Fatemeh Mohebalizadeh
Industrial Engineer at Morbern- Claim this Profile
Click to upgrade to our gold package
for the full feature experience.
Topline Score
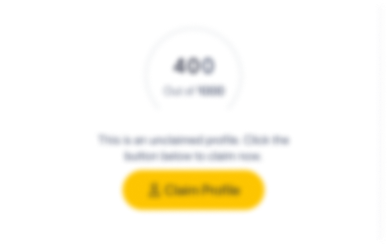
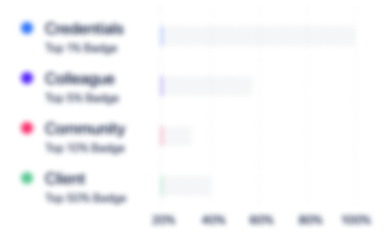
Bio


Credentials
-
Lean Six Sigma Green Belt Certification
Six Sigma Global InstituteDec, 2019- Nov, 2024 -
Certified in Production and Inventory Management (CPIM)
APICSSep, 2019- Nov, 2024 -
Effective Project Management
National Iranian Oil CompanyMay, 2009- Nov, 2024 -
Master of Engineering Management (MEM): professional Industrial engineering as a subfield of professional engineering (360 hours of post-graduation training courses and 520 hours in management and professional projects)
National Iranian Oil CompanyMay, 2009- Nov, 2024 -
Microsoft Office Project
National Iranian Oil CompanyMay, 2009- Nov, 2024 -
Primavera
National Iranian Oil CompanyMay, 2009- Nov, 2024
Experience
-
Morbern
-
Canada
-
Textile Manufacturing
-
1 - 100 Employee
-
Industrial Engineer
-
Apr 2021 - Present
-
-
-
Green Belting Industries Ltd.
-
Canada
-
Textile Manufacturing
-
1 - 100 Employee
-
Industrial Engineer
-
Feb 2018 - Nov 2020
• Managed the production floor • Led cross-functional teams to carry out different process improvement projects and investigated to uncover root causes and implemented effective solutions. • Provided direction, coaching and leadership to supervisors • Supply chain analysis: demand planning, introducing forecasting methods to forecast 2020 demands, defining min and max for each product, employing EOQ and order point system • Analyzed production cost and capacity • Provided… Show more • Managed the production floor • Led cross-functional teams to carry out different process improvement projects and investigated to uncover root causes and implemented effective solutions. • Provided direction, coaching and leadership to supervisors • Supply chain analysis: demand planning, introducing forecasting methods to forecast 2020 demands, defining min and max for each product, employing EOQ and order point system • Analyzed production cost and capacity • Provided production with “fast response” troubleshooting • Generated and maintained effective daily and weekly production schedules • Analyzed daily and weekly materials requirement • Continuously monitoring and evaluating the appropriate inventory levels to be maintained to meet the customers' demand and avoid aged inventory • Monitoring the execution of production plans with the Manufacturing plant • Ensuring that all materials and final products are processed accurately in the ERP system Led various process improvement projects: • Improved on time delivery through utilizing Six Sigma tools, improving production planning, inventory management, demand planning and establishing effective communications with customers and internal departments • Minimized raw materials waste and production scrap. Developed various process maps as well as different training procedures to collect scrap data in the plant and also in ERP system • Improved SOPs to reduce production cost, time, quality, and scrap Show less • Managed the production floor • Led cross-functional teams to carry out different process improvement projects and investigated to uncover root causes and implemented effective solutions. • Provided direction, coaching and leadership to supervisors • Supply chain analysis: demand planning, introducing forecasting methods to forecast 2020 demands, defining min and max for each product, employing EOQ and order point system • Analyzed production cost and capacity • Provided… Show more • Managed the production floor • Led cross-functional teams to carry out different process improvement projects and investigated to uncover root causes and implemented effective solutions. • Provided direction, coaching and leadership to supervisors • Supply chain analysis: demand planning, introducing forecasting methods to forecast 2020 demands, defining min and max for each product, employing EOQ and order point system • Analyzed production cost and capacity • Provided production with “fast response” troubleshooting • Generated and maintained effective daily and weekly production schedules • Analyzed daily and weekly materials requirement • Continuously monitoring and evaluating the appropriate inventory levels to be maintained to meet the customers' demand and avoid aged inventory • Monitoring the execution of production plans with the Manufacturing plant • Ensuring that all materials and final products are processed accurately in the ERP system Led various process improvement projects: • Improved on time delivery through utilizing Six Sigma tools, improving production planning, inventory management, demand planning and establishing effective communications with customers and internal departments • Minimized raw materials waste and production scrap. Developed various process maps as well as different training procedures to collect scrap data in the plant and also in ERP system • Improved SOPs to reduce production cost, time, quality, and scrap Show less
-
-
-
Ryerson University
-
Canada
-
Higher Education
-
700 & Above Employee
-
Research Assistant
-
Sep 2017 - Dec 2018
Optimizing a cold supply chain network in southern Ontario Optimizing a cold supply chain network in southern Ontario
-
-
-
University of Guelph
-
Canada
-
Higher Education
-
700 & Above Employee
-
Graduate Teaching Assistant
-
Sep 2014 - Dec 2016
-
-
Graduate Research Assistant (As a Master Student)
-
Sep 2014 - Jun 2016
Master's Thesis: Balancing, Sequencing, and Determining the Number and the Length of Workstations in a Mixed Model Assembly Line (Assembly line balancing and sequencing)
-
-
-
OTC - Oil Turbo Compressor
-
Oil and Gas
-
100 - 200 Employee
-
Project Control Specialist
-
Jul 2012 - Apr 2014
• Responsible for engineering, procurement, and construction (EPC) planning, scheduling, and cost control • Coded project activities by the project work breakdown structure for cost and schedule integration and analysis in Microsoft Project • Established project baselines • Leaded, coordinated, and facilitated interactive planning sessions at each part of the project to assist in overall project plan, WBS consistency, schedule development and forecasting of project requirements •… Show more • Responsible for engineering, procurement, and construction (EPC) planning, scheduling, and cost control • Coded project activities by the project work breakdown structure for cost and schedule integration and analysis in Microsoft Project • Established project baselines • Leaded, coordinated, and facilitated interactive planning sessions at each part of the project to assist in overall project plan, WBS consistency, schedule development and forecasting of project requirements • Defined and optimized critical paths, performed total float analysis, and management the status of critical activities • Analyzed suppliers’ schedules to ensure correct relationships and accurate data • Provided solutions for corrective actions due to delays in certain aspects of the project • Tracked and updated the actual progress and cost versus the planned progress and cost • Prepared project status and cost reports, and analyzed variance reports • Acted as a primary point of contact for all internal and external project control functions on assigned projects • Visited different sites to monitor the progress of the project
-
-
Production Planner/Scheduler
-
Jun 2009 - Jun 2012
• Reviewed client orders and prepared the production plan in MS Project in coordination with maintenance, production, inventory control and purchasing departments to ensure on-time delivery of orders • Developed production schedules • Planned and scheduled material release to the production based on total demand requirements and capacity availability • Communicated with 16 suppliers and managed supplier Schedules to meet production requirements /customer demands. • Coordinated and… Show more • Reviewed client orders and prepared the production plan in MS Project in coordination with maintenance, production, inventory control and purchasing departments to ensure on-time delivery of orders • Developed production schedules • Planned and scheduled material release to the production based on total demand requirements and capacity availability • Communicated with 16 suppliers and managed supplier Schedules to meet production requirements /customer demands. • Coordinated and communicated with multiple internal departments to determine product requirements, assure the timely delivery of raw materials, monitor inventory level, verify completion of quality control on raw materials, pass in-process and final inspections, and to ensure production processes, and deliveries are progressing according to the plan • Updated production schedules of different products with actual data from suppliers, production, inventory, and quality control departments • Coordinated with Production Supervisor as needed to identify and resolve issues regarding production and inventory, and provided proper solutions • Monitored work in progress (WIP) on the plant and adjusted schedule when required due to material shortages or other manufacturing interruptions • Prepared weekly progress reports for over 50 parts of axillary and accessary of Gas Turbo Compressor specific to purchasing materials, inventory, production, and inspections • Prepared production cost analysis, compared the actual and standard production cost, and analyzed variance reports • Attended different levels of weekly meeting such as production status review meetings • Undertook regular site visits to production facilities of the company and also different suppliers to inspect the processes, discuss issues, and communicate implementation of regulations
-
-
-
-
Project Control Specialist
-
May 2005 - May 2008
• Developed project planning and scheduling • Developed project work and cost breakdown structures and integrated them with schedule • Assisted in budget estimation and resource planning • Monitored and reported critical path and schedule performance of the total project • Tracked and updated schedules, costs, and quality of work being completed with inputs from different internal departments • Alerted the project team and manager about any problems that affect the project… Show more • Developed project planning and scheduling • Developed project work and cost breakdown structures and integrated them with schedule • Assisted in budget estimation and resource planning • Monitored and reported critical path and schedule performance of the total project • Tracked and updated schedules, costs, and quality of work being completed with inputs from different internal departments • Alerted the project team and manager about any problems that affect the project, and provided solutions to the project control team • Prepared weekly project status reports highlighting project cost, schedule, variances, and areas of concern • Visited sites to ascertain project work progress • Participated in different weekly meeting including project status meeting, delay analysis and evaluation. Show less • Developed project planning and scheduling • Developed project work and cost breakdown structures and integrated them with schedule • Assisted in budget estimation and resource planning • Monitored and reported critical path and schedule performance of the total project • Tracked and updated schedules, costs, and quality of work being completed with inputs from different internal departments • Alerted the project team and manager about any problems that affect the project… Show more • Developed project planning and scheduling • Developed project work and cost breakdown structures and integrated them with schedule • Assisted in budget estimation and resource planning • Monitored and reported critical path and schedule performance of the total project • Tracked and updated schedules, costs, and quality of work being completed with inputs from different internal departments • Alerted the project team and manager about any problems that affect the project, and provided solutions to the project control team • Prepared weekly project status reports highlighting project cost, schedule, variances, and areas of concern • Visited sites to ascertain project work progress • Participated in different weekly meeting including project status meeting, delay analysis and evaluation. Show less
-
-
Education
-
Ryerson University
Master's degree, Industrial Engineering (Supply Chain Networks Optimization) -
University of Guelph
Master's degree, Industrial Engineering (Line balancing and sequencing; Production Planning and Scheduling)
Community
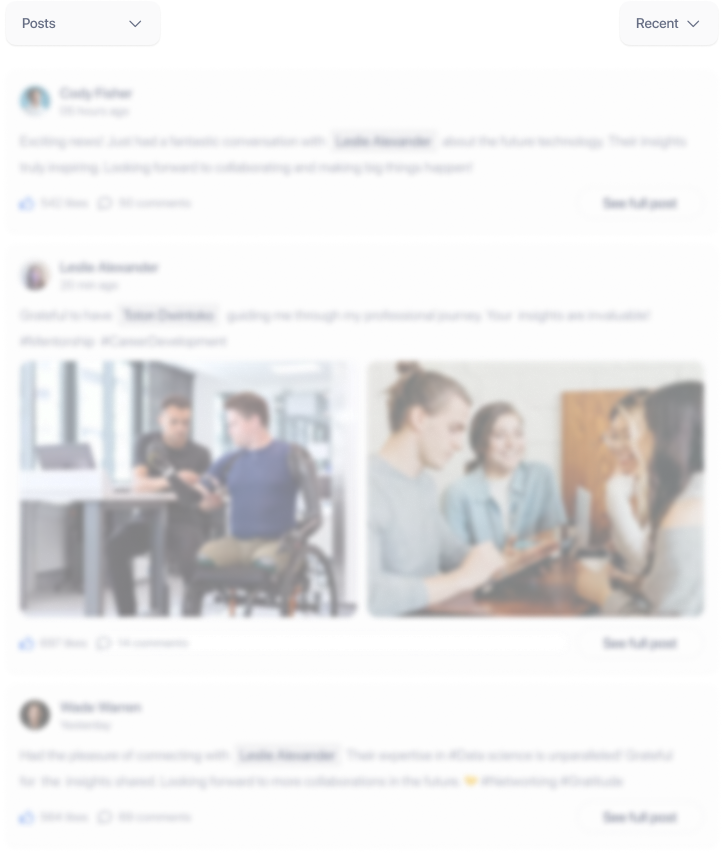