Eric Raschke
Service Manager at The Numina Group- Claim this Profile
Click to upgrade to our gold package
for the full feature experience.
Topline Score
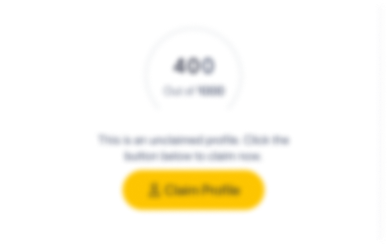
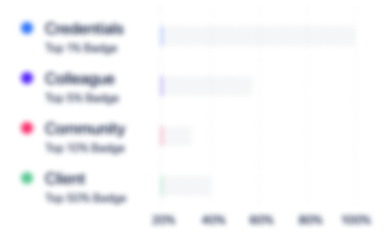
Bio


Experience
-
Numina Group
-
United States
-
Automation Machinery Manufacturing
-
1 - 100 Employee
-
Service Manager
-
May 2013 - Present
Manage assigned projects including coordination of installation of all equipment.Lead support of hardware related equipment issues. Manage assigned projects including coordination of installation of all equipment.Lead support of hardware related equipment issues.
-
-
-
Corelle Brands
-
United States
-
Manufacturing
-
500 - 600 Employee
-
Maintenance Manager
-
Apr 2011 - Apr 2013
Promoted to Maintenance Manager after a year and a half of leading the maintenance department.• Supervised a team of eight collective bargaining employees.• Maintenance department spending down 21% since taking over the maintenance department.• Led maintenance crew through example in troubleshooting technical problems• Responsible for maintenance of 700,200 square foot facility and all equipment contained within• Responsible for controls, modifications and changes to 9,500 feet of conveyor which included a 21 lane sortation conveyor.• PLC programming, modification and troubleshooting of 12 facility PLC’s• Analyzed and Troubleshot any equipment which was too complex for maintenance associates• Implemented and managed preventive maintenance procedures on all facility equipment which was previously non-existent.• Consolidated and organized all equipment documentation to make easily accessible for all maintenance associates• Facilitated talks with contractors to identify the correct contractor for assigned projects• Participated in team to identify and implement best approach for lighting costs to be reduced by over 50%• Maintained all facility changes and modifications in AutoCAD• Provided engineering support of all plant engineering projects• Maintain inventories of radios, fork lifts, fork lift batteries, lockers and facility keys.• Implemented daily meetings with maintenance department to ensure all were on the same page.
-
-
Maintenance Supervisor
-
Jan 2010 - Apr 2011
• Supervised a team of eight collective bargaining employees.• Led maintenance crew through example in troubleshooting technical problems• Responsible for maintenance of 700,200 square foot facility and all equipment contained within• Responsible for controls, modifications and changes to 9,500 feet of conveyor which included a 21 lane sortation conveyor.• PLC programming, modification and troubleshooting of 12 facility PLC’s• Analyzed and Troubleshot any equipment which was too complex for maintenance associates• Implemented and managed preventive maintenance procedures on all facility equipment which was previously non-existent.• Consolidated and organized all equipment documentation to make easily accessible for all maintenance associates• Facilitated talks with contractors to identify the correct contractor for assigned projects• Maintained all facility changes and modifications in AutoCAD• Provided engineering support of all plant engineering projects• Maintain inventories of radios, fork lifts, fork lift batteries, lockers and facility keys.
-
-
Electrical Engineer
-
Jul 2006 - Jan 2010
• Led maintenance crew through example in troubleshooting technical problems• Responsible for controls, modifications and changes to 9,500 feet of conveyor which included a 21 lane sortation conveyor.• PLC programming, modification and troubleshooting of 12 facility PLC’s• Analyzed and Troubleshot any equipment which was too complex for maintenance associates• Implemented and managed preventive maintenance procedures on all facility equipment which was previously non-existent.• Revamped facilities spare parts inventory to consolidate like parts and reduce time searching for spare parts• Maintained all facility changes and modifications in AutoCAD• Provided engineering support of all plant engineering projects• Created documentation for new SOP’s to obtain a more efficient and consistent end result.• Maintain inventories of radios, fork lifts, fork lift batteries, lockers and facility keys.• Rebuilt continuous motion side sealer for sealing packages for use on an assembly line saving $13,000 in the first year alone.• Created program to rotate fork lift batteries through a FIFO to maintain the optimum charge for each battery and limit downtime to equipment
-
-
Education
-
DeVry University
Bachelors, Electronics Engineering Technology
Community
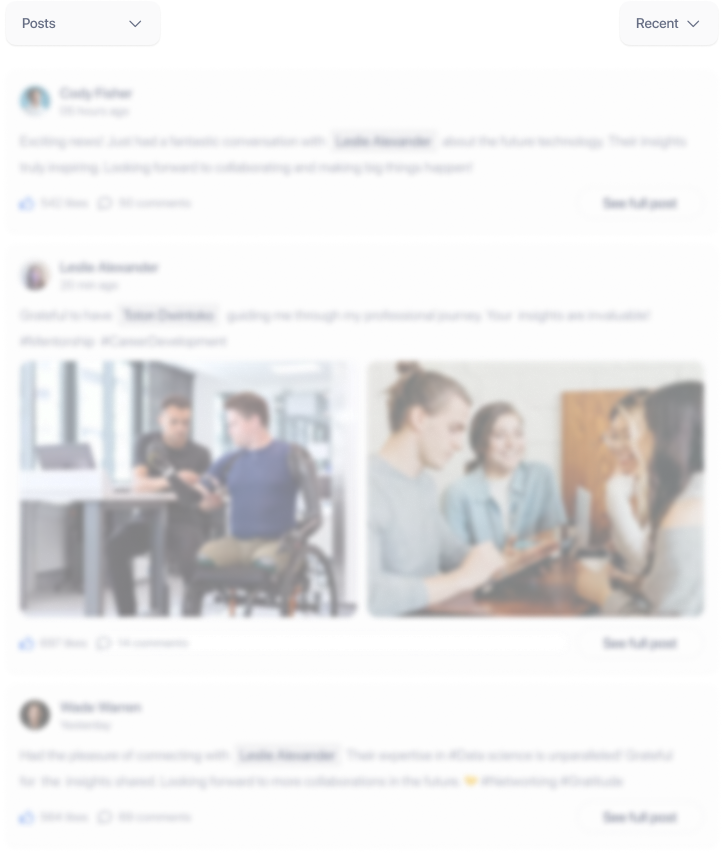