Farhan Ahmed
Manufacturing Engineer at Raytheon Technologies- Claim this Profile
Click to upgrade to our gold package
for the full feature experience.
-
Bangla Full professional proficiency
-
German Limited working proficiency
Topline Score
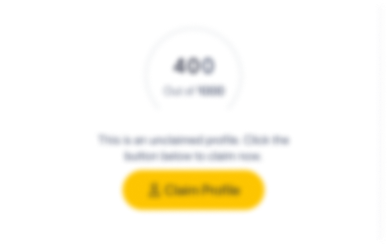
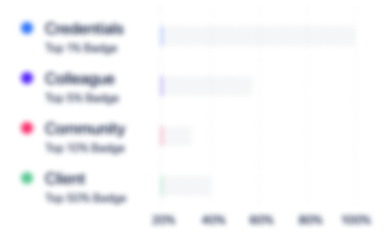
Bio


Experience
-
Raytheon Technologies
-
Corona, California, United States
-
Manufacturing Engineer
-
Feb 2020 - Present
- Generated Standard Work procedures to effectively produce composite panels for Boeing 737 LAV program - Updated Routers with necessary operations required to manufacture parts - Lead and conducted RCCA projects, and implemented corrective actions that ensured permanent solutions - Facilitated PFMEA completion for new parts, and assuring process adheres to quality requirements - Conducted EH&S Job Hazard Analysis & PFMEA’s in regards to process, safety, and operating equipment - Facilitated Kaizen projects to reduce scrap and improve productivity - Implemented SPC and Control charts; trained personnel in their use and interpretation as a quality control tool
-
-
-
Precision Castparts
-
United States
-
Aviation & Aerospace
-
700 & Above Employee
-
Supply Chain Manager
-
Jan 2019 - Feb 2020
- Supply chain management of all Titanium and Aluminum alloys- Assisted in Outside Processing of Ultrasonic Testing, Fracture toughness, Stress corrosion, and Chemistry testing- Managed all shop, tool, machine, and equipment required to function properly and efficiently- Managed and ordered Aluminum and Titanium Alloys using Just in Time principles- Determined Safety Stock levels required based on demand - Established contracts with suppliers to meet best possible price- Implemented min/max ordering schedules for shop and machine supplies- Data Analysis on expenditures using Lean Manufacturing principles
-
-
Manufacturing Engineer
-
Nov 2016 - Feb 2020
- Generated new part master routings with necessary sequence of operations - Generated Work Shop Orders with maximum efficiency to meet weekly/quarterly goals - Optimized number of forgings per job reducing the forgings, saw time, and scrap on job- Reduced excess use of raw material input on forgings which saved $115,000- Optimized allocations of material to work orders eliminating scrap and loss of material- Sustained a low scrap rate of 2% in Inventory of unusable material scrap using Lean principles- Demonstrated a scrap prevention project resulting in cost savings of $70,000- Scheduled and managed start and completion dates based on required operations of all parts - Generated cost estimations for new job quotes with respect to all cost of each operation and material cost
-
-
-
Carlton Forge Works
-
Paramount, CA 90723
-
Quality Engineer & Manufacturing Engineer Intern
-
Sep 2015 - Nov 2016
- Analyzed processes required for efficient design/processing of forgings for seamless rolled rings and open/closed die forgings; - Evaluated specifications of finished product; analyzed results from lab test reports, and ensured product meets specifications; - Updated and constructed First Article Inspection Reports (FAIR) for production to ensure quality standards in the production process; - Performed Furnace Analysis with a purpose to see if the heat up and cool down times are at high quality standards of the company. Analyzed equilibrium time during heat up and cool down practices, examined the reaction of furnace hearth in regards of heating specific parts. - Implemented a Linear regression model which helped in predicting the time it requires to Vacuum Degas Titanium 6-4 parts, and as a result, decreased lead time by 4hrs and reduced cost - Planned jobs using the Oracle DBMS
-
-
-
Dauntless Industries Inc.
-
West Covina, California
-
Industrial Engineer Intern
-
Jun 2015 - Dec 2015
- Constructed a facility redesign to maximize production efficiency, new storage layout for finished goods, raw materials, and mold tools - Implemented an Automated Packaging system, determined the optimal number of workers needed for efficient flow for packaging process, improved employee working condition/workstation by applications of Ergonomics and Lean principles, and eliminated wastage of space - Defect rate was reduced by specifying assignable cause variations in production process, using statistical quality control methods, implemented improvements by use of conveyor belt on Encore Bottle Cap production
-
-
-
Wine Country Houdini - Gourmet Gift Baskets
-
Fullerton, CA
-
Industrial Engineer Intern
-
Jun 2014 - Nov 2014
- Supported production processes to increase productivity and efficiency by creating line staffing - Improved line balancing for assembly lines - Identified and resolved Bottlenecks - Distributed tasks for a calibrated flow - Conducted Time Motion studies - Designed, introduced, and implemented an improved layout that reduced the number of workers from 12 workers to 10 workers and standardized an improved method of the task - Supported production processes to increase productivity and efficiency by creating line staffing - Improved line balancing for assembly lines - Identified and resolved Bottlenecks - Distributed tasks for a calibrated flow - Conducted Time Motion studies - Designed, introduced, and implemented an improved layout that reduced the number of workers from 12 workers to 10 workers and standardized an improved method of the task
-
-
Education
-
California State Polytechnic University-Pomona
Bachelor of Science (BS), Industrial Engineering -
California State Polytechnic University-Pomona
Lean Six Sigma - Green Belt Certification
Community
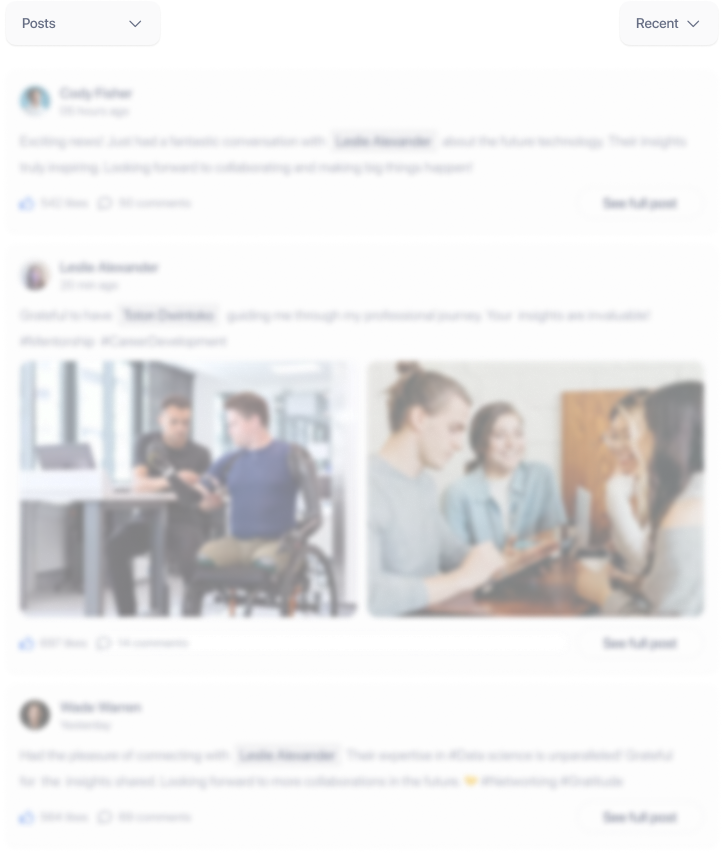