Elvis Molina
Production Manager - Pest and Rodent Control Division at Woodstream Corporation- Claim this Profile
Click to upgrade to our gold package
for the full feature experience.
-
English Native or bilingual proficiency
-
Spanish Native or bilingual proficiency
Topline Score
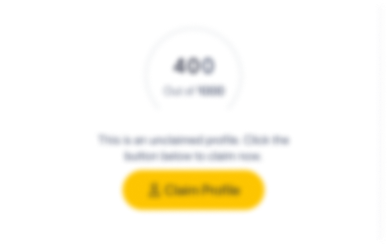
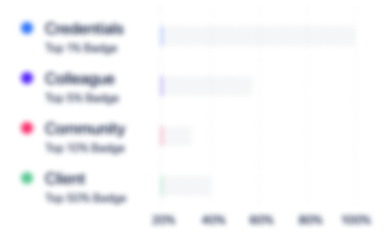
Bio

LinkedIn User
I have worked on and off with Elvis over the years and it has always been a joy. He is very great at what he does and I hope to continue our professional relationship.

Jim Bakken
To whom it may concern: I have known Elvis Molina for approximately 4 years. I am Jim Bakken, an Account/Project Manager at Placon Corporation. I have 8 years of experience working in Project Management and have seen many young professionals come and go. Elvis Molina is one individual I have worked with who uniquely stands out. Elvis and I met while working at Select Sound and later worked at Gar Plastic together. During our time together, Elvis displayed an innovative mindset, an eagerness to learn, and a perseverance that could not compare to his coworkers. When I met Elvis, I knew right away that he is a hardworking and self-motivated individual. Elvis was working 2 or 3 jobs at the time while taking college courses and was able to balance all the demands and excel at his roles at both Select Sound and Gar Plastic. I watched Elvis firsthand implement his experience and knowledge in operations and supply chain to create a leaner and more functional workflow at Gar Plastic. Please feel free to reach out with further questions.

LinkedIn User
I have worked on and off with Elvis over the years and it has always been a joy. He is very great at what he does and I hope to continue our professional relationship.

Jim Bakken
To whom it may concern: I have known Elvis Molina for approximately 4 years. I am Jim Bakken, an Account/Project Manager at Placon Corporation. I have 8 years of experience working in Project Management and have seen many young professionals come and go. Elvis Molina is one individual I have worked with who uniquely stands out. Elvis and I met while working at Select Sound and later worked at Gar Plastic together. During our time together, Elvis displayed an innovative mindset, an eagerness to learn, and a perseverance that could not compare to his coworkers. When I met Elvis, I knew right away that he is a hardworking and self-motivated individual. Elvis was working 2 or 3 jobs at the time while taking college courses and was able to balance all the demands and excel at his roles at both Select Sound and Gar Plastic. I watched Elvis firsthand implement his experience and knowledge in operations and supply chain to create a leaner and more functional workflow at Gar Plastic. Please feel free to reach out with further questions.

LinkedIn User
I have worked on and off with Elvis over the years and it has always been a joy. He is very great at what he does and I hope to continue our professional relationship.

Jim Bakken
To whom it may concern: I have known Elvis Molina for approximately 4 years. I am Jim Bakken, an Account/Project Manager at Placon Corporation. I have 8 years of experience working in Project Management and have seen many young professionals come and go. Elvis Molina is one individual I have worked with who uniquely stands out. Elvis and I met while working at Select Sound and later worked at Gar Plastic together. During our time together, Elvis displayed an innovative mindset, an eagerness to learn, and a perseverance that could not compare to his coworkers. When I met Elvis, I knew right away that he is a hardworking and self-motivated individual. Elvis was working 2 or 3 jobs at the time while taking college courses and was able to balance all the demands and excel at his roles at both Select Sound and Gar Plastic. I watched Elvis firsthand implement his experience and knowledge in operations and supply chain to create a leaner and more functional workflow at Gar Plastic. Please feel free to reach out with further questions.

LinkedIn User
I have worked on and off with Elvis over the years and it has always been a joy. He is very great at what he does and I hope to continue our professional relationship.

Jim Bakken
To whom it may concern: I have known Elvis Molina for approximately 4 years. I am Jim Bakken, an Account/Project Manager at Placon Corporation. I have 8 years of experience working in Project Management and have seen many young professionals come and go. Elvis Molina is one individual I have worked with who uniquely stands out. Elvis and I met while working at Select Sound and later worked at Gar Plastic together. During our time together, Elvis displayed an innovative mindset, an eagerness to learn, and a perseverance that could not compare to his coworkers. When I met Elvis, I knew right away that he is a hardworking and self-motivated individual. Elvis was working 2 or 3 jobs at the time while taking college courses and was able to balance all the demands and excel at his roles at both Select Sound and Gar Plastic. I watched Elvis firsthand implement his experience and knowledge in operations and supply chain to create a leaner and more functional workflow at Gar Plastic. Please feel free to reach out with further questions.

Credentials
-
Leadership Foundations
LinkedInSep, 2023- Nov, 2024 -
Plastic Molding Fundamentals
UdemySep, 2023- Nov, 2024 -
Top 10 Rules for Highly Effective Leadership
LinkedInSep, 2023- Nov, 2024 -
Teamwork Foundations
LinkedInJul, 2023- Nov, 2024 -
Business Etiquette: Phone, Email, and Text
LinkedInJun, 2023- Nov, 2024 -
Coaching and Developing Employees
LinkedInMar, 2023- Nov, 2024 -
Performance Management: Conducting Performance Reviews
LinkedInMar, 2023- Nov, 2024 -
Successful Supervision - Leadership Course
Cargas SystemsFeb, 2023- Nov, 2024 -
Communication Foundations
LinkedInDec, 2022- Nov, 2024 -
Developing Leadership Presence
LinkedInDec, 2022- Nov, 2024 -
Employee Engagement
LinkedInDec, 2022- Nov, 2024 -
Improving Equipment Uptime and Performance with TPM
University of Wisconsin-MadisonNov, 2022- Nov, 2024 -
Understanding Business
LinkedInOct, 2022- Nov, 2024 -
Be the Manager People Won't Leave
LinkedInFeb, 2022- Nov, 2024 -
Human Intelligence - Critical Thinking
CPA.comAug, 2021- Nov, 2024 -
Time Management
CPA.comAug, 2021- Nov, 2024 -
Emotional Intelligence
CPA.comJun, 2021- Nov, 2024 -
Leading vs Managing
CPA.comJun, 2021- Nov, 2024 -
Coaching and Mentoring
CPA.comMay, 2021- Nov, 2024 -
Fall Protection
American Society of Safety Professionals (ASSP)May, 2021- Nov, 2024 -
Finance Foundations
LinkedInSep, 2020- Nov, 2024 -
Finance and Accounting
International Business Management Institute (IBMI)Sep, 2020- Nov, 2024 -
Lean Foundations
LinkedInJun, 2020- Nov, 2024 -
Lean Six Sigma Yellow Belt Certification
GoLeanSixSigma.comJun, 2020- Nov, 2024 -
Process Improvement Foundations
LinkedInJun, 2020- Nov, 2024 -
Public Speaking Foundations
LinkedInJun, 2020- Nov, 2024 -
Six Sigma: Green Belt
LinkedInMay, 2020- Nov, 2024 -
Lean Inventory Management
LinkedInApr, 2020- Nov, 2024 -
Strategy and Operations
International BusinApr, 2020- Nov, 2024 -
Business Process Improvement
LinkedInMar, 2020- Nov, 2024 -
Quality Management Foundations
LinkedInMar, 2020- Nov, 2024 -
Strategic Planning Foundations
LinkedInFeb, 2020- Nov, 2024 -
OSHA 10
OSHA Training Institute Education CenterDec, 2019- Nov, 2024 -
Time Management for Managers
LinkedInOct, 2019- Nov, 2024 -
Implementing Supply Chain Management
LinkedInAug, 2019- Nov, 2024 -
Inventory Management Foundations
LinkedInAug, 2019- Nov, 2024 -
Job Skills: Supply Chain and Operations
LinkedInJul, 2019- Nov, 2024 -
Six Sigma Foundations
LinkedInJul, 2019- Nov, 2024 -
Working with Difficult People
LinkedInJul, 2019- Nov, 2024 -
Operational Excellence Foundations
LinkedInJun, 2019- Nov, 2024 -
8 Wastes Training & Certificate
GoLeanSixSigma.comMar, 2019- Nov, 2024 -
5S Training & Certificate
GoLeanSixSigma.comFeb, 2019- Nov, 2024 -
A3 Certificate
GoLeanSixSigma.comFeb, 2019- Nov, 2024 -
Supply Chain Foundations
LinkedInJul, 2018- Nov, 2024 -
Lean Six Sigma Foundations
LinkedInJun, 2018- Nov, 2024 -
Lean Six Sigma White Belt Certification
Aveta Business InstituteJun, 2018- Nov, 2024 -
Operations Management Foundations
LinkedInJun, 2018- Nov, 2024 -
Fall Protection for the Competent Person
LWSC Latino Worker Safety Center - Multilingual Safety TrainingApr, 2021- Nov, 2024 -
Hazard Communication (GHS)
LWSC Multilingual Safety TrainingMar, 2020- Nov, 2024 -
Respiratory Protection
LWSC Multilingual Safety TrainingMar, 2020- Nov, 2024 -
Silica Hazard Awareness
LWSC Multilingual Safety TrainingMar, 2020- Nov, 2024 -
CPR & AED
American Heart AssociationJun, 2020- Nov, 2024 -
Visual Management
GoLeanSixSigma.com
Experience
-
Woodstream Corporation
-
United States
-
Manufacturing
-
200 - 300 Employee
-
Production Manager - Pest and Rodent Control Division
-
Nov 2022 - Present
-
-
Manufacturing & Warehouse Operations Manager - Wild Bird Division
-
May 2022 - Nov 2022
•Responsible for our overall Wild Bird Feeder Assembly and Warehouse operation in Beaver Dam, WI as well as our Wild Bird Nectar Production and Warehouse operation in Juneau, WI including safety, quality, employee relation, process improvement, etc.•Completed the successful implementation of a quality management system (QMS) to make our nectar facility compliant with FDA rules and regulations including the areas of Hazardous Analysis Critical Control Points (HACCP) and the Food Safety Modernization Act (FSMA).•Facilitated a smooth transition as part of the acquisition of Classic Brands into the Woodstream Corporation family including the adoptions and implementation of new policies and procedures as well as the ERP transition going from Oracle NetSuite into AS400.•Achieved over 365 days of no-loss time due to work injury through the use of proper PPE and safety-first culture.•Developed Wisconsin's leadership team to continue Wisconsin's operations in my absence as I transitioned to a new division of the company. Show less
-
-
-
Classic Brands LLC
-
United States
-
Manufacturing
-
1 - 100 Employee
-
Manufacturing and Warehouse Operations Manager
-
Aug 2021 - May 2022
•Responsible for the manufacturing and warehouse operations of the Droll Yankee facility in Connecticut, US, and the wild bird nectar facility in Wisconsin, US •In a strategic initiative to improve the bottom line, relocated the manufacturing, warehousing, and eCommerce operation from Connecticut, US to Wisconsin, US •In addition to the manufacturing/assembling of wild bird feeders, and warehouse operations, I was responsible for our eCommerce/direct-to-consumer shipping operations, quality, maintenance, and safety programs. •While overseeing our wild bird nectar concentrate, ready-to-use (RTU), and dry sugar divisions, and in collaboration with our maintenance team, engaged in line-specific process improvements that increased throughputs by 20% •Was responsible for the operation of two different production facilities (our $6.5 million revenue Bird Feeder Assembly and our $3.5 million revenue division wild bird nectar) simultaneously managing staffing relations, in-site safety & quality, and coordinating with different teams in-site and remotely to ensure that products and were always available and of the highest quality for our customers from both facilities •Successfully reduced the headcounts by 30% in both facilities combined while maintaining the same level of operations efficiencies through process improvements, merging roles, and promotions, and eliminating redundant roles and tasks. •Build relationships with temp agencies, freight carriers, training, service and supplies providers to drive a success operation on all levels. •Initiated the implementation of a quality management system (QMS) to make our nectar facility compliant with FDA rules and regulations including the areas of Hazardous Analysis Critical Control Points (HACCP) and the Food Safety Modernization Act (FSMA). Show less
-
-
-
GAR Plastics
-
United States
-
Plastics Manufacturing
-
1 - 100 Employee
-
Operations Manager
-
May 2018 - Aug 2021
•Responsible for managing warehouse operations (including shipping, receiving, and inventory accuracy), maintenance, quality control & assurance, manufacturing production scheduling and safety, ensuring that all products are manufactured safely, on schedule, within quality standards and cost effective •Successfully created, implemented, and managed a production planning schedule that changed the organization's production operation to one well-structured that ensured all products were produced on time and were always available. This translated to over $13M or over 20% growth in sales in 2019 by maximizing plastics grinding and extrusion production runs and reducing changeover downtime•Developed and managed an MRP system that improved our levels of inventories by effectively reducing our on-hand Polystyrene inventory allowing purchasing to purchase the correct amount needed per month which in turn reduced our warehouse usage by 15% while ensuring that we wouldn’t have either excess or lack of materials•Work in conjunction with company officers (CEO & CFO) in the development of short-term and long-range strategic planning, policies, programs, procedures, and operational objectives•Effectively managed three different production facilities simultaneously managing staffing relations and logistics to ensure that products and staff were always available for production in all three facilities •Through staff restructuring, reduced freight expenses from 14% to 7% of total sales and over $150K in savings a year •Successfully established and launched the company’s quality assurance program involving line quality checks, inbound/outbound quality checks, retain collections, product control utilization, material testing, and inbound sampling•Reduced rate of head injuries and box cutter injuries to zero (0) by implementing the use of PPE across the entire organization Show less
-
-
Production Supervisor
-
Mar 2018 - Apr 2018
Responsible for supervising production operations.
-
-
-
Bell Laboratories, Inc.
-
United States
-
Manufacturing
-
1 - 100 Employee
-
Baits & Formulations Production Supervisor
-
Mar 2017 - Mar 2018
•Selected to direct and oversee approximately 90 employees, providing direct supervision to 45 production employees in the baits and formulations department, including Shift Coordinators, Machine Operators, Formulators, and Packers: and indirect supervision to 45 plastics & assembly employees, including, Plastic Inspectors, Auto-Assembly Inspectors, Shipping & Receiving, Quality Assurance, Maintenance, Trainers and Shipping & Receiving Personnel •Ensured the production of company products was at the highest quality level at the lowest possible cost, meeting company performance standards, customer specifications, and delivery requirements •Partnered with the Production Manager and Human Resources to manage employee relations issues and address, document, and resolve employee issues promptly •Successfully restructured the Telstar Glue Card department operation removing one packer from the room and successfully using said packer to improve our capacity. This resulted in the implementation of the new operation process on all three production shifts •Elevated 3rd shift’s production performance to numbers never seen before through team-building initiatives •Created 3rd shift operational plan for transitioning to a new facility while operating the old one at the same time •Built the best milling operation crew that was later on used as the standard to train other staff members in other shifts •Through the employment of lean six sigma initiatives, improved production issues in the glue line department increasing product output from 500 boxes of glue traps to over 700 cases per shift •Reduced the turnover of the baits and formulations department from 36% to under 25%in with several months of zero (0) turnover in my department •Authored and delivered all performance reviews and disciplinary records for the department promptly Show less
-
-
-
VPP Group, LLC
-
Norwalk, Wisconsin
-
Production Manager
-
Jan 2016 - Mar 2017
•In charge of the daily processing of 150,000 to 220,000 pounds of meat by gathering information from different departments and coordinating with marketing/sales to fulfill all scheduled orders on time •Reduced overhead expenses in the production department by successfully merging a supervisory and managerial role, resulting in over 50K dollar savings a year •Provided direct supervision to between 65 and 90 employees combined in the production, receiving, shipping, and whiz departments to ensure all products were produced in a safe and timely manner that complied with company good manufacturing practices (GMPs) and USDA rules and regulations •Applied lean manufacturing and six sigma concepts to streamline production processes that improved production efficiencies resulting in a reduction of production overtime expenses •Collaborated with Maintenance to ensure the safe and reliable functioning of all production equipment •Analyzed daily production yields by comparing yields against company standards to ensure the best quality of the product was made with the least amount of waste; defects were corrected, and continuous improvement was achieved; successfully maintaining production yields between 68% and 72% •Collaborated with the quality control and sanitation departments to ensure product was being produced to the highest quality and sanitary standards •Responsible for interviewing, and hiring staff as well as providing performance reviews, and disciplinary actions and collaborated with HR for employee terminations Show less
-
-
-
Century Foods International
-
United States
-
Health, Wellness & Fitness
-
1 - 100 Employee
-
Quality Control Laboratory Technician I
-
Oct 2013 - Oct 2015
• Inspected, sampled, prepared, and evaluated ingredients/components, intermediate products, and finished products while meeting quality parameters in a safe, sanitary, and productive manner and reporting all results to quality management. • Based on the quality program, approved product to be processed, monitored the production of approximately 350 bottles of “ready to drink” (RTD) product per minute to ensure the required output and quality were satisfied• Ensured compliance with the Hazard Analysis Critical Control Points (HACCP) program and maintained the program in the production facility by providing training to all new quality control technicians• Examined samples of raw products to determine if they were ready for production or needed adjustment and implemented the necessary corrections utilizing AS400 software• Collected samples and performed various tests, including, but not limited to, in-line sensory testing, in-line titratable acidity testing, in-line pH testing, ATP swabbing, equipment sponges swabbing to prevent bacteria growth, and in-line production sampling to ensure the product was ready to be sent to the packaging department• Ensured company standards, Good Manufacturing Practices (GMPs), SOPs, safety rules, Good Laboratory Practices (GLPs), and food/dietary supplement regulatory requirements were followed Show less
-
-
Packaging Specialist
-
Jul 2013 - Oct 2013
• Packaged and stacked finished product containers for shipping• Completed setups, changeovers, and operation of the equipment to production and quality standards• Inspected and verified codes and integrity of packaging within the required specifications of the product• Assisted in all other duties assigned by supervisor and management
-
-
-
Wisconsin Department of Corrections
-
United States
-
Government Administration
-
400 - 500 Employee
-
Correctional Officer I
-
Oct 2013 - Jul 2014
• Supervised inmates and ensured they were complying with both DOC rules/regulations and institutional rules and regulations • Provided security and safety to over 1,000 inmates, personnel, and the public • Taught, modeled, and reinforced positive change for inmates to help them successfully reintegrate back into society • Responsible for ensuring that all areas and cells (locks, door tracks, and frames; opening and inspection of security screens, desks, chairs, tables, etc.) were inspected • Directed and escorted inmates to locations within the facility and outside the facility at correct times for appointments or other scheduled activities • Formally offered position as Sergeant after 6 months of employment Show less
-
-
-
Puerto Rico Police
-
Law Enforcement
-
1 - 100 Employee
-
Homicide Investigations Intern
-
Jan 2011 - May 2011
• Performed Crime Scene Investigation on homicide cases, suicides, and natural death as well on others major cases on a case by case basis • Coordinate the securing or disposition of case related property • Participated of witness interviews and suspects interrogation • Assisted to other Department Units, as well as outside agencies requesting assistance in the processing of crime scene evidence • Completed reports of arrests, accidents, and evidence securing • Responsible for drawing sketches of crime scenes for evidence purposes Show less
-
-
Education
-
Southern New Hampshire University
Master of Business Administration - MBA, Operations and Supply Chain Management -
Quinlan School of Business, Loyola University Chicago
Certificate, Mini-MBA, Business Administration and Management, General -
Liberty University
Certificate Degree, Legal Studies, General -
Inter American University of Puerto Rico-Aguadilla
Bachelor of Science - BS, Criminal Justice and Corrections
Community
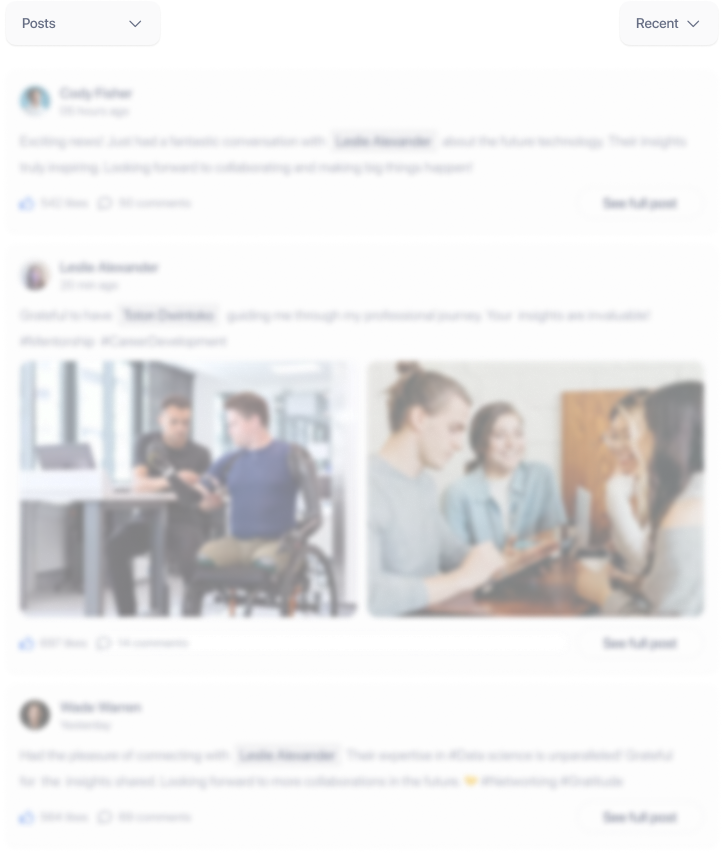