Emily Johnson
Purchasing Buyer at TOYO AUTOMOTIVE PARTS, USA, INC- Claim this Profile
Click to upgrade to our gold package
for the full feature experience.
Topline Score
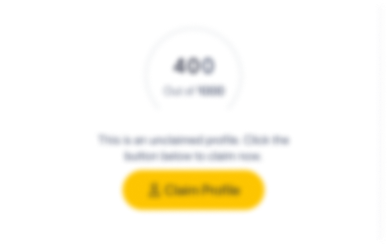
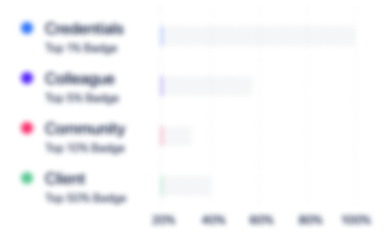
Bio


Experience
-
TOYO AUTOMOTIVE PARTS, USA, INC
-
United States
-
Truck Transportation
-
1 - 100 Employee
-
Purchasing Buyer
-
2019 - Present
Purchases all supplies, materials, and parts for the company.Oversee materials coming into the plant (including Toyota, Nissan, & service operations)Works to schedule delivery of materials, supplies, and equipment.Maintains inventory levels to ensure deliveries occur within customer timelines.Ensure all start-up projects and build out projects are properly communicated and planned to all appropriate management and production staff.Manages all transportation costs and charges.Manages and monitors storage of purchsaed parts and finished goods.Negotiates and completes contracts with vendors for optimal cost and delivery times.Manages Suppliers and Customers regarding items such as delivery performance, forecasts, and pricing.Generate all production raw materials orders for both domestic and import stock.Collaborates with other departments and leadership to identify and develop needs and requirements for equipment, materials, products, and acceptable substitutions.Collaborates with sales, customer service, and logistics departments to maximize efficiency.Communicates with suppliers to resolve problems that may arise regarding delivery, quality, price, or conditions of sale.Maintains knowledge of trends, prices, buyers, and delivery conditions to anticipate future material availability.Report all NAFTA documentation to customersMonitor and strive to achieve customer targets relative to minority and women owned businesses.Risk management for suppliers (develop systems and methods to manage all types of risks)Visit suppliers as necessary for negotiation of supply program.Responsible for issuing PO’s for all raw materials,MRO and indirect supplies to all suppliersReview any discrepant Invoices related to any suppler purchases.Evaluate vendor quotes and services to determine most desirable supplier and prepare RFQ packages for suppliers, organize quote comparisons.
-
-
-
Boyd
-
United States
-
Appliances, Electrical, and Electronics Manufacturing
-
700 & Above Employee
-
Purchasing Buyer
-
Jul 2018 - May 2019
Oversaw the purchasing of supplier components, materials and packaging for production to include forecasting and planning based on customer purchase orders.Created and released purchase orders for direct, indirect materials, and maintenance item to maintain inventory and ensure on-time delivery to customers.Coordinated with purchasing, production, engineering, quality and sales to achieve customer required delivery dates.Handled the inventory conversion, setup items, vendor information and inventory location into Job Shop/Navision purchasing software.Assessed the impact of engineering change orders and executes changes as required such as tooling and print plates.Assisted with special projects (i.e. new product/customer ramp-up plans).Negotiated and implemented cost savings initiatives with MRO suppliers (current savings 6K ytd)Booked transportation for shipping of all incoming out coming orders through 3rd party logistics company, corresponded with suppliers and emailing appropriate documents inside/outside personal.Responsible for ensuring all receiving paperwork is accurate and enter Job Shop/Navision purchasing software.Reviewed and managed monthly inventory for the facility.
-
-
-
U.S. Tsubaki Automotive
-
United States
-
Manufacturing
-
1 - 100 Employee
-
Purchasing Buyer
-
Oct 2017 - Jun 2018
Managed supplier releases within QAD system working with vendors to ensure on time delivery and performance.Controlled the inventory in accordance with management objectives, setting safety stock and reviewing QAD for proper settings of all parameters to ensure delivery.Reported any shortages, missed deliveries, etc. related to the production environment to the Materials Managed for assisted action through use of the Critical Shortage Report.Worked with Logistics on shortages, etc. to ensure customer needs are met to the OEM customers.Works closely with related departments to communicate any part shortages and recovery plans.Entered and maintained data into Excel to manage any circumstance related to a supplier issues for tracking and plan/action records.Entered requisitions into EAM and sends PO’s to the vendors after approval (Indirect materials, MRO, Tool Room, Office Supplies, Etc.).Followed up on Requisitions to be sure they are approved timely and PO’s were issued and sent on time.Worked closely with Accounting to ensure approval or surcharges are managed of prior to entry into the systems for payment/reconciliation and created Debit Memos to suppliers related to quality and delivery issues.Maintained supplier relationships and assisted in sourcing new MRO suppliers.Monitored supplier performance and took appropriate action when necessary; Participates in Supplier Ratings through the Report Card Systems Meetings.Assisted the Materials Manager in reporting all monthly metrics related to the supply chain in Portland Facility (QOS, Local meetings).Assisted the Materials Manager with projects, cost savings activities and other related activities as neededPreformed related tasks to the Materials functions as directed by the Materials Manager or the Production Planning & Procurement Supervisor.
-
-
-
-
Production Control Coorindator
-
Jun 2013 - Oct 2017
Planed, coordinated and managed all areas related to production control: Including all production schedules, JIT implementation, inventory, and continuous improvement. Directed production control activities and effectively communicate to production team memberReviewed inventory including organizing and managing cycle count program at TN facility Partner with materials, manufacturing and purchasing departments to identify and resolve all issues/concerns related to production Managed production planning and scheduling for on-time delivery Recommended process improvements for high quality, cost effectiveness and excellent customer services.Lead/Coordinated JIT implementation actionsBack up coverage for production supervisors as requiredActive team member of cross functional teams by providing direction and ideas
-
-
-
Old Navy
-
United States
-
Retail
-
700 & Above Employee
-
Retail Operations Manager
-
Jan 2012 - May 2013
Responsible for the driving results in planning and preparing an extraordinary customer and associate experience, while meeting and exceeding company productive standards and delivering on controllable contribution. Managed, train, coach, supervise and direct staff to ensure consistent application the company defined best practices and standards to maximize sales, profitability and the customer experience.Managed activities related to improve profitability within the store, including process and productivity stands and improvement, expense controls and maximizing gross margin.Managed execution through effective planning, prioritizing, communication and follow-upImplement company standards and best practices, monitors improvement and areas of opportunityDrove results and enforcing company guidelines and policies Performed Leader on Duty responsibilities open/close storeMonitored payroll/schedule and adjust to business needsOwner of Loss Prevention, Risk Management and Safety within the store facilityPerformed monthly Store Compliance and Shrink Audits Handled all maintenance issues and coordinate with Facility Services Managed supply expense
-
-
-
Gap
-
United States
-
Retail
-
700 & Above Employee
-
Operations Supervisor
-
May 2009 - Jan 2012
Gap Inc. Distribution CenterResponsible for the direct supervision of multiple associates regarding daily activities in the inbound, outbound, manual picking, sorting, and shipping department in different facilities to ensure that production volumes are achieved and shipped to the Old Navy and Banana Republic Brands. Manage and give direction to team members by coaching & developing associates on efficient work methods and ways to continually improve the department.Supported and effectively communicate policy and procedures as outlined in the Gap Inc. HR Handbook and The Safety Ability GuidelinesCompleted safety incident and accident investigation forms and associate follow up to solve for root cause analysis and possible safety improvementsReduced associate ER related issues within the departmentsManaged HR issues within the department including, PTO, Kronos, absenteeism, corrective action and conflict resolutionMonitored staffing levels to reduce indirect timeMet budget and ship complete requirementsWorked with maintenance on safety and operational concerns
-
-
Executive Administrative Assistant
-
Feb 2007 - Apr 2009
Provided executive administrative support to the Facility Director, Operations Managers, and Supervisors. Act as liaison between Director and Managers for gathering data for analysis, reporting and distribution in addition to a wide-range of administrative functions.Coordinated Daily Old Navy Ship Complete report for division, compose summation, and distributed to corporate VP'sInterfaced with Campus Support Managers on various reports and projectsOwned and managed the start of shift communication template to produce an effective weekly communication tool for all SDC departments achieving positive feedback on improving communication from SDC associatesSuggested idea to update current FISH logo by having a campus contest partnered with Safety manager and Steering team and responsible for successful logo updateAdministered and managed SDC recognition program: reducing cost by eliminating nominee t-shirts, creating user friendly nominees forms and establishing an innovative method for managers to vote each monthDelivered Director Visibility to indirect employee time by partnering with Support Management to create new report. This report was shared as a best practice with other Facility Directors across the campusGenerated a supply ordering cost savings of over $4K annually by consolidating warehouse supply vendors
-
-
-
-
Manufacturing Supervisor
-
Jun 2003 - Dec 2006
Responsible for scheduling and coordinating production and maintenance activities and the allocation of resources to achieve short and long term plant production and quality goals and objectives. Supervised 35-40 employees in a high-volume, fast-paced automotive manufacturing environment while maintaining associate morale, meeting production rates/standards and achieving customer quality requirements under adverse conditions.Reduced monthly overtime by 5% and increased units per man hour from 15.5 to 18.6 by restructuring assigned resources and eliminating unnecessary overtime.Planned production capacities and coordinated line changeovers in order to meet monthly and yearly master production schedules.Directed activities of maintenance associates in order to achieve efficient changeovers, PMS, tool changes, and incorporated requested maintenance projects into schedules.Performed internal Quality Systems Audits & ISO: 14001 within Gallatin Plant and other Bosch locationsInterfaced with quality, manufacturing, management, and plant personnel to ensure production and quality requirements were met on time.Maintained aggressive, high-volume production schedule by ensuring that material and processes were efficient and bottlenecks eliminated.
-
-
Administrative Coordinator, Maintenance, Operations & Engineering
-
Oct 1995 - May 2003
Provided administrative support for 28 people throughout Maintenance, Operations and Engineering to include maintaining calendars, arranging travel, training, coordinating/facilitating meetings and preparing reports & presentations.Created databases/spread sheets and associated training for inter and intra departmental dataExperienced in interpreting/entering technical data into MPACT softwareImplemented tooling work order system in SAP; Evaluated effectiveness on a monthly basis, resulting in an annual savings of $50KDeveloped training materials for various new program/process implementationsTrained as a Continuous Improvement Process Coordinator, facilitating several workshops including EIW, PIW, QI for administrative and manufacturing processesQuality and Safety document control champion: maintain master lists all departments: operations, engineering, maintenance and safetySelected for role of Auditor for Internal/External Quality Systems Audits, Internal ISO 14001, 5s office/manufacturing environment in addition to current role responsibilities.
-
-
Education
-
Trevecca Nazarene University
Bachelor's degree, Human Relations Business Management
Community
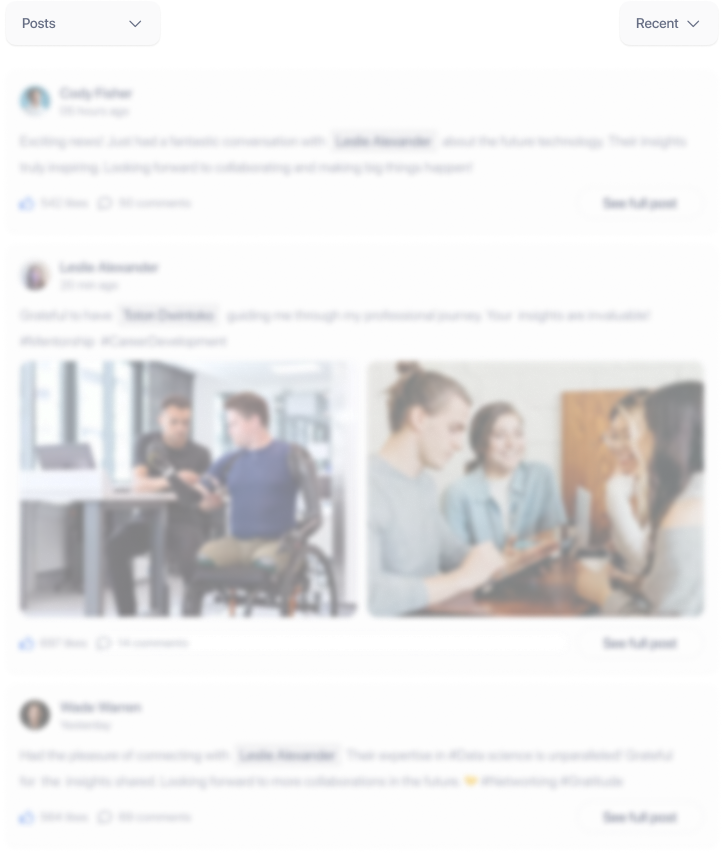