Edwin Salazar
Director, Customer Logistics at Simple Mills- Claim this Profile
Click to upgrade to our gold package
for the full feature experience.
-
Spanish -
-
French Limited working proficiency
Topline Score
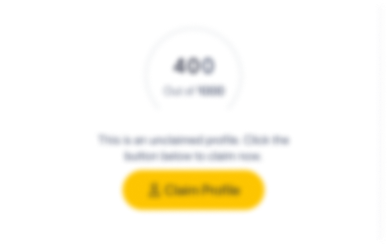
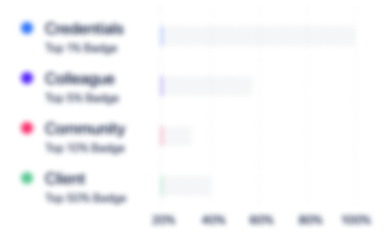
Bio


Credentials
-
Supply Chain Technology & Systems
edXSep, 2021- Nov, 2024 -
Supply Chain Dynamics
edXOct, 2019- Nov, 2024 -
Supply Chain Fundamentals
edXMar, 2018- Nov, 2024 -
Supply Chain Analytics
edXDec, 2017- Nov, 2024
Experience
-
Simple Mills
-
United States
-
Food and Beverage Manufacturing
-
1 - 100 Employee
-
Director, Customer Logistics
-
May 2022 - Present
-
-
Senior Manager, Customer Logistics
-
Mar 2021 - May 2022
• Lead a team of 6 employees ranging from Managers to Analysts covering Customer Supply Chain and Supply ChainSystems (ERP/EDI).• Own key relationships with 3PL partners including 3rd party warehouse and freight brokers.• Leading Warehouse RFP and co-leading Freight RFP to manage growing volume.• Main NetSuite admin that implements new processes including new workflows, writing scripts and maintaining master data.• Leads operation that maintains a 98+% annual fill rate, while managing product with relatively low shelf-life.
-
-
Senior Manager, Supply Chain Analytics
-
Nov 2019 - Mar 2021
• Led company-wide implementation of new ERP system paired with EDI and E-Comm modules.• Led technical and change management discussions with cross-functional teams to instill new technical and process changes.• Coordinated and ran UAT for both ERP and EDI implementations internally and externally to ensure functionality at launch.• Successfully launched new ERP and EDI systems simultaneously during global pandemic in newly-introduced remote work environment, with no major effect on key company KPIs.
-
-
-
Levy Restaurants
-
United States
-
Food & Beverages
-
700 & Above Employee
-
Supply Chain Innovation Manager
-
Jun 2019 - Nov 2019
- Helped lead implementation of new Procure-to-Pay/ERP at Levy's various locations nationwide - Worked cross functionally with both internal and external parties to solve complex problems throughout implementation - Training lead across various locations - Helped lead implementation of new Procure-to-Pay/ERP at Levy's various locations nationwide - Worked cross functionally with both internal and external parties to solve complex problems throughout implementation - Training lead across various locations
-
-
-
Wayfair
-
United States
-
Retail
-
700 & Above Employee
-
Manager, Inventory Planning Strategy
-
Aug 2017 - Jun 2019
• Partnered with top suppliers to develop their inventory strategy within CastleGate (CG) -Wayfair’s distribution network • Successfully executed strategy within supplier’s business goals to deliver CG annual sales of $46MM across 6800 SKUs • Oversaw supplier’s inventory health and developed unique exit strategies when inventory was deemed unhealthy • Led team of two which managed 23 suppliers with over $63.5MM in annual sales and average on-hand inventory of $30MM • Led co-op hiring within CG that led to hire of 8 co-ops and have conducted over 50 FTE interviews for analyst/manager roles • Represented inventory planning within international cross-functional team that helped launch new Canadian warehouse • Developed replenishment strategy to steadily ramp up Canadian warehouse and maintain inbound flow across 50+ suppliers • Bi-Annually participated in furniture trade shows where I would present key CG KPIs to various supplier C-level executives
-
-
-
Diageo
-
United Kingdom
-
Beverage Manufacturing
-
700 & Above Employee
-
Materials Planner
-
Feb 2017 - Aug 2017
• MRP Planner of $1MM category for Diageo North America's largest facility by volumeMeticulously manage label and corrugate inventory levels to ensure service is met while minimizing overall inventory levels• Manage master data to optimize planning ability of ERP system (SAP) including, but not limited to, BOM auditing• Lead plant and supplier relations to develop a highly collaborative partnership• Leading small projects to improve overall cycle counting processes and warehouse storage optimization
-
-
Commercialization Project Manager
-
Jan 2015 - Jan 2017
• Project Manager leading cross functional teams to commercialize new products in the Canadian market• Managed North America's Innovation and Brand Change KPIs and performance reporting that was shared with NAM senior leadership on a weekly and monthly basis• Designed and Implemented new SharePoint team site to facilitate ways of working and streamline processes for project managers leading cross functional teams• Recurring member of small annual team that focused on continuously improving Diageo's Commercialization processes to be best in class• North American lead the design and implementation of a new global portfolio management tool (Planview Enterprise) that would be used across various functions throughout Diageo• Planview global super user who frequently led training sessions for employees across the globe.
-
-
-
General Mills
-
United States
-
Manufacturing
-
700 & Above Employee
-
Team Leader II, Production Supervisor
-
Sep 2013 - Jan 2015
• Direct supervision of 3rd shift team of 35+ employees including production workers and maintenance technicians.• Start-up/Project manager for $1MM project that increased capacity and flexibility of cereal processing system.• Effectively managed all safety, quality, cost, and technical issues that arose on the backshift.• Served as main off-shift contact for R&D during 3 new product startups in the plant.• Trained new Team Leaders and monitored their progress throughout to ensure successful onboarding.• Managed and resolved conflicts that arose within team on shift while minimizing impact on plant's operation.
-
-
Manufacturing Engineering Associate
-
Aug 2011 - Sep 2013
• Engineering rotational program that exposed me to Systems & Project Engineering as well as Team Leading.• Led various improvements in system engineering role that delivered over $100M in annual cost savings to the plant.• Created a system startup reduction team that experienced a 19% reduction in startup times during the year I led it.• Project manager on projects that led to $70M in annual cost savings and improved personal safety in the plant.
-
-
-
General Mills
-
United States
-
Manufacturing
-
700 & Above Employee
-
Operations/Engineering Intern
-
Jun 2010 - Aug 2010
• Developed improved communication methods and applications to convey critical information to production team. • Implemented Continuous Improvement tools at the floor level to improve production performance & reliability. • Developed improved communication methods and applications to convey critical information to production team. • Implemented Continuous Improvement tools at the floor level to improve production performance & reliability.
-
-
-
General Mills
-
United States
-
Manufacturing
-
700 & Above Employee
-
Quality & Regulatory Operations Intern
-
Jun 2009 - Aug 2009
• Learned necessary microbiology material and lab procedures to successfully complete intern project. • Conducted kill step validation on snack bars to ensure production process met all food safety guidelines. • Learned necessary microbiology material and lab procedures to successfully complete intern project. • Conducted kill step validation on snack bars to ensure production process met all food safety guidelines.
-
-
Education
-
Cornell University
M. Eng, Engineering Management -
Cornell University
BS, Operations Research & Information Engineering
Community
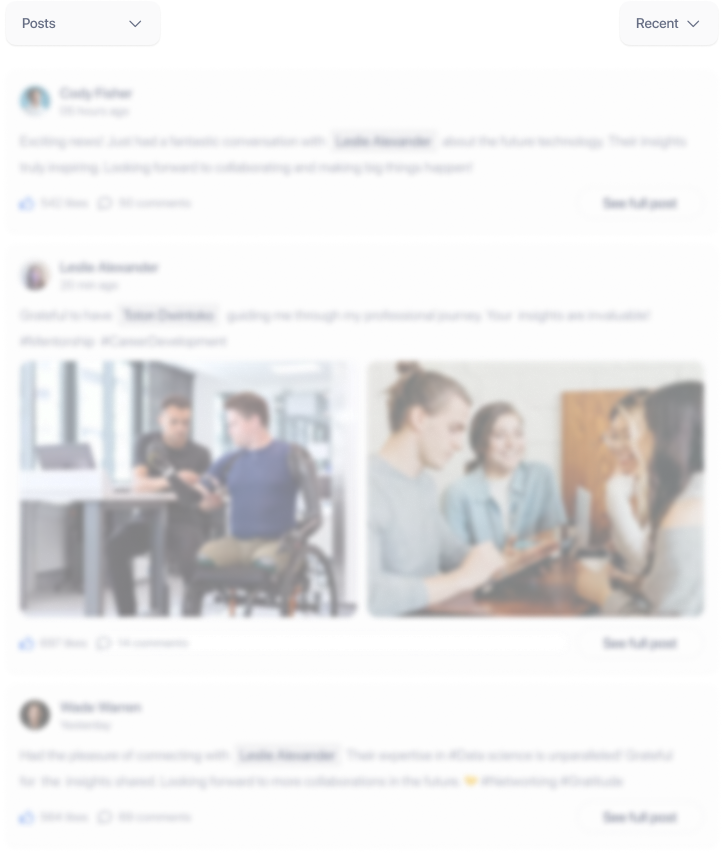