
Eric Zimmerman
Chief Operating Officer at Duraco- Claim this Profile
Click to upgrade to our gold package
for the full feature experience.
Topline Score
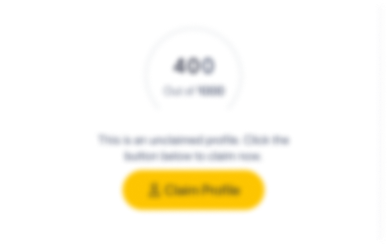
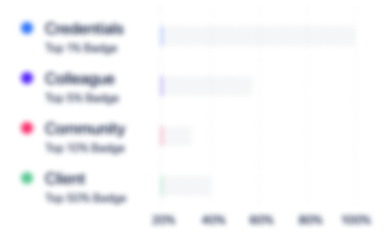
Bio

Daniel S. Nelson
I had the pleasure of sitting at the executive table at Gaco Western with Eric for 7 years as we built and then divested a highly valuable market leading company. While at Gaco, Eric rapidly built his own leadership team that established operations excellence under his guidance. Within the Executive Leadership Team, I saw Eric lean in at various times to challenge his peers during decision making processes, thus improving the outcomes of the decisions. We also had seasons of fun together laughing at each other's jokes, but fun aside, it was a privilege for me to work with Eric so closely over this period of time and to witness his professionalism, leadership and his ability to connect and command respect at any level.

Sean Lotspeich
It was my pleasure to work with Eric at the Firestone Building Products company, part of the Bridgestone Corporation, in 2019 and 2020. Eric led Operations while I was leading Quality. He had a complicated role, with many plants under his authority. Eric was an excellent partner, supporter and driver of advancing the quality within the organization, and helping us progress the continual improvement journey and culture. Nothing ever felt like an unnecessary "battle" between Ops and Quality, due in part because Eric fostered a very collaborative, team-oriented environment. He has a personality that is easy to get along and work with, but he also knows how to get bottom-line results. It would be my pleasure to work with Eric again. I highly recommend him.

Daniel S. Nelson
I had the pleasure of sitting at the executive table at Gaco Western with Eric for 7 years as we built and then divested a highly valuable market leading company. While at Gaco, Eric rapidly built his own leadership team that established operations excellence under his guidance. Within the Executive Leadership Team, I saw Eric lean in at various times to challenge his peers during decision making processes, thus improving the outcomes of the decisions. We also had seasons of fun together laughing at each other's jokes, but fun aside, it was a privilege for me to work with Eric so closely over this period of time and to witness his professionalism, leadership and his ability to connect and command respect at any level.

Sean Lotspeich
It was my pleasure to work with Eric at the Firestone Building Products company, part of the Bridgestone Corporation, in 2019 and 2020. Eric led Operations while I was leading Quality. He had a complicated role, with many plants under his authority. Eric was an excellent partner, supporter and driver of advancing the quality within the organization, and helping us progress the continual improvement journey and culture. Nothing ever felt like an unnecessary "battle" between Ops and Quality, due in part because Eric fostered a very collaborative, team-oriented environment. He has a personality that is easy to get along and work with, but he also knows how to get bottom-line results. It would be my pleasure to work with Eric again. I highly recommend him.

Daniel S. Nelson
I had the pleasure of sitting at the executive table at Gaco Western with Eric for 7 years as we built and then divested a highly valuable market leading company. While at Gaco, Eric rapidly built his own leadership team that established operations excellence under his guidance. Within the Executive Leadership Team, I saw Eric lean in at various times to challenge his peers during decision making processes, thus improving the outcomes of the decisions. We also had seasons of fun together laughing at each other's jokes, but fun aside, it was a privilege for me to work with Eric so closely over this period of time and to witness his professionalism, leadership and his ability to connect and command respect at any level.

Sean Lotspeich
It was my pleasure to work with Eric at the Firestone Building Products company, part of the Bridgestone Corporation, in 2019 and 2020. Eric led Operations while I was leading Quality. He had a complicated role, with many plants under his authority. Eric was an excellent partner, supporter and driver of advancing the quality within the organization, and helping us progress the continual improvement journey and culture. Nothing ever felt like an unnecessary "battle" between Ops and Quality, due in part because Eric fostered a very collaborative, team-oriented environment. He has a personality that is easy to get along and work with, but he also knows how to get bottom-line results. It would be my pleasure to work with Eric again. I highly recommend him.

Daniel S. Nelson
I had the pleasure of sitting at the executive table at Gaco Western with Eric for 7 years as we built and then divested a highly valuable market leading company. While at Gaco, Eric rapidly built his own leadership team that established operations excellence under his guidance. Within the Executive Leadership Team, I saw Eric lean in at various times to challenge his peers during decision making processes, thus improving the outcomes of the decisions. We also had seasons of fun together laughing at each other's jokes, but fun aside, it was a privilege for me to work with Eric so closely over this period of time and to witness his professionalism, leadership and his ability to connect and command respect at any level.

Sean Lotspeich
It was my pleasure to work with Eric at the Firestone Building Products company, part of the Bridgestone Corporation, in 2019 and 2020. Eric led Operations while I was leading Quality. He had a complicated role, with many plants under his authority. Eric was an excellent partner, supporter and driver of advancing the quality within the organization, and helping us progress the continual improvement journey and culture. Nothing ever felt like an unnecessary "battle" between Ops and Quality, due in part because Eric fostered a very collaborative, team-oriented environment. He has a personality that is easy to get along and work with, but he also knows how to get bottom-line results. It would be my pleasure to work with Eric again. I highly recommend him.

Experience
-
Duraco
-
Manufacturing
-
1 - 100 Employee
-
Chief Operating Officer
-
Aug 2021 - Present
PE owned, high growth business for specialty adhesive tapes, release liners, and coatings for a wide range of industries and consumer applications. PE owned, high growth business for specialty adhesive tapes, release liners, and coatings for a wide range of industries and consumer applications.
-
-
-
-
Vice President of Operations
-
Jan 2021 - Jul 2021
PE owned, high growth business focused on paint, coatings, sealants, spray foam insulation, adhesives, underlayments, and other building envelope products. Major chemistries include acrylic, epoxy, silicone, asphalt, and urethane. Asphalt products are focused on both building envelope as well as paving applications. Annual revenue of approximately $1 billion.Consultant role responsible for 25 manufacturing facilities in the US, UK, and Canada, the manufacturing engineering group as well as the continuous improvement team over this same footprint.• Focused on the integration of a $400 MM acquisition in January of 2021 and a $200 MM business in May 2021: manufacturing leadership, EHS, quality, manufacturing execution, standard work and Lean deployment.• Evaluated, established, and re-organized manufacturing, engineering, and continuous improvement teams focused on creating disciplined standards and operational metrics to support the business growth.• Gained synergies through manufacturing footprint and warehouse consolidations thereby reducing complexity and cost.• Supported engineering and safety reviews for rebuild of production unit damaged by fire prior to acquisition.• With HR, developed a process to improve recruitment and retention of plant teammates.
-
-
-
Firestone Building Products
-
United States
-
Wholesale Building Materials
-
500 - 600 Employee
-
Director of Global Manufacturing and Engineering
-
Nov 2017 - Mar 2020
Firestone Building Products Purchased Gaco Western in April of 2017.Provided leadership for 15 manufacturing locations across the U.S., Germany, and Spain as well as the project and process engineering functions with a team of over 1,500 worldwide. A member of the Executive Leadership Team and on the BOD for two FSBP European entities.Key accomplishments:· Rebuilt the leadership team at the largest facility to properly address and sustain a manufacturing turn-around operation in 2018. Significant achievements were sustained in safety, quality, leadership, training, infrastructure improvements, mechanical reliability, process control, and labor relations. This success resulted in increased reliability and stability as demonstrated by a 27% increase in production from 2017 vs. current. OSHA TIR reduced by over 33% to 1.05.· Finalized the integration of Gaco Western into the FSBP model while maintaining and propagating best practices between both.· Re-focused the Engineering team on project management, timelines, and established core competencies in the process engineering function. This team was responsible for approximately $50M in spending on infrastructure, capacity improvements, and new product introductions.· Provided oversight and advocacy for the new construction, start-up, commissioning, and ERP implementation of the insulation board facility in Germany.· Led a manufacturing team to complete over $5M in cost-down activities across all plants in 2018 and an additional $3M in 2019.· Employed lean continuous improvement tools in all facilities. The manufacturing group is currently in year three of this journey and continues to demonstrate significant capacity increases as measured through OEE2 improvements in all manufacturing product lines.
-
-
-
-
Vice President, Operations and General Manager
-
Jun 2011 - Nov 2017
As a member of the Executive Leadership Team, instrumental in growing the business from approximately $40M in 2011 to approximately $150M in 2016. Provided the leadership and strategic direction for the Operations side of the business which included Customer Service, Purchasing, Manufacturing, Engineering, Inventory Management, and Logistics.Gaco Western offers a family of brands which offer best-in-class solutions for a variety of commercial, industrial, and residential applications including specialty coatings for roof, pedestrian and traffic decking and spray polyurethane foam insulation.Key accomplishments:· Worked closely with the IB firm to detail the Operations side of the business during the selling process.· Built and led a team of high-performing operations professionals focused on improving the business and exceeding customer expectations.· Established a focus on safety through leadership upgrades, detailed processes, and training. Reduced the Total Injury Rate (TIR) from 8.86 (a three-year average) to 2.47 (a three-year average); 2017 was 1.58.· Supported the manufacturing team in creating significant improvements in manufacturing areas that more than doubled silicone production by:o Developing standardized work procedures for processing and change-overso Implementing effective scheduling processes· Reduced mis-manufactured production from a rate of 1.4% to less than 0.2% through detailed root cause analysis and corrective actions, eliminating over 500K pounds of mis-manufactured material annually.· Defined procedures to qualify alternate raw materials and utilized these qualifications to leverage over $2M in annual raw material savings with global suppliers.· Worked with a team to establish quality processes, including chemical compounding validation studies, Measurement Systems Analysis (MSA), and test method Standard Operating Procedures (SOP) where none existed previously.
-
-
-
-
Regional Operations Manager
-
Oct 2005 - Jun 2011
Provided leadership and management of three manufacturing facilities to include customer service, production, quality control, warehousing and trucking. Responsible for the effective management of 150 employees, a $20 million expense budget and $7 million in inventory to produce over $100 million in sales.Hydrite is a specialty chemical manufacturer and distributor operating in the Midwest with nine manufacturing facilities serving a wide variety of market segments with industrial, food grade, FCC and OTC products.Key Accomplishments:*Established a strong safety culture to significantly decrease the number of recordable injuries.*Focused the management team and developed solid manufacturing competencies.*Developed and implemented lean manufacturing principles to drive a system of continuous improvements, lowering manufacturing costs by 10%.*Reduced inventory by over 25% by establishing inventory management tools at different levels of the organization.*Represented operations in the development of the strategic long range goals of the different business groups served by the manufacturing locations.*Worked with large, national customers to develop new products and processes.*Developed and implemented plans to comply with Department of Homeland Security and International Fire Codes.
-
-
-
QA Products Inc.
-
United States
-
Food and Beverage Manufacturing
-
Director of Operations
-
2004 - 2005
QA Products is a Confectionery topping producer with the largest US market share serving industrial, food service, wholesale bakeries and bakery distribution accounts,Provided leadership and direction for a 120 person operations group including manufacturing, warehousing, sanitation, quality control, supply chain and engineering. Managed a $9 million budget producing $35 million in sales. Member of the Executive staff of the company.Key Accomplishments:*Established a professional and accountable management and supervisory group.*Established quality processes to re-gain business with large national accounts.*Achieved the company's highest AIB score of 920.*Instituted visual management and scheduling tools that improved extrusion productivity by over 10%*Developed an incentive plan that engaged the workforce in safety and productivity improvements.*Implemented a skill progression plan for the maintenance department to set pay criteria.*Led large capacity expansion capital projects that allowed company to meet sales growth for existing and new products.*Directed a HACCP team to thoroughly review all production areas to improve food safety.
-
-
-
Henkel Technologies
-
IT Services and IT Consulting
-
100 - 200 Employee
-
Plant Manager
-
1998 - 2003
Re-focused the facility to increase productivity and safety performance while ensuring compliance with all regulations. Managed a $6 million expense budget to produce over $50 million in annual sales. Deeply involved with sales and marketing in all new product launches and customer requirements.Henkel Surface Technologies is a chemical manufacturing company producing surface treatment chemicals, and adhesives, sealants, and extrusions for the automotive industry. ISO 9000, ISO 14000, and TS16949 certified.Key Accomplishments:* Developed and implemented a new plant business process which increased on time shipping from 93% to 99.8%.* Implemented a behavioral-based safety program that increased associate ownership of the safety process.* Implemented an associate involvement program to establish lean manufacturing techniques that led to significantly higher production rates.* Increased first pass quality rate from 79% to 95%.* Doubled the production rate on a highly utilized cell to allow more production on two shifts than was previously capable on three shifts.* Implemented an incentive system tied to plant metrics led by and for plant associates.* Led the facility to become ISO 14001 Certified. (September 2002)* Transitioned the facility’s quality system to TS 16949, which replaced QS 9000.* Provided leadership and direction for a cross-functional site team, which designed and built a $4 million automated process adding $5 million in annual sales. * Provided leadership and direction for integrating a newly acquired company.* Established a common warehouse and logistics flow.* Redesigned the associate pay progression system to align it for both facilities.* Managed Henkel’s St. Louis, Missouri facility for 15 months, producing inorganic surface pre-treatment chemicals prior to being promoted to the Oak Creek facility.
-
-
-
-
Business Unit Leader
-
1994 - 1998
Solutia Inc.is a world-class, food grade chemical manufacturing facility producing chemical leavening agents for the baking industry. Responsible for all aspects of two departments including budgeting, cost forecasting, capital planning, and all quality and compliance issues. Products sold generated $18 million in annual sales. The production department was a sold-out, high profile unit with many single sourced customers. Direct supervisory experience with salary and union workforces. * Led a cross-functional team from sales, engineering, technology, marketing, technical service, and plant process engineering to develop a $10 million expansion to double production capacity. The project was presented and approved in 1998.* Completed projects to achieve over a 30% capacity increase, setting record production levels. * Developed and co-chaired a plant wide safety and health inspection program .* Extensive involvement in the award of the Star Status from OSHA’s Voluntary Protection Program. (July ’97)
-
-
-
General Chemical Corporation
-
United States
-
Plant Manager
-
1991 - 1994
Responsible for a plant with annual gross profit margin of $2.5 million. Developed and implemented environmental, safety, and product quality programs.Direct supervisory experience with union and non-union workforces.* Advanced from plant manager over Detroit operation, to Operations Supervisor, then to Plant Manager of East St. Louis Plant within two years.* Lowered labor costs per ton by 25% by increasing production throughput.* Gained significant project management experience through design, installation, and operation of a $250,000 pollution control project uniquely applied to a specialized production process.
-
-
-
US Army
-
United States
-
Law Enforcement
-
1 - 100 Employee
-
Captain
-
1987 - 1991
Maintenance and logistics manager with positions of increased responsibility - from platoon leader, to maintenance control officer, to assistant support operations officer.* Managed the production control of a 260-person maintenance company.* Planned logistical needs and executed these plans during major military training exercises.* Established and managed accounts in excess of $400,000 for external maintenance and supply support during Operation Desert Storm. Maintenance and logistics manager with positions of increased responsibility - from platoon leader, to maintenance control officer, to assistant support operations officer.* Managed the production control of a 260-person maintenance company.* Planned logistical needs and executed these plans during major military training exercises.* Established and managed accounts in excess of $400,000 for external maintenance and supply support during Operation Desert Storm.
-
-
Education
-
United States Military Academy at West Point
Bachelor of Science (BS), Mechanical Engineering -
Washington University in St. Louis
Master of Business Administration (MBA), Business Administration, Management and Operations
Community
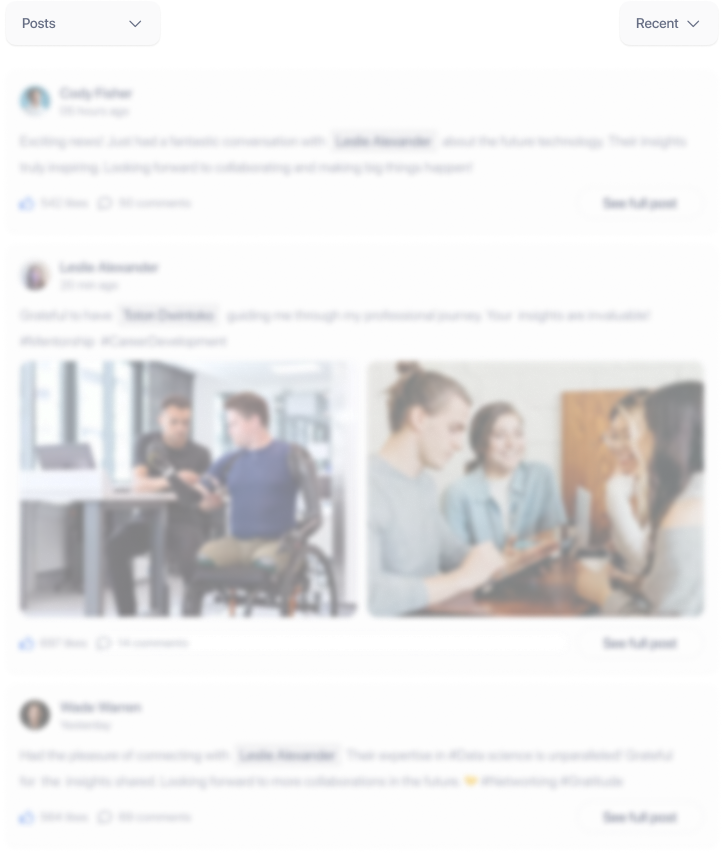