Fabio Carlini de Oliveira
Diretor Geral at Sterilex Científica- Claim this Profile
Click to upgrade to our gold package
for the full feature experience.
-
English Native or bilingual proficiency
-
Portuguese Native or bilingual proficiency
Topline Score
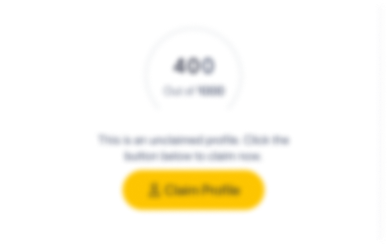
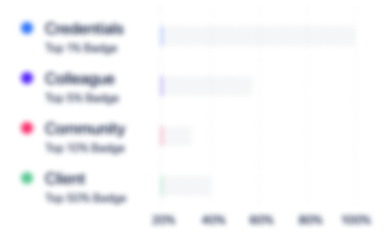
Bio

Ednaldo Silveira
Fabio has an exceptional knowledge about end-to-end process in different type of business. I had a chance to discuss opportunities of improvements with him about my organization. He showed me an impressive leadership with exceptional capacity to keep people engaged and build strength relationship to create a sense of organization and focus. In addition, Fabio has incredible capacity of handle several things in the same time, structure his thought from technical and management perspective that graduate him to be a valued advisor.

Ricardo Chaves
I would like to register as client my great satisfaction in relation to the results obtained after the procedures performed by the consulting and guidance of VALOREM, especially about Fábio Carlini work's. The approaches designed to improve operational results lead to a rapid return, all due to alignment, clarity of efforts and focus on what really makes sense for sustainable and robust development, conditioning the company to a new level and thus preparing it for new and bigger challenges. Passo para registrar como cliente a minha grande satisfação em relação aos resultados conquistados após trabalhos realizados através da consultoria e direcionamento da VALOREM, em especial ao trabalho de Fábio Carlini. As abordagens direcionadas para as melhorias dos resultados operacionais conduzem ao rápido retorno, tudo em função do alinhamento, clareza dos esforços e foco no que realmente faz sentido para um desenvolvimento sustentável e robusto, condicionando a empresa para um novo patamar e desta forma a preparando para novos e maiores desafios.

Ednaldo Silveira
Fabio has an exceptional knowledge about end-to-end process in different type of business. I had a chance to discuss opportunities of improvements with him about my organization. He showed me an impressive leadership with exceptional capacity to keep people engaged and build strength relationship to create a sense of organization and focus. In addition, Fabio has incredible capacity of handle several things in the same time, structure his thought from technical and management perspective that graduate him to be a valued advisor.

Ricardo Chaves
I would like to register as client my great satisfaction in relation to the results obtained after the procedures performed by the consulting and guidance of VALOREM, especially about Fábio Carlini work's. The approaches designed to improve operational results lead to a rapid return, all due to alignment, clarity of efforts and focus on what really makes sense for sustainable and robust development, conditioning the company to a new level and thus preparing it for new and bigger challenges. Passo para registrar como cliente a minha grande satisfação em relação aos resultados conquistados após trabalhos realizados através da consultoria e direcionamento da VALOREM, em especial ao trabalho de Fábio Carlini. As abordagens direcionadas para as melhorias dos resultados operacionais conduzem ao rápido retorno, tudo em função do alinhamento, clareza dos esforços e foco no que realmente faz sentido para um desenvolvimento sustentável e robusto, condicionando a empresa para um novo patamar e desta forma a preparando para novos e maiores desafios.

Ednaldo Silveira
Fabio has an exceptional knowledge about end-to-end process in different type of business. I had a chance to discuss opportunities of improvements with him about my organization. He showed me an impressive leadership with exceptional capacity to keep people engaged and build strength relationship to create a sense of organization and focus. In addition, Fabio has incredible capacity of handle several things in the same time, structure his thought from technical and management perspective that graduate him to be a valued advisor.

Ricardo Chaves
I would like to register as client my great satisfaction in relation to the results obtained after the procedures performed by the consulting and guidance of VALOREM, especially about Fábio Carlini work's. The approaches designed to improve operational results lead to a rapid return, all due to alignment, clarity of efforts and focus on what really makes sense for sustainable and robust development, conditioning the company to a new level and thus preparing it for new and bigger challenges. Passo para registrar como cliente a minha grande satisfação em relação aos resultados conquistados após trabalhos realizados através da consultoria e direcionamento da VALOREM, em especial ao trabalho de Fábio Carlini. As abordagens direcionadas para as melhorias dos resultados operacionais conduzem ao rápido retorno, tudo em função do alinhamento, clareza dos esforços e foco no que realmente faz sentido para um desenvolvimento sustentável e robusto, condicionando a empresa para um novo patamar e desta forma a preparando para novos e maiores desafios.

Ednaldo Silveira
Fabio has an exceptional knowledge about end-to-end process in different type of business. I had a chance to discuss opportunities of improvements with him about my organization. He showed me an impressive leadership with exceptional capacity to keep people engaged and build strength relationship to create a sense of organization and focus. In addition, Fabio has incredible capacity of handle several things in the same time, structure his thought from technical and management perspective that graduate him to be a valued advisor.

Ricardo Chaves
I would like to register as client my great satisfaction in relation to the results obtained after the procedures performed by the consulting and guidance of VALOREM, especially about Fábio Carlini work's. The approaches designed to improve operational results lead to a rapid return, all due to alignment, clarity of efforts and focus on what really makes sense for sustainable and robust development, conditioning the company to a new level and thus preparing it for new and bigger challenges. Passo para registrar como cliente a minha grande satisfação em relação aos resultados conquistados após trabalhos realizados através da consultoria e direcionamento da VALOREM, em especial ao trabalho de Fábio Carlini. As abordagens direcionadas para as melhorias dos resultados operacionais conduzem ao rápido retorno, tudo em função do alinhamento, clareza dos esforços e foco no que realmente faz sentido para um desenvolvimento sustentável e robusto, condicionando a empresa para um novo patamar e desta forma a preparando para novos e maiores desafios.

Experience
-
Sterilex Científica
-
Brazil
-
Medical Equipment Manufacturing
-
1 - 100 Employee
-
Diretor Geral
-
Aug 2022 - Present
-
-
Diretor de Finanças e Operações (Head de Supply Chain, Compras, TI, Finanças e Recursos Humanos)
-
Aug 2021 - Aug 2022
- Implementação de modelo de gestão conforme SOX e boas práticas de governança corporativa- Gestão do processo de implementação ERP - SAP Business One - Modelo de gestão financeira com resultados expressivos em geração de valor- Melhorias diversas de processos com foco em expansão, sustentabilidade do negócio e desenvolvimento de capabilidades chaves- Alinhamento estratégico e desdobramento operacional com foco na ágil e efetiva implementação- Reorganização da proposta de desenvolvimento humano com foco na consolidação de equipe de alta performance.- Expansão portfólio de produto por meio de parceria estratégicas e desenvolvimento técnico Show less
-
-
Superintendente de Operações
-
Jan 2021 - Aug 2021
Gestão estratégica das áreas de Supply Chain, Finanças, Fiscal e Recursos Humanos.
-
-
Gerente de Operações e Supply Chain
-
Nov 2020 - Jan 2021
Gestão das áreas de Supply Chain e Fiscal
-
-
-
Gestão Valorem
-
Brazil
-
Business Consulting and Services
-
Strategic Turn Around - Operations and Supply Chain Associate
-
Nov 2019 - Present
Significant results in turnaround through the generation of value supported by strong expertise in Operations, Supply Chain and Finance. Systemic vision and executive experience with balance between short-term deliveries and the business sustainability. Our Solution: - Operations and Supply Chain support guided by the financial and strategic perspectives Our strengths: - Global Experience - Strategic partnership - Strong network in different segments - Focused in Operations and Supply Chain but with background in finance and strategy - Team building and people development - Good communication across different hierarchic levels - Effective results in different segments Our differential: - Commitment in achieving goals - Teaching by doing - Result Culture Show less
-
-
-
Aptar
-
Packaging and Containers Manufacturing
-
700 & Above Employee
-
Supply Chain Brasil & Cajamar Operations Director
-
Jul 2017 - Oct 2019
Successful career, resulting in three merit promotions in almost seven years. History below: - Supply Chain Brazil & São Paulo COO – Since Oct 2018- Supply Chain Brazil & Cajamar COO – Jun 2017– Sep 2018- Plant Manager - Cajamar – Jan 2014 – May 2017- Industrial Manager - Cajamar - Oct 2012 – Dec 2013Aptar Group is a US$ 6 Billion US based company provider of packaging, dispensing, and sealing solutions, for the beauty, personal / home care, prescription drug, health care, injectable, food / beverage markets (12700 people / 18 countries). Three sites in Brazil / 1000 people.Production / Manuf Eng. / Operational Excellence / Full Supply Chain / Purchasing / Procurement / Quality / Maintenance / HSE.Team of 420 employees (1 Senior Manager / 5 Managers).Main Results: Lean approach - Hard savings / cost avoidance of US$ 7,8 MM + people’s engagement & development + Reduction of 67% in the absenteeism rate + customer Service Level improvement + quality rate. Cajamar site was scored in 2017 the “best” amongst 67 in the world. Supply Chain reorganization resulting in a lean / fast process, improving the service level rate (90% to 98%) supporting the business growth (double size in the 7 years) in 2018; High Tech expertise for assembling / anodizing (capacity increase, cost competitiveness, high quality level) Supply foot print strategy (make or buy) Portfolio harmonization strategy (reduction of 1000 SKU + 40% of capacity increase + cost competitiveness); Turnaround for Jundiai Operation (+business volume + operational capacity) resulting in an annual saving of US$ 1,5 million project to 2019; Quality process reorganization with strong improvement in the area results and client perception; Landfill Certification / PCMAP - ISO 22716 / FSSC 22000 and ISO 14000 maintenance. Reduction of slow moving level Supplier / subcontractors development program Ergonomic and Safety concepts implementation: TOP3 in the group Show less
-
-
Plant Manager
-
Jan 2014 - Jul 2017
-
-
Industrial Manager
-
Oct 2012 - Dec 2013
-
-
-
ROSSINI MURTA
-
Brazil
-
Automotive
-
1 - 100 Employee
-
Operations Manager
-
May 2007 - Oct 2012
Rossini Murta is a Brazilian company, 450 employees and revenues of R$ 90 MM focused on machining mechanical parts for different applications and customers (ZF, Caterpillar, Volkswagen, Valtra, TRW, General Electric and others for South and North America Market). Responsibilities: Manufacturing & Industrial Engineering / Production Management / Operational Excellence & Continuous Improvement / Production Planning (Materials & Scheduling) / Warehouse Management / Quality (Supplier, Product & Process, Systems) / Maintenance Engineering & Management of Facilities / Supply Chain Management (Sourcing, Purchasing, Logistics and Customer Service) / HSE Management / Project Management / Product Engineering / HR and Finance. Team: 400 people - 4 managers / 2 supervisors Results: Lean Manufacturing, TPM and Six Sigma - savings / cost avoidance of US$ 7 MM and a manufacturing cost reduction of 40%. Considering freight optimization, Scrap reduction, labor and machine efficiency, new chart organization, make or buy decision and cost reduction as a result of negotiations with suppliers and implementation of contracts aligned with service level agreements. Potential development of employees: The project is based on lean techniques and area management training - focused on consistent continuous improvement & teamwork culture development; Service Level managing program implementation: OTIF Improvement (65% to 99%) and overall quality rate from 100.000 to 30 PPM S&OP implementation. Emphasis on sales forecast. MRP implementation (TOTVS) OHSAS 18000, ISO 14000, ISO TS16949, QSB and VDA 6.3 Implementation Working capital improvement. stock reduction (120 to 20 days) and payment deadline. Zero accident program. From 48 to 576 (Thousand Labor hours without an accident) Balanced Score Card. Implemented to drive the all of the organization to determine and to follow short, medium & long term strategies Show less
-
-
-
RFS - Radio Frequency Systems
-
Germany
-
Telecommunications
-
400 - 500 Employee
-
Manufacturing Manager
-
2004 - 2007
American Company (Alcatel-Lucent Group), 400 employees in Brazil and an annual revenue of R$ 250 MM focused on Wireless Infrastructure Solutions, RF Transmission & Distribution Solutions, Radio Link Networks and Broadcast & Defense Systems present in over 20 countries. Areas included as my role within Manufactring Management: Production Management (Planing/ Manufacturing & Industrial Engineering / Warehouse Management / Quality (Process) / Logistics A total team of 100 employees, with 4 supervisors Lean Manufacturing / 6 Sigma implementation resulting an accumulated hard savings / cost avoidance of US$ 8 MM and a manufacturing cost reduction of 50%. Considering freight optimization, Scrap reduction, labor and machine efficiency, new chart organization, make or buy projects (subcontracting no core business process) and nationalization projects for several families of products. Potential development of employees: The project is based on lean techniques and area management training (on the job or/and structured training strategy) - focused on consistent continuous improvement & teamwork culture development; Product Nationalization: Management of transferring of High Technology projects from European and North American sites in order to nationalize the manufacture of strategic product families creating a new business unit. Service Level managing program implementation: OTIF Improvement (From 65% to 99%) and overall quality rate from 300.000 to 120 PPM (parts per million) by zero defect program MRP implementation – SAP R3 Reduction of manufacturing lead-time / productive capacity expansion. Reduction of 70% for the lead-time to manufacture the main product families by new process & layout organization (pull process) and fast setup as a result of SMED implementation including a total capacity expansion of over 300%, contributing strongly for the inventory reduction and working capital. Zero accident program implementation (30 to 700) - TLWA Show less
-
-
-
Valeo
-
France
-
Motor Vehicle Parts Manufacturing
-
700 & Above Employee
-
Process Technologist
-
2001 - 2004
Lean Manufacturing methodologies implementation such as VSM, TPM, 5S & Visual Management, Cell Design, PDCA, SMED, Hoshin, 5S, Kanban, Kaizen projects, Poka-Yoke and FMEA implementation Layout and workflow modification All assembly lines (10) were modified to cell design considering one-piece flow production resulting in an overall productivity gain of 30% and a reducing of 45 % of labor efficiency Layout and workflow modification All assembly lines (10) were modified to cell design considering one-piece flow production resulting in an overall productivity gain of 30% and a reducing of 45 % of labor efficiency Self-control implementation The quality activities in the assembling lines were totally transferred for the direct labor by the implementation of a development & training program implementation (Versatility Matrix), visual documents standardizing the work activities, poka-yokes and CEP aligned with the mains risks identified by the FMEA update. Ergonomic concepts implementation: The project was based on application of standard ergonomic tools such as OCRA (Occupational Repetitive Action Checlist) / SI (Strain-Index) and HAL (Hand Activity Level) for work station validation obtaining as result the elimination of ergonomic issues. Project team member for new products: Process and quality member for new products development. Show less
-
-
-
-
Tecnologo de Processos
-
1999 - 2001
-
-
Education
-
University of North Carolina at Chapel Hill
Executive MBA, Part of "ONE MBA" MBA program -
Fundação Getulio Vargas
Executive MBA, Part of "ONE MBA" MBA program -
Rotterdam School of Management, Erasmus University
Executive MBA, Part of "ONE MBA" MBA program -
University of Miami Herbert Business School
Executive MBA, Administração e Negócios -
EGADE Business School del Tecnológico de Monterrey
Executive MBA, Part of "ONE MBA" program -
厦门大学
Executive MBA, Part of "ONE MBA" MBA program -
Fundação Getulio Vargas (BR)|Rotterdam Management (NL)| Xiamen University (CH)|EGADE Business School|(MX)Miami Business School (USA)
Global Executive MBA OneMBA, Business Management -
FIA Business School
Master of Business Administration (MBA), Business Administration and Management, General -
AMA – American Management Association – New York
Master of Business Administration (MBA), Planejamento Estratégico -
Fundação Vanzolini
Pos Graduação em Administração Industrial -
Faculdade de Tecnologia de São Paulo - FATEC-SP
Bachelor of Technology (B.Tech.), Processsos de Fabricação -
Anhanguera Educacional
Engineer's degree, Mechanical Engineering -
SENAI Suíço-Brasileira
Community
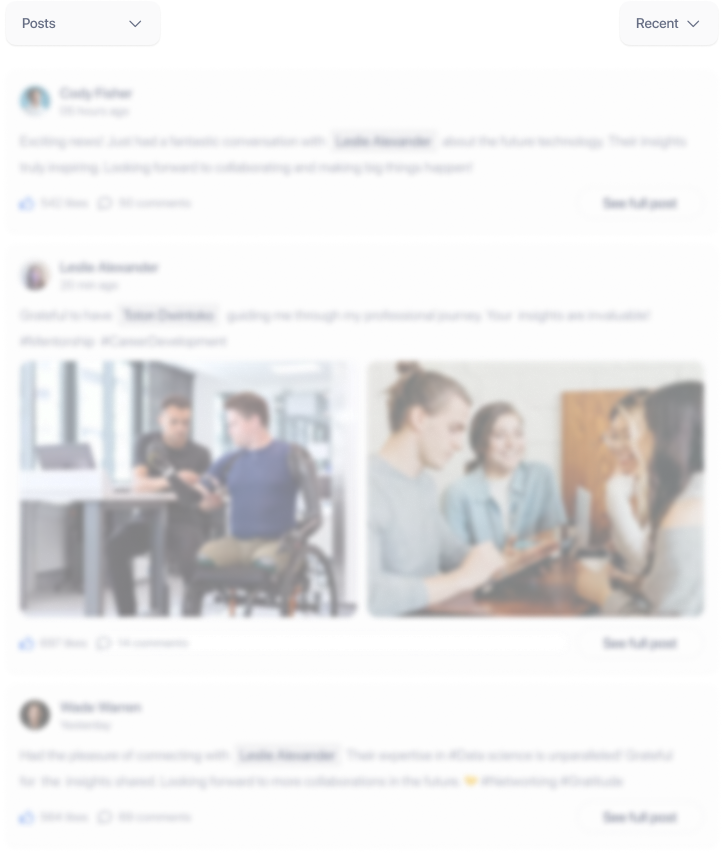