Fatma El-Abyad
Quality Director at International Group For Modern Coatings - MIDO- Claim this Profile
Click to upgrade to our gold package
for the full feature experience.
-
English -
Topline Score
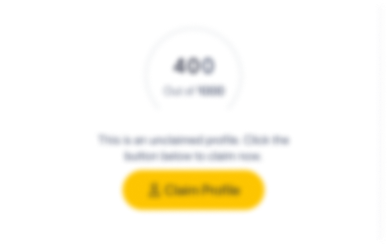
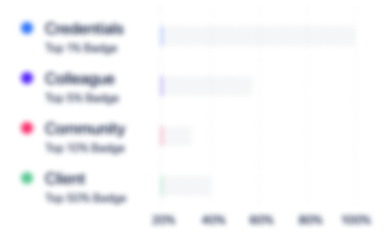
Bio

Dale Johnson
Fatma has a very professional approach to the business needs together with attention to detail of key quality aspects and processes for enhancements

Mohamed Moussa
I worked closely to Fatma for about eight years in the same team. I found her such a devoted and patient colleague and very passionate about her job. Fatma used to be very helpful and thoughtful colleague and gained a very wide popularity among our company. She is a hard working colleague, a dedicated team worker, able to multi-task and a problem solving oriented. She has a strong expertise on all quality aspects.

Dale Johnson
Fatma has a very professional approach to the business needs together with attention to detail of key quality aspects and processes for enhancements

Mohamed Moussa
I worked closely to Fatma for about eight years in the same team. I found her such a devoted and patient colleague and very passionate about her job. Fatma used to be very helpful and thoughtful colleague and gained a very wide popularity among our company. She is a hard working colleague, a dedicated team worker, able to multi-task and a problem solving oriented. She has a strong expertise on all quality aspects.

Dale Johnson
Fatma has a very professional approach to the business needs together with attention to detail of key quality aspects and processes for enhancements

Mohamed Moussa
I worked closely to Fatma for about eight years in the same team. I found her such a devoted and patient colleague and very passionate about her job. Fatma used to be very helpful and thoughtful colleague and gained a very wide popularity among our company. She is a hard working colleague, a dedicated team worker, able to multi-task and a problem solving oriented. She has a strong expertise on all quality aspects.

Dale Johnson
Fatma has a very professional approach to the business needs together with attention to detail of key quality aspects and processes for enhancements

Mohamed Moussa
I worked closely to Fatma for about eight years in the same team. I found her such a devoted and patient colleague and very passionate about her job. Fatma used to be very helpful and thoughtful colleague and gained a very wide popularity among our company. She is a hard working colleague, a dedicated team worker, able to multi-task and a problem solving oriented. She has a strong expertise on all quality aspects.
0
/5.0 / Based on 0 ratingsFilter reviews by:
Credentials
-
CMQ/OE, ISO TS 16949, ISO 14001, OHSAS 18001
-
Experience
-
International Group For Modern Coatings - MIDO
-
Egypt
-
Chemical Manufacturing
-
1 - 100 Employee
-
Quality Director
-
Feb 2020 - Present
-
-
-
PROMETEON TYRE GROUP
-
Italy
-
Motor Vehicle Manufacturing
-
700 & Above Employee
-
Market Quality Manager
-
Apr 2017 - Apr 2018
1. Investigating and resolving customer claims. 2. Evaluating the performance of products through conducting several market surveys. 3. Communicating findings with R&D to develop current or new products. 4. Evaluating R&D actions through following up market test for tires 1. Investigating and resolving customer claims. 2. Evaluating the performance of products through conducting several market surveys. 3. Communicating findings with R&D to develop current or new products. 4. Evaluating R&D actions through following up market test for tires
-
-
-
Pirelli
-
Italy
-
Motor Vehicle Manufacturing
-
700 & Above Employee
-
Market Quality Manager
-
Feb 2015 - Apr 2017
1. Investigating and resolving customer claims.2. Evaluating the performance of products through conducting several market surveys.3. Communicating findings with R&D to develop current or new products.4. Evaluating R&D actions through following up market test for tires
-
-
Industrial Quality Manager
-
Feb 2013 - Feb 2015
Applying control plansInstalling and following up of improvement projects
-
-
Sustainability Manager
-
Jan 2011 - Feb 2015
Reporting to company CEOIn parallel of being a quality manager, I hold the function of sustainability and EO manager with the following responsibilities;• Planning for company external initiatives within company guideline and related budget• Communicating with external NGO, local community and governmental entities to execute the initiatives.• Representing company and communicating Pirelli sustainability model and achievements within CSR communities in Egypt.• Preparing the company for the SA8000 audit, according to the audit plan• Facilitating the annual reporting for sustainability KPI to issue the overall group annual sustainability report.• Monitoring the EO (Equal Opportunity) policy application in the company,reporting any claim to HQ and following up investigation and related actions. Show less
-
-
QA Manager
-
Oct 2010 - Feb 2013
1) Responsible for the planning and application of internal audit system including product audit, system audit and manaufacturing process audit according to the requirements of ISO TS 16949:2009 QMS2) Conducting and follow up the action plan of the management review3) Maintaining and updating of documentation system4) Creating and maintaining control plan and FMEA5) Follow up the implementation of MSA and its related action plans6) Suggesting and following up the implementation of quality improvements projects Show less
-
-
-
AAC
-
Austria
-
Media Production
-
200 - 300 Employee
-
Quality Assurance Manager (Certified Lead auditor ISO TS 16949:2009)
-
Feb 2002 - Oct 2010
-Conducting quarterly management review meeting and following up the related actionplans. -Updating quality manual for the scope of the quality management system and the processes interaction.-Approving annual Internal (system/process) audit plan and following up the implementation of the internal audit procedure.-Verifying the effectiveness of the corrective actions implementation before closing it.-Planning for the annual implementation of external audits according to ISO TS16949:2002.-Following up customer SRS and related customer feedback on monthly basis, this includes information exchange to any customer location and organizing of various feedbacks to the different department channels.-Planning for proper preparation for customer visits (Specially process audits) and following up the implementation of customer requirements included in visits reports or action plan.-Responsible for following up the implementation for all the activities inside the QA department such as documents and records control, product audit including batches releases, sample making arrangement and reporting, internal rejection reporting for quality circles, following up of corrective and preventive actions, traceability reports for the WIP and packed batches. Show less
-
-
Quality Planning Section Head
-
Mar 2003 - Aug 2006
- Applying APQP (Advanced Product Quality Planning), including feasibility study for new projects, project time plan, control plan, FMEA and process flow chart.- Following up of different projects (new products) time plan for each activity in the plan internally and with the customers.- Revision of customer specification and drawings for its update and starting feasibility study for each affecting change to make the necessary decisions.- Following up customer complain according to the 8D problem solving technique.This include, grouping of different teams, following up every team brainstorming results, sample making and corrective actions. Initiating quality review process to discuss all the open 8Ds, corrective action due dates and responsiblity implementation.Handling customer communications and feed back regarding to technical issues.-Following up customer action plans as a result of customer periodical process audit-Organizing the sample making procedure in the foundry as a system foroptimization and developments.-Joining internal audit team (according to ISO/TS 16949:2002) during theperiodical internal audit.- Creating and revising of work Instructions and procedures for all the related activities. Show less
-
-
-
International Plastics company
-
Italy
-
Plastics Manufacturing
-
1 - 100 Employee
-
QC Section Head
-
Jul 1996 - Feb 2002
• Sampling during process for inspection. • Performing acceptance sampling for received lots. • Analysis of data collected to control the process and verifying the • capabilities of the machines using statistical quality control methods and TQM. tools. • Design of gauges used in inspection to control the inprocess quality control. • Following up customers complains and managing a solution or modification for different elements of the production operation that might cause that complains. Show less
-
-
Education
-
ESLSCA
Master of Business Administration (MBA), International Marketing -
Alexandria University
High Diploma, Indutrial Engineering -
Alexandria University
Bacholar, Production Engineering
Community
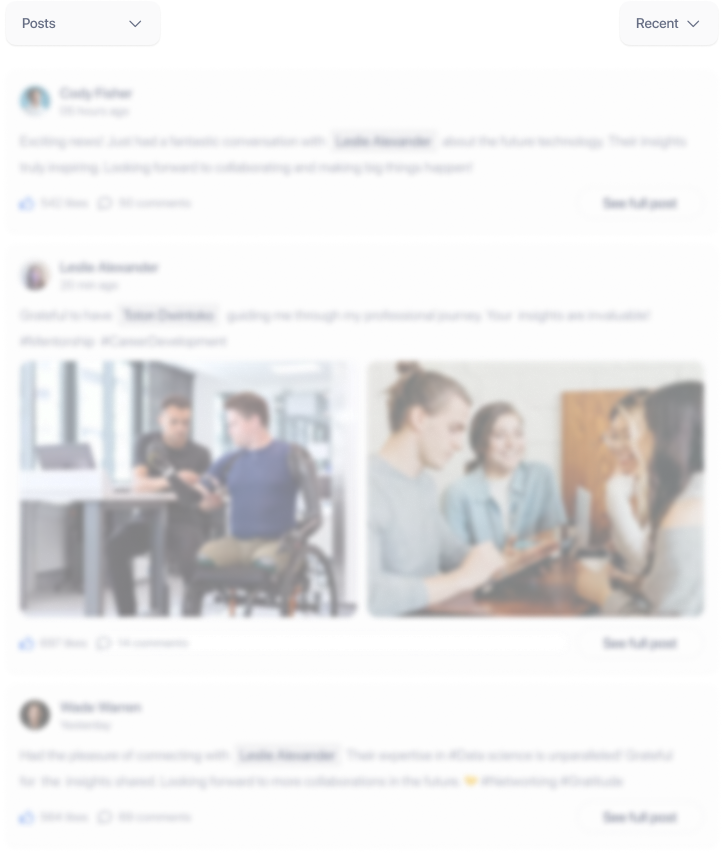