Firsada Adhari
Continuous Improvement Manager at NS BlueScope- Claim this Profile
Click to upgrade to our gold package
for the full feature experience.
Topline Score
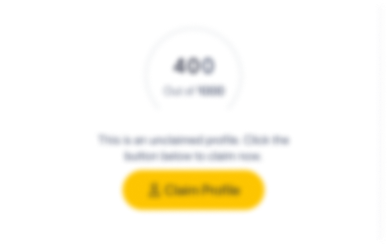
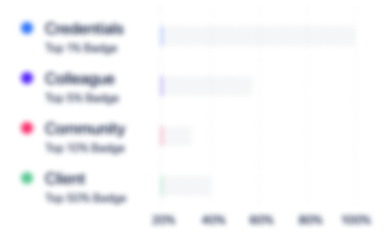
Bio

Tino Amsal
Strong in detail. Firsada perform detail work in his task. I work with him to build Solvent Recovery Facility. He accept all the task challenge to prove he can deliver the goals. Congratulations Firsada with the promotion. I am sure you'll be more succesfull in your carreer.

Tino Amsal
Strong in detail. Firsada perform detail work in his task. I work with him to build Solvent Recovery Facility. He accept all the task challenge to prove he can deliver the goals. Congratulations Firsada with the promotion. I am sure you'll be more succesfull in your carreer.

Tino Amsal
Strong in detail. Firsada perform detail work in his task. I work with him to build Solvent Recovery Facility. He accept all the task challenge to prove he can deliver the goals. Congratulations Firsada with the promotion. I am sure you'll be more succesfull in your carreer.

Tino Amsal
Strong in detail. Firsada perform detail work in his task. I work with him to build Solvent Recovery Facility. He accept all the task challenge to prove he can deliver the goals. Congratulations Firsada with the promotion. I am sure you'll be more succesfull in your carreer.

Experience
-
NS BlueScope
-
Singapore
-
Wholesale Building Materials
-
200 - 300 Employee
-
Continuous Improvement Manager
-
Sep 2018 - Present
To manage and facilitate CI activities and initiatives across the plants/departments to improve process capability, plant efficiency and reduce waste.Assist in data analysis with commercial team to identify improvement opportunities and work with team to deliver improvement projects To implement effective CI projects, using 5S, Kaizen, A3 and other lean manufacturing methodologiesMonitoring and driving overall plant efficiency to improve OEE (Overall Equipment Effectiveness)Take ownership for monthly manufacturing dashboard ensuring up to date data is correct and availableEffectively communicate plans and priorities and support teams in delivering key improvementsTo collect, monitor, evaluate and report on supporting data and subsequent utilization of data to CI ProjectsTo facilitate and formulate improvements hypotheses within A3 Thinking ProcessSupport deployment of Lean Tools such as 5S, Visual Factory Aids, Poka Yoke, to improve plant safety, quality and yield performance.Lead Weekly Manufacturing Project Alignment to validate that actions lead to desired performance improvements.
-
-
Senior Process Engineer
-
May 2010 - Aug 2018
Worked in process engineering area especially in surface treatment and in line painting area.Duties: Making improvement in safety, production and quality, review/establish procedures and system of work, mantain process and equipment reliability, supervise troubleshooting and guidance for problem solving.Responsibilities & duties Improvement in production area to increase safety performance, yield and OEELead special project in ownership area (Design, Fabrication and Installation) which related to safety, quality and productivity.Reviews and monitors production process to assure quality and adherence to requirements of standard procedures especially at Surface Treatment & Inline Painting area.Ensuring all relevant safety objectives (Hazard Register, COP, Critical Procedure) and legal requirements are observed and under controlledPrepare and review JSEA, ATWP, Isolation Procedure with maintenance team to ensure commissioning and shutdown activity event on target.Assist and verification equipment refer to Factory Acceptance Test (FAT), coordination with Maintenance & Engineering team Technical specification review and assist mechanical calculation Establish SOP, Guidance, Best Practices, Engineering Change Management, and Checklist related to safety, process, quality and environment Regularly train and educate operator for refreshment training especially in fire prevention system paint coater room, NIR Oven and Operational Paint Coater Room
-
-
-
PT Dharma Polimetal Tbk
-
Indonesia
-
Manufacturing
-
300 - 400 Employee
-
PPTE (Product, Process Tooling & Engineering) Section Head
-
Jun 2002 - May 2010
Responsibilities & duties Supervising and coordinating with Group Head for daily activities and troubleshooting at the shop floor Establish monthly report to summarize Cost Reduction Program (CRP), Breakdown Tools & Equipments, Line Improvements, Projects Achievements based on KPI and Monthly Activity Plan. Designing Fault Tree Analysis (FTA), Manufacturing Technical Quality Requirement (MTQR), Value Stream Mapping (VSM) Establish Process Quality Check Sheet (PQCS), PFMEA, Flow Process Plan, Working Instruction (WI) and setting machine parameter for new installed equipments before mass production Establish and analyzing capability equipment and process (Cp) Preventing, predicting, maintaining process tools in order to optimizing production activity to avoid line stop or breakdown tools. Responsible to managing crew activity for SS (Suggestion System) and QCC (Quality Control Circle) related to Kaizen and Lean Manufacturing Implementation
-
-
Education
-
Universitas Gadjah Mada (UGM)
Bachelor's degree, Teknik Mekanika Mechanical Engineering -
Polytechnic University of Indonesia
Associate's degree, Teknologi/Teknisi Teknik Manufaktur
Community
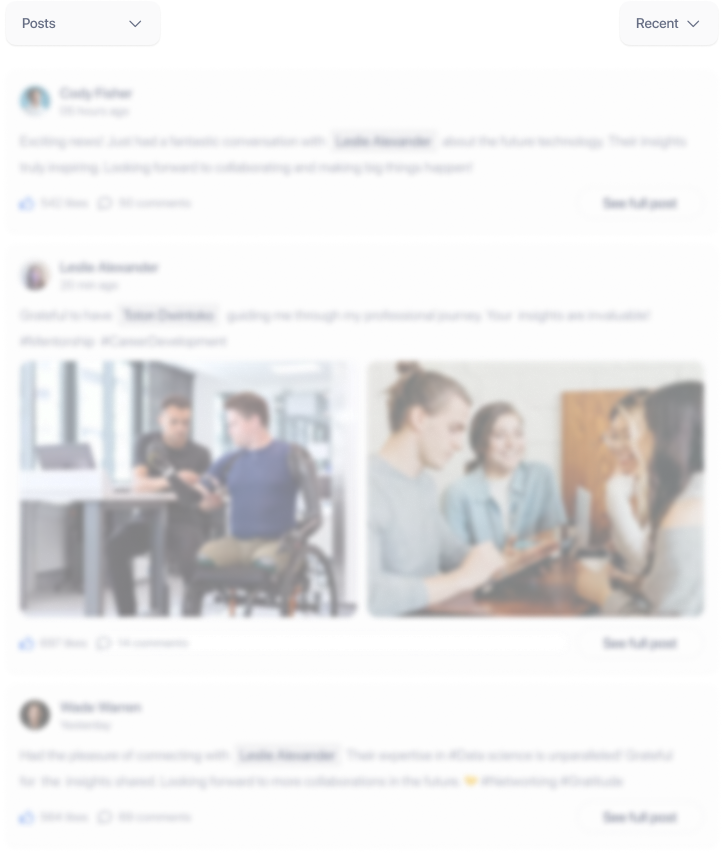