Emily Schnarr
Director of Operations at Hardy Process Solutions, a Roper Technologies company- Claim this Profile
Click to upgrade to our gold package
for the full feature experience.
Topline Score
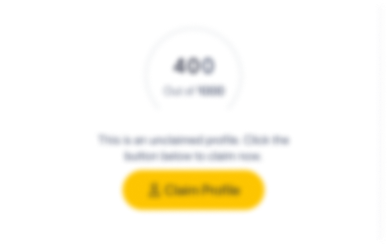
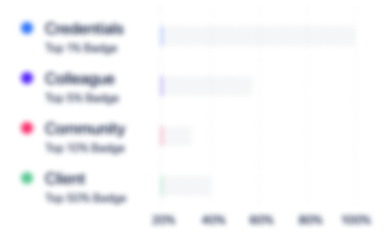
Bio

April Cooper
Emily is an excellent leader who is able to not only set high level strategy but also get into the weeds of a problem when her expertise is necessary to solve an issue. I appreciated the interest and effort she gave to ensuring success of the company and those that worked for her whether directly or indirectly. While her skills and expertise are both deep and broad, it is her interpersonal skills that set her apart and make her an exceptional leader.

Steven Lehr
Emily is an outstanding leader, manager and mentor. Her ability to address complex problems in an intelligent and systematic way is unparalled and consistently produces positive results. Emily is unflappable and calm under pressure. She is process oriented and understands how to implement tactical solutions to achieve overall strategic objectives. Emily creates unique and creative solutions to problems and executes their implementation flawlessly. I would highly recommend Emily for any position requiring an intelligent leader and manager that builds teams and achieves results.

April Cooper
Emily is an excellent leader who is able to not only set high level strategy but also get into the weeds of a problem when her expertise is necessary to solve an issue. I appreciated the interest and effort she gave to ensuring success of the company and those that worked for her whether directly or indirectly. While her skills and expertise are both deep and broad, it is her interpersonal skills that set her apart and make her an exceptional leader.

Steven Lehr
Emily is an outstanding leader, manager and mentor. Her ability to address complex problems in an intelligent and systematic way is unparalled and consistently produces positive results. Emily is unflappable and calm under pressure. She is process oriented and understands how to implement tactical solutions to achieve overall strategic objectives. Emily creates unique and creative solutions to problems and executes their implementation flawlessly. I would highly recommend Emily for any position requiring an intelligent leader and manager that builds teams and achieves results.

April Cooper
Emily is an excellent leader who is able to not only set high level strategy but also get into the weeds of a problem when her expertise is necessary to solve an issue. I appreciated the interest and effort she gave to ensuring success of the company and those that worked for her whether directly or indirectly. While her skills and expertise are both deep and broad, it is her interpersonal skills that set her apart and make her an exceptional leader.

Steven Lehr
Emily is an outstanding leader, manager and mentor. Her ability to address complex problems in an intelligent and systematic way is unparalled and consistently produces positive results. Emily is unflappable and calm under pressure. She is process oriented and understands how to implement tactical solutions to achieve overall strategic objectives. Emily creates unique and creative solutions to problems and executes their implementation flawlessly. I would highly recommend Emily for any position requiring an intelligent leader and manager that builds teams and achieves results.

April Cooper
Emily is an excellent leader who is able to not only set high level strategy but also get into the weeds of a problem when her expertise is necessary to solve an issue. I appreciated the interest and effort she gave to ensuring success of the company and those that worked for her whether directly or indirectly. While her skills and expertise are both deep and broad, it is her interpersonal skills that set her apart and make her an exceptional leader.

Steven Lehr
Emily is an outstanding leader, manager and mentor. Her ability to address complex problems in an intelligent and systematic way is unparalled and consistently produces positive results. Emily is unflappable and calm under pressure. She is process oriented and understands how to implement tactical solutions to achieve overall strategic objectives. Emily creates unique and creative solutions to problems and executes their implementation flawlessly. I would highly recommend Emily for any position requiring an intelligent leader and manager that builds teams and achieves results.

Credentials
-
6Sigma Green Belt
GreenleeJan, 2008- Sep, 2024 -
Certified Supply Chain Professional (CSCP)
APICSMay, 2012- Sep, 2024
Experience
-
-
Director of Operations
-
Jul 2022 - Present
-
-
Supply Chain Manager
-
Oct 2021 - Jul 2022
-
-
-
EM & M Consulting, LLC
-
Public Relations and Communications Services
-
Owner, Primary Consultant
-
2020 - 2022
- Passion project during COVID-19. Developing own firm. - Mission: Guiding and mentoring individuals and businesses to develop strategies to achieve their goals through data analysis, lean thinking, crucial conversations, Genchi Genbutsu, and project management. - Passion project during COVID-19. Developing own firm. - Mission: Guiding and mentoring individuals and businesses to develop strategies to achieve their goals through data analysis, lean thinking, crucial conversations, Genchi Genbutsu, and project management.
-
-
-
Carlisle Interconnect Technologies
-
United States
-
Appliances, Electrical, and Electronics Manufacturing
-
700 & Above Employee
-
Manufacturing Manager
-
Mar 2021 - Oct 2021
-
-
-
TASUS Corporation
-
United States
-
Motor Vehicle Manufacturing
-
100 - 200 Employee
-
Plant Manager
-
Oct 2018 - Feb 2020
Career transition to overseeing larger team of 200 (6 direct management reports) and learning injection molding ($30M annual sales); navigating challenge of insufficient capacity through staffing increase, efficiency improvements, and outsourcing which resulted in 1800 past due hours reducing to less than 50 in three months; rebuilding TPS foundation; creating a culture balanced between rewarding positive behavior and accountability; partnering with critical customer and TASUS team to identify root causes of quality performance decline and developing action plan to address; restoring confidence of customers in the Indiana team’s ability to provide quality product on time. Show less
-
-
-
Greenlee
-
Machinery Manufacturing
-
Plant Manager - Louisville Operations
-
Jun 2015 - Sep 2018
Working with the team in Louisville to exceed customer expectations through on time delivery, quality and productivity. Louisville supplies weldments and painted and cut parts to the other Textron Tools and Test manufacturing facilities, along with Storage Boxes and Material handling products to our customers in the field. Change is constant here which provides an excellent opportunity to live out continuous improvement.
-
-
Director of Customer & Distributor Support
-
Oct 2014 - Jun 2015
Responsible for leading the Customer Service organization and Factory Service Center. Focused on strengthening Greenlee's relationship with both our distributor base as well as our end users. Working to improve the overall efficiency of the customer service team by introducing lean processes.
-
-
Supply Chain Manager
-
Nov 2013 - Oct 2014
Overseeing inventory and forecast management. Supporting standard work and process development for our corporate supply chain processes. Digging deep into data analysis and SAP to ensure we are set up for success. Customer Care. Project Management of On Time Delivery improvements for request and promise date performance, including SAP enhancements. Training and Coaching the ISC Team regarding our Materials and Lean Vision and Culture.
-
-
Plant Manager
-
Oct 2012 - Oct 2013
Plant Manager at Greenlee's Genoa, IL facility
-
-
Plant Manager
-
Feb 2011 - Sep 2012
Plant Manager at Greenlee's Louisville, Kentucky facility.
-
-
Manufacturing Manager
-
Sep 2008 - Feb 2011
Productivity analysis; expense management; EHS Coordinator (Mesa, AZ and Vista, CA); resource management through cross training and flexible workforce; developing cycle count strategy; August 2009 SAP implementation and process controls (ITAR Business); lead transition team relocating a product line
-
-
Materials Manager
-
Dec 2006 - Sep 2008
Inventory analysis and reduction; contract negotiations; developing purchasing ISO procedures; May 2008 SAP Implementation; restructuring supply chain team; partnering with suppliers; cost reductions; implementing SIOP; partnering with engineering on NPI
-
-
Senior Buyer
-
Jul 2006 - Dec 2006
Purchasing, scheduling and disbursement of components for PCB Assemblies; inventory and PPV analysis; reporting purchasing and inventory results to management; communicating with production planning and warehouse to improve supply chain; creating and improving purchasing procedures and reports; supply and demand analysis; coordinating purchasing assignments with buyers
-
-
Buyer
-
Jan 2005 - Jul 2006
Purchasing, scheduling and disbursement of components for PCB Assemblies and parts to support copper model manufacturing; inventory maintenance; RFQ and PO communication with vendors; acquire knowledge of components, parts and assemblies required by Tempo products1/2005 - 9/2005 was through Manpower in a temp-to-hire position at Greenlee (Tempo at the time)
-
-
-
University of Louisville
-
United States
-
Higher Education
-
700 & Above Employee
-
Lecturer
-
Aug 2017 - Dec 2017
Teaching Operations Management course. Developing lectures and assignment content. Providing tutoring and sharing real-world experiences with students. Honored to receive the student nominated Top 5 Faculty Favorites Award. Teaching Operations Management course. Developing lectures and assignment content. Providing tutoring and sharing real-world experiences with students. Honored to receive the student nominated Top 5 Faculty Favorites Award.
-
-
-
Sony Electronics
-
United States
-
Computers and Electronics Manufacturing
-
700 & Above Employee
-
Varied Supply Chain Roles
-
Sep 1999 - Jun 2004
Project Coordinator Buyer/ Material Planner Material Planner (Started in September 1999 as a temp assignment to Sony through Adecco) Project Coordinator Buyer/ Material Planner Material Planner (Started in September 1999 as a temp assignment to Sony through Adecco)
-
-
Education
-
University of Notre Dame
Master’s Degree, Business Analytics -
San Diego State University-California State University
Bachelor of Science (B.S.), Business Administration and Management, General
Community
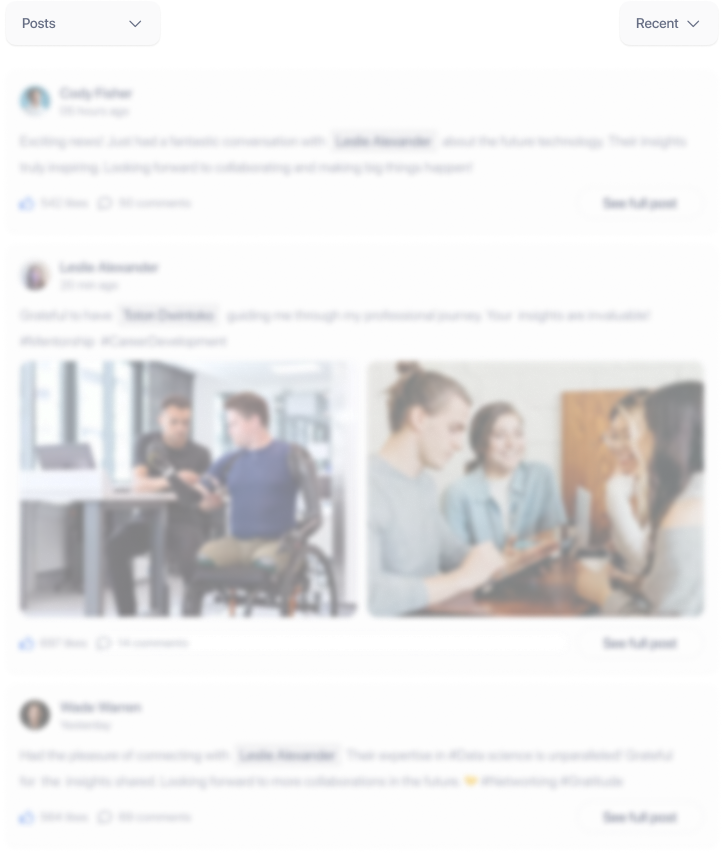