Eissa Mohamed
Supply Chain Manager at Albashaier- Claim this Profile
Click to upgrade to our gold package
for the full feature experience.
Topline Score
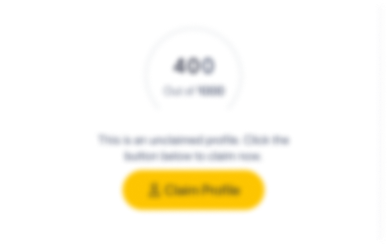
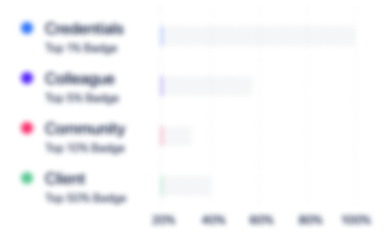
Bio
0
/5.0 / Based on 0 ratingsFilter reviews by:
Experience
-
Albashaier
-
Food and Beverage Manufacturing
-
1 - 100 Employee
-
Supply Chain Manager
-
Aug 2022 - Present
-
-
Supply Chain Management Consultant
-
Oct 2019 - Jul 2022
-
-
-
El Rancho Egypt
-
Egypt
-
Food and Beverage Manufacturing
-
1 - 100 Employee
-
Supply Chain Manager
-
Apr 2022 - Jul 2022
-
-
-
-
Supply Chain Manager
-
Aug 2020 - Mar 2022
-
-
-
Milky's
-
Cameroon
-
Manufacturing
-
1 - 100 Employee
-
Supply Chain Director
-
Mar 2018 - Jul 2019
-
-
-
Wadi El-Nile for Agricultural & Animal Products
-
Egypt
-
Food and Beverage Services
-
1 - 100 Employee
-
Supply Chain Manager
-
May 2016 - Feb 2018
I established the supply chain system from A to Z planning, sourcing, purchasing, production and transport, and implementing initiatives to reduce the overall supply chain cost base around 2 million dollars in the first year. Monitoring data management to keep accurate delivery. Working closely with suppliers and service providers to improve operations and reduce cost and Improving supplier capability to meet the business’s needs. Communicating needs & objectives to managers & key personnel in procurement, logistics & production. Negotiating contracts to reduce costs and achieve maximum efficiency. Accurately calculating total supply chain costs in relation. Obtaining quotes for transportation and also making cost comparisons. Supply planning in advance for seasonal periods and promotional events. Ensuring the continuity of product supply. Coming up with solutions to availability issues. In charge of the supply chain budget. Involved in the hiring, training, supervising and mentoring of supply chain staff. Show less
-
-
-
Al-Watania Poultry (Egypt)
-
Egypt
-
Food and Beverage Manufacturing
-
300 - 400 Employee
-
Procurement Section Head
-
Feb 2011 - May 2016
Start working with Al Watania from Feb. 2011 in Procurement department as a senior order expedition specialist. After one year only promoted to strategic procurement supervisor (Packing material, Vaccines, Corn, Soya meal, Feed additives and Gasoline), and in 2015 promoted to a procurement section head and the assistance of the procurement manager in all the annual tenders. I was following-up all the PR and PO for all the five companies in the Al Watania Poultry group, so I established a PR and PO follow-up system as following. Register the purchase request details with the confirmed dates form the requester and the procurement department. Register the purchase order details based of the PR registration. Create communication follow-up sheet for each purchase order. Confirm order receiving and delivery date with the supplier. Solving any problem to affect the purchase order. Update the follow-up sheet with the confirmed delivery dates. Daley report for the all The purchase requests and orders Status. Weekly KPIs report for each specialist showing the percentage of saving and in time delivery. Monthly report for the orders delivered and under delivering purchase orders. Show less
-
-
-
Gianet Group
-
United Kingdom
-
1 - 100 Employee
-
Planning Section Head
-
Jun 2010 - Dec 2010
Designed a Planning System Designed a Planning System
-
-
-
-
Planning Section Head
-
Jan 2010 - Apr 2010
I established a new planning system. Production planning for each month. Master production schedule. Material requirements planning. Bill Of material. Production activities follow up and control. Daily, weekly and monthly reports for the production and order situations. I established a new planning system. Production planning for each month. Master production schedule. Material requirements planning. Bill Of material. Production activities follow up and control. Daily, weekly and monthly reports for the production and order situations.
-
-
-
Marche Market
-
Canada
-
Food and Beverage Services
-
Project Manager
-
Sep 2008 - Dec 2009
The mission was to startup the market and put it on the right way. The results were more improved than they anticipated, that during the soft opening and before the official opening, the sales numbers was second grade in 10th of Ramadan city's markets. Participated in market structuring. Established and implemented the startup plan. Established working system. The mission was to startup the market and put it on the right way. The results were more improved than they anticipated, that during the soft opening and before the official opening, the sales numbers was second grade in 10th of Ramadan city's markets. Participated in market structuring. Established and implemented the startup plan. Established working system.
-
-
-
-
Partner and Manager
-
Jun 2006 - Oct 2008
This project started with two grinding machines, After one year they were three machines working with full capacity (12 hours/day), and in the 3rd year I imported two new CNC machines from China, as first time for this brand name after a long research, As result I imported another two machines to another workshops. Highly accuracy (± 0.01 mm). Workers training. Machine operator. Sales agreements. Marketing management. This project started with two grinding machines, After one year they were three machines working with full capacity (12 hours/day), and in the 3rd year I imported two new CNC machines from China, as first time for this brand name after a long research, As result I imported another two machines to another workshops. Highly accuracy (± 0.01 mm). Workers training. Machine operator. Sales agreements. Marketing management.
-
-
-
MAC Carpet
-
Textile Manufacturing
-
100 - 200 Employee
-
Senior Production Planner
-
Dec 1999 - Jan 2003
Production planning and follow up all production and Export process, On average exporting more than 1,500,000 Sqm./Month, Following up around 15 orders producing/day , loading and shipping 8 containers every day. I had started as ordinary employee in export department, and by industrious behaviors, I have promoted to export manager's assistant, Team leader, and production planner. Data Collecting and analyses. Creating simple and accurate Follow up models. Production and shipping schedule for all the new orders. Daily, weekly and monthly reports for the production and order situations. Follow up new quality processes. Follow up and improving all of the production processes. Participated in DOMOTEX HANNOVER 2003. AS Team Leader ( Production Follow up team ) Selecting and training the team members. Dividing team's tasks. Private guidance for each team member depends on his skills and ability. Improving employee relationships. Sustainable improving team productivity. This team was 8 members, now they are the leaders in the planning and follow up department over 70 employees. As Export Manager's assistant ( Fareast's Region) Preparing and managing everything related to region's orders. Follow up region's order's production. Follow up the loading and shipping containers. Following up and reviewing the documents. Follow up the new samples dispatch and customer's confirmation. Preparing for customers' hosting. Show less
-
-
Community
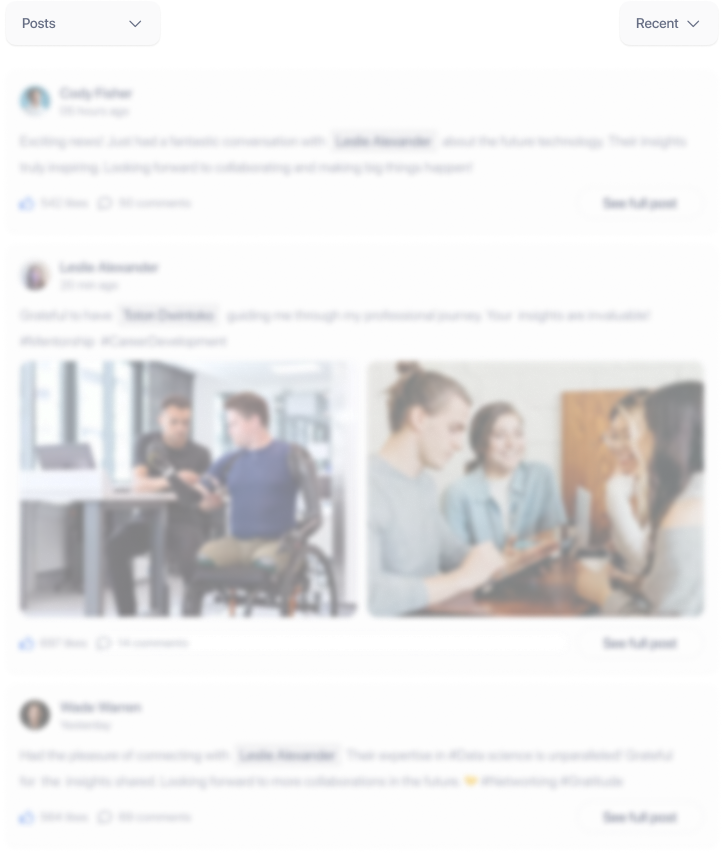