Edson Ramírez
Continuous Improvement Manager - Americas Operations at Wagner Spray Tech- Claim this Profile
Click to upgrade to our gold package
for the full feature experience.
-
Español Native or bilingual proficiency
-
Inglés Full professional proficiency
Topline Score
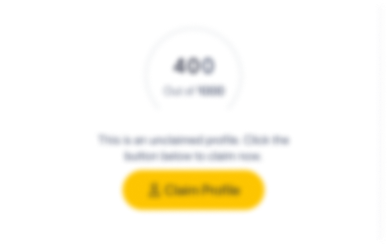
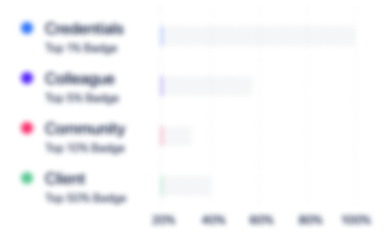
Bio


Credentials
-
Lean Manager
The Ohio State University
Experience
-
Wagner Spray Tech
-
United States
-
Consumer Goods
-
300 - 400 Employee
-
Continuous Improvement Manager - Americas Operations
-
Jul 2020 - Present
Srategic role to execute the world class vision throughout Wagner's Operations to achieve the financial objectives. Main responsibilities: - Drive the Continuous Improvement efforts within the functional business areas. - Provide leadership and strategic thinking for implementing the CI initiatives - Design the Continuous Improvement strategy for the Americas Operation in the US. - Coordinate the transformation through the operations to ensure the correct systems, processes, tools and methods that deliver consistent results to improve the Business' performance. Show less
-
-
-
Exertus Consulting
-
Mexico
-
Business Consulting and Services
-
1 - 100 Employee
-
Continuous Improvement and Lean Manufacturing Projects - BU Manager
-
Dec 2009 - Jul 2020
Management Position focused to lead Operational and Strategic Projects, achieving financial benefits by USD $ 25 M and metrics improvement by 45 %. Exceeded performance goals of my Business Unit by an average of 19 % during five consecutive years. Key responsibilities: • Coordinate manufacturing process assessments and define strategies to improve operational performance. • Lead Operations Improvement Projects: Assessment, budgeting, planning, execution, tracking and reporting. • Achieve operational and financial goals defined with shareholders. • Coach and mentor of Senior Project Consultants, Process Consultants and Business Analysts. Main implementations: • Shop floor systems to manage the operations area and track process performance • Manufacturing processes design: Flow, staffing and KPIs • Lean Manufacturing Tools and Continuous Improvement Systems - Design, Training, Coaching and implementation • Coordination of kaizen workshops in areas such as: Commercial, Demand Planning, Logistics, Purchasing, Operations, Merchandising and Finance. • Design of Continuous Improvement organizational structure, processes design, job profiles, roles, responsibiities, performance metrics and organizational transition plan. • Design of inventory strategies and replenishment schemes to optimize net working capital and improve customer service level • IBP design, meetings structure, roles, definition of demand, operations, supply and financial metrics Main Achievements: • Significant improvement in EBITDA by 12 %, by implementing new supply chain and operational strategies. • Improved operational indicators and profitability by 45 %, by the implementation of Continuous Improvement systems. • Increased production efficiency by optimizing a manufacturing process (27% improvement.) • Implemented Lean Strategies, resulting in a 18 % increase in productivity, a 28 % increase in process uptime and a 58 % decrease in quality rejections. Show less
-
-
-
Visteon Corporation
-
United States
-
Motor Vehicle Manufacturing
-
700 & Above Employee
-
Operational Excellence Manager
-
May 2008 - Dec 2009
Design, plan and implement the operative strategies to achieve organizational objectives defined by Visteon Corporation. Assigned by the North America CEO to develop the strategy for Shingo Prize. • Plant was awarded with Shingo Bronze Medallion for Operational Excellence. I was recognized with the Leading the Way Award, granted by Visteon Global Corporation for exemplary results and outstanding performance. • Responsible to ensure productivity and efficiency of the production lines. • Responsible to lead the execution of Value Stream Maps and Kaizen Workshops. Savings by USD $ 3.5M • Deployment of the TPM Strategy, machines uptime increased by 28%, OEE improved 18% and Scrap reduced by 58%. • Freights cost optimization by $ 2.2 M due to reduce transportations, relocate supplier base and define inventories schemes. • EBITDA margin improved from a negative – 36 % to 9 % in two years. • Lean Manufacturing Training & Coaching | More than 500 employees of all organizational levels were trained in North America facilities. Development of Kaizen leaders. • Development of a business assessment model to measure the Lean and Continuous Improvement maturity level (Cultural Behaviors, usage of Lean and CI Tools), performance improved from 71 to 94 % in one year Show less
-
-
-
Whirlpool Corporation
-
United States
-
Manufacturing
-
700 & Above Employee
-
Engineering Leader
-
Apr 2006 - May 2008
Supervision and administration of the Industrial Engineering department activities related with: - Productivity studies. Increasing from 80% to 88% by the elimination of bottle necks - Implementation of the Toyota Production System project. Improving the production efficiency with a reduction of 35% in the headcount as well as 51% of Service Incident Rate (Service Calls) - Report and control of key metrics OEE and OA. Elaboration of the action plans increasing the results from 70% to 82% - Responsible of the optimization and improvement of the production processes, machinery and equipment. Reduction of 27% in downtimes. - Development of the plant capacity plan, line balance and Headcount control - Support to the development of new projects and the introduction of new models (Trial runs, pilots and prototypes) - Layout administration and control manufacturing footprint changes - Responsible to coordinate optimization projects to maximize productivity and profitability, Show less
-
-
-
S.C. Alcoa Fujikura S.R.L.
-
Motor Vehicle Manufacturing
-
1 - 100 Employee
-
Manufacturing Engineer
-
Jan 2002 - Apr 2006
Responsible to design, implement and maintain the production systems of the production lines: • Development of continuous improvement projects to reduce operation and manufacturing costs by 36 %. • Assigned to the Corvette 2005 Launch Project for General Motors Company. • Responsible to design the assembly line, manufacturing process, PFMEA and Plant layout for Corvette Harnesses, implementing two assembly lines without Quality issues. • Control, management and implementation of engineering changes in the production floor, as well to assure the successful execution of the APQP process. Show less
-
-
Education
-
EUDE Business School
Master of Business Administration - MBA -
The Ohio State University - The Max M. Fisher College of Business
Executive Education - Lean Manager Specialist, Lean Manufacturing Certification -
Instituto Tecnológico y de Estudios Superiores de Monterrey / ITESM
Ingeniero Industrial y de Sistemas, Ingeniería
Community
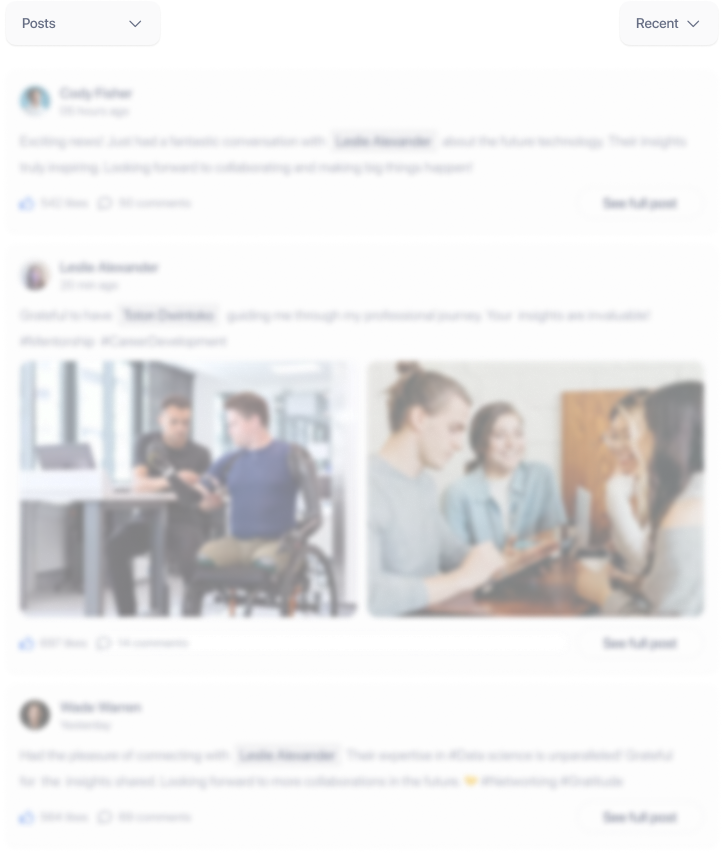