Fernando Sanchez
Sr. Director Quality Assurance at IRRAS AB- Claim this Profile
Click to upgrade to our gold package
for the full feature experience.
Topline Score
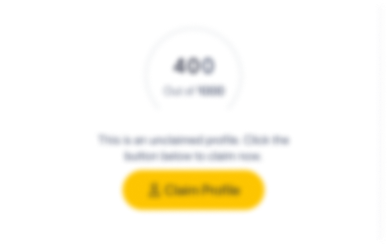
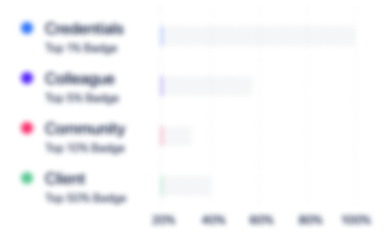
Bio


Credentials
-
Lean Six Sigma Black Belt (ICBB)
BDOct, 2012- Oct, 2024 -
Certified Manager of Quality/Organizational Excellence (CMQ/OE)
ASQ - World HeadquartersMar, 2010- Oct, 2024 -
Certified Quality Engineer (CQE)
ASQ - World HeadquartersAug, 2009- Oct, 2024 -
Certified Purchasing Manager (CPM)
ISM University of Management and EconomicsMay, 2003- Oct, 2024
Experience
-
IRRAS AB
-
Sweden
-
Medical Equipment Manufacturing
-
1 - 100 Employee
-
Sr. Director Quality Assurance
-
Nov 2021 - Present
Deploy revised design control processes/procedures incorporating software, human factors, and electrical/mechanical disciplines, while executing early clinical, marketing, regulatory, manufacturing, and quality assurance engagement from beginning of design project. Oversee team of Quality Engineers, Document Control Specialists, and Inspectors, while boosting QA team’s performance in audit readiness and key performance indicators (KPIs), such as CAPAs, SCARs, and NCMRs. Conduct initial 5S, direct Lean, and Six Sigma training. • Decreased launch of new products by four months and product failures by 14% via implementing Lean Sigma methodology throughout the Design, manufacturing, and shipping processes. • Established Quality Assurance team overseeing full medical device lifecycle from customer/clinical input via design, manufacturing, post-market surveillance, and end-of-life. • Met requirements of ISO 13485, MDSAP, CFR 820, and EUMDR by rewriting quality management system with functional department heads. • Steered Regulatory Affairs team with successful submission in the FDA, EUMDR, MDSAP and Middle East markets. • Reduced final inspection timelines by 68%, while increasing defect detection and documentation. • Expanded compliance on design controls, clinical research, and manufacturing operations. • Hosted FDA, CDPH, MDR, and MSAP audits with 49% reduction in findings year to year. Show less
-
-
-
BioTelemetry, Inc.
-
United States
-
Biotechnology Research
-
100 - 200 Employee
-
Director of Quality Assurance
-
Jan 2018 - Oct 2021
Administered quality and regulatory professionals across three sites in United States. Developed state-of-the-art CAPA review board, NCR, and SCAR practices, increasing availability of relevant improvement data and reducing 50% backlog within three months. Devised personnel performing quality engineering design controls, manufacturing-based quality operations, regulatory affairs, distribution, risk assessment, document control, internal/external audit, and post-market surveillance. Upgraded legacy risk management files to comply with ISO 14971:2019 with subject matter experts. • Met regulatory requirements of design, manufacturing, distribution, and post-market surveillance operations, while performing as key liaison between regulatory bodies and operating divisions within company. • Acquired drastic 70% reduction of external findings and finding severity, while overseeing internal audit program increasing number of internally qualified auditors. • Enhanced 43% efficiency by initiating and leading early quality design assurance involvement on all R&D (hardware/software) projects. • Reduced six-month time-to-market KPI for new products and four weeks for redesign projects by executing Lean Sigma methodology to design and development procedures, while designing efficient hardware/software design and development process. • Ensured continued and improved compliance with MDSAP, EUMDR, QSR, ISO 13485:2016, and 14971:2019 standards with newly created regulatory affairs department. • Transited legacy and new medical devices to EUMDR regulation one year ahead of schedule. Show less
-
-
-
US Navy
-
United States
-
Armed Forces
-
700 & Above Employee
-
Lt. Commander US Navy - retired
-
May 1991 - Oct 2020
Naval Special Warfare - Corpsman Naval Special Warfare - Corpsman
-
-
-
BD
-
United States
-
Medical Equipment Manufacturing
-
700 & Above Employee
-
Principal Quality Engineer
-
Jan 2013 - Dec 2018
Served as infusion pumps R&D quality engineer for both US and International products. Conducted Assurance Case and 510K preparation for FDA review and approval of medical devices. Acted as the Quality Engineering – regulatory affairs liaison to national and international regulatory bodies. • Prepared and presented the company's first Assurance Case that the FDA accepted with no revisions or denials. FDA used this Assurance Case submission as an example to the infusion pump industry. • Implemented the company's new Assurance Case methodology, training five peers to assist in future AC - 510K submissions. • Performed risk management per 14971 for US and International infusion devices. • Coordinated the transition from 14971:2007 to 14971:2012. Sourced, procured, and validated the new risk management software suite. • Provided thoughtful application of the quality management system to all stages of product design for complex electro-mechanical infusion pumps with a heavy emphasis on software development. Creative problem solving and flexible solutions were the key to accomplish an on-time delivery of new products while meeting all QMS requirements. • Acted as management representative for FDA, internal, and customer audits and as Quality Engineering point of contact for quality management system audits. Collaborated with a multidisciplinary team on responses to observations, recalls, etc. Show less
-
-
-
Spectrum Assembly, Inc.
-
United States
-
Appliances, Electrical, and Electronics Manufacturing
-
1 - 100 Employee
-
Quality Assurance Manager
-
Oct 2011 - Dec 2013
1. Implementation of the ISO 13485:2003 and AS9100 rev C Quality Management Systems with an emphasis on First Pass Yield improvement, product development and organizational excellence. 2. Management representative and point of contact for compliance to CFR 820, 510K submissions, and regulatory audits from the FDA, California Food and Drug branch with an emphasis on Class II and Class III medical devices. 3. Main point of contact and management representative with CSA, MDD and UL for testing, quarterly audits, requalification audits and verification testing. 4. Coordinated the “paperless WO traveler and documentation system” management team. This project reduced the amount of hard copy traveler, instructions and drawings in the production floor and reduced by 11% the amount of production defects due uncontrolled documentation revision changes. 5. Introduced and implemented the supplier monitoring and evaluation system that increased the average on time delivery from 67% to 92% and reduced the supplier rejection rate by 14% 6. Managed the updated training seminars for the IPC-A-610, J-STD-001E and IPC-A-620 with the purpose of improving operator soldering, W&C and inspection skills. 7. Sourced, purchased and implemented the first CNN Visual Inspection Machine. 8. Implemented formal incoming inspection procedures for products such as metal machined parts, sheet metal parts, printed circuit boards, plastic molded, plastic extrusion parts, etc. Show less
-
-
-
Delkin Devices | Rugged Controlled Storage
-
United States
-
Appliances, Electrical, and Electronics Manufacturing
-
1 - 100 Employee
-
Director of Quality and Engineering
-
Jan 2007 - Sep 2011
Wrote all required QMS documentation and achieved ISO 9001:2000 certification in 6 months with no findings or observations during the initial assessment. Implemented formal incoming inspection techniques, introduced the National Instruments Vision Builder automatic inspection software, and planned and implemented in process and FQA procedures, resulting in 15% reduction of defects on outgoing material and a 7% reduction of returned material in the first 5 months. With the operations department head, conducted time and motion studies, changed the floor layout, and eliminated most inefficient processes which resulted in average 20% improvement on the SMT lines. Planned for methods to increase operational effectiveness by applying lean manufacturing techniques. Instituted a new product introduction methodology to ensure that all new product designs incorporated quality safeguards as well as to ensure adequate design for manufacturability standards. Coached the engineering department on appropriate design and development procedures and integrated the quality function as part of the design process. Was requested to oversee the purchasing and production control department for a 6-month period to mentor and provide leadership in the 4 busiest months of the year. Hired and trained the new Purchasing Manager and Jr. Buyer. Still work alongside of this group to increase the department's efficiency. With the purchasing department, implemented the supplier selection process and supplier evaluation programs to increase the vendor's ability to supply acceptable material and release nonperforming vendors. Also oversaw the revamping of the supplier corrective action program. Performed supplier audits. Received the 2007 employee of the year award for "outstanding effort and hard work above and beyond the requirements of his job". Show less
-
-
-
Datron World Communications, Inc.
-
United States
-
Defense and Space Manufacturing
-
1 - 100 Employee
-
Quality Assurance Manager
-
Oct 2005 - Dec 2006
Created a team-oriented environment that enabled the incoming inspection function to reduce inspection time from an average of 20 days down to ~6 days. Administrated the factory acceptance function by ensuring that the visiting customer would find the tested equipment in an acceptable stage. Also coordinated the customer complaints/investigation of rejected material with an emphasis on creating both corrective and preventive actions as well as proposing new designs, re-designs, or other product solutions for the customer's applications. Successfully rewrote the Quality Manual (Level 1) and Operating procedures (Level 2) to ensure compliance to the ISO 9001:2000 standard. Acted as the management representative and coordinated all aspects of the ISO compliance function. Oversaw review and QA approval of new designs, specifications, instructions, and other documentation thru the document review process with the purpose of integrating quality from the beginning of the design. Implemented quality reporting, trend reviews, SPC, conformance-nonconformance tracking, and monthly data analysis; prepared the monthly quality report that was presented to the senior executive staff. Managed corrective and preventive action functions (CAPA), optimized the current system, and developed an accountability standard to be used in all departments. With the purchasing department, worked on a supplier rating system, supplier symposium day as well as conducting small "consulting" visits to key suppliers. Show less
-
-
-
Cole Instrument Corporation
-
United States
-
Appliances, Electrical, and Electronics Manufacturing
-
1 - 100 Employee
-
Purchasing Manager
-
Apr 2003 - Oct 2005
-
-
Senior Quality Engineer
-
Jul 2001 - Apr 2003
-
-
Education
-
Universidad Autónoma de Baja California
Master's degree, Business Administration and Management, General -
San Diego State University
Affiliate Finance and Economy program, Finance, General -
Universidad Autónoma de Baja California
Bachelor's degree, Business Administration and Management, General
Community
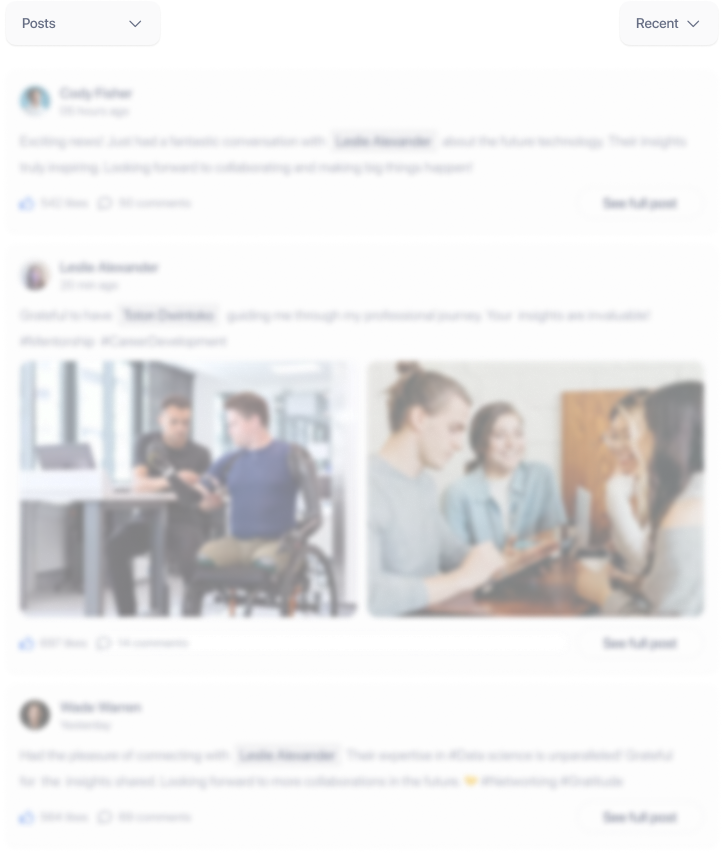