Frank Lazzaro
Sr Manufacturing Engineer at NSTAR Global Services- Claim this Profile
Click to upgrade to our gold package
for the full feature experience.
Topline Score
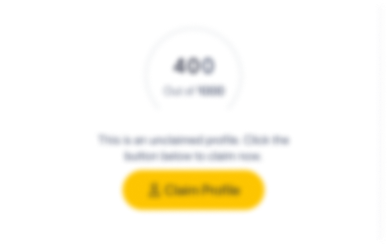
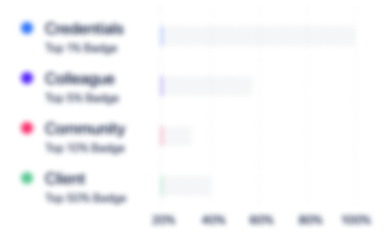
Bio

Andrew Schwab
I worked with Frank for over a year at ATMI. During this time, Frank was always someone you could go to if you needed help on a project or any other work related problems. Frank has extensive knowledge of the manufacturing environment. He was also a vital resource to me when I had any project management questions. Frank is passionate in his work and makes sure everything is done correctly. He was a pleasure to have in the office as a colleague and as a friend.

Kurt Zahler
I worked with Frank for several years at a Manufacturing facility. He led Discrepant Material Reduction team in which Frank and his team made significant results in reducing both internal and supplier related issues. He led a successful DMAIC project focused specifically on physically damage issues. The project ended with positive results and led to some Best Known Methods (BKM’s) implemented across the entire site. Frank has a strong knowledge of machine shop processes and is what I consider a subject matter expert in this arena. I found working with Frank a pleasure and someone that I knew could get the job done with results.

Andrew Schwab
I worked with Frank for over a year at ATMI. During this time, Frank was always someone you could go to if you needed help on a project or any other work related problems. Frank has extensive knowledge of the manufacturing environment. He was also a vital resource to me when I had any project management questions. Frank is passionate in his work and makes sure everything is done correctly. He was a pleasure to have in the office as a colleague and as a friend.

Kurt Zahler
I worked with Frank for several years at a Manufacturing facility. He led Discrepant Material Reduction team in which Frank and his team made significant results in reducing both internal and supplier related issues. He led a successful DMAIC project focused specifically on physically damage issues. The project ended with positive results and led to some Best Known Methods (BKM’s) implemented across the entire site. Frank has a strong knowledge of machine shop processes and is what I consider a subject matter expert in this arena. I found working with Frank a pleasure and someone that I knew could get the job done with results.

Andrew Schwab
I worked with Frank for over a year at ATMI. During this time, Frank was always someone you could go to if you needed help on a project or any other work related problems. Frank has extensive knowledge of the manufacturing environment. He was also a vital resource to me when I had any project management questions. Frank is passionate in his work and makes sure everything is done correctly. He was a pleasure to have in the office as a colleague and as a friend.

Kurt Zahler
I worked with Frank for several years at a Manufacturing facility. He led Discrepant Material Reduction team in which Frank and his team made significant results in reducing both internal and supplier related issues. He led a successful DMAIC project focused specifically on physically damage issues. The project ended with positive results and led to some Best Known Methods (BKM’s) implemented across the entire site. Frank has a strong knowledge of machine shop processes and is what I consider a subject matter expert in this arena. I found working with Frank a pleasure and someone that I knew could get the job done with results.

Andrew Schwab
I worked with Frank for over a year at ATMI. During this time, Frank was always someone you could go to if you needed help on a project or any other work related problems. Frank has extensive knowledge of the manufacturing environment. He was also a vital resource to me when I had any project management questions. Frank is passionate in his work and makes sure everything is done correctly. He was a pleasure to have in the office as a colleague and as a friend.

Kurt Zahler
I worked with Frank for several years at a Manufacturing facility. He led Discrepant Material Reduction team in which Frank and his team made significant results in reducing both internal and supplier related issues. He led a successful DMAIC project focused specifically on physically damage issues. The project ended with positive results and led to some Best Known Methods (BKM’s) implemented across the entire site. Frank has a strong knowledge of machine shop processes and is what I consider a subject matter expert in this arena. I found working with Frank a pleasure and someone that I knew could get the job done with results.
0
/5.0 / Based on 0 ratingsFilter reviews by:
Experience
-
NSTAR Global Services
-
Semiconductor Manufacturing
-
100 - 200 Employee
-
Sr Manufacturing Engineer
-
Jul 2011 - Present
In a Contract position, working for Applied Materials through NStar Global Services, as Sr Manufacturing Engineer • Leading the Manufacturing Engineering team in establishing the necessary data bases required to review, propose, and develop, the ‘True Value’ of product based upon Good Manufacturing Practices. • Leading the team in the necessary DFX models (DFM/A/P), to assure that the product is designed, developed and produced in a manner that will yield profitability to both AMAT and the supply base. • Developing the scenario that affords management to identify and assist Manufacturing Engineers broaden their skill levels insuring that the required fabrication (machining, milling, welding, etc.) is utilized appropriately. Show less
-
-
-
Mayville Products Corporation
-
United States
-
Mining
-
Technical Program Manager
-
Jun 2010 - Jul 2011
Located in Singapore providing both Technical Expertise for the transitioning of Semi-conductor mainframes as well as providing the necessary Quality experience required to qualify the Singapore manufacturer in achieving ISAT SSQA qualification. • Responsible for the introduction of outsourced Semi-Conductor Frames to Singapore and the successful implementation of SSQA audit as defined by Applied Materials for Mayville and its Singaporean partner HFB. • Leading MPC and HFB in merging the assets of both companies into a cohesive team developing each of the companies strengths to develop MPC’s presence in Singapore • Led the Singaporean transition team in developing the necessary production skills that has lead to a successful implementation of the AP and FI-FFU frames in Singapore. • Developed OMS’s, WIs, introduced a NPI program and a HR development Matrix based upon existing and desired skills. • While leading the transition team, was responsible for developing the Quality team in Singapore to present and qualify for the SSQA Audit, as well as leading the teams in passing their ISO 9001-2010 audit. Show less
-
-
-
ATMI
-
United States
-
Semiconductor Manufacturing
-
1 - 100 Employee
-
Project Mgr / Sr MfgE
-
2008 - Jun 2010
Responsible for the transitioning of product from one corporation location (KY) to an outsourced manufacturer (MN) with an effective high-volume manufacturing environment. This required direct interface with the supplier for achieving on-time delivery and quality. Additionally responsible for the introduction of both in-house and outsourced systems such as the Modular Manufacturing Equipment as well as having the responsibility of the corporate-wide conversion from an Agile ERP system to Oracle ERP system, occurring across 5 ATMI locations in the U.S., Europe, and Asia, as well as with all 1st level suppliers. This includes all planning and implementation activities related to policies, procedures, and training for all employees and supplier teams. Our product team is comprised of representatives from various engineering functional groups (mechanical, chemical, and manufacturing) dedicated to this high-visibility corporate initiative. Show less
-
-
-
Applied Materials
-
United States
-
Semiconductor Manufacturing
-
700 & Above Employee
-
Value Engineering Mngr / Sr Manufacturing Engineer
-
Jun 2000 - Apr 2008
Sr Manufacturing Engineer / DEA 200m, directly responsible for new cross-divisional products (both in-house and out-sourced). Reponsible for validation of volume builds, manufacturing documentation, cycle time validation, engineering change orders and supplier issue resolutions, including design and validation of all test and build fixtures, transportability and ergonomics compliance. Additionally, I represent volume operations during SSQA audits specifically for the evaluation of the Suppliers various manufacturing processes. Manager, Value Engineering (4 yrs): managed a group of 10 MfgE’s responsible for ‘should-costing’, Design for Manufacturing and Assembly (DFM/A) utilizing GD&T and supplier negotiations in establishing ‘true’ costs for contracted parts. The team had Material Cost Savings objectives of identifying and implementing $1m per headcount in realized dollars derived from DFM/A implementations and should-costing negotiations with Suppliers. Show less
-
-
-
Intermedics Orthopedics
-
Hospitals and Health Care
-
1 - 100 Employee
-
Sr Mfg Engr
-
1999 - 2001
-
-
-
-
Mgr MfgE, Manufacturing
-
Apr 1998 - Apr 2000
Responsible for the planning and redirection of the facility from a traditional batch manufacturer to a lean/flow facility. Utilized Flow Technology principles throughout the facility (including the electronics, sheet metal, plastics, and screw machine departments) as well as the final assembly lines. Directed two cross-functional teams comprised of personnel from design engineering, manufacturing engineering, purchasing, production, production control, quality, customer service, and facility/maintenance for the implementation of the Flow Initiative as well as standardized processes for New Product Introduction; Efficiency improved to 78%, from 65%, and On-Time Delivery to MRP improved to 94%, from 78%. Show less
-
-
Education
-
Distance Education
MfgE Major / IE Minor, Manufacturing Engineering
Community
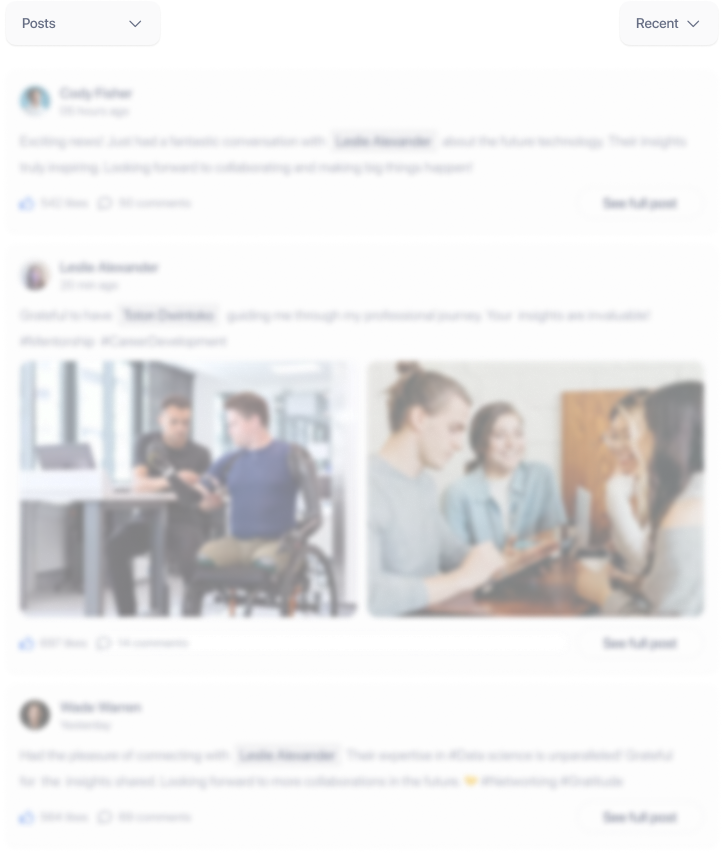