FARRUKH PERVEZ
Director Quality Assurance Regulatory Affairs at Fabrication Enterprises Inc.- Claim this Profile
Click to upgrade to our gold package
for the full feature experience.
-
Urdu -
-
Punjabi -
-
Hindi -
Topline Score
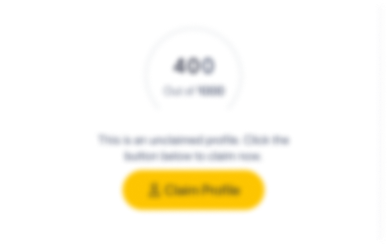
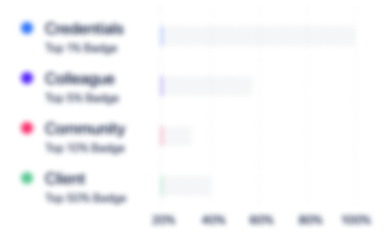
Bio

Alina Myronova
Farrukh is a honest person, hard-working professional, and he is always willing to assist in any way he can. It is a pleasure to know and work with him

Moazzam Yasoob
Farrukh is detailed oriented, thorough and has a very good grasp of the product he is responsible for. I worked with Farrukh in Multinet as a technical support engineer and was impressed by his intelligence, skill, his ability to work with development & technical teams. I would recommend Farrukh for senior position in product/project management or QA management roles.

Alina Myronova
Farrukh is a honest person, hard-working professional, and he is always willing to assist in any way he can. It is a pleasure to know and work with him

Moazzam Yasoob
Farrukh is detailed oriented, thorough and has a very good grasp of the product he is responsible for. I worked with Farrukh in Multinet as a technical support engineer and was impressed by his intelligence, skill, his ability to work with development & technical teams. I would recommend Farrukh for senior position in product/project management or QA management roles.

Alina Myronova
Farrukh is a honest person, hard-working professional, and he is always willing to assist in any way he can. It is a pleasure to know and work with him

Moazzam Yasoob
Farrukh is detailed oriented, thorough and has a very good grasp of the product he is responsible for. I worked with Farrukh in Multinet as a technical support engineer and was impressed by his intelligence, skill, his ability to work with development & technical teams. I would recommend Farrukh for senior position in product/project management or QA management roles.

Alina Myronova
Farrukh is a honest person, hard-working professional, and he is always willing to assist in any way he can. It is a pleasure to know and work with him

Moazzam Yasoob
Farrukh is detailed oriented, thorough and has a very good grasp of the product he is responsible for. I worked with Farrukh in Multinet as a technical support engineer and was impressed by his intelligence, skill, his ability to work with development & technical teams. I would recommend Farrukh for senior position in product/project management or QA management roles.
0
/5.0 / Based on 0 ratingsFilter reviews by:
Experience
-
Fabrication Enterprises Inc.
-
United States
-
Health, Wellness & Fitness
-
1 - 100 Employee
-
Director Quality Assurance Regulatory Affairs
-
Oct 2021 - Present
Provide regulatory and quality assurance oversight for EU MDR, CMDR and 21 CFR Prepare responses to regulatory authorities, supplements, and amendments. cDocument review and corrections. Provide guidance to international and local sales departments Customer Complaints System CAPA System Vendor Management Direct Internal and external compliance program. audits and site inspections by federal and regulatory agencies. Update, Control and maintain Document Control Systems Change Control System Provide regulatory input to ensure all activities are in compliance with appropriate regulation and standards, including FDA, EU MDR, ISO 13485 and MDSAP, CMDR Keep apprise with new regulations, standards, policies and guidance issued by relevant regulatory authorities. Managing direct reports. Management reviews. Lead and facilitate MRB activities Show less
-
-
-
Apothecus
-
United States
-
Medical Practices
-
Director Of Quality Assurance
-
Jul 2019 - Jun 2021
• Lead Quality Assurance Department as required through processes and methodologies • Maintaining and Managing QMS, Policy & Procedures, Controls to ensure products are in compliance with established standards and regulatory requirements • Gap Analysis • Creating and updating SOPs, Test Procedure, Work Instruction, Incoming and Final Inspection Procedures • Creating Verification & Validation protocol for different systems. • Ensuring that V &V Plan has been followed and carried out accordingly. • Hosting and facilitating FDA ,Registrar Audits and Customer Audits • Communicating and Responding with Registrar and regulatory bodies. • Scheduling and conducting internal and external audits • Complaint Handling i.e. in compliance with cGMP, 21 CFR Part 803 & 806 • CAPA Management • Change Control Management • Risk analysis and Risk management • Analysis and Trending • NCR, SCAR and CAPA Management • Assisting COO w/r to Regulatory Requirements. • Liaison between Operations and QAD • Calibration and Preventive Maintenance System Controls • Document Control Management System • First Article Inspection and Final Inspection • Lead MRB and QRB to resolve disposition issues • Implementation and monitoring Supplier Management System • Maintaining Supplier performance report • Assessing new critical suppliers and implementing suppliers management system • Addressing supplier non-conformance issues and resolving through direct communication and CAPAs • Creating required inputs, outputs and reports for Management Review • Creating and updating AVL (Approved Vendor List) • RMA Procedure and Complaint Handling Procedure (related to Medical Components/Devices/Fem Care products) • Complaint handling Procedure, analyzing, processing and escalating potential MDR and track closure compliance. • Managing QA Team and Training • Conducting Investigations & Managing Deviation • Managing, Compiling and Reviewing Master Batch Record, Annual Product Review and disposition of Batches Show less
-
-
-
Sustain, LLC
-
United States
-
Environmental Services
-
1 - 100 Employee
-
Quality Assurance Manager
-
Mar 2019 - Jul 2019
• Lead Quality Assurance Department as required through processes and methodologies • Gap Analysis • Creating and updating SOPs, Test Procedure, Work Instruction, Incoming and Final Inspection Procedures • Creating Verification & Validation protocol for different systems. • Ensuring that V &V Plan has been followed and carried out accordingly. • Scheduling and conducting internal and external audits • Complaint Handling i.e. in compliance with cGMP, 21 CFR Part 803 & 806 • Change Control Management • Risk analysis and Risk management • Analysis and Trending • NCR, SCAR and CAPA Management • Assisting COO w/r to Regulatory Requirements. • Liaison between Operations and QAD • Document Control Management System • Maintaining and Supervising Change Control System and Notification System • First Article Inspection and Final Inspection • Lead MRB and QRB to resolve disposition issues • Implementation and monitoring Supplier Management System • Maintaining Supplier performance report • Assessing new critical suppliers and implementing suppliers management system • Addressing supplier non-conformance issues and resolving through direct communication and CAPAs • Creating required inputs, outputs and reports for Management Review • Creating and updating AVL (Approved Vendor List) • RMA Procedure and Complaint Handling Procedure (related to Medical Components/Devices/Fem Care products/ ) • Complaint handling Procedure, analyzing, processing and escalating potential MDR and track closure compliance. Show less
-
-
-
-
Quality Systems Specialist
-
Feb 2018 - Jul 2018
• Creating and updating SOPs, Test Procedure, Work Instruction, Incoming and Final Inspection Procedures • Scheduling and conducting internal and external audits • Complaint Handling i.e. 21 CFR Part 803 & 806 • Reviewing and Gathering Field Reports from Field Engineers and Customer Service Engineer. • Analysis and Trending • NCR, SCAR and CAPA Management • Supervising and monitoring QA inspectors and Technical Assistant Engineers • Assisting Director of Quality Assurance w/r to Regulatory Requirements. • Communicating with Registrar (LRQA) regarding upgrade, recertification. • Liaison between Operations and QAD • Document Control Management System • Maintaining and Supervising Change Control System and Notification System • First Article Inspection and Final Inspection • Active member of MRB and QRB • California Prop 65 Compliance Project Lead • Implementation and monitoring Supplier Management System • Maintaining Supplier performance report • Assessing new critical suppliers and implementing suppliers management system • Addressing supplier non-conformance issues and resolving through direct communication and CAPAs • Creating required inputs, outputs and reports for Management Review • Creating and updating AVL (Approved Vendor List) • RMA Procedure and Complaint Handling Procedure (related to Medical Components/Device) • Complaint handling Procedure, analyzing, processing and escalating potential MDR and track closure compliance. Show less
-
-
-
Qosina
-
United States
-
Medical Equipment Manufacturing
-
1 - 100 Employee
-
Quality Assuranced Supervisor
-
Feb 2016 - Nov 2017
• Support Quality Assurance Department as required through processes and methodologies • Successful in achieving ISO 13485 certification • Gap Analysis • Creating and updating SOPs, Test Procedure, Work Instruction, Incoming and Final Inspection Procedures • First Article Inspection and Final Inspection • Training/Managing Quality Assurance Inspectors, Technicians and Internal Auditors • Scheduling and conducting internal and external audits • CAPA • Creating Testing and Inspection Criteria, Implementation, Training, Monitoring. • Creating Test procedures and protocols • Assisting Manager of Quality Assurance w/r to Regulatory Requirements. • Communicating with Registrar (LRQA) regarding upgrade, recertification. • Conducting & Scheduling Internal and External Audits • Liaison between Operations and QAD • Document Control Management System • Supervise Change Controls • Active member of MRB • California Prop 65 Compliance Project Lead • Ensuring Labeling requirements for Cosmetics and Medical devices are in compliance with statutory and regulatory authorities • Ensuring that labels are complying with ingredient disclosure, label warning and temper-resistance requirements. • Implementation and monitoring Supplier Management System • Maintaining Supplier performance report • Assessing new critical suppliers and implementing suppliers management system • Addressing supplier non-conformance issues and resolving through direct communication and CAPAs • Maintaining and controlling Product Change process and Notifications System • Creating and updating AVL (Approved Vendor List) • Calibration Procedure • RMA Procedure and Complaint Handling Procedure (related to Medical Components/Device) • Handling environmental aspects system related to ISO 14001. • Performing Pest control Audits and Product Preservation Audits • Complaint handling Procedure (Using MS CRM software and GP ERP System) Show less
-
-
-
MAXIMUS
-
Australia
-
Advertising Services
-
Quality Assurance Specialist
-
Dec 2013 - Oct 2015
• Support Quality Assurance Department as required through processes and methodologies • Verification &Validation • Creating Test Procedure, Work Instruction, Incoming and Final Inspection Procedures • CAPA • Training • Creating SOPs, Work Instructions, Testing and Inspection Criteria, Implementation, Training, Monitoring. • Assist Director of Quality Assurance w/r to Regulatory Requirements • Internal and External Audits • Liaison between Operations OPS and QAD • Document Control Management System • Implementation of Supplier Management System • RMA Procedure and Complain Handling Procedures Show less
-
-
-
-
Quality Assurance Software Specialist
-
Mar 2012 - Oct 2013
Validation & Verification Test Plan Quality Assurance Documentation SOPs, SRS. Training Validation & Verification Test Plan Quality Assurance Documentation SOPs, SRS. Training
-
-
-
AMAC
-
Chile
-
Construction
-
1 - 100 Employee
-
QA Software Specialist
-
2012 - Oct 2013
• Support Quality Assurance Department as required through processes and methodologies • Create test cases scenarios for field test trials • Verification &Validation of Software • Creating Test Procedure • CAPA • Training Q.A Inspectors and Technicians • Creating SOPs, Implementation, Training, Monitoring. • Analyzing Organizational Software Requirement • Assist Director of Quality Assurance w/r to Regulatory Requirements w/r Software. • Internal and External Audits • Liaison between R&D and QAD • Document Control Management System • Implementation of Supplier Management System • Calibration Procedure • RMA Procedure and Complain Handling Procedures Show less
-
-
-
Schick Technologies
-
Medical Device
-
QA Inspector/Tester
-
Oct 2006 - Feb 2012
• Utilize various inspection tools (i.e. Calipers, Visual Measurement Systems OGP, Tappi Charts) and inspection methodology (variable and attribute Sampling Plan) to assess production and engineering evaluation samples. • Ensure internal (Engineering, Marketing, and Manufacturing) and external customers communications relating to material non-conformance and inspection methodologies are addressed in accordance to QMS and ISO 13485 standards. • Evaluate the functionality of electrical components with Hipot/continuity testing equipment and visually observed the soldering workmanship per the IPC standard. • Assist the quality Manager and comply dimensional data to analyze component variation using statistical tools to identify the correlation with independent population and dimensional variation. (i.e. ANOVA). • Participate in non-conforming product disposition and implement incoming inspection strategy developed by the quality engineers. • Inspecting PCB Boards and Assembly with accordance to IPC-A-610 Standard for Acceptability of Electronic Assemblies • Conducting Software quality assurance throughout SDLC process (Requirement, GUI,FS,TS etc) • Participate in Verification and Validation (V&V) • Conducting Root cause analysis and CAPA (i.e. related to incoming parts and outgoing finished goods) • Conducting test and Validation in S/W Dept in different S/W tools such as C, C++, SQL, Lab view, Java etc • Assist Quality Manager/Director in FDA/ISO Audits. • Conducting Internal Audits • QA Documentation Show less
-
-
-
Schick Technology
-
Renewable Energy Semiconductor Manufacturing
-
QA Inspector/ Tester
-
2007 - 2009
-
-
-
-
Business/System Analyst
-
Mar 2002 - Apr 2006
Requirement Analysis, Design, Testing. Requirement Analysis, Design, Testing.
-
-
-
-
Quality Assurance Manager
-
2005 - 2006
-
-
Education
-
Institute of Business Administration
MCS, computer sciences -
IMS Punjab University
Master's degree, Computer Science
Community
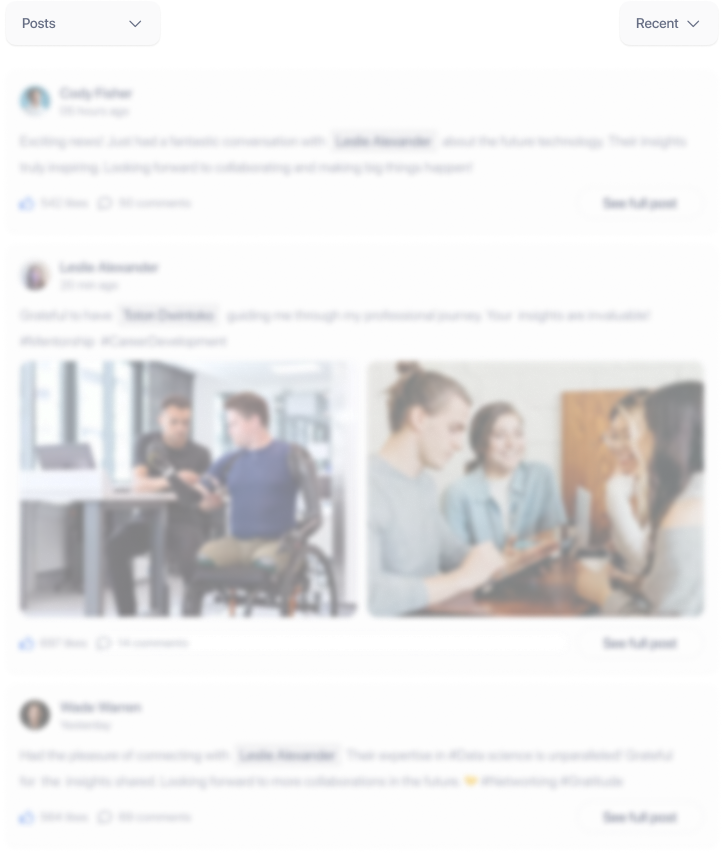