Evon Small
Production Manager at Federal White Cement- Claim this Profile
Click to upgrade to our gold package
for the full feature experience.
Topline Score
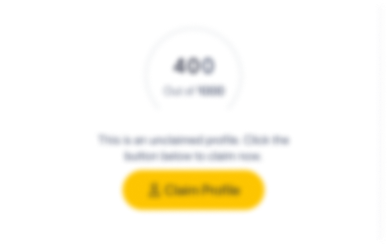
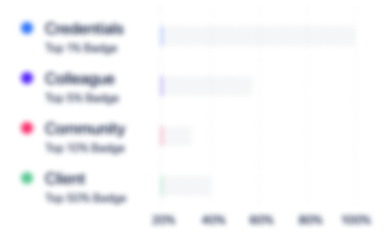
Bio

Gerald Young
Evon has worked in the cement industry for a number of years. He is highly motivated and an excellent employee Gerald L Young

Godfrey Stewart
I experienced first hand Evon's competence as a process engineer while we worked together at Caribbean Cement Co. Ltd. He was good at summarizing data into useful trends that supported reliability and quality and presented that data simply so that it was well understood by different levels of individuals in the business. His responses were timely and he has good communication and relationship skills.

Gerald Young
Evon has worked in the cement industry for a number of years. He is highly motivated and an excellent employee Gerald L Young

Godfrey Stewart
I experienced first hand Evon's competence as a process engineer while we worked together at Caribbean Cement Co. Ltd. He was good at summarizing data into useful trends that supported reliability and quality and presented that data simply so that it was well understood by different levels of individuals in the business. His responses were timely and he has good communication and relationship skills.

Gerald Young
Evon has worked in the cement industry for a number of years. He is highly motivated and an excellent employee Gerald L Young

Godfrey Stewart
I experienced first hand Evon's competence as a process engineer while we worked together at Caribbean Cement Co. Ltd. He was good at summarizing data into useful trends that supported reliability and quality and presented that data simply so that it was well understood by different levels of individuals in the business. His responses were timely and he has good communication and relationship skills.

Gerald Young
Evon has worked in the cement industry for a number of years. He is highly motivated and an excellent employee Gerald L Young

Godfrey Stewart
I experienced first hand Evon's competence as a process engineer while we worked together at Caribbean Cement Co. Ltd. He was good at summarizing data into useful trends that supported reliability and quality and presented that data simply so that it was well understood by different levels of individuals in the business. His responses were timely and he has good communication and relationship skills.

Experience
-
Federal White Cement
-
Canada
-
Building Materials
-
1 - 100 Employee
-
Production Manager
-
Oct 2022 - Present
-
-
Project
-
Nov 2020 - Oct 2022
-
-
-
thyssenkrupp
-
Germany
-
Industrial Machinery Manufacturing
-
700 & Above Employee
-
Business Development Sales / Cem BU Service
-
Jul 2019 - Oct 2020
• Provides technical insight on CEM revamp opportunities, based on plant specific operations / technology while working together with tkIS Canada service sales colleagues in the region • Support the development and implementation plans for strategic CEM accounts that exceed expectations in revenue retention/growth, account profitability, and customer satisfaction/loyalty. • Identify, develop and manage partners within CEM industry to achieve goals. • Develops a complete understanding of the CEM organizations’ structure and key buying influencers. • Performs technical client presentations articulating the value proposition of product / solution / service offerings within CEM industry. • Supports the group with input for development of forecasts, budgets, customer proposals and operating plans • Provides frequent updates and participates in reviews for account planning based on changing market, customer conditions, and competitive activity. • Provides input and maintains all customer business / technical / outage activities, leads, opportunities and results in CRM (MS Dynamics 365), relevant to the CEM market in the region Show less
-
-
-
Holcim
-
Switzerland
-
Wholesale Building Materials
-
700 & Above Employee
-
Production Coordinator
-
May 2018 - Apr 2019
Safety leadership:• Promotes safety by ensuring tailgate and safety meetings are held with the area group.• Develops and implements the proper safety procedures (SOPs) with a continuous improvement perspectiveContinuous Improvement:• Work with key leaders of the Cross Functional Teams which consist of key Production, Quality, Maintenance and Process personnel • Owns Root Cause Failure Analysis • Proactively looks for improvements and performance gains while eliminating reliability issues.Financial:• Participates in the annual production budget preparation and contributes to the input of the raw materials • Manages expansion plant yearly budget including refractory and support services.• Adheres to the overall production forecast and reviews the distribution forecast.• Formulates capital and cost savings projects to improve efficiency and submits appropriation requests to secure project capital.Coordination• Defines the expansion area yearly objectives (e.g. safety, environmental performance, quality, cost reduction, performance) with input from plant objectives, cascade it with all employees.• Manage, direct and coordinate overall activities of the department and interaction with other departments.• Plans and executes refractory work for K6.• Is the commissioning coordinator and lead for the startup of equipment after major outages.• Updates and creates operational SOPs and implements in a continuous improvement model.• Coordination with the Finish Mill and Shipping Coordinator stocking and handling of incoming additive raw materials via rail.• Ensures environmental abatement additives are available, manage supply chain as required.Personnel• Application and administration of the Collective Agreement.• Responsible for team development of assigned personnel by providing resources, training and direction needed to promote team process. Show less
-
-
Sr Process Coordinator
-
Jul 2011 - Apr 2018
* Participate in Housekeeping & Safety Audits * Supervise the process group * Facilitates daily plant performance meeting which involves a cross functional teams * Overall responsibility for all process lines (PreCaliner kiln, Long dry kiln, Cement & Raw Mills (ball mills)* Conducts process measurements, heat & mass balances and process audits to continually optimize process lines and establish benchmarks.* Involves in commissioning of new Precalciner Kiln and VRM lines and emission mitigation systems (SNCR & DAA systems)* Maintain environmental emission standards* Work on special projects to optimize and improve efficiency of process units* Involves in root cause analysis (RCA) and decision making team on recommendations to prevent re-occurrence of failures.* Power champion at Lafarge Exshaw plant. Coordinate action plans around power reduction at the plant. Conduct power audits at other Lafarge plants.* “Lucie” champion at Lafarge Exshaw plant. Tune the parameters in the control software (“Lucie”) to optimize the operation of the Kilns & mills Show less
-
-
Process Cordinator
-
Jun 2008 - Jun 2011
* Participate in Housekeeping & Safety Audits * Participate in team based safety program and conduct regular VFL * Work on a number of projects to improve safety on the job* Perform job safety analysis (risk assessments)* Direct responsibility for Two Cement Ball Mills that produces five cement products, A four stage Pre-Calciner * Kiln & Coal Mill (indirect firing)* Process inspections & measurements on process lines* Works closely with quality department in setting optimum targets to optimize burning while achieving quality clinker & cement* Conduct Audits on Kiln & Mills process lines* Power & Specific Heat Reduction Programs Power Champion (coordinating the power reduction program) * Provides SOP for safe operation of units Show less
-
-
-
GraceKennedy Ltd.
-
Jamaica
-
Consumer Services
-
500 - 600 Employee
-
Project Coordinator
-
Oct 2007 - Dec 2007
• Coordinated & documented all policies and procedures with all department heads (Sales, Procurement, International Trade, Warehousing, Production, Customer Service. • Documented all areas of high potential negative financial impact to the company profitability. • Implemented systems improvements to prevent production loss. • Implemented systems to mitigate or minimize high risk that have the potential for high negative financial impact on the company. Show less
-
-
-
Caribbean Cement Company
-
Jamaica
-
Wholesale Building Materials
-
1 - 100 Employee
-
Process Engineer
-
Oct 1989 - Oct 2005
Process Engineer • Provided guidelines for stable operation of the production units to improve efficiency and reduce production cost. • Analyze plant data to assess operating performance levels and to develop and implement solutions for continuous process improvements and optimizations. • Work closely with Quality Department to ensure clinker quality will deliver the optimum product quality at the minimal operation cost. • Conduct Root Cause Analysis (RCA) whenever there is failure to prevent a reoccurrence. • Make recommendations to modify process designs, operating systems and hardware/software equipment to optimize the process. • Work closely with electrical, instrument and maintenance departments to ensure reliability of the various operating units. Production Shift Supervisor Supervise twenty five unionized employees from various disciplines. • Coordinated and scheduled activities of workers. • Prepared monthly and other production reports. • Troubleshoot and resolved problems quickly. • Controlled the efficiency and effectiveness of overtime work. • Organized and coordinated activities for emergency repairs. • Promulgated good health and safety practices for all employees. • Ensured proper operation and maintenance of all equipment and auxiliaries. • Controlled expenditure in accordance with budget. Show less
-
-
Education
-
The University of the West Indies, Mona
-
The University of the West Indies, Mona
Post Graduate Diploma in Management Studies, Operations Management and Supervision -
The University of the West Indies, Mona
BSc, Honors
Community
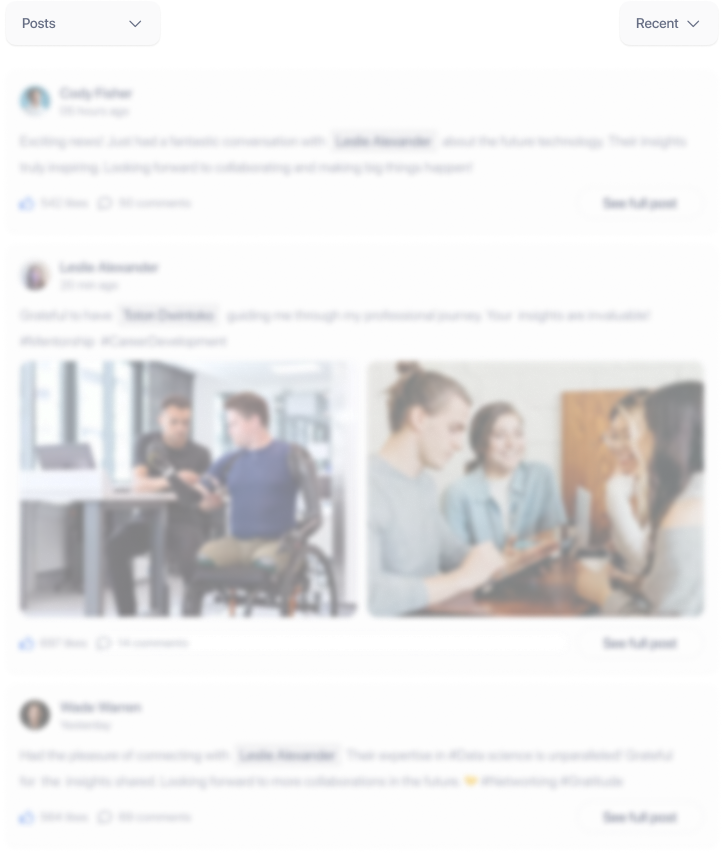