Ferenc KURUCSAI
General Manager - BAKONY TECHNICAL CERAMICS LTD. at BAKONY TECHNICAL CERAMICS LTD.- Claim this Profile
Click to upgrade to our gold package
for the full feature experience.
Topline Score
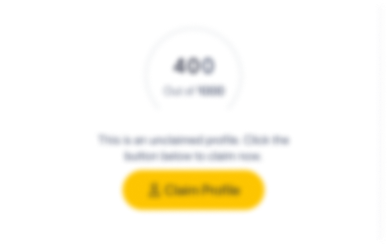
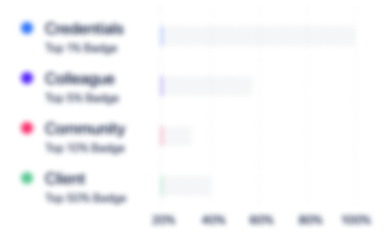
Bio


Experience
-
BAKONY TECHNICAL CERAMICS LTD.
-
Hungary
-
Glass, Ceramics and Concrete Manufacturing
-
1 - 100 Employee
-
General Manager - BAKONY TECHNICAL CERAMICS LTD.
-
2019 - Present
BAKONY TECHNICAL CERAMICS LTD. (NUMBER OF EMPLOYEES: 200 P.) (REVENUE: ≈ 2.6 BILLION HUF) Manage the Company's strategic and annual objectives (BUDGET), guide and follow the execution of capital investment (CAPEX) plans and projects. Define and execute the business strategy (-export ratio more than 97%-), drive, and deliver top and bottom-line improvements. Full P&L responsibility; manage the daily, middle, and long-term activities (200 employees). Commercial strategy definition, key partners, and customer negotiations. Coordination of material-, product-, and business development projects. Important projects: Project: Significant profitability increase Cost structure analysis, and modification, re-negotiation of supply contracts. Implemented continuous improvement culture change through collaboration and communication - standardized scorecard and objectives, reports. Results: significantly increased the efficiency, decreased the cost of raw-, and additional materials, cost of energy. (Base 2018: 100%, 2018 vs. 2019: 195 % 2018 vs. 2020: 271 % 2018 vs. 2021: 454 %) high improvement for three years. Project: Decrease customer complaint costs (-export ratio more than 97%-) Product portfolio analysis, and modification, re-negotiation of contracts, data visualization, PDCA with daily GEMBA activities, continuous improvement project (ISO 9001, and ISO 13485). Results: significantly decreased the low efficiency (high rejects rate, additional transfers) contractor and other activities. NC-, and CNC machining cells, robot cell in the final grading). (base 2019: 100%, 2019 vs. 2020: 39%, 2019 vs. 2021: 16%) high improvement for last years. Show less
-
-
-
Imerys
-
France
-
Mining
-
700 & Above Employee
-
-
Dec 2017 - Nov 2018
IMERYS WOLLASTONITE LLC., USA (NUMBER OF EMPLOYEES: 65 P.) (REVENUE: 35 M USD ≈ 13 BILLION HUF)Priority occupational health and safety and environmental activities.Direct the investments projects, supporting and considering financial analysis, determine the impact (P&L) on the business. Business planning (BUDGET) and (CAPEX) plans.General daily and annual activities: operations, EHS, quality, supply chain and logistics, financial, customer services. Coordinating the activities between the mine and the Factory. KPI visualization and control.Important project:Project: Beneficiation circuit improvement (de-bottle neck)Duration: 5 months, used methods: pareto analysis, value stream analysis, 5M.Results: increase the (bottle neck) capacity of the circuit by 35 - 40 %, (without significant investments) => Work organization opportunity to turned from 7 days to 5 days. Show less
-
-
-
Dec 2014 - Dec 2017
IMERYS KILN FURNITURE HUNGARY LTD. (NUMBER OF EMPLOYEES: 300 P.) (REVENUE: ≈ 6,0 BILLION HUF)Managing and controlling the annual-, (BUDGET, CAPEX and P&L), and the monthly planning and control process (KPI system).Controlling the material-, product developments, coordinate the European Design Centre of Imerys Kiln Furniture business unit with 8 engineers (design, developments, new product ramp-up projects).Driving the process developments, -supply chain reorganization-, financial analysis of each process improvement to determine the impact on the business and the project priorities.Relocation of the special ceramic plant with all technology form Spain (95 employees) to Hungary.Maintaining contact with key commercial supervising the customer visits, coordinating the presentation of the new technical solutions/applications (cordierite-, Hi Alumina-, SIC kiln furniture elements / complex kiln car superstructure applications -with metal and other additional parts-) .Important project:Project: “Safety first” (-WLTA- project)Duration: continuous, Used methods: 6S, Take 5, Serious 7, general safety methods. Result: 2.500.000 working hours Without Lost Time Accident (-WLTA-) between June 2010 and October 2016. Show less
-
-
-
Oct 2008 - Dec 2014
Managed and controlled plant production, maintenance, and industrial and technical logistic activities.Provided effective leadership and direct supervision of departmental leaders (15,) and direct and indirect staff (180 employees).Ensured that the investment projects were accomplished according to the objectives. Prepared financial analysis of each process improvement to determine the impact on the business and the project priority.Drive a culture proactively focused on environmental (CO2 quota monitoring), health, and safety, driving towards zero-incident safety culture mindset.Important projects:Project: Relocation of the division’s Spanish factory to Hungary Lead the transfer and scale-up of new ceramic technology (knowledge, 2 technological lines, machines). Duration 6 months. Used methods: VSM analysis, 5S. Result: The project finished on time and budget (>5 MEUR), within forecasted KPI-s.Project: Evaluated, motivated and coached manufacturing staff to maintain the continuity of efficient plant output, while improving product quality, controlling, and decreasing operational cost applying the preventive maintenance, CI, LEAN, 5S, PDCA … .Result: 5,5 % production cost decreasing Show less
-
-
-
-
General Manager - DUAL PLATFORM CONSULTING LTD:
-
Jan 2008 - Dec 2016
Independent consultancy projects: Managed general industrial projects from concept phase through to manufacture and installation (food-, and technical ceramics industries). Independent consultancy projects: Managed general industrial projects from concept phase through to manufacture and installation (food-, and technical ceramics industries).
-
-
-
-
Dairy Production Manager - SOLE MIZO Co.
-
2006 - 2007
SOLE MIZO CO. (NUMBER OF EMPLOYEES: 1200 P.) (REVENUE: ≈ 89.2 BILLION HUF) Coordinated the daily production activities (in melted products and túrócsoki plant), supervised workforce to ensure the timely flow of products (65 employees), and product quality. Optimised production, defined, recommended and introduced new best practices. SOLE MIZO CO. (NUMBER OF EMPLOYEES: 1200 P.) (REVENUE: ≈ 89.2 BILLION HUF) Coordinated the daily production activities (in melted products and túrócsoki plant), supervised workforce to ensure the timely flow of products (65 employees), and product quality. Optimised production, defined, recommended and introduced new best practices.
-
-
-
-
Technical Director - Suli Host Ltd.
-
2004 - 2006
SULI-HOST LTD. (NUMBER OF EMPLOYEES: 330 P.) (REVENUE: ≈ 2.5 BILLION HUF) Managed catering activities in Szeged (325 employees), developed the monitoring of indicators according to the company profile. Liaised with leaders of the local council, heads of educational institutions and corporations. Planned, and supervised procurements, negotiated with suppliers and business partners. SULI-HOST LTD. (NUMBER OF EMPLOYEES: 330 P.) (REVENUE: ≈ 2.5 BILLION HUF) Managed catering activities in Szeged (325 employees), developed the monitoring of indicators according to the company profile. Liaised with leaders of the local council, heads of educational institutions and corporations. Planned, and supervised procurements, negotiated with suppliers and business partners.
-
-
-
-
Plant Manager - HAJDÚ BÉT Co.
-
2003 - 2004
HAJDÚ-BÉT CO. (EMPLOYEES: >3 000 EMPLOYEES) (REVENUE: ≈ 38 BILLION HUF) Was responsible for production (ready to eat meals, and ready to eat kebab) and logistics (50 - 270 employees). Managed and supervised purchasing and manufacturing processes and deliveries to clients. Developed new products (ready to eat kebab-, and chicken breast fillet products) for manufacturing. HAJDÚ-BÉT CO. (EMPLOYEES: >3 000 EMPLOYEES) (REVENUE: ≈ 38 BILLION HUF) Was responsible for production (ready to eat meals, and ready to eat kebab) and logistics (50 - 270 employees). Managed and supervised purchasing and manufacturing processes and deliveries to clients. Developed new products (ready to eat kebab-, and chicken breast fillet products) for manufacturing.
-
-
-
-
Deputy Plant Manager
-
2002 - 2003
Operational management of the production plant of the Mezőkovácsháza unit in Hajdú Bét Co. (100 - 150 employees). Introduction of production management system software (MES system with CRM modul). Operational management of a canning plant (goose and duck liver products). Coordinating the retail unit and activities of the Factory Unit. Operational management of the production plant of the Mezőkovácsháza unit in Hajdú Bét Co. (100 - 150 employees). Introduction of production management system software (MES system with CRM modul). Operational management of a canning plant (goose and duck liver products). Coordinating the retail unit and activities of the Factory Unit.
-
-
-
-
Deputy Plant Manager - SOLE HUNGÁRIA Co.
-
2001 - 2002
SOLE MIZO CO. (NUMBER OF EMPLOYEES: 1200 P., REVENUE: ≈ 89.2 BILLION HUF) Ensured quality production, outputs met the expectations of Customers. Directed 6 supervisors, and organised operations personnel (90 – 100 employees). Introduced quality assurance standards and supervised the system. Integrated HACCP into ISO system, adjusted routines to stringent hygienic requirements. SOLE MIZO CO. (NUMBER OF EMPLOYEES: 1200 P., REVENUE: ≈ 89.2 BILLION HUF) Ensured quality production, outputs met the expectations of Customers. Directed 6 supervisors, and organised operations personnel (90 – 100 employees). Introduced quality assurance standards and supervised the system. Integrated HACCP into ISO system, adjusted routines to stringent hygienic requirements.
-
-
-
-
-
1998 - 2001
HUNGERIT Co. (NUMBER OF EMPLOYEES: 1650 P.) (REVENUE: ≈ 42.5 BILLION HUF)Introduced quality assurance standards -for all plants- and supervised the system after certification.Integrated HACCP into ISO system -for every production areas- , adjusted routines to stringent hygienic requirements. Provided training to employees to meet the regulations.
-
-
-
1995 - 1998
Ensured quality production, outputs met the expectations of customers and owners.Directed 4 supervisors, and organised operations personnel (250 - 300 employees).Provided training to employees to meet the regulations.
-
-
Education
-
University of Szeged
Le Groupe ESIDEC at College of Food Industry - Higher education, Logistics, Materials, and Supply Chain Management -
University of Szeged
College of Food Industry - Bachelor's degree - Quality Assurance System Engineer, Quality Assurance -
University of Szeged
College of Food Industry - Bachelor's degree- Food Engineer BSc. -
MSHA (Mine Safety and Health Administration)., USA – NY State
Mining work-safety and health training -
EUZERT Ltd., Budapest
Certified SIX SIGMA Black belt expert, LEAN - Continuous improvement -
EUZERT Ltd., Budapest
Certified SIX SIGMA Green belt expert, LEAN - Continuous improvement -
Imerys Co., Torino
Imerys Safety University, Occupational health and safety -
Imerys Co., Brussels
Imerys Finance Course, Finance, General -
Imerys Co., Paris
Project management and Capex - Opex training, Project Management -
Samling Ltd., Budapest
Certified LEAN manager, Lean - Continuous improvement -
Tequa Consultancy Centre, Budapest
Project management / MS Project, Project Management -
Tequa Consultancy Centre, Budapest
Environmental manager, Environmental Studies
Community
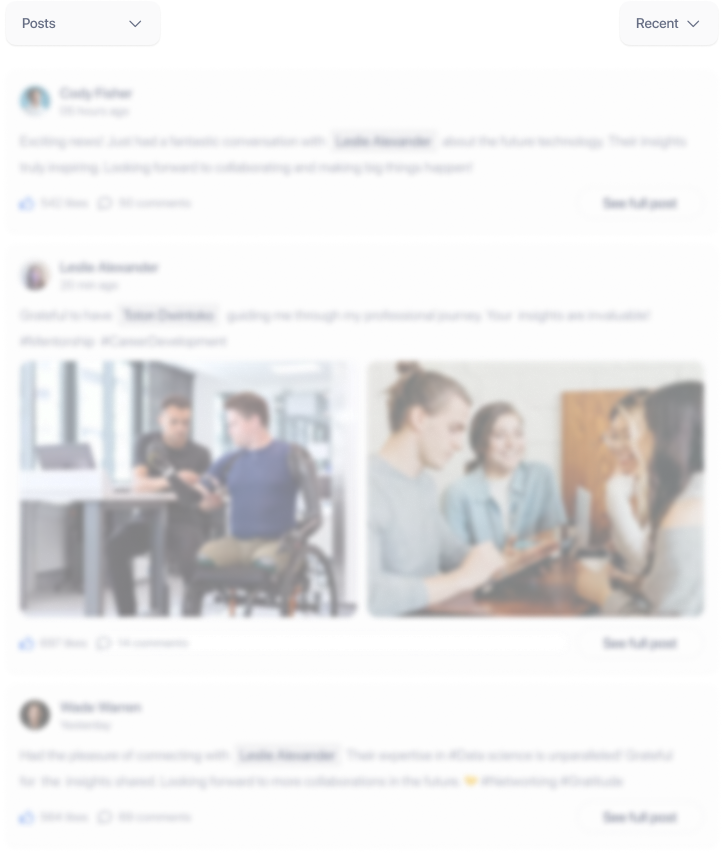