François Vandaele
Senior Consultant at Quoretex- Claim this Profile
Click to upgrade to our gold package
for the full feature experience.
-
English -
Topline Score
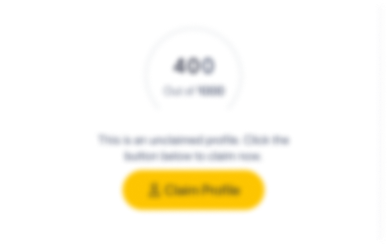
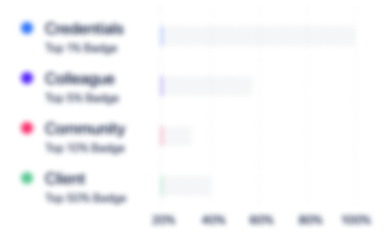
Bio


Credentials
-
Greenbelt
BCFJun, 2014- Nov, 2024
Experience
-
Quoretex
-
France
-
Biotechnology Research
-
1 - 100 Employee
-
Senior Consultant
-
Apr 2020 - Present
-
-
-
MaSTherCell
-
Belgium
-
Biotechnology Research
-
1 - 100 Employee
-
Project Leader chez MaSTherCell
-
Apr 2020 - Oct 2020
Project Leader at MaSTherCell Gosselies to build a commercial plant for therapeutic cells Project Leader at MaSTherCell Gosselies to build a commercial plant for therapeutic cells
-
-
-
Cadres en Mission - Portage
-
France
-
Human Resources Services
-
300 - 400 Employee
-
Project Leader chez MaSTherCell
-
May 2019 - Mar 2020
Project Leader at MaSTherCell Gosselies to build a commercial plant for therapeutic cells Project Leader at MaSTherCell Gosselies to build a commercial plant for therapeutic cells
-
-
-
Expleo Lifesciences & Healthcare (Formerly Assystem Care)
-
France
-
Pharmaceutical Manufacturing
-
1 - 100 Employee
-
Senior Consultant - Deviation, Team and Project Management
-
Nov 2017 - Mar 2019
Context and mission:-The Biotech Quality Group started on site with a fixed price package to close an amount of deviations in 6 months time.-Second part of the project was rolled out as contracting a team of about 20 people and performance commitment. I joined during that 2nd phase.Roles and responsibilities: Deviation, Team and Project Management-Mission started by operational deviation investigation as part of manufacturing team (2 months): .Pooling .Sterile filtration .Filling (RABS) .Lyophilisation .Capping .Visual inspection .Utilities .Calibration-Mission went on with transversal consultant team management (50% time) added to investigations (50% time) during 4 months: .On boarding of newcomers in consultants’ deviation team .Interface with customer management to control backlog reduction .Performance KPI, weekly meetings and monthly Steering Committee with client management .Develop tools to share KPIs and make them endorsed by whole organisation .Ensure progresses according to site engagement towards authorities-Third part of the mission is focused on major deviations and mentoring (6 months): .Investigate complicated topics such as: .HVAC failure of one whole building .Impact of a standard non-compliance for freeze dryers .Challenge environmental monitoring in sterile areas .Long lead deviations .Support to Technical ServicesResults:-Backlog under control and reduced down to 2 weeks operation by mid-July.-Performance: investigate 1 deviation per person and per day for investigators.-And close 1.7 deviations per person and per day for QA.-Propose remediation actions and simplification.-Reallocate resources on line with backlog evolution in 4 manufacturing buildings.-Handle CAPA for technical services such as : .Incubation room regulation issues .Hidden surface in mixing tanks .Build up and deliver training “Lyo for dummies” for investigation team. Show less
-
-
Senior Consultant - URS for Hospital Central Pharmacy extension
-
Oct 2017 - Oct 2017
Context and mission:- Write URS for Hospital Central Pharmacy to double surface in order to regroup all magisterial anticancer preparations (25 000 per year).- Sterile preparation in isolators.- Collect customer needs: pharmacists, technical services, architects, infra structure, engineering, clinical trials, bio safety, validation, EHS.- Limit impact at minimum on routine activities and patients’ treatment during extension works.- Scope submitted to SwissMedic and public enquiry.Roles and responsibilities: URS- 500 sqm extension.- Class B, C and D rooms and HVAC.- Isolators under negative pressure.- Psychotropic compounds handling.- Pharmacy offices and lab upgrade.- Include Hospital procedures and Ways of Working.- Flow sketches.- Backup and Continuity Plan.Results:- T0: interviews and data collection.- T0 + 1 month: URS submission to Hospital key stakeholders.- T0 + 1.5 month: URS approved. Show less
-
-
Senior Consultant - Apollo Maturity Diagnostic and Sustainability
-
Feb 2017 - Sep 2017
Context and mission:-Production units’ management has changed (50 % replaced – 3 buildings – more than 500 p). The Technical Services management was completely renewed (and half of them were newcomers)-Key objectives were to reinforce quality mind-set and to develop technical skills-Mission started by a full Apollo Maturity Diagnostic on all technical activities-Diagnostic report was presented to leadership team and road map was designed for sustainability program-Sustainability program was rolled out during 7 months-The 2 steps mission was designed as fixed price packagesRoles and responsibilities: Diagnostic and Sustainability-Mission started by a full Apollo Maturity TM Diagnostic on all technical activities: 3 consultants – 1 month-2nd step Sustainability program consists on: .Mentoring .Learning program design .Workshops to design and set up Technical Services organization-An action log collected gaps, remediation steps, learning needs, training courses and mentoring topics: 63 actions logged-4 Key mentees were identified to improve the Quality & Technics performance: Maintenance, QA, Reliability and Engineering-Competencies assessment for each of the 4 mentees: self-assessment, manager assessment and progresses follow up-Develop selected competencies with a customised mentoring program based on: problem solving, shop floor gemba, technical lesson, shadowing to improve behaviours-Support managers’ qualification on deviation process: technical data collection, root cause analysis and writing skills-Build-up 4 training modules: Project Management, Handover, Good Engineering Practices, Quality Mind-set and Maintenance Strategy. Modules given to teams selected among the whole production unit-4 workshops to design the Technical organisation with its management and their partners: Vision / Mission, Roles & Responsibilities, Way of working, Team rules, Interfaces & Communication Show less
-
-
Senior Consultant - Apollo Maturity Diagnostic and Workshops
-
Jul 2016 - Jan 2017
Context and mission:‒ Develop Apollo maturity TM model for BQG: a tool designed to assess site organisation maturity. This tool was awarded in 2013 with Innoviris Brussels Capital Rise price (young innovative company). Join the team as an Apollo practitioner.‒ Build up the Apollo pack fast track for Handover in projects.‒ Design a module for Learning BQG package “Still and WFI”. Module given to customer mentees and all BQG consultant staff.‒ Realize a deviation handling benchmark for a Swiss customer: Recurrence, Criticality, Deviation vs Event, Release.‒ Make a diagnostic for a Swiss customer on his Qualification & Verification documentation. Propose IT solutions to prevent re-writing and process reengineering with mentoring accompaniment.‒ Animate a workshop on Risk Analysis applied in Qualification in a customer plant.‒ Design and animate a workshop on Handover in a customer plant. Show less
-
-
Senior Consultant - Technics in Quality to improve efficiency
-
Jul 2015 - Jul 2016
Context & mission:-Production unit stopped during several months to realize key improvements following an inspection-Management wanted to implement & develop QA oversight for engineering & maintenance activities-Realize a diagnostic on Quality & Technics, management was looking for a focus diagnostic on 4 processes: Handover, Maintenance, Calibration & Measurement, Q&V-Design a road map to mentor 4 managers and to have a QA oversight on engineering & maintenance-Help the unit in designing Quality & Technical future organisations-Mission was designed as a fixed price package including data collection, mentoring & organisation workshopsRoles & responsibilities: Diagnostic & Mentoring-The diagnostic based on Apollo maturity model focused on: . Gap analysis between Basic of Design & cGMPs . Interviews of key stakeholders & actors . Documentation data collection: SOP, Guidance, KPI-An action log collected gaps, remediation steps & mentoring topics: 25 actions logged-Key mentees were identified to improve the Quality & Technics performance-Competencies assessment for each of the 4 mentees: self-assessment, manager assessment & progresses follow up-Focus on HVAC design upgrade to improve Environmental Monitoring & response to FDA observation. Act as a unit embedded expert: deviations, corrective actions, project definition, dry fog problem solvingResults:-Production unit Maturity diagnostic in 2 months-Road map defined with engineering documentation oversight-Mentor Quality & Technical managers with measured progress-Better collaboration between Quality & Maintenance: deviations closed quicker, common problem solving sessions-Build a set of KPIs to follow maintenance activities & GMP respect-Act as a technical referent inside manufacturing unit: produce a FAQ list to be shared with other units-Dry fog cycles back to routine. Re-engineer HVAC balancing to meet GMP requirements-Design a training HVAC for Dummies given to all unit management staff Show less
-
-
Senior Consultant - Root Cause Analysis
-
Jul 2014 - Jun 2015
Alignment to File : Root Cause analysisContext and mission:- Based on current initiatives: File gap assessment, remediation plan and root cause analysis, the management was looking for an innovative way of addressing the root cause analysis and designing the road map of implementation for targeting sustainability in this matter.- The Alignment to File gap analysis compared operational documents to Regulatory File regarding: - QC activities from release, monitoring to quality decision tests - Manufacturing activities from cell culture, purification, adsorption, formulation to filling - Commercial stability studies- The root cause analysis program is a critical phase following gap analysis in order to validate and complete the preventive project. Therefore change management and good alignment between all initiatives to focus on add value and return of investment required very good project management and a clear strategy.Roles and responsibilities: Root Cause Analysis (RCA)- Select a representative group of vaccines.- Analyze data to select a limited number of valuable gaps to perform RCA.- Organize and manage RCA Workshops with teams of Subject Matter Experts (Manufacturing, QC, QA, RA, Validation and Product & Process).Results:- Select 0.1% of gaps to conduct RCA. Gaps selected are representative of Product, Process area, Department involved in correction, Document to correct and Type of gap. That selection gives the maximum impact with minimum effort.- Deliver a set of root causes and corrective / preventive actions to improve and simplify document process for operation and registration.- Design a Database in order to : - collect all information - regroup same type of gaps in improvement areas - make easier remediation plan follow up - produce Key Process Indicators (KPI)- Develop and implement a pilot text mining techniques to allow a drastic time reduction during remediation prioritization by the Alignment to File team (time divided by 4). Show less
-
-
-
Delpharm
-
France
-
Pharmaceutical Manufacturing
-
700 & Above Employee
-
Senior Project Manager
-
Feb 2014 - May 2014
Role and responsibilities:- Strategic projects management- Gel formulation workshop and 2 packaging lines (1000 m²) for FDA market- Technical coordination : suppliers, engineering, manufacturers- Transversal value stream project leadership : manufacturing, quality, maintenance, industrialization, supply chain, finance, procurement (15 people)- Qualification coordination- Start up- Technical batch- Registration batches- Greenbelt with BCF Consultants : Lean – 6 sigma, data analysis with Minitab software Show less
-
-
Plant Director
-
Apr 2012 - Feb 2014
Role and responsibilities:- Business Unit – 65 p – Hormonal gels :- Manufacturing, Quality, Supply Chain, Technical, Finance, Human Resources- Complete flow from order to finished products invoice- Turn Over : 13 M€- Volumes increase by 20 %- Customer service improvement (OTIF)- ANVISA site approval : Solving 2 pending major issues: cleaning validation and purified water loop qualification- New customer introduction : Quotation, approval audits, analytical methods transfer, manufacturing process transfer with customer regulatory service, new vial filling validation, cleaning validation due to new recipes introduction, registration batches- 2 new packaging lines : project leadership, AFMPS- Change of logistic sub-contractor and move sampling booths back to the plant- Build up site leadership team- Embed new acquired site in group network- Check with the customer the discrepancies between registration files and operational practices (Batch record, SOP, CoA)- Manage deviations to release batches in due time- Insure root cause analysis for abnormal batches and final decision with the QP Show less
-
-
-
GSK
-
United Kingdom
-
Pharmaceutical Manufacturing
-
700 & Above Employee
-
Senior Manager Technical Services
-
Feb 2006 - Apr 2012
-
-
-
Abbott
-
United States
-
Hospitals and Health Care
-
700 & Above Employee
-
Industrial Engineering Manager
-
1997 - 2006
Role and responsibilities: - Project Management: Building, revamping, sterile area, process equipment, packaging lines, laboratory, offices, utilities… - Management of 2 project coordinators - Site master plan elaboration : re-design warehouse and storage flow, QC lab re-engineering - Investment budget management - Project teams construction and lead - Collect user needs and realize feasibility studies - Write down users specifications and financial aspects - Quotation, negotiation and suppliers’ selection - Users and maintenance training - Follow up and projects improvement : acceptance, installation, start up, validation and ramp up - Whole sterile area rebuilding managed by site team: bulk preparation, 2 lyophilizers, 1 filling line. 6 months shutdown, requalification included - Member of site Class A certification team (Oliver WIGHT): Sales & Operation Planning, performance measurement. Site certified in 2005 - ERP deployment in QC lab : planning (BPCS) - Test new artworks on packaging lines and then improve QC controls accuracy (reception and in process control) - Speaker during US Corporate conferences : packaging, on-line and in process control Show less
-
-
-
Bestfoods
-
Manufacturing
-
1 - 100 Employee
-
Project Manager
-
1993 - 1997
-
-
Maintenance & EHS Manager
-
Apr 1991 - 1993
-
-
-
Nestlé
-
Switzerland
-
Food and Beverage Services
-
700 & Above Employee
-
Project Manager
-
1988 - 1991
-
-
Education
-
Institut catholique d'Arts et Métiers / ICAM
Ingénieur, Généraliste -
École Supérieure d'Électricité / Supelec
Ingénieur, Electricité Industrielle
Community
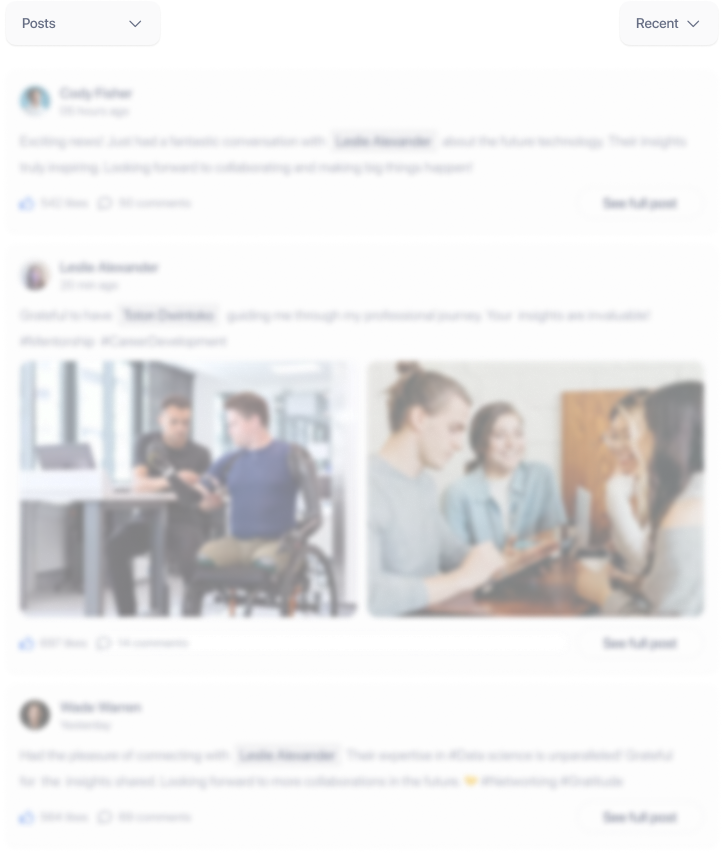