Francisco Saavedra
Plant Engineer and Maintenance Supervisor at Coast Packing Company- Claim this Profile
Click to upgrade to our gold package
for the full feature experience.
-
English Full professional proficiency
-
Spanish Native or bilingual proficiency
Topline Score
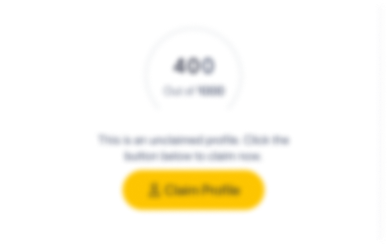
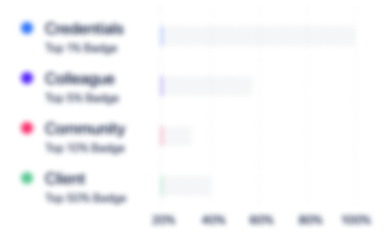
Bio


Credentials
-
Six Sigma Green Belt
DuPontAug, 2015- Oct, 2024 -
Category I – Vibration Analyst, ISO 18436-2
Universidad de ConcepcionJul, 2010- Oct, 2024
Experience
-
Coast Packing Company
-
United States
-
Food and Beverage Manufacturing
-
1 - 100 Employee
-
Plant Engineer and Maintenance Supervisor
-
May 2018 - Present
• Increased 50% of Preventive and Predictive Maintenance work to prevent equipment failure and downtime by implementing new CMMS (computerized maintenance management system). • Increased 25% daily production in critical process area through implementation of steam optimization project. • Reduced on 30% inventory levels by implemented a 5S process on maintenance stockroom to optimize costs, developing standards, SOPs, training, defining minimum stock and reorder point, and establishing visual management. • Updated and upload to CMMS over 300 critical equipment BOM defining proper inventory level according to criticality and usage. • Efficiently managed projects to increase efficiency, improve safety, reduce costs and ensure minimal interruption to plant operations. Show less
-
-
-
ENAP
-
Professional Training and Coaching
-
200 - 300 Employee
-
Operations Integrity Engineer
-
Oct 2016 - Aug 2017
• Collaborated with process and maintenance engineers on risk analysis, audits in process areas, compliance with risk improvement recommendations, and standardization of best maintenance practices. • Coordinated and monitored all aspects of MOC Process for the site, including training, support, preparing the required documentation and facilitating the Risk Review Meetings for each proposed change. • Compiled over 75 recommendations from risk companies, PSM and law compliance into a single spreadsheet establishing unique progress criteria. • Ensured 100% closing of MOC processes pending for more than two years. Show less
-
-
-
-
Reliability Engineer & MIQA Leader
-
Apr 2013 - Sep 2016
• Reduced 90% of downtime of a critical process equipment through a Green belt Six Sigma Project. • Achieved 73% of planned and scheduled maintenance by implementing Asset Care Management best practices, such as work and defects identification, KPIs implementation, scheduling and planning. • Collaborated with Process Engineers and Maintenance Supervisors to identify 100% of PSM Critical Equipment and supported the development of their technical specifications. • Developed preventive maintenance plans for 100% of pressure vessels and pressure relief devices across the facility. • Continually reviewed, updated and improved preventive/predictive plans and frequencies, maintenance procedures, BOMs and CMMS data reliability to increase mechanical integrity of PSM critical equipment. • Led cross-functional teams to analyze critical equipment breakdowns through RCFA to reduce downtime. Show less
-
-
-
ARAUCO
-
Chile
-
Paper and Forest Product Manufacturing
-
700 & Above Employee
-
Internship
-
Jul 2011 - Jan 2012
• Supported vibration analysts during diagnostic of defects using advanced vibration techniques such as envelope, modal and relative phase analysis • Proposed recommendations to eliminate repetitive failure on critical equipment of Pulp Area, through a relative phase vibration analysis. • Determined optimum measurement points, alarm parameters and monitoring techniques to ensure an effective monitoring system to detect early stage bearing defects on 100% of the drying presses. • Supported vibration analysts during diagnostic of defects using advanced vibration techniques such as envelope, modal and relative phase analysis • Proposed recommendations to eliminate repetitive failure on critical equipment of Pulp Area, through a relative phase vibration analysis. • Determined optimum measurement points, alarm parameters and monitoring techniques to ensure an effective monitoring system to detect early stage bearing defects on 100% of the drying presses.
-
-
Education
-
Universidad de Concepción
Master of Science (M.Sc.), Mechanical Engineering -
Universidad de Concepción
Engineer’s Degree, Mechanical Engineering -
Saint John's School, Concepción
Community
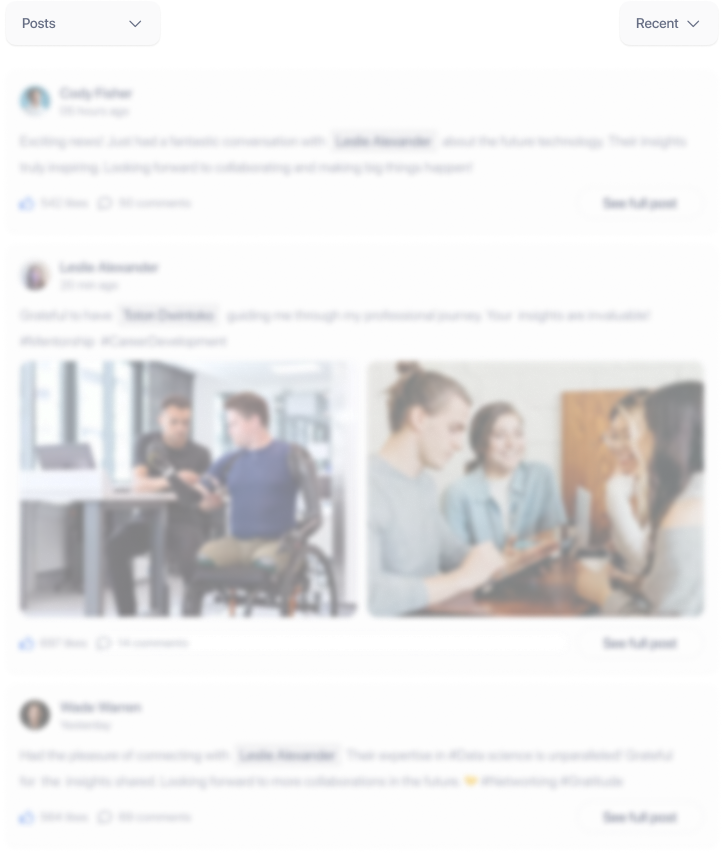