Eunice Qing
QA at Sensitron Semiconductor- Claim this Profile
Click to upgrade to our gold package
for the full feature experience.
-
English -
Topline Score
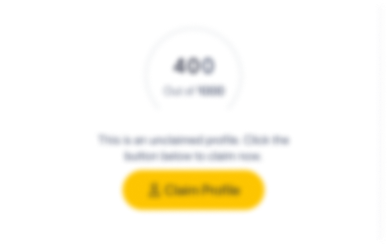
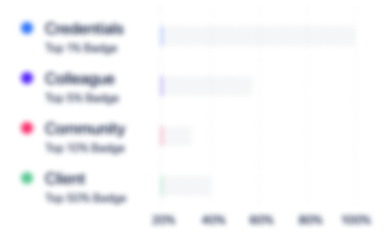
Bio
0
/5.0 / Based on 0 ratingsFilter reviews by:
Experience
-
Sensitron Semiconductor
-
United States
-
Defense and Space Manufacturing
-
1 - 100 Employee
-
QA
-
Feb 2012 - Present
1.Establish quality system and procedure for raw material purchase and incoming inspection to sure the quality is conform with the requirements of PO and quality requirements of the headquarter in American. 2.Assess the suppliers and vendors’ qualification. Audit the vendors as schedule on site and provide audit report, follow up the corrective& preventive actions implementation to sure the quality is continuous improve. 3.Communicate with the supplier to solve the quality issue if raw material non-conformity happened. 4.Set up quality system to monitor, check and manage all the products in processing and outgoing to meet the production quality requirements. 5.Set up SOP, train, audit and follow up to make SOP real effective to achieve continuous improving. 6.Coordinate with production and equipment departments to sure quality purpose is achieved. 7.Communicate with the customer to know more their requirements and assist solve the customer’s complaints as well to increase their satisfaction. 8.Assist and support the third party audit on site or off-site from the headquarter and their customers complaints. 9.Report the quality status to Quality Director in American headquarter regularly and irregularly
-
-
-
-
Fabric Technologist
-
Jan 2008 - Jan 2012
1.Review and analyze Quality Manuals of asigned Strategic Customers.1) Highlight differences between company internal standard test methods and requirements against asigned Strategic Customer requirements.2) Evaluate cost increase due at differences of test methods, technical requirements and submissions procedures.3) Assess if requirements and procedures should be changed or eliminated, even if they have been settled time ago. In every case, customer / garment vendor has to be informed, and new procedure accepted for both sides.4) Evaluate potential risks of articles adopted by asigned Strategic Customers. 2. Work closely with every production department and clients to find quality risks and reduce potential issues and further establish necessary action plans. 3. Analyze and establish Temporary and Final Technical Specification according to Customer’s testing conditions and test method making sure that mid-points are correlated with company internal technical Specification. Closely communicate with customers to avoid misunderstandings to make the production going smoothly and reduce the claims in future.1) Achieve necessary agreements with Customers on Quality issues.2) Coordinate with developments for new project inquiry.3) Co-ordinate with QC for fabric technical requirements.4) Communicate with customers during bulk production stage for technical issues. 4. Deal with the claims from customers and give timely feedback and quality analysis and compensation suggestion, settle the final claims and inform related departments and monitor them do corrective actions.
-
-
Knitting Quality Specilist
-
Sep 2004 - Jan 2008
1. In charge of assessing raw material testing samples, establishing and maintaining raw materials testing database.2. In charge of preparing all the claim information and samples to claim suppliers and follow up it.3. Provide suppliers performance data support to top management which is one of the most important indicators for supplier performance assessments to make purchasing decision4. In charge of collecting knitting quality information and collating and analyze data to provide valuable quality information and quality report. Trace information on knitting side for production analysis. Push daily quality improvement.5. In charge of establishing and monitoring knitting quality inspector job. Work together with them to improve and enhance process control.6. Assist QA improve quality management system including QMS documents writing and distributing as well as QMS internal and external audit.7. Write new SOP (Standard Operation Procedure)according knitting operation requirements.8. Assist knitting manager train SOP for operators and give the test.9. Audit SOP periodically or aperiodically in workshop, improve and update SOP. Complete SOP report and give the improvement suggestion.10. Help knitting department translate documents from Chinese to English and vice versa, all kinds of statistic reports and relative paper work.11. Communicate with the plants located in Spain or Philippines to propel the quality projects processing.
-
-
Education
-
Nanjing University of Aeronautics and Astronautics
Associate's degree, Business English -
南京师范大学
Bachelor's degree, 英语
Community
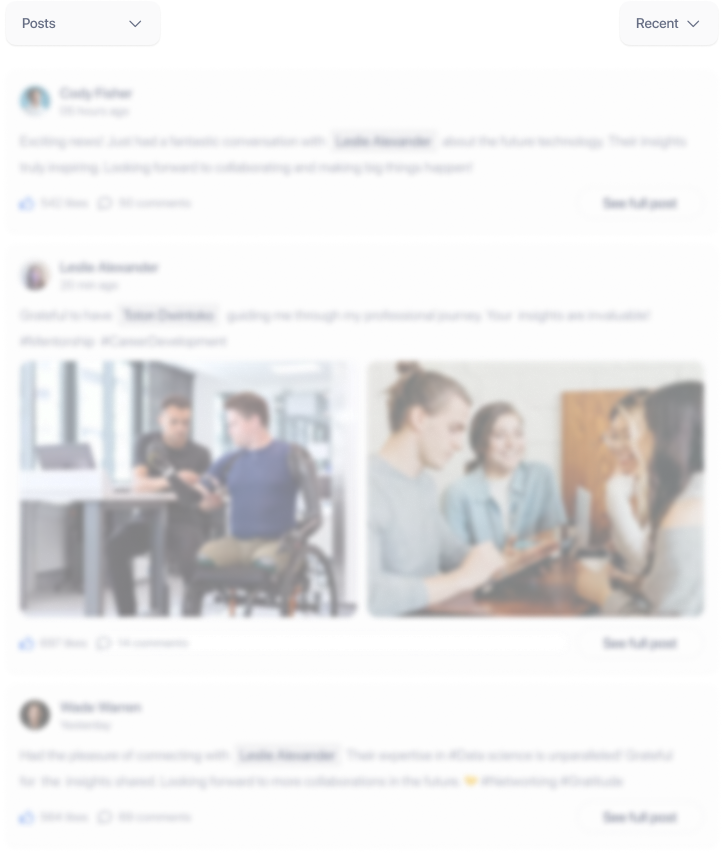