Emily Assuncao
Director - Eglinton LRT at Metrolinx- Claim this Profile
Click to upgrade to our gold package
for the full feature experience.
-
English Native or bilingual proficiency
-
Greek Limited working proficiency
-
Portuguese Elementary proficiency
Topline Score
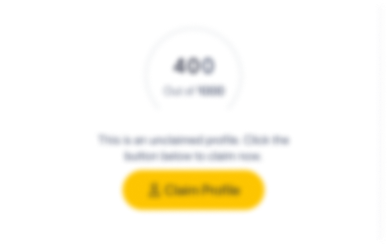
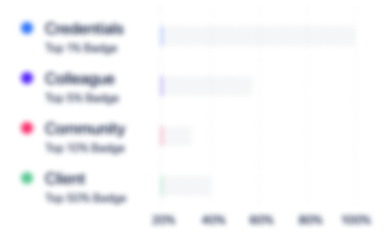
Bio


Credentials
-
Project Management Professional
Project Management InstituteJul, 2017- Nov, 2024 -
P. Eng.
Professional Engineers OntarioSep, 2000- Nov, 2024
Experience
-
Metrolinx
-
Canada
-
Ground Passenger Transportation
-
700 & Above Employee
-
Director - Eglinton LRT
-
Jul 2019 - Present
• Delivers project through construction and commissioning and transfer to asset owners and Operations within scope, on budget, and schedule, following good project management and construction practices; ensuring compliance with Metrolinx design standards and applicable municipal, provincial and federal codes• Manages complex project issues and risks, facilitates effective conflict resolution, and communicates with internal and external stakeholders and manages their expectations• Plans directs and monitors all aspects of the assigned LRT line, including project financial accountability, contract and schedule management, contractor adherence to reference designs and performance specifications, and support for program communications and intergovernmental relations during all stages of the project.• Delivers and provides leadership in the delivery of corporate policy regards to Safety, Quality, People and Cost• Ensures that construction activities are managed in a manner that minimizes stakeholder impacts.• Creates and manages the strategic direction for the area of responsibility, develops, presents and negotiates specifics of business cases to operationalize strategic initiatives.• Liaison and communications with external providers/partners to ensure alignment develops and maintains a strong network with authorities, government agencies, consultants and contractors to coordinate projects, set priorities, and deadlines, share best practices and lessons learned. • Providing technical and commercial leadership for all aspects of transit-rail systems elements including system requirements analysis, system and subsystem design, interface management, safety analysis, installation, systems integration, testing and commissioning, vehicle-rail interface, traction power, OCS, signaling/train control, communications, SCADA, power, fare collection, and other related disciplines.
-
-
-
FIRST
-
United States
-
Non-profit Organization Management
-
700 & Above Employee
-
Coach
-
Jan 2014 - Present
Coach FIrst Lego League Teams via TDSB
-
-
-
Toronto Transit Commission (TTC)
-
Urban Transit Services
-
700 & Above Employee
-
Manager - Bus Transportation
-
May 2018 - Jul 2019
• Accountable for the day-to-day operation and administration of the assigned bus transportation division• Ensuring transit services are delivered in a safe and cost effective manner in accordance with the TTC’s goals and objectives• Managing the activities of a large group of personnel and trouble-shooting problematic situations• Ensuring the TTC Way – respect one another; value each other’s time; tell people what’s happening; stay safe; mind your space and help others out, is maintained throughout the workplace, extended customers, communities and partners• Ensuring optimum performance of operating personnel, including attendance management, safe operating, customer service etc.• Interviewing and counselling employees, initiating corrective measures, submitting reports and following up to ensure compliance• Leading change and promoting a culture of accountability and customer service• Ensuring the critical paths of the TTC’s corporate plan, “advancing to the next level” are incorporated into the goals and objectives of the daily operation of running a division• Promoting safety consciousness and safe operating procedures• Reviewing the Divisional budget and providing justification for recommended changes• Maintaining good relations with Union representatives, support staff, municipal officials and the travelling public• Maintaining divisional files and records on accidents, discipline, performance and attendance• Treating passengers and employees with respect and dignity and ensuring the needs of those with disabilities are accommodated and/or addressed in accordance with the Ontario Human Rights Code and Related Orders so that they can fully benefit from the TTC as a service-provider and employer
-
-
Manager - Closures and Diversions
-
May 2015 - May 2018
• Planning and coordinating transit services associated with the occurrence of special events such as parades, street festivals, film shoots, and construction, etc. to ensure that the best interests of TTC customers are upheld• Assessing the potential impact of special events on regular TTC Transit services (i.e. investigating and troubleshooting problem situations, and recommending solutions to problems)• Developing detailed transit disruption and special event plans, including staffing and coordinating alternate TTC routes and schedules including provisions for additional buses, supervisory personnel, etc.• Liaising with appropriate Divisional staff, Transit Control and maintenance departments to ensure that all transit services associated with closures and disruptions are operated efficiently and safely, and that regular TTC services are restored as soon as possible• Communicating closure and disruption information to TTC and external stakeholders including Business Improvement Associations, neighbourhood groups, City Councillors Coordinating special surface transit services required as a result of subway-related incidents e.g. temporary closure of subway stations • Attending regular meetings with Toronto Police, City of Toronto, and various event organizers to advocate for the customer and ensure minimal disruption possible by major events• Coordinating contract customer service workers for use during service disruptions and special events, including all facets of contract administration for 3 contractors• Planning and preparing itineraries and routings for all event/service related bus charters including arrangements for vehicles and route maps• Providing consultation, direction, advice and guidance regarding major, escalated construction site management issues/construction problems/issues affecting TTC modes of transportation• Managing Customer Service Contracts providing staff for all closures and diversions
-
-
Assistant Manager - Planning
-
Apr 2012 - May 2015
• Organizing, implementing and documenting subway closures and special event plans for subway operations• Scheduling meetings with stakeholders including TTC Departments and external agencies to determine what assets are required to effectively support future subway closures and special events• Organizing work between various TTC departments to ensure customer expectations are met• Initiating training for personnel working subway closures and special events• Actively participating in the development of subway closure schedules• Providing administrative oversight for external event contractors• Investigating and troubleshooting problem situations • Acting as a Transportation Lead for special events and subway closures as required• Working with the Training Department to ensure the provision of appropriate training/certification for Transit Control personnel.• Assisting in the selection and training of personnel• Coordinating, scheduling and documenting staff training • Reviewing and updating all training correspondence, manuals, and progress reports• Develops program goals, objectives, strategies and measures
-
-
Acting Manager - Analysis & Procedures
-
Jun 2012 - Sep 2013
conducting and/or directing various analyses and cost/benefit studies of Subway Transp. operations, including interpreting results of studies as well as developing and recommending alternatives to correct deficiencies and improve operational efficiency;developing, documenting, recommending, implementing, monitoring and evaluating new and/or revised operating and administrative rules, standards and procedures for the department; ensuring that such rules and procedures do not negatively impact on the safety of customers and employees;preparing and monitoring performance measures for various aspects of the business to ensure safety, efficiency and quality of services provided;acting as a departmental resource and providing advice, direction and interpretation regarding rules, procedures, standards and performance measures;assisting the Head in the overall management of departmental operations and the handling of key issues such as performance measures and quality assurance;assisting in the implementation of Commission/Department policies;assisting in the development, consolidation and administration of departmental business plans and budgets;assisting with the development and implementation of cost control programs and other initiatives related to the operation and the administration of the various Sections of the Department, including Station Operations/Collectors, the Transit Control Centre and the various Subway Transportation Divisions;monitoring departmental compliance to pertinent government legislation/regulations and recommending means to improve compliance;developing and recommending various programs to improve departmental communications, joint problem solving and customer relationsliaising with internal/external contacts regarding areas of responsibilityresearching information and preparing/presenting various reports and recommendations related to the workkeeping abreast of industry trends, best practices and new technology
-
-
Acting Project Manager - Plant Maintenance
-
Jun 2011 - Mar 2012
- Project management system for facility repair projects and new construction projects.- Work Order Request process - Communication with customers on the Work Order Request process- Prioritization by Safety Department of Safety Related Work Order Requests that require design by E&C- Condition assessments- Short and long term planning for repair / replacement- Cost estimating- Job plan development- Resource planning- Construction and service contract management- Lease construction / maintenance management- Developer construction / maintenance management- Project scheduling for Plant maintenance trades, Electrical Trades and Sheet Metal Trades- Warranty management- Maintenance manual management - Operating budget impacts of Capital Budget Projects
-
-
Supervisor - Operations Support
-
Sep 2010 - Mar 2012
Responsible for system management procedures and techniques applicable to safety, quality assurance, environmental compliance, emergency procedures, computerized information services, budget development and standard operating procedure.Coordinate construction activities, corrective maintenance activities and preventative maintenance activities.Knowledge of applicable codes and regulations such as the Occupational Health & Safety Act, Ministry of the Environment Regulations, Employment Standards Act etc. Creating a computerized maintenance management systems word processing, database, spreadsheets, power point presentations and report generation is essential. plan and direct the activities of subordinate employees. Possess sound judgement, highly developed organizational, analytical, problem solving and interpersonal skills. Comprehensive knowledge of the Ontario Human Rights Code and Related Orders including disability accommodation and accessibility requirements pertaining to passengers and employees
-
-
-
Magna International
-
Canada
-
Motor Vehicle Manufacturing
-
700 & Above Employee
-
Program Manager
-
Nov 2008 - Sep 2010
Conduct weekly design review meetings with the customer and in house designersCoordinate with project team to develop “project launch cycle”, monitor progress and develop Corrective actions when requiredCoordinate with the Purchasing Department to ensure on time and on budget material procurementReview strategic Value Engineering opportunities with customer(s) for mutually beneficial cost savingsReview technical drawing and specifications from customers and draft quotations and capacity plans for all new business opportunities presented to Rollstamp
-
-
-
Magna International
-
Canada
-
Motor Vehicle Manufacturing
-
700 & Above Employee
-
Special Projects Manager
-
Dec 2005 - Nov 2007
Saved Rollstamp over $250,000 annually on supplier transportation costs by implementing milk runs for specific suppliers and coordinating all deliveries in order to prevent major disruptions to the flow of productionManaged the implantation of a fully integrated real-time paperless shop floor system Blackhawk Systems within our plant to improve our supply chain process to the customerAutomated Debit Memos by launching a new software package to be used plant wide
-
-
-
Magna International
-
Canada
-
Motor Vehicle Manufacturing
-
700 & Above Employee
-
Materials Manager
-
May 2003 - Nov 2004
Developed, designed and implemented functional policies and programs that make major changes in overall business performance based on long-term needs.Contributed to the continuous improvement of department through analysis and the development and implementation of sound management practices and procedures.Provided program management staff with direction and guidance, processes and tools to increase efficiencies and improve effectiveness of the departmentWorked with Honda Engineering to become the first North American Supplier to paint metal Lead and motivated a diverse workforce, ensuring effective teamwork, provided resolution to controversial labor relations issues, ensured high standards of work quality and organizational performanceDeveloped, recommended and administered the annual budget for the department, and ensured that expenditures were controlled and maintained within approved budget limitations Enhanced and promoted the department’s vision by providing strong leadership, setting strategic direction, goals and priorities and by taking a proactive approach to problem solving Provided leadership, direction and support to program managers who are accountable for the day-to-day operation of the DivisionEnsured that all projects were planned, coordinated and executed in conformance with project management and corporate standards Demonstrated commitment to the organization’s values and principles and forged effective partnerships with various stakeholders
-
-
Six Sigma Engineer
-
Jun 2002 - May 2003
Utilized problem solving techniques during my Six Sigma training to reduce paint rejects on a specific program, which resulted in an annual savings of $200,000 Saved Rollstamp over $250,000 annually on supplier transportation costs by implementing milk runs for specific suppliers and coordinating all deliveries in order to prevent major disruptions to the flow of productionManaged the implantation of a fully integrated real-time paperless shop floor system Blackhawk Systems within our plant to improve our supply chain process to the customerAutomated Debit Memos by launching a new software package to be used plant wide
-
-
Paint Manager
-
May 2000 - May 2002
Developed, designed and implemented functional policies and programs that make major changes in overall business performance based on long-term needs.Contributed to the continuous improvement of department through analysis and the development and implementation of sound management practices and procedures.Provided program management staff with direction and guidance, processes and tools to increase efficiencies and improve effectiveness of the departmentLead and motivated a diverse workforce, ensuring effective teamwork, provided resolution to controversial labor relations issues, ensured high standards of work quality and organizational performanceDeveloped, recommended and administered the annual budget for the department, and ensured that expenditures were controlled and maintained within approved budget limitations Enhanced and promoted the department’s vision by providing strong leadership, setting strategic direction, goals and priorities and by taking a proactive approach to problem solving Provided leadership, direction and support to program managers who are accountable for the day-to-day operation of the DivisionEnsured that all projects were planned, coordinated and executed in conformance with project management and corporate standards Demonstrated commitment to the organization’s values and principles and forged effective partnerships with various stakeholders
-
-
Process Systems Manager
-
May 1998 - Apr 2000
Coordinated the launch of over 15 major programs in six months in order to fill up production on the plastic paint line and communicated any issues with upper management on a weekly basis Established process parameters for all paint spray equipment in the plant by the design and execution of experiments and created a procedure for documenting all parametersLed a cross-functional team to draft a Process Failure Mode and Effect Analysis on the paint line process and developed a control plan in order to improve the quality of parts and increase productivity within the paint lineEstablished a preventative maintenance and calibration schedule of all paint equipment within the paint line in order to prevent major disruptions to the flow of production resulting from equipment mal-functions Ensured that all Control Plans, Testing Instructions, Production Part Approval Part testing for Paint Durability are being done as per customer specifications and in accordance to Business Operating Systems ManualMonitored production of product through both physical review of work in process and through review of labor and costing report data. Aided in development of corrective actions where neededUtilized lean tools such as Total Productive Maintenance, 5S, Standard Work, Quick Changeover, etc. and articulated these needs to people who lacked the training to recognize the need
-
-
Project Engineer/Cost Estimator
-
Jul 1996 - May 1998
Coordinated the launch of over 15 major programs in six months in order to fill up production on the plastic paint line and communicated any issues with upper management on a weekly basis Established process parameters for all paint spray equipment in the plant by the design and execution of experiments and created a procedure for documenting all parametersLed a cross-functional team to draft a Process Failure Mode and Effect Analysis on the paint line process and developed a control plan in order to improve the quality of parts and increase productivity within the paint lineEstablished a preventative maintenance and calibration schedule of all paint equipment within the paint line in order to prevent major disruptions to the flow of production resulting from equipment mal-functions Ensured that all Control Plans, Testing Instructions, Production Part Approval Part testing for Paint Durability are being done as per customer specifications and in accordance to Business Operating Systems ManualMonitored production of product through both physical review of work in process and through review of labor and costing report data. Aided in development of corrective actions where neededUtilized lean tools such as Total Productive Maintenance, 5S, Standard Work, Quick Changeover, etc. and articulated these needs to people who lacked the training to recognize the nee
-
-
-
-
Project Engineer
-
Feb 1996 - Jun 1996
Ensured that all Control Plans, Testing Instructions, Production Part Approval Part testing for Paint Durability are being done as per customer specifications and in accordance to Business Operating Systems ManualMonitored production of product through both physical review of work in process and through review of labor and costing report data. Aided in development of corrective actions where neededUtilized lean tools such as Total Productive Maintenance, 5S, Standard Work, Quick Changeover, etc. and articulated these needs to people who lacked the training to recognize the need
-
-
-
-
Paint Circulation System Supervisor
-
Jun 1995 - Feb 1996
Responsible for the successful completion of Flushing out and debugging of the Paint Circulation System that was installed by Environmetric Process Controls IncSupervised and trained unionized Environmetric’s Process Controls contractors and unionize Ford employees to flush out and run each Paint Circulating SystemAttended daily production meetings with other Ford Contractors and ensured the successful launch of theNew Paint Circulation System at Ford Motor CompanyCoordinated with other subcontractors to ensure adherence to the overall launch time lineOversaw all activities within the Paint Mix Room during the launch of the new Ford Oakville Assembly Plant Paint Line
-
-
Education
-
University of Toronto
App. Sc, Mechanical Engineering
Community
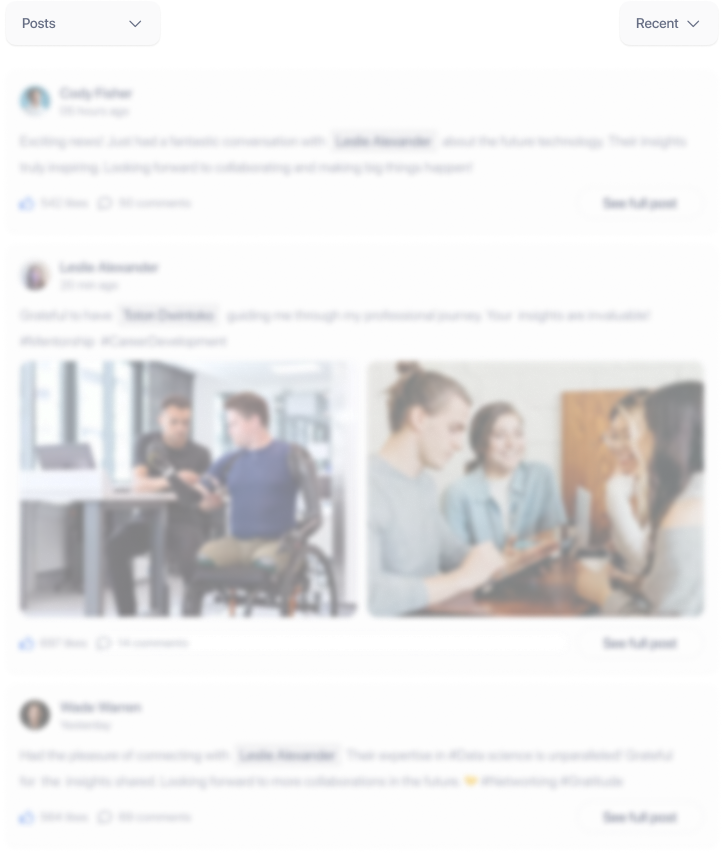