Erika Lences Belianska
Program coordinator at Udenco- Claim this Profile
Click to upgrade to our gold package
for the full feature experience.
Topline Score
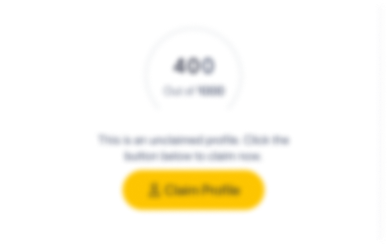
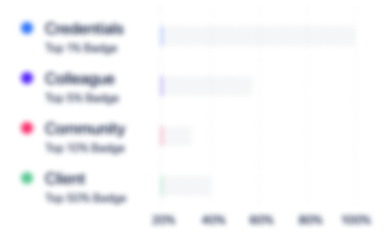
Bio


Credentials
-
Quality management system and Internal Auditor - ISO 9001:2015 and ISO 19011:2018
CeMS, s.r.o.Jun, 2019- Oct, 2024 -
Project management
FBE Bratislava s.r.o. - For Business ExcellenceNov, 2016- Oct, 2024 -
Quality management System - Internal Auditor - according to standard ISO 13485:2016 and ISO 19011:2018
Systémy jakosti s.r.o.Aug, 2019- Oct, 2024
Experience
-
Udenco
-
Netherlands
-
Industrial Machinery Manufacturing
-
1 - 100 Employee
-
Program coordinator
-
Jan 2016 - Present
Cooperation with the Top management of the company and all parties in the holding group with preparation and realization of sales activities. Responsible for communication with all customers in term of special requests out of standard operative processes – changes in forecasting, price offers for special technical support or other requests, communicating the problems in deliveries with financial impacts etc.Managing customers´ requests within our company – spreading information and establishing the team of people needed to fulfill customers´ requests – keep timing of customer task under control.Support of all departments to deliver products of customers in agreed quality level and on time.Analyzing differences in customers´ orders in relation to forecasting.Coordinating all activities of production phase out – collect and share the information, prepare plan, inform our departments, check the financial aspect like excess stock and communicate the plan and rest material value back to customer for final agreement.Preparing sales plan. Show less
-
-
Logistics coordinator
-
May 2013 - Jan 2016
Responsible for whole logistics process – receiving and recording customer orders, production planning, material ordering and deliveries trucking, optimizing of inventory level in accordance to cash flow, watching covering of production requirements, managing of material complains, communication with suppliers at daily base, managing of finished goods transportation
-
-
-
SiiX Corporation
-
Japan
-
Appliances, Electrical, and Electronics Manufacturing
-
300 - 400 Employee
-
Logistics assistant
-
May 2013 - May 2013
Communication with suppliers at daily base, suppliers relationship developing, purchase orders issuing, deliveries tracking, preparation of PO confirmations, team support for all logistics assistants, invoice issuing, checking and recording, ordering of overhead material, material receiving, finish goods shipping out. Communication with suppliers at daily base, suppliers relationship developing, purchase orders issuing, deliveries tracking, preparation of PO confirmations, team support for all logistics assistants, invoice issuing, checking and recording, ordering of overhead material, material receiving, finish goods shipping out.
-
-
-
Samsung Electronics
-
South Korea
-
Computers and Electronics Manufacturing
-
700 & Above Employee
-
Purchaser
-
Jan 2013 - Apr 2013
Development of suppliers relationships; obtaining customer demand information; participation on production planning according to customer´s delivery schedule and current level of finished goods stock considering ordered materials and production capacity; preparation and continuous updating of the purchase plans for the assigned range material; particular communication with suppliers for the purpose of materials ordering, managing and monitoring of deliveries timing, handling of claimed parts, processing of related documents; issuing purchase orders; invoices obtaining in time; control of content and timely processing of documents relating to the material purchases; solving quantitative discrepancies and price differences with suppliers Show less
-
-
-
Ryoka (M) Sdn Bhd
-
Malaysia
-
Plastics Manufacturing
-
1 - 100 Employee
-
Material controller
-
May 2011 - Dec 2012
Development of suppliers relationships; purchase contract preparation; analyzing of possibilities of cost saving relating to purchasing and proceeding cost saving purpose; obtaining customer demand information; participation on production planning according to customer´s delivery schedule and current level of finished goods stock considering ordered materials and production capacity; preparation and continuous updating of the purchase plans for the assigned range of inputs and goods (basic materials and overhead materials); communication with suppliers particularly for the purpose of materials ordering, managing and monitoring of deliveries timing, handling of claimed parts, processing of related documents (goods receipt slips, goods issue slips, invoices, credit notes and other); issuing purchase orders and claims against suppliers; invoices obtaining in time; control of content and timely processing of documents relating to the material purchases in relation of accounting, reporting to the parent company, VAT agenda and cast flow; matching of goods receipt slips/goods issue slips with suppliers´ invoices/credit notes and solving quantitative discrepancies and price differences with suppliers and informing the accounting department about occurred discrepancies in time Show less
-
-
Junior material controller
-
Sep 2010 - May 2011
Responsibility for material planning including inventory control, placing orders to suppliers; responsibility for making in-house production plan in conjunction with production planner; responsibility for controlling the material supply and products receiving schedule for sub contract manufacturing companies; making necessary arrangement for materials to keep production running, invoicing to customers
-
-
Education
-
Univerzita Mateja Bela v Banskej Bystrici
Inženýr (Ing.), The economy and management of the small and medium enterprises
Community
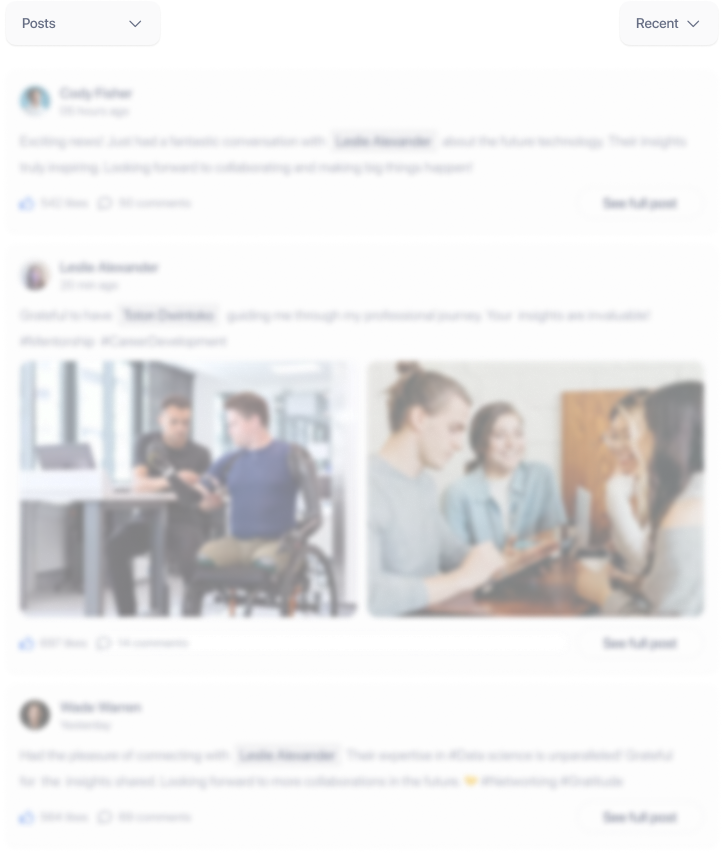