litigation, legal assistance and jurisdiction involving military members. Show less
-
-
-
-
Chief Of Police (Military)
-
Jan 1996 - Sep 1997
Belle Chase, LA Naval Air Station Security Leading Chief Petty Officer. Key duties Deputy Security Officer - Investigations Deputy Security Officer - Operations Anti-Terrorism Coordinator
-
-
-
US Navy
-
United States
-
Armed Forces
-
700 & Above Employee
-
Shipmate
-
1988 - 1991
-
-
Education
-
Defense Acquisition University
-
Embry-Riddle Aeronautical University
Technical Management/Logistic & Transportation
Community
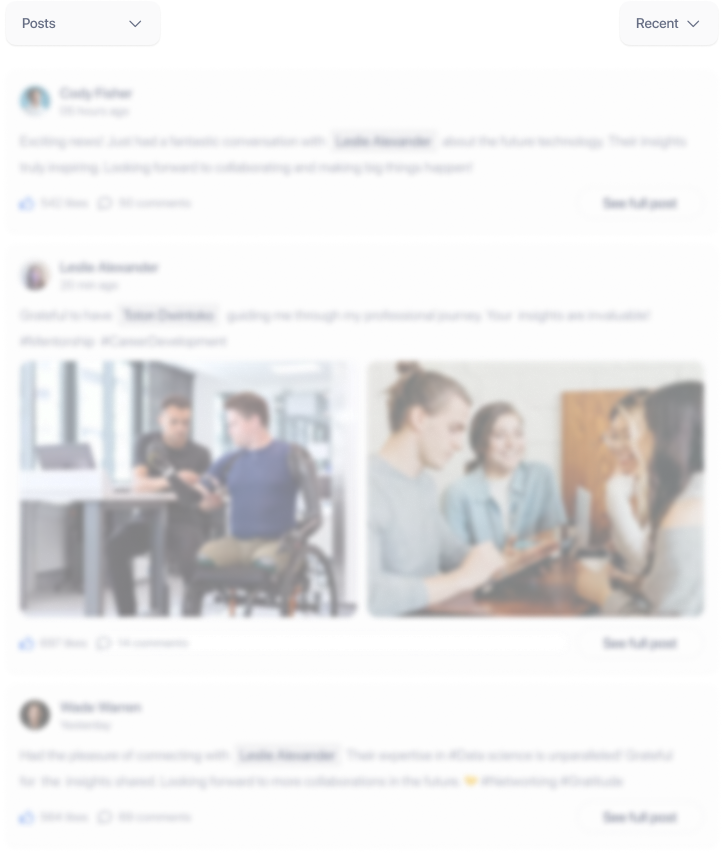