Francisco Lopez
Vice President of Manufacturing at NIPPON SEIKI DE MEXICO, S.A. DE C.V.- Claim this Profile
Click to upgrade to our gold package
for the full feature experience.
-
English -
Topline Score
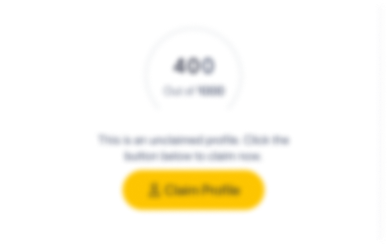
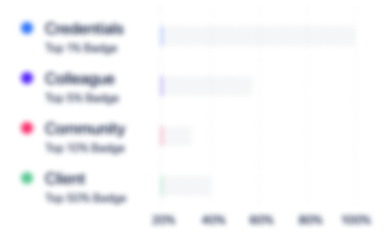
Bio


Experience
-
NIPPON SEIKI DE MEXICO, S.A. DE C.V.
-
Mexico
-
Semiconductors
-
100 - 200 Employee
-
Vice President of Manufacturing
-
Dec 2019 - Present
Manage 2 plants with different processes. Fabrication of Automotive clusters. Create and definition of budget, business growth, customer satisfaction, ERP implementation, successful new model launches, operation profit increase, keep IATF certification, productivity improvement to achieve cost reduction projects, benchmarking activities and continuous improvement implementation in all the company. Create a built to last company. Manage 2 plants with different processes. Fabrication of Automotive clusters. Create and definition of budget, business growth, customer satisfaction, ERP implementation, successful new model launches, operation profit increase, keep IATF certification, productivity improvement to achieve cost reduction projects, benchmarking activities and continuous improvement implementation in all the company. Create a built to last company.
-
-
-
ML Industries, Inc Planta Fco I. Madero
-
Motor Vehicle Manufacturing
-
1 - 100 Employee
-
Director Of Manufacturing
-
Sep 2018 - Oct 2019
Manage 3 plants located around Torreon area. Main goals: Achieve budget, business growth including new businesses, implement cost saving programs, develop the management staff to make sure we will have a successful and flawless launches in every new business. Improve overall efficiency, external quality, certify the Madero plant with ISO IATF, keep San Pedro with this same certificate, implement OEE to track real efficiency in the plant, improve actual MPS operational system. Improve actual HR system to make this organization in one of the best places to work within Torreon area. Mfg. Process. Cutting and sewing process for airbags and trim covers. Manual sewing for steering wheels Show less
-
-
-
Delphi Technologies
-
United Kingdom
-
Motor Vehicle Manufacturing
-
700 & Above Employee
-
Plant Manager
-
Oct 2016 - Sep 2018
Manage Operational Business, responsible for manufacturing, quality, production control and logistics, maintenance, manufacturing and industrial engineering, new launches, lean manufacturing, purchasing, human resources and finance. Main goals: Achieve budget including 6% manufacturing performance improvement year over year, Operations Income improvement according to the sales and mix goal at the budget, obtain Ford Q1 certification, obtain BIQS GM certification, obtain ISO IATF quality certification, improve 30% customer quality performance year over year, improve OEE 5% year over year, implement new Delphi lean manufacturing system, implement VSM, reduce inventory down to 18 days on hand, build a committed and responsible self-motivated staff team able to lead and create the best place to work in Juarez. Mfg. Process. Injection molding & assembly process to make injectors, smart remote actuators, solenoids, speed sensors & electronic valves for the automotive industry Show less
-
-
-
Johnson Electric
-
Hong Kong
-
Appliances, Electrical, and Electronics Manufacturing
-
700 & Above Employee
-
Director Of Operations
-
Sep 2015 - Aug 2016
Start up a new plant and consolidate the brand new first JE plant in Zacatecas. Manage Operational Business, responsible for administration, production, quality, logistics, maintenance, engineering, human resources and controlling. Main goals: Develop foundations to establish a world class company for the automotive industry. Startup the project management department. Startup of 8 different programs at the same time (Nissan GM as tier 1) and others as tier 2. Startup the student training program with an investment of 4.5 Mio USD. Mfg. Process. Injection molding, Stamping & Assembly process for electric motors Show less
-
-
-
TS Tech Americas, Inc.
-
United States
-
Motor Vehicle Manufacturing
-
500 - 600 Employee
-
Plant Manager
-
Feb 2010 - Aug 2014
Manage Operational Business, responsible for administration, production, quality, logistics, maintenance, engineering, human resources and controlling. Main goals: Improve current operation for both Tricon plants. According to company goals participate to develop business planning activities to make sure company will achieve future TSTech main goals. Make sure that Quality, Delivery and Cost objectives will be followed according to company requirements Manage Operational Business, responsible for administration, production, quality, logistics, maintenance, engineering, human resources and controlling. Main goals: Improve current operation for both Tricon plants. According to company goals participate to develop business planning activities to make sure company will achieve future TSTech main goals. Make sure that Quality, Delivery and Cost objectives will be followed according to company requirements
-
-
-
MAHLE
-
Germany
-
Motor Vehicle Manufacturing
-
700 & Above Employee
-
Plant Manager
-
Jun 2007 - Jan 2010
Manage Operational Business, responsible for administration, production, quality, logistics, maintenance, engineering, human resources and controlling. Main goals: Develop the business plan for five years, implement the MAHLE German culture in all the organization, and maintain the quality certification for ISO-TS 16949 system. Guide the company for growth according to the strategic sales budget and planned operational result Manage Operational Business, responsible for administration, production, quality, logistics, maintenance, engineering, human resources and controlling. Main goals: Develop the business plan for five years, implement the MAHLE German culture in all the organization, and maintain the quality certification for ISO-TS 16949 system. Guide the company for growth according to the strategic sales budget and planned operational result
-
-
-
Condumex
-
Mexico
-
Appliances, Electrical, and Electronics Manufacturing
-
700 & Above Employee
-
Plant Manager
-
Nov 1989 - Jun 2007
Manage Operational Business, responsible to transfer and consolidate Dana Muskegon and Richmond plants in the Saltillo facility. Move Monterrey (Camisa) plant to Saltillo facility. Close old Monterrey plant and finish all labor relation with all the union and non union personnel. Obtain the ISO-TS 16949 quality certificate and start up operation in Saltillo plant. Manage Operational Business, responsible to transfer and consolidate Dana Muskegon and Richmond plants in the Saltillo facility. Move Monterrey (Camisa) plant to Saltillo facility. Close old Monterrey plant and finish all labor relation with all the union and non union personnel. Obtain the ISO-TS 16949 quality certificate and start up operation in Saltillo plant.
-
-
Education
-
IPADE Business School
D1, Business Administration and Management, General -
Instituto Tecnológico y de Estudios Superiores de Monterrey / ITESM
Master of Business Administration (MBA), Marketing -
Universidad Panamericana
Bachelor's degree, Industrial Engineering
Community
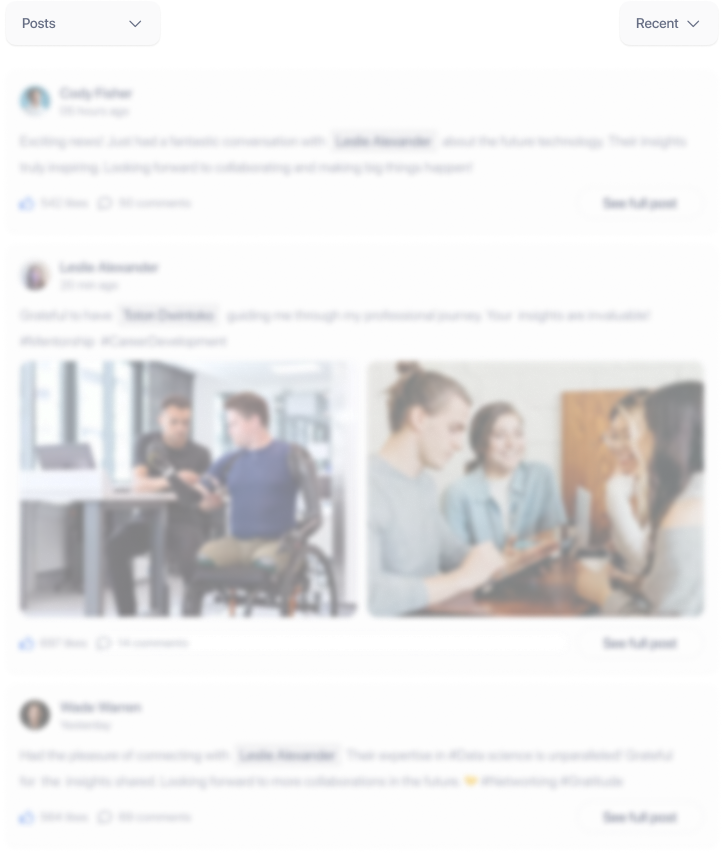