
Elizabeth Hunter BSc (Hons)
Specifications Technologist at FoodPack- Claim this Profile
Click to upgrade to our gold package
for the full feature experience.
Topline Score
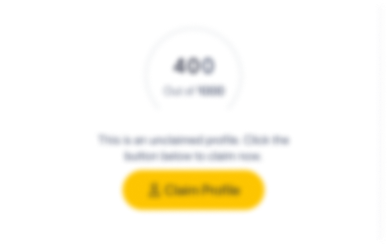
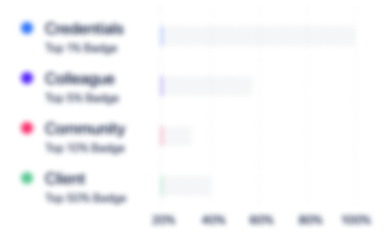
Bio


Credentials
-
Audit and Inspection Skills
PROGRESS SAFETY LTDMar, 2019- Nov, 2024 -
TQC Food Training
Ashbury TrainingFeb, 2019- Nov, 2024 -
One Day Food & Drink Labelling
Campden BRIJan, 2019- Nov, 2024 -
Managing Food Allergens for Manufacturing
Verner WheelockSep, 2017- Nov, 2024 -
Cleaning in the Food Industry
The Chartered Institute of Environmental HealthAug, 2017- Nov, 2024 -
Food Safety Supervision for Manufacturing Level 3
Royal Society for Public HealthOct, 2016- Nov, 2024 -
HACCP for Food Manufacturing Level 3
Royal Society for Public HealthJun, 2016- Nov, 2024 -
Pest Awareness
EcolabJun, 2016- Nov, 2024 -
Auditing Skills
Verner WheelockApr, 2016- Nov, 2024 -
Food Allergy Online Training
Food Standards AgencyApr, 2016- Nov, 2024 -
Food and Drink Labelling and Additives
Campden BRIMar, 2016- Nov, 2024 -
First Aid
Culina Group LimitedFeb, 2020- Nov, 2024 -
Food Safety in Food Manufacturing L2
The Chartered Institute of Environmental Health -
Working safely with chemicals
CCL PENTASOL LIMITED
Experience
-
FoodPack
-
United Kingdom
-
Food Production
-
1 - 100 Employee
-
Specifications Technologist
-
Jul 2019 - Present
Fully responsible for creating, reviewing and managing products and material specifications on internal and external retail customers Web-based portals. I have in depth experience with all major retailer portals. Responsible for Managing supplier approval on site. I have developed and maintained a fantastic system for Supplier Approval at Foodpack. It is one of my proudest achievements and I really take pride in my systems and ensure they are effective and easily followed in the event of audits. Audit Experience: Very comfortable in front of an auditor and able to remain calm and present clearly and concisely and work well under pressure. Third Party Audit Experience Includes: AIB, BRC, RSPO, Soil Association, ASDA bolt on for AA and Free From, Tesco Audit etc. I am also responsible for risk assessing all raw materials on site for Vulnerability and Threats for adulteration and keeping upto date with emerging threats and new legislation. Responsible for completing, issuing and maintaining Raw Material Intake Cards and Manufacturing Specifications which captures all information necessary to produce food legally, safely and the quality demanded by the customer. Responsible for the upkeep and maintenance of the QMS including document control. Responsible for all artwork approvals on site and ensuring all own branded artwork is in compliance with Regulation (EU) No 1169/2011. ( I have 8+ years of experience with Reg 1169/2011). HACCP and Vulnerability Team member. Hands on involvement in carrying out and presenting Traceability Exercises. Carrying out mock recall exercises.Responsible for maintaining the calibration schedule on site. Apart of the internal auditing team ensuing all audits are carried out in a timely manner to schedule and ensure all actions are monitored until close out.
-
-
-
Sime Darby Oils
-
Malaysia
-
International Trade and Development
-
200 - 300 Employee
-
Quality Assurance Technologist
-
Mar 2019 - Jul 2019
During my 5 months at SDO, I implemented a new internal audit and supplier approval system and also I updated all documents in the QMS in line with a business transition and company name change. Although this was a very short time at SDO, I feel like my time was well spent and I enjoyed my time and learnt a lot about an industry I wasn't very familiar with (fat and oils).During this time, I took part in the BRC, Kosher & RSPO audits.
-
-
-
Trigon Snacks Trading Ltd
-
United Kingdom
-
Food and Beverage Manufacturing
-
1 - 100 Employee
-
Technical technologist
-
Jul 2018 - Mar 2019
Reason for leaving: RedundancyMy main responsibility on site is to support Site Technical Manager in the management of the safety, legality, quality and Brand Standards of Own Brands for major retailers. Writing of Specifications and Quality Attribute Sheets & Utilisation of Customer Portals.To ensure that manufacturing standards are in place to meet all customer and legal requirements and supporting Factory Technical Manager to ensure that the site is aware of and complying with customer Technical policies, codes of practice, and legal requirements.Responsible for Supplier Approval across site ensuring that our system adheres to BRC requirements.To manage retailer customer complaints and production of KPI reports, with trending and interpretation of data.To work with NPD in development and sign off of new products for retailers and to conduct artwork checks on own branded and retailer artworks using pack copies and the Regulation 1169/ 2011 FIC.Carrying out internal audits in line with the schedule against BRC and IFS standards.Hands on involvement with IFS, BRC, Fair Trade, Organics, RSPO, Customer visits and other external accreditation audits.I also adhoced worked within the Quality Assurance lab, line checking as well as carrying out in process checks for quality and food safety.During my time at Trigon Snacks Trading Ltd, I gained very valuable knowledge of many different raw materials and I have built a very strong working relationship with both suppliers and customers.
-
-
-
Bevie
-
New Zealand
-
Food and Beverage Services
-
1 - 100 Employee
-
Technical Officer
-
Apr 2016 - Jun 2018
Formally SPL International Ltd My roles within Bevie as a Technical Officer cover a wide range of tasks working alongside all Departments on site. I am a Supervisor responsible for the Hygiene Operative and Technical and Quality Assistant. My main other responsibilities are: Liaising with cross functional teams internally and externally to ensure all requests are fulfilled in a timely manner and to the high standard which is expected. Site hygiene and housekeeping - managing and maintenance of cleaning procedures and schedules. Managing the internal auditing system by scheduling, planning, and conducting internal audits on site according to the scope of the BRC Standard. Managing and monitoring the supplier and service supplier approval system. Co- managing the internal artwork approval system - ensuring artwork complies with Regulation 1169/2011 Fully trained member of the HACCP team. Hands on involvement in third party audits including BRC, kosher etc. Completing all customer document requests including product specifications , MSDS, CofA, SAQ, manufacturers etc.
-
-
-
SPL International
-
United Kingdom
-
Food and Beverage Services
-
100 - 200 Employee
-
Technical Administrator
-
Sep 2015 - Apr 2016
My main role is within the technical department at SPL International encompasses many area's within the business and working very closely with various other departments. Since my role has developed in SPL, I cover a wide range of tasks listed below:• I am fully trained in HACCP level 3 and a member of the HACCP team – also involved in updating process flows.• I have hands on involvement and knowledge of the BRC standard version 7. • I am involved in scheduling and completing internal audits on a regular basis and ensuring that these get carried out on time. – I also ensure that all NC’s get closed out on time and follow up on corrective actions. • I take part in other third party audits such as Kosher/ BRC• I am involved in ensuring all service suppliers are approved and attending supplier audits alongside my manager. • I am heavily involved in supplier approval and approval of raw materials . – I also ensure that all supplier accreditation is up to date.• I am responsible for keeping our food fraud and vulnerability assessment up to date by keeping documented evidence of relevant incidences which may relate to the company. – I also present this information in the monthly CI meeting. • I have an input with artwork approval and ensuring that product labeling complies with the Food information to consumer regulation 1169/2011. • I complete all customer’s technical documentation (Product Specifications, CofA’s, SAQ’s) and try to input into customer enquiries. • I am responsible for completing all MSDS enquiries have an input in chemical awareness. • I am involved within procedure writing to ensure that all our procedures are in line with BRC v7.I really enjoy this role and face all new challenges head on and gaining valuable experience for my future within the food manufacturing industry.
-
-
-
McDonald's
-
United States
-
Restaurants
-
700 & Above Employee
-
Crew Trainer
-
Jun 2008 - Sep 2015
During sevens years at McDonalds, I have gained a lot of valuable experience and I can cope well in pressurised situations. I am fully trained in food quality, cleanliness and service and I am able to apply this knowledge within my working environment. I gained many life skills at Mcdonalds such as commitment, reliability and loyalty. I have developed excellent people and customer service skills. I am always willing to accept new challenges and open to learning new skills.
-
-
Education
-
Cardiff Metropolitian University
Bachelor’s Degree, Food Science and Nutrition -
Broughton Hall High School
A-levels
Community
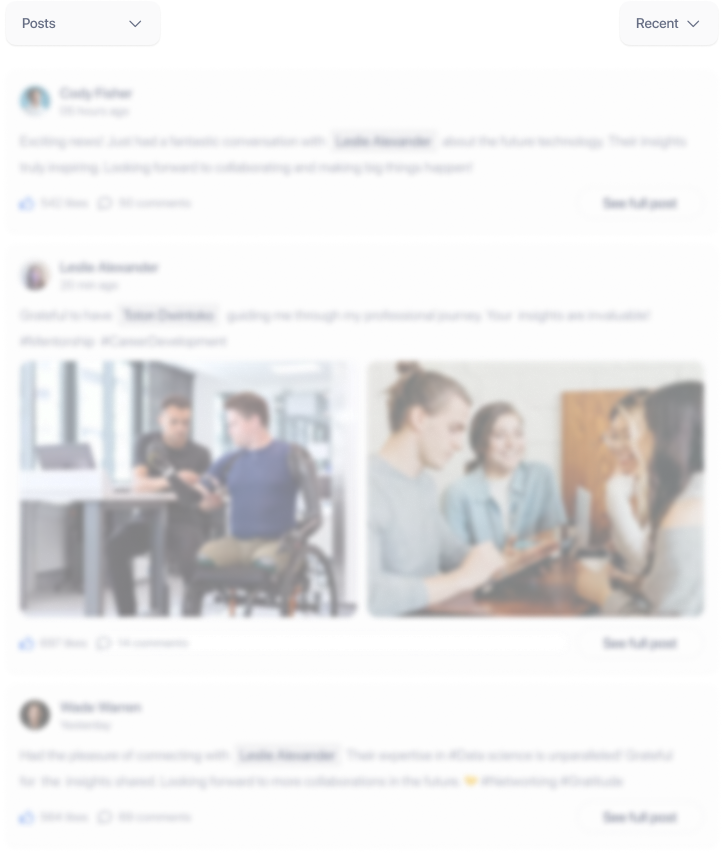