Elzbieta Czupik
Operations Director at °CRYO Science- Claim this Profile
Click to upgrade to our gold package
for the full feature experience.
-
English Full professional proficiency
-
German Professional working proficiency
Topline Score
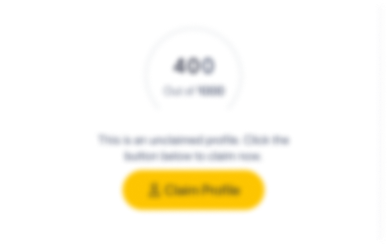
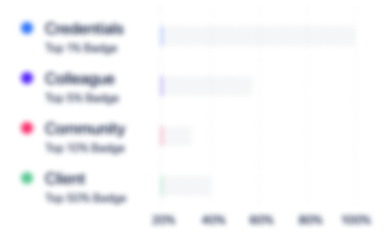
Bio

Tyron Williams
I have had the pleasure of working with and learning from Ela during her time with Rockwool. Her passion and ability to cut through the 'noise' and help you see the problem in a positive way is a gift. She is skilled in both Lean and TOC which gives her a very high skill set for strategy development and her personality allows her to deal with all areas of a business. I would strongly recommend Ela to make a great difference to any organisation that is looking to change and improve.

Niels Olesen
From 2014 to 2016 I was the manager for Elzbieta. Elzbieta was part of the central Rockwool LEAN team and her responsibility was to implement the Lean and Leadership culture together with local lean coaches and Management in the Central Eastern area of Europe covering 4 large factories; 2 in Poland, 1 in the Czech republic and 1 in Hungary. Another part of her job was to develop the Lean strategy, roadmap and training materials together with the central team and adjust it to the culture in the Eastern European factories. In the Lean implementation Elzbieta developed the strategy for the 4 factories and run workshops in strategy deployment together with top management teams, made end to end value stream maps of the factories, thus finding great potential for improvements and set up a performance management structure with KPI´s and daily board meetings at all levels in the factory. Elzbieta trained employees and managers on all levels in Lean tools as 5S, Standard Work, SMED etc. Improvements were implemented using Blitz Kaizen events according a methodology developed in cooperation with Simpler. Elzbieta also trained all the managers in Std. Leader Work, GEMBA walking and more traditional leadership skills like Situational management, Change Management, Coaching and Conflict solving. As a person Elzbieta was highly respected for her skills and great ways to interact and communicate with all employees from the Managing Director to the Operator on the shop floor. I hereby give Elzbieta my highest recommendation. If you have further questions you are welcome to contact me. Niels Olesen

Tyron Williams
I have had the pleasure of working with and learning from Ela during her time with Rockwool. Her passion and ability to cut through the 'noise' and help you see the problem in a positive way is a gift. She is skilled in both Lean and TOC which gives her a very high skill set for strategy development and her personality allows her to deal with all areas of a business. I would strongly recommend Ela to make a great difference to any organisation that is looking to change and improve.

Niels Olesen
From 2014 to 2016 I was the manager for Elzbieta. Elzbieta was part of the central Rockwool LEAN team and her responsibility was to implement the Lean and Leadership culture together with local lean coaches and Management in the Central Eastern area of Europe covering 4 large factories; 2 in Poland, 1 in the Czech republic and 1 in Hungary. Another part of her job was to develop the Lean strategy, roadmap and training materials together with the central team and adjust it to the culture in the Eastern European factories. In the Lean implementation Elzbieta developed the strategy for the 4 factories and run workshops in strategy deployment together with top management teams, made end to end value stream maps of the factories, thus finding great potential for improvements and set up a performance management structure with KPI´s and daily board meetings at all levels in the factory. Elzbieta trained employees and managers on all levels in Lean tools as 5S, Standard Work, SMED etc. Improvements were implemented using Blitz Kaizen events according a methodology developed in cooperation with Simpler. Elzbieta also trained all the managers in Std. Leader Work, GEMBA walking and more traditional leadership skills like Situational management, Change Management, Coaching and Conflict solving. As a person Elzbieta was highly respected for her skills and great ways to interact and communicate with all employees from the Managing Director to the Operator on the shop floor. I hereby give Elzbieta my highest recommendation. If you have further questions you are welcome to contact me. Niels Olesen

Tyron Williams
I have had the pleasure of working with and learning from Ela during her time with Rockwool. Her passion and ability to cut through the 'noise' and help you see the problem in a positive way is a gift. She is skilled in both Lean and TOC which gives her a very high skill set for strategy development and her personality allows her to deal with all areas of a business. I would strongly recommend Ela to make a great difference to any organisation that is looking to change and improve.

Niels Olesen
From 2014 to 2016 I was the manager for Elzbieta. Elzbieta was part of the central Rockwool LEAN team and her responsibility was to implement the Lean and Leadership culture together with local lean coaches and Management in the Central Eastern area of Europe covering 4 large factories; 2 in Poland, 1 in the Czech republic and 1 in Hungary. Another part of her job was to develop the Lean strategy, roadmap and training materials together with the central team and adjust it to the culture in the Eastern European factories. In the Lean implementation Elzbieta developed the strategy for the 4 factories and run workshops in strategy deployment together with top management teams, made end to end value stream maps of the factories, thus finding great potential for improvements and set up a performance management structure with KPI´s and daily board meetings at all levels in the factory. Elzbieta trained employees and managers on all levels in Lean tools as 5S, Standard Work, SMED etc. Improvements were implemented using Blitz Kaizen events according a methodology developed in cooperation with Simpler. Elzbieta also trained all the managers in Std. Leader Work, GEMBA walking and more traditional leadership skills like Situational management, Change Management, Coaching and Conflict solving. As a person Elzbieta was highly respected for her skills and great ways to interact and communicate with all employees from the Managing Director to the Operator on the shop floor. I hereby give Elzbieta my highest recommendation. If you have further questions you are welcome to contact me. Niels Olesen

Tyron Williams
I have had the pleasure of working with and learning from Ela during her time with Rockwool. Her passion and ability to cut through the 'noise' and help you see the problem in a positive way is a gift. She is skilled in both Lean and TOC which gives her a very high skill set for strategy development and her personality allows her to deal with all areas of a business. I would strongly recommend Ela to make a great difference to any organisation that is looking to change and improve.

Niels Olesen
From 2014 to 2016 I was the manager for Elzbieta. Elzbieta was part of the central Rockwool LEAN team and her responsibility was to implement the Lean and Leadership culture together with local lean coaches and Management in the Central Eastern area of Europe covering 4 large factories; 2 in Poland, 1 in the Czech republic and 1 in Hungary. Another part of her job was to develop the Lean strategy, roadmap and training materials together with the central team and adjust it to the culture in the Eastern European factories. In the Lean implementation Elzbieta developed the strategy for the 4 factories and run workshops in strategy deployment together with top management teams, made end to end value stream maps of the factories, thus finding great potential for improvements and set up a performance management structure with KPI´s and daily board meetings at all levels in the factory. Elzbieta trained employees and managers on all levels in Lean tools as 5S, Standard Work, SMED etc. Improvements were implemented using Blitz Kaizen events according a methodology developed in cooperation with Simpler. Elzbieta also trained all the managers in Std. Leader Work, GEMBA walking and more traditional leadership skills like Situational management, Change Management, Coaching and Conflict solving. As a person Elzbieta was highly respected for her skills and great ways to interact and communicate with all employees from the Managing Director to the Operator on the shop floor. I hereby give Elzbieta my highest recommendation. If you have further questions you are welcome to contact me. Niels Olesen
0
/5.0 / Based on 0 ratingsFilter reviews by:
Experience
-
°CRYO Science
-
Poland
-
Machinery Manufacturing
-
1 - 100 Employee
-
Operations Director
-
Jul 2021 - Present
-
-
-
Phillips Europe
-
Poland
-
Transportation/Trucking/Railroad
-
1 - 100 Employee
-
Managing Director
-
Dec 2019 - Feb 2021
• Driving company’s objectives (Sales, Gross Margin, Operating Expenses, Net Income, EBITA) and reporting regularly to all the owners and management board. • Managing diverse team (Sales & Marketing, R&D, Purchasing, Production, Quality, Warehouse, Maintenance, HR, IT, H&S). • Preparing comprehensive business plans, budgets, and investment plans. • Researching and implementing new initiatives to drive revenue, lower operating costs while using Operational Excellence tools. • Continuous monitoring of the annual budget and ensure that revenue/sales targets are met. • Maintaining the quality of products, services, customer support, and level of service in line with service level agreements. • Promoting the wellness of staff. Implementing policies in line with health and safety guidelines to create a diverse and safe working environment. Show less
-
-
-
-
Rockwool Operational Excellence / Lean Coach International A/S
-
2014 - 2019
• ROPEX program implementation (Lean Manufacturing, Theory of Constraints, Operational Diagnostics), Toyota Production System in international production sites. • Developing a coherent strategy on every organization level while using different tools (Hoshin Kanri, Strategy and Tactic Tree) aimed to increase operational efficiency (e.g. Throughput, Time Efficiency, reducing of materials, etc.). • Creating a tailor-made solution with an international cross-department team focused on increasing sales and market share while developing and installing Irresistible Offer in the supply chain (TOC). • Leading training and workshops of Value Stream Mapping, Problem Solving, 5’S, Standard Work, SMED, TPM, TWI, Kanban, Kaizen Blitz (Rapid Improvement Event) in the multi-cultures environment (Europe, North America, Russia, China). • Performance management system implementation (Oobeya) with significant involvement of shopfloor focused on increasing overall KPIs (Safety, Quality, Productivity, etc). Show less
-
-
-
General Electric
-
Canada
-
Machinery Manufacturing
-
1 - 100 Employee
-
Materials Manager (Supply Chain Manager)
-
Oct 2011 - Dec 2013
• Managing departments: Purchase, Production Planning, Customer Service and Internal Logistics departments as well as raw materials and finished goods warehouses. • Creation and implementation of strategy related to purchase of raw materials and semi-finished products for the plant, while maintaining optimum stock levels and focus on transport cost. • Annual budgets planning in the areas of all stock recourses, overheads and investments. • Managing departments: Purchase, Production Planning, Customer Service and Internal Logistics departments as well as raw materials and finished goods warehouses. • Creation and implementation of strategy related to purchase of raw materials and semi-finished products for the plant, while maintaining optimum stock levels and focus on transport cost. • Annual budgets planning in the areas of all stock recourses, overheads and investments.
-
-
-
Flint Group
-
United States
-
Consumer Services
-
1 - 100 Employee
-
LOGISTIC DEPARTMENT MANAGER, PROJECT MANAGER
-
Jun 2004 - Sep 2011
06.2010 – 09.2011 Logistic Department Manager, Project Manager 03.2006 – 05.2010 Logistic Department Manager 06.2004 – 02.2006 Logistic Specialist • Managing departments: Purchase, Customer Service, Production and Warehouse departments. • Building and maintaining good relations with key customers. • Training employees in Lean Six Sigma (5S, Visual Management, VSM, Muda Elimination, DMAIC, Project Management). • Planning layout of production lines, warehouses and material flow in the new plant. • Coordination of SAP implementation. Show less
-
-
-
BASF
-
Germany
-
Chemical Manufacturing
-
700 & Above Employee
-
Logistics specialist
-
Jan 2002 - May 2004
• Creation of orders and control of timely deliveries of raw materials, products and services. • Forecasting supply demands to motherplants through forecasts received from end customers. • Creation of orders and control of timely deliveries of raw materials, products and services. • Forecasting supply demands to motherplants through forecasts received from end customers.
-
-
Education
-
International Certification of Lean Six Sigma Methodology
-
Szkoła Główna Handlowa w Warszawie
Diploma, Post-graduate Logistics Management Studies -
Uniwersytet Łódzki
Master's degree, Economics
Community
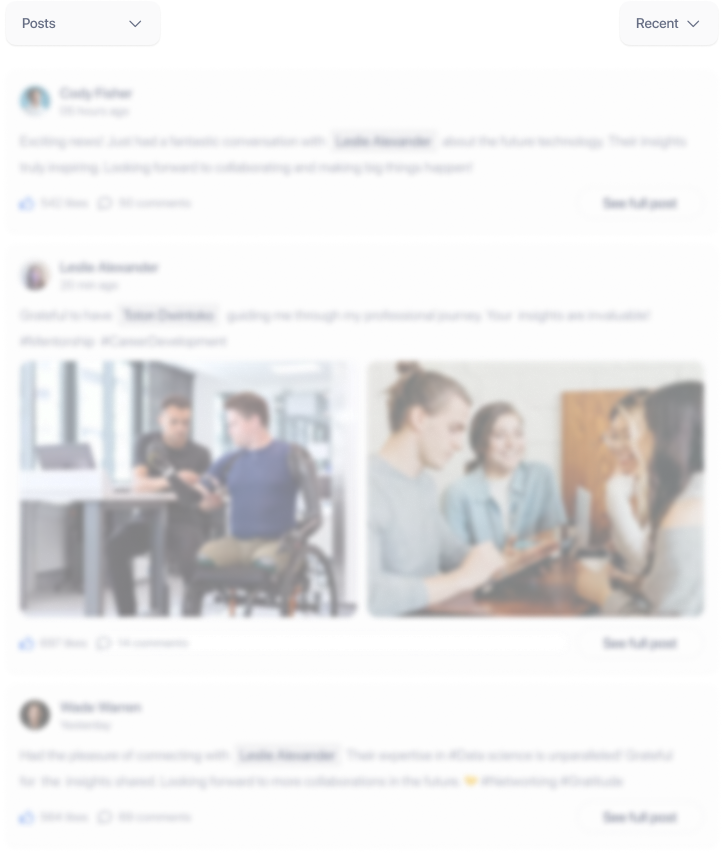