Eric Wilder
VP of Sales, Inventory and Operations Planning at VIS, LLC SC- Claim this Profile
Click to upgrade to our gold package
for the full feature experience.
Topline Score
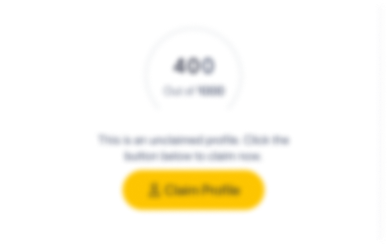
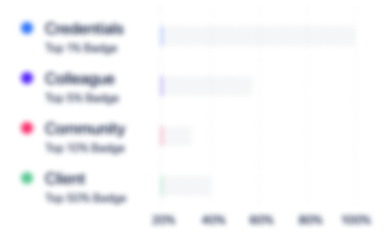
Bio


Experience
-
VIS, LLC SC
-
United States
-
Executive Offices
-
1 - 100 Employee
-
VP of Sales, Inventory and Operations Planning
-
Jan 2023 - Present
- Leading initiative to reduce inventory risk and improve on time delivery through improved demand planning systems, forecasting and SIOP planning- Leading corporate initiative to reduce inventory over 27%- Improved on time delivery by 23% for $200M group of businesses- Reduced sku complexity by 37%
-
-
VP of Strategy and Continuous Improvement
-
Jul 2021 - Dec 2022
-
-
VP of Continuous Improvement
-
Apr 2020 - Jun 2021
- Implemented Benchmarking and KPI Management- Implement Blackbelt program for lean tools organization development- Led initiative to role out standard work flow at a new distribution center that consolidated 4 smaller facilties and cut labor cost over 57%.
-
-
-
Filtration Group
-
United States
-
Manufacturing
-
300 - 400 Employee
-
Manufacturing Operations Manager
-
Mar 2018 - Apr 2020
- Top performer/Recognized as Key Talent by FG corporate team and created value proposition for specified product releases in coordination with commercial team to maximize brand value as development opportunities. - Managed 100 person team. - Reduced turnover from turnover from 81% to 16%. - 37% EBITDA improvement through labor & material productivity lean improvements, sku rationalization efforts, and adding capacity. - Partnered with sales to win market share & quickly add capacity using lean flow improvement to increase sales by 53% with Home Depot Show less
-
-
Value Stream and Safety Manager
-
Jan 2017 - Mar 2018
- Improved service levels to over 95% - Sustained one-year safety incident free using Dupont Stop Safety Training.
-
-
Rotating Manufacturing Supervisor
-
Jan 2016 - Dec 2016
-
-
-
Colfax Fluid Handling
-
Machinery Manufacturing
-
200 - 300 Employee
-
Continuous Improvement Manager
-
Jan 2013 - Dec 2015
Danaher Spinoff Company- Managed operational excellence rollout at 11 businesses and developed a collaborative workforce model through benchmarking and best practice sharing.- Mapped out and implemented corrective actions as lean/business leader for three business units with $100M annual revenue to emphasize customer value and eliminate waste.- Reduced working capital needs by 27% and managed eight purchase part Kanban events. - Reviewed KPI performance of over 2.5 years while shifting NC facility from a level 1 to 3 (best in class of 11 facilities).- Administered two pull events with $131K in savings under Shingijutsu and Harris Group, focusing on improving manufacturing efficiency and working capital reduction. Show less
-
-
Lean Manufacturing Engineer
-
Aug 2011 - Dec 2012
-
-
-
Pelton & Crane
-
United States
-
Medical Equipment Manufacturing
-
1 - 100 Employee
-
Manufacturing Engineer Contractor
-
Aug 2010 - Jul 2011
PELTON CRANE, A DANAHER COMPANY Charlotte, NC August 2010 to July 2011 Fulfilled customer and stakeholder needs within statutory and regulatory requirements while supporting Pelton Crane in acquiring the ISO 9000 certification and FDA compliance for multiple assembly lines. Participated in 2 DBS Events/Kaizens, including lean line design and standard work while removing waste. Collaborated with engineers to create new designs for products and processes. PELTON CRANE, A DANAHER COMPANY Charlotte, NC August 2010 to July 2011 Fulfilled customer and stakeholder needs within statutory and regulatory requirements while supporting Pelton Crane in acquiring the ISO 9000 certification and FDA compliance for multiple assembly lines. Participated in 2 DBS Events/Kaizens, including lean line design and standard work while removing waste. Collaborated with engineers to create new designs for products and processes.
-
-
-
Equitable Property Group
-
Charlotte, NC
-
Principal/Entrepreneur
-
2008 - Aug 2010
- Procured, sold, and leased 35 single and multi-unit fixer-upper properties while creating and offering custom real estate solutions. - Settled terms and formulated marketing plans to attract investors and lock deals while achieving desired business objectives. - Raised funds, administered construction, and coached a small team to market options. - Procured, sold, and leased 35 single and multi-unit fixer-upper properties while creating and offering custom real estate solutions. - Settled terms and formulated marketing plans to attract investors and lock deals while achieving desired business objectives. - Raised funds, administered construction, and coached a small team to market options.
-
-
-
Weyerhaeuser
-
United States
-
Paper and Forest Product Manufacturing
-
700 & Above Employee
-
Manufacturing Engineer
-
Jan 2005 - May 2008
- Discovered new methods, monitored quality control procedures, and operated CNC equipment to establish housing sections in a manufacturing environment. - Participated in 3 Kaizen events that strengthened understanding of improving an existing process. - Monitored equipment installations and supported 11 nationwide startups to leverage growth. - Impacted organizational development by lowering material waste from 4.9% to 1.6%, maximizing productivity from 15 to 30 square feet per person-hour, and approving 11-time cards. Show less
-
-
Education
-
Harvard Business School Online
Post graduate, Disruptive Strategy, Negotiation Mastery -
University of Mary Washington
Master of Business Administration (M.B.A.) -
James Madison University
Bachelor's degree, Manufacturing Engineering
Community
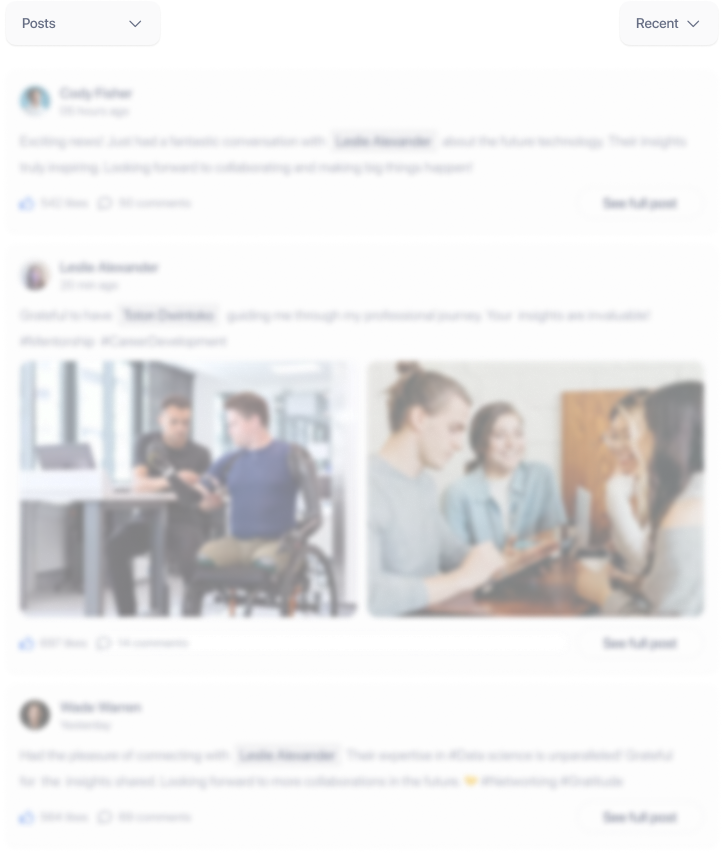