Francisco Javier Gamez Cavazos
Quality Engineer Customer Service at NISSEI ADVANTECH MEXICO S.A DE C.V- Claim this Profile
Click to upgrade to our gold package
for the full feature experience.
Topline Score
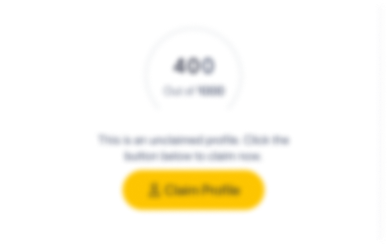
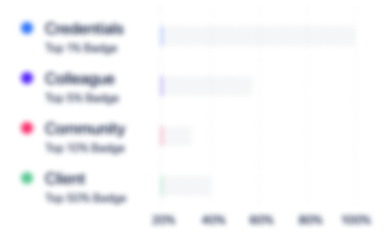
Bio


Credentials
-
CQI-9 Evaluacion del sistema de tratamiento termico.
Plexus Training SystemSep, 2012- Nov, 2024 -
Internal Auditor TS16949:2009
TACJul, 2010- Nov, 2024
Experience
-
NISSEI ADVANTECH MEXICO S.A DE C.V
-
Mexico
-
Automotive
-
1 - 100 Employee
-
Quality Engineer Customer Service
-
Oct 2016 - Present
Leading action plans for corrective actions resulting from customer complaints, scheduling visits to the United States with our clients in order to know our weakness and strengthen in their perspective, as well as the generation of action plans based on the methodology of problem solving.ResponsibilitiesMission of the Position: Verify and supervise that the product in the customer's plant meets the previously established quality requirements.Activities: • Analyze any factors external to the product that could affect the quality of the product (storage, handling or assembly at the client's plant). • Provide technical support to the customer regarding quality problems related to the automotive components of the company.• Look for alternatives to solve any problem related to the product. • Constantly in contact with quality or production staff of the client to attend to their requests. • Explore and know the customer's production line. • Line assembly assistance to operational staff, supervisors and SQA. • Guarantee management. • Monitoring and communication with the client. • Preparation of reports. • Report incidents encountered by the customer, solutions offered and handling suspect material.
-
-
Quality Engineer Injection Plastic
-
Jan 2015 - Present
Ensure that the Quality system works efficiently in the Plastic Injection process; complying with each of the standards defined to ensure a reliable process, product and service for the satisfaction of customers, through Quality Performance Monitoring, savings projects (Kaizen). Focused on eliminating repetitive problems, reducing costs and ensuring the effectiveness of countermeasures implemented based on root cause analysis with the multidisciplinary team. (Yokoten).Activities:• Implement the Quality Management System (QMS)• Implementation of Improvements (Savings Projects $) • Attention to complaints and claims of the Client.• Development of product specifications. (Inspection Standards). • Participation in the development of packaging specifications. • Development of work procedures and instructions. • Development and approval of first parts, parts of new projects • Continuous improvement project follow-up. (Kaizen)• Coordination and Supervision of the personnel in charge. • Coordinate the control and compliance of the calibrations and / or verifications of the measurement equipment. • Control products and nonconforming parts of the area (Quarantine and nonconforming product area). • Establish and document the acceptance criteria of the products.• Coordinate the product inspection process, as well as its statistical analysis • Responsible for the preparation and updating of process control plans. Activity with the multidisciplinary team of the process.
-
-
-
Metalsa
-
Mexico
-
Motor Vehicle Manufacturing
-
700 & Above Employee
-
Quality Control Specialist
-
Jan 2010 - Nov 2014
Support Quality System Management ISO TS 16949 & ISO 14000 • External, internal & Layered Process Audits.• Following to corrective actions from external and internal audits• Support to corrective actions from Customer Complaints• Documents Control (Visual Aids, Process Sheets, Drawings)• Support to implementation of projects using APQP. Stamping Process • Assure the quality of the product manufactured on stamping process• Develop quality gates on shop floor to increase the effectiveness of detection of defects.• Followings to PPAP’s and APQP process for new products• Reduction of PPM´s using SPC and TPS methodology.• Development of savings and improvement projects. Roll forming and Plasma Cut Process / Heat Treatment • Assure the quality of the product manufactured on Roll forming and Plasma cut process / Heat treatment.• Develop quality gates on shop floor to increase the effectiveness of detection of defects.• Followings to PPAP’s and APQP process for new products• Reduction of PPM´s using SPC and TPS methodology.• Development of savings and improvement projects. •ISO/TS 16949 Internal Auditor, Periodic internal cross audits (Quality, Operations, Logistics, Maintenance & Tooling Departments) o LPA. Inspection & Rework Department •Create and standardization of inspection and rework methods for quality assurance. • Nonconformance and suspect material control.
-
-
Quality Specialist (Steel Incoming Inspection).
-
Jul 2008 - Dec 2009
Steel Incoming Inspection •Quality assurance of dimensional, attributes, mechanical properties, chemical properties.• Create report and follow up of Nonconformance product to Steel (Ternium Guerrero & Churubusco).• Steel supplier change / analysis of impacts in process. • Steel characteristic comparison for critical supply cases / create internal deviations for quality assurance.• Department procedures. • Nonconformance control.Intern (before completing the University). •Analyze process for generating work procedures, inspection records and inspection frequencies. • Understanding quality specifications to provide it with the technical staff.the report defects found in steel incoming inspection area to generate notifications to the provider and follow up to corrective from the suppliers.
-
-
Education
-
Universidad del Norte
IIA, Ingeniero Industrial Administrador
Community
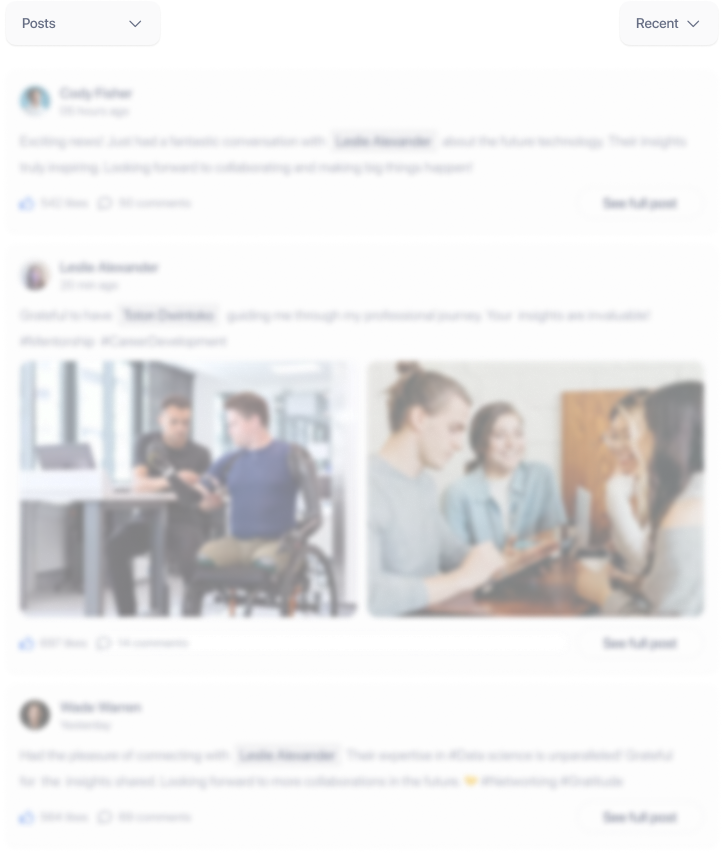