Francis Naylor
Quality, Health & Safety Manager at Wilson Power Solutions Ltd- Claim this Profile
Click to upgrade to our gold package
for the full feature experience.
Topline Score
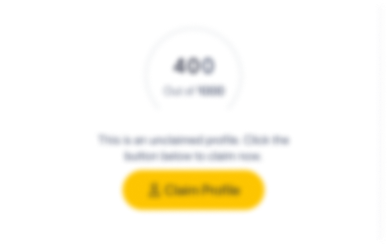
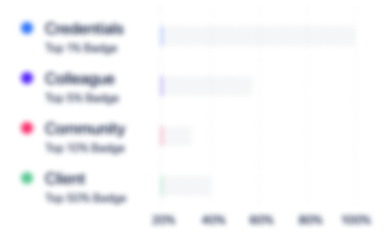
Bio

Paul Leeuwerke
Francis's knowledge and experience on the design, manufacturer and adaptation of electrical MV distribution switchgear is unchallengeable. His focus on detail, team work and customer service has assisted Yorkshire Switchgear --> Merlin Gerin --> Schneider Electric in providing market leading switchgear for the past three decades from their factories in Leeds (Meanwood Road and now Jack Lane) and installed in UK and worldwide Electrical Distribution Networks. Should you have the opportunity to employ him, snap him up before your competitors do....

Paul Leeuwerke
Francis's knowledge and experience on the design, manufacturer and adaptation of electrical MV distribution switchgear is unchallengeable. His focus on detail, team work and customer service has assisted Yorkshire Switchgear --> Merlin Gerin --> Schneider Electric in providing market leading switchgear for the past three decades from their factories in Leeds (Meanwood Road and now Jack Lane) and installed in UK and worldwide Electrical Distribution Networks. Should you have the opportunity to employ him, snap him up before your competitors do....

Paul Leeuwerke
Francis's knowledge and experience on the design, manufacturer and adaptation of electrical MV distribution switchgear is unchallengeable. His focus on detail, team work and customer service has assisted Yorkshire Switchgear --> Merlin Gerin --> Schneider Electric in providing market leading switchgear for the past three decades from their factories in Leeds (Meanwood Road and now Jack Lane) and installed in UK and worldwide Electrical Distribution Networks. Should you have the opportunity to employ him, snap him up before your competitors do....

Paul Leeuwerke
Francis's knowledge and experience on the design, manufacturer and adaptation of electrical MV distribution switchgear is unchallengeable. His focus on detail, team work and customer service has assisted Yorkshire Switchgear --> Merlin Gerin --> Schneider Electric in providing market leading switchgear for the past three decades from their factories in Leeds (Meanwood Road and now Jack Lane) and installed in UK and worldwide Electrical Distribution Networks. Should you have the opportunity to employ him, snap him up before your competitors do....

Experience
-
Wilson Power Solutions Ltd
-
United Kingdom
-
Appliances, Electrical, and Electronics Manufacturing
-
1 - 100 Employee
-
Quality, Health & Safety Manager
-
Jun 2022 - Present
-
-
Special Projects Manager
-
Sep 2020 - Jun 2022
-
-
-
Schneider Electric
-
France
-
Automation Machinery Manufacturing
-
700 & Above Employee
-
Customer Advocate
-
Oct 2014 - Sep 2020
• Single point of contact for all customer complaints.• Ensure reported post-delivery problems a rectified in a timely manner.• Product investigation and closing reports using 8D / 5 Why’s root cause analysis.• Validate corrective and preventive actions resulting from analysis of the returned products.• Meet the customer if needed and share the findings of the investigation and close the complaint.• Provide necessary feedback to all relevant internal departments and ensure corrective actions are put in place to prevent futurereoccurrence of the problem. Show less
-
-
Engineering Manager - Medium Voltage and Transformers
-
Feb 2010 - Oct 2014
Leading a team of twelve engineers covering all aspects of the engineered to order MV products.Investigate customer requirements to ensure they are feasible and assess the implications on manufacture.Compile cost estimate for the proposed design solution, ensuring resource and proposed man-hours are calculated and deliverable, factoring in current and on-going work to ensure build is achievable.Compile cost estimate for the proposed design solution.Prioritise work in date order relating to the manufacturing program.Liaise with Customers / Sales Engineers ensuring any technical queries regarding design; assembly and installation of the product are answered.Liaise with other subsidiary sites with reference to the design of group products ensuring compatibility of range.Ensure efficient and timely processing of all orders, which require engineering input.Quality Value Engineering - cost savings by design / assembly.Product evolution/improvements.Project planning of major design improvements.Supplier selection. Show less
-
-
Project Manager – Medium Voltage Primary Product Development (GenieEvo 2000 Amp)
-
Sep 2007 - Feb 2010
Responsibility for a team of fourteen engineers covering design, planning, QA, industrialisation and workshop prototyping and test.• Validate the project time scales and budget in line with the original project file and ensure the year-end objectives are achieved re time / cost.• Ensure that the technical challenges of the project are well understood.• Voice of the customer (VOC). Capture the customer's expectations, preferences and aversions.• Consider various unit architectures and ensure that the product meets our customer expectations.• Develop a good working relationship with the companies Technology Centres.• Working with the Design Engineers and Business Development Manager develop a clear strategy for the deployment of thecompany’s core project tools.• Produce accurate project plan and communicate progress to date.• Manage the project cost file (€2.1 Million budget).• Ensure the project team has the necessary skills and training to conduct their role effectively.• Work closely with the Purchasing and Procurement teams.• Failure Mode and Effects Analysis (FMEA).• Type testing at Schneider Electric’s in house facility – Volta, Grenoble, France.• Lead the Industrialisation team, production line layout and assembly instructions.• Produce product decision trees.• Product Hand Over matrix.Key successes of the project:• First 2000A Switchboard – Equinix London Data Centre 5 (LD5) £1.8 million phase 1, £1.95 million phase 2.• First 2500A Switchboard – Bahamas Electricity (Baha Mar Ltd – Hotel / Casino Complex) £2.4 million.• Bulk contracts awarded by Western Power Distribution and Scottish Power. Show less
-
-
Standard Contracts Manager Medium Voltage and Transformers
-
Jun 2004 - Sep 2007
Responsibility for a team of twelve engineers / technicians.Ensure efficient and timely processing / contracts management of all standard Medium Voltage and Transformer orders. Responsibility for leading the delivery of MV projects. Approximately 60% of these were delivered into DNO’s with remaining 40% feeding into Independent Connection Providers, HV contractors and private networks.Lead the management of bulk contracts and ensure close working relationship with customers are maintained and developed within these key accounts.Participate in negotiations of Bulk Contracts, extensions / price variations.Contract planning and execution.Production planning and scheduling using complexity model.Ensure payment is made on time and in line with agreed terms and conditions.Implementation of SAP - Process Mapping of the complete production system from tender enquiry to order process, production build, despatch and invoice.Transfer and rationalisation of all part numbers and bill of materials into the new system.Create new routings and build milestone measures for the new live production schedule.Implementation of just in time part process to reduce stock levels. Show less
-
-
Offer Manager (Primary Tendering)
-
Mar 2002 - Jun 2004
• Responsibility for a team of nine engineers, tendering function for all MV Primary / Secondary Products.• Implementation of a standard offer, creation of standard panel types with pre-engineered drawing layers / pre-costed bills ofmaterial.• Creation of a decision tree configurator, ultimately this led to a vastly improved response time in compiling tenders. Should theorder be won, the bills of material could then be copied in to the MRP system thus reducing engineering time.• Investigate feasibility of customer requested product adaptations, to allow a decision to be made on whether to proceed.• Approve tender price / costing estimates.• Ensure that all enquiries that fall outside the scope of the business are referred to an alternative subsidiary as quickly aspossible.• Monitor and report on the achieved margin for all non-standard product orders as compared to the tendered margins, reporton the variances.• Be proactive in eliminating any contract-related issue that might lead to non-payment of invoices. Show less
-
-
Current Product Design Manager
-
Dec 1992 - Mar 2002
• Responsibility for a team of eighteen engineers / technicians.• Manage all aspects of contracts design, wiring and works manufacturing instructions.• Own and maintain the commercial product offer, with respect to design, ease of assembly and cost.• Investigate customer requirements to ensure they are feasible and assess the implications on manufacture.• Compile cost estimate for the proposed design solution.• Prioritise work in date order relating to the manufacturing program.• Liaise with customers / Sales Engineers ensuring any technical queries regarding design; assembly and installation of theproduct are answered.• Liaise with other subsidiary sites with reference to the design of group products ensuring compatibility of range. Show less
-
-
Design Engineer (Engineered to Order)
-
1986 - Dec 1992
• Design of technical solutions in line with customer requests.• Took part in mechanical design feasibility studies.• Production of layout drawings for possible assessment by external customers and technical departments.• Detail of component drawings for manufacture.
-
-
Mechanical Apprentice
-
Jun 1982 - Jun 1986
• Onsite installation testing and commissioning.• Product development workshop training and testing.• Three months in each production cell.
-
-
-
M. Sedgwick & Co Ltd
-
Leeds, England, United Kingdom
-
Mechanical Apprentice
-
Jun 1981 - Jun 1982
-
-
Education
-
Leeds Beckett University
BTEC Higher National Certificate (HNC) in Mechanical / Production Engineering. (Including additional, Mechanical Engineering -
Airedale and Wharfedale College (Now Leeds City College – Horsforth Campus)
BTEC Ordinary National Certificate (ONC) in Mechanical / Production Engineering., Mechanical Engineering
Community
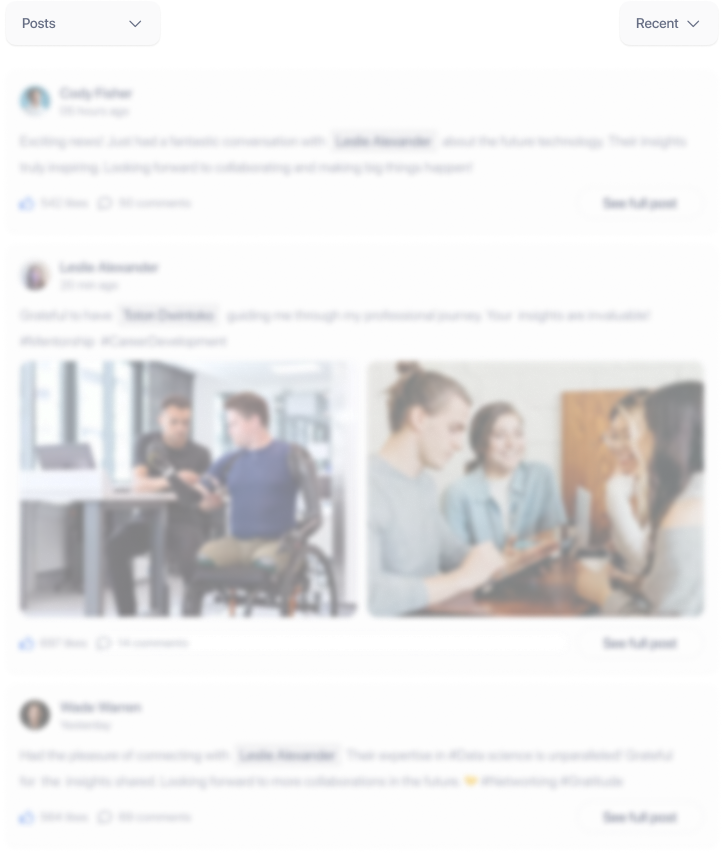