Florin Alexandru Marin
Supply Chain Logistics Manager at AgroConcept - New Holland Agriculture- Claim this Profile
Click to upgrade to our gold package
for the full feature experience.
Topline Score
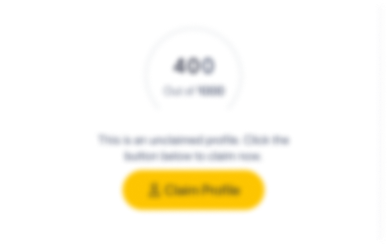
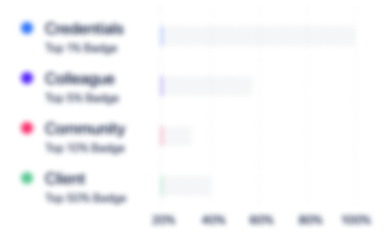
Bio


Experience
-
AgroConcept
-
Romania
-
Machinery Manufacturing
-
1 - 100 Employee
-
Supply Chain Logistics Manager
-
May 2018 - Present
Management of machine imports (starting with the smallest implements and up to the largest combines, no spare parts).Finding forwarders, price negotiation. Managing budgets and deadlines.Management of machine (complete agricultural machines/no spare parts) deliveries to the end customer.Finding forwarders, price negotiation. Managing budgets and deadlines.Management of Dealer Arrival Report and Pre-Delivery Inspection activities.
-
-
Product Manager
-
Jan 2016 - Apr 2018
Creating all the basic procedure sets for all after sales depts.Creating detailed procedure sets for all service activities, all of the Pre-Delivery Inspection activities.Design and creation of all after sales official forms (from concept, data to be included/excluded to printing the forms) based ondiscussions with the manufacturers representatives (7 major manufacturers represented, each with it's own requirements).Design and creation of all warranty forms - one form to cover all the possibilities and requirements.Creating the job descriptions for each of the job titles in the after sales depts.Creating training documentation.Training - periodical (with individual team leaders or individual branch service team)Arranging, preparing and launch of the extended warranty program, creating the info material for sales team + sales team trainingsessions.Creating presentation and info material for after salses depts. After sales depts. training. General info meeting showing the product andsome of it s advantages. Presenting sales strong points and pricing explainedCreating all extended warranty forms.Ensuring that all the supplier quality and excellence demands are met (importer terms set for each supplier), specifically on theprocedural side of the business.Creating semi automated reports for the main after sales depts.Focus on the warranty side (the part of the business that is under the most scrutiny and also the part of the business with the strictestrules).Preparation for the importer audit (supplier checking that all demands are met, all paperwork is in order and all claims are properlymanaged). Show less
-
-
-
Titan Machinery România
-
Romania
-
Farming
-
1 - 100 Employee
-
Warranty Manager
-
May 2011 - Dec 2015
Establishing the warranty procedure set and implementation. Individual training with every team leader. Training each service team. Following the paperwork set required for each type of claim, placing claims and following until final payment. Managing Warranty Costs and reporting to Stakeholders. Establishing the warranty procedure set and implementation. Individual training with every team leader. Training each service team. Following the paperwork set required for each type of claim, placing claims and following until final payment. Managing Warranty Costs and reporting to Stakeholders.
-
-
-
BERGERAT MONNOYEUR
-
Machinery Manufacturing
-
700 & Above Employee
-
Logistics manager - spare parts
-
May 2007 - May 2011
Management of import activities. Maintaining proper stock levels. Forwarder negotiation. Creation of "translator software" between company proprietary software (CAT) and I.N.S. Intrastat software (reading data from CATERPILLAR software, generating the lines (variables as per rule set) and generating the final file form that is getting sent to INS. Effectively cutting down the processing time to less than a day (from what used to be 2-3 hours each day)creating anywhere from 4000 to 5000 distinct lines each month. Monthly I.N.S. “intrastat” declaration Show less
-
-
-
Avery Dennison Label and Packaging Materials
-
United States
-
Manufacturing
-
700 & Above Employee
-
Supply Chain Logistics Manager
-
Nov 2005 - May 2007
Management of import activities, export activities, internal deliveries.Management of budgets and deadlines, ensuring production requirements are always available while maintaining low costs.Identifying forwarders, contract negotiation. Ongoing contracts management. Customs paperwork and formalities.Managing the high volume of imports (1-2/day), exports (10-15individual imp/ day) and internal deliveries (20-30 / day).Creation of "automation software" for optimising logistics (no UI/ reads outputs from the industrial production software, identifiesproduction/finished goods requirements, checks against available stock, checks against min/max/reorder levels and generates orderquantities for each individual item, splits by supplier and even generates the order e-mails + txt list of order details (cut down processingtime to around 20 min/day) allowing for proper management of all logistics activities in the allocated time.Revising and adding to the logistics procedures set. Show less
-
-
Navision Implementation specialist
-
Apr 2005 - Nov 2005
Centralization of the aftersales departments requests relating to the new NAV implementation.Staying in touch with the implementing company, following requests, module testing, etc.Supervising the creation of a new "translator" program and UI. (Software links in real time the industrial production software and NAV,*considerably cuts down processing time.Creating a detailed "user manual" for both NAV implementation and the "translator". Manual eliminates the need for basic training forregular users. Show less
-
-
Warehouse Supervisor
-
Mar 2004 - Apr 2005
Establishing a proper warehouse (location, preparaing).Creating the procedures set used for warehiuse operation.Implemention of the procedures set and warehouse team training (new custom software linked directly with the induatrial productionsoftware used by the company).Defining the minimum/maximum/reorder stock levels and implementation.Creating a set of rules to help set stock levels based on available stocks worldwide(intercompany) and sales forecasts.
-
-
Machine operator (production)
-
Dec 2003 - Mar 2004
Using the company provided design and printing software. Printing on a variety of materials using industrial thermal transfer printers
-
-
-
METRO Romania
-
Wholesale
-
300 - 400 Employee
-
Technical Representative and Sales Asistant (it products)
-
Mar 2001 - Aug 2001
Providing customers with advice (software/hardware). Making recommendations based on customer needs/budget. First receipt of warranty claims for it equipment. Basic level of tech support (for pre-assembled, sealed, and no os installed pc systems). Providing customers with advice (software/hardware). Making recommendations based on customer needs/budget. First receipt of warranty claims for it equipment. Basic level of tech support (for pre-assembled, sealed, and no os installed pc systems).
-
-
Education
-
University of Bucharest
Bachelor's degree, Computer Engineering -
Universitatea „Spiru Haret” din București
Bachelor's degree, Marketing/Marketing Management, General -
Scoala superioara comerciala Nicolae Kretzulescu
accounting & statistics, Economy and statistics
Community
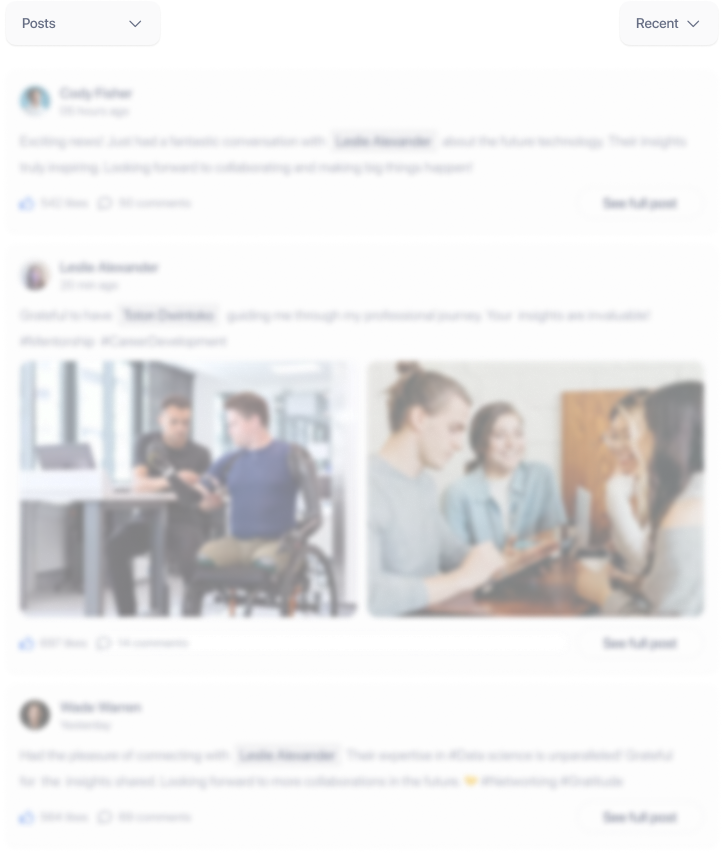