
Evens Romilus, MBA
Manufacturing Manager at Organized Living- Claim this Profile
Click to upgrade to our gold package
for the full feature experience.
-
English Native or bilingual proficiency
-
French Native or bilingual proficiency
-
Haitian Creole Native or bilingual proficiency
-
Spanish Elementary proficiency
Topline Score
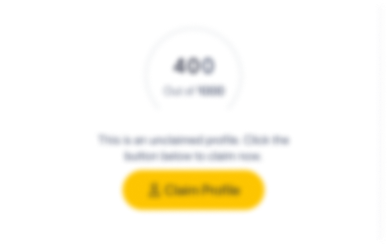
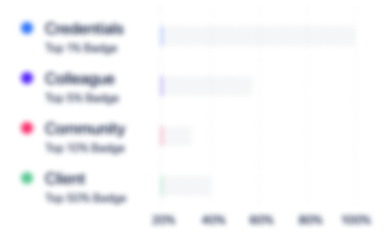
Bio


Experience
-
Organized Living
-
United States
-
Building Materials
-
1 - 100 Employee
-
Manufacturing Manager
-
Nov 2020 - Present
Plan, determine optimal utilization of manufacturing workers and equipment to meet manufacturing goals.Determine if new manufacturing machines, methods are needed.Ensure that manufacturing stays on schedule and within budget.Coordinate manufacturing with Sales, Marketing, Procurement, and other departments, as well as with vendors and shippers.Help ensure that customer, statutory, standards, and internal requirements are met or exceeded.Hire, train, and evaluate manufacturing workers; monitor workers to ensure they meet performance and safety requirements.Analyze manufacturing data and identify trends, anomalies, and opportunities for improvement; identify and utilize methods of making manufacturing process more efficient and effective (reducing waste, using lean).Write manufacturing reports and present to top management.Direct corrections (corrective action) of any manufacturing problems that may arise;
-
-
-
Faurecia
-
France
-
Motor Vehicle Manufacturing
-
700 & Above Employee
-
PC&L Transformation Manager
-
Nov 2018 - Present
Production control and logistics Transformation Manager| strategic planning| implement necessary changes to enable performance at optimum ability| demonstrate innovation and creativity|attention to details|influence key decision|proactive and able to use initiative
-
-
Autonomous Production Manager (UAP)
-
Aug 2019 - Nov 2020
Manage overall operations and is responsible for the effective and successful management of labor, productivity, quality control and safety measures as established and set for the Operations Department. Ensure safe and efficient operations. Serve as a company representative on regulatory issues. Enhance the operational procedure, systems and principles in the areas of information flow and management, business processes, enhanced management reporting and looks for opportunities to expand systems. Carry out supervisory responsibilities in accordance with company's policies and applicable laws.Responsibilities may include interviewing, selection and hiring; training new and existing employees; planning, assigning and directing work; authoring and discussing with employees performance appraisals; addressing employee performance and corrective action plans; employee motivation and rewards. Organizing the budget of the company in collaboration with the director.
-
-
UAP Manager
-
Nov 2016 - Nov 2020
-
-
UAP Manager/Superintendent
-
Aug 2017 - Mar 2018
Follow production plans, as well as Group standard processes; assure feasibility of production plans.Achieve financial targets: prepare and present the budget; manage the actual production costs based on "ideal" costs; maintain product margin, and monitor serial productivity (labor level, material consumption, etc.).Manage the team: assure appropriate staffing, maintain working environment according to Group Health, Safety & Environment (HSE) standards , detect and advise training needs, share information (transparency), participate in career management initiatives, etc.Serve as official plant representative to the customer: meet established customer specifications concerning cycle time, delivery, quality, quantity and costs; implement preventative and corrective measures in the production process to assure that customer demands are properly met; coordinate with client's quality team to meet all customer standards.Implement action plans in order to improve functionality/productivity and to obtain program and Group objectives; make necessary corrective adjustments.Participate in the creation of Production System Efficiency (PSE) projects.Coordinate resource planning with Industrial Engineering department concerning stocks, equipment, staffing, activities, etc.Maintain dashboard indicators/status reports to monitor lead time, supply-chain targets, HSE performance, etc.
-
-
UAP Supervisor
-
Nov 2016 - Aug 2017
Lead the Quality Cost & Delivery (QCD) Performance for designated groups:Direct QCD initiatives: set targets, implement plans, track daily results, make appropriate adjustments in resource planning in order to attain desired results.Drive actions for improvement: communicate with the Autonomous Production Unit Manager, Production Supervisors of other shifts, and support functions to ensure a transparent information flow, collaborate to define improvement areas and precise action plans.Manage team performance: know team problems, define areas for performance improvements with team members, drive teamwork, lead problem solving groups, lead workshops on quality improvement methods (5S, TPM, 6M…).
-
-
-
Dallas Group of America, Inc.
-
United States
-
Chemical Manufacturing
-
1 - 100 Employee
-
Manufacturing Supervisor
-
Apr 2016 - Nov 2016
Responsible for induction of all newcomers in my perimeter. Ensure the organization and scheduling of training actions. Analyze flexibility and multi-skills, and define training plans in order to develop team autonomy and improvement spirit. Monitor certification process for each operator and update in real time flexibility grid. Manage daily absenteeism, holidays, safety rules enforcement, environment risk analysis, APZ communication & performance boards update. Ensure respect of standards stops (breaks, meetings) by checking systematically on Genba, and validate operators working time. Maintains quality service by establishing and enforcing organization standards. Responsible for personnel involvement and ensure a positive social climate. Ensure that standard of reaction are applied with rigor (eg. KOSU) perform escalation according to standards. Conduct operators’ annual appraisals, as well as salary, review with career interviews. Provides manufacturing information by compiling, initiating, sorting, and analyzing production performance records and data; answering questions and responding to requests. Creates and revises systems and procedures by analyzing operating practices, record-keeping systems, forms of control, and budgetary and personnel requirements; implementing change.
-
-
-
Valeo
-
France
-
Motor Vehicle Parts Manufacturing
-
700 & Above Employee
-
Manufacturing Production Supervisor
-
May 2013 - May 2016
Accomplishes manufacturing staff results by communicating job expectations; planning, monitoring, and appraising job results; coaching, counseling, and disciplining employees; initiating, coordinating, and enforcing systems, policies, and procedures. Maintains staff by recruiting, selecting, orienting, and training employees; developing personal growth opportunities. Maintains work flow by monitoring steps of the process; setting processing variables; observing control points and equipment; monitoring personnel and resources; studying methods; implementing cost reductions; developing reporting procedures and systems; facilitating corrections to malfunctions within process control points; initiating and fostering a spirit of cooperation within and between departments. Completes production plan by scheduling and assigning personnel; accomplishing work results; establishing priorities; monitoring progress; revising schedules; resolving problems; reporting results of the processing flow on shift production summaries. Maintains quality service by establishing and enforcing organization standards. Ensures operation of equipment by calling for repairs; evaluating new equipment and techniques. Provides manufacturing information by compiling, initiating, sorting, and analyzing production performance records and data; answering questions and responding to requests. Creates and revises systems and procedures by analyzing operating practices, record-keeping systems, forms of control, and budgetary and personnel requirements; implementing change.
-
-
Customer Service Representative/Master Scheduler
-
May 2013 - Apr 2016
• Develops planning reports in support of new and updated plans, programs and regulations for all GM OE products• Receives, processes and verifies the accuracy of orders from customers utilizing the organization’s internal SAP systems and customer purchase orders.• Initiates required action for response to customer service requests for order changes, including the maintenance of order/customer information files and communicates changes to the appropriate personnel/departments.• Ensures and provides quality service to both internal and external customers.• Receives inquiries from and/or contacts the organization’s branch/regional offices to resolve a variety of order-related issues.• Accesses the company’s internal systems to obtain and extract order information and provide customer service management with the data for inclusion in various scheduled and special reports• Performs assigned system maintenance to various electronic order files.• Participates and provides expertise as a member of the customer service’s departmental team. • The team's objectives are develop and recommend changes to existing methods and systems to increase the accuracy, efficiency and responsiveness of the customer service department as a whole• Prepares and presents detailed reports on development proposals to program team, logistics, customer service• Collects a variety of statistical data and prepare reports and information such as customer delivery rating, take rates, forecast.• Participate in new work process tools to enhance the Project Controls deliverables• Participate and provide input to enhance and improve department functions, work procedures and instructions
-
-
Education
-
Indiana Wesleyan University
Master's degree, Applied Management -
Indiana University Southeast
Bachelor of Arts (B.A.), English Language and Literature/Letters -
Ashworth College
Associate of Science (A.S.), Criminology/Pre-Law
Community
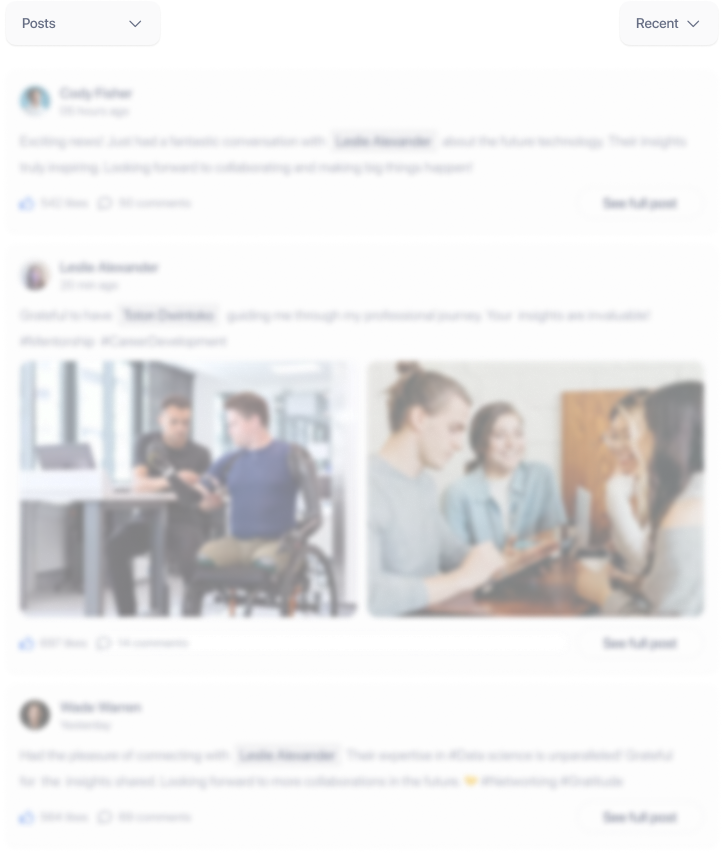