Edgar Emilio Silva Cajiga, MBA
Vice President Business Transformation at Invincible Boats- Claim this Profile
Click to upgrade to our gold package
for the full feature experience.
-
English Full professional proficiency
-
Spanish Native or bilingual proficiency
-
French Limited working proficiency
Topline Score
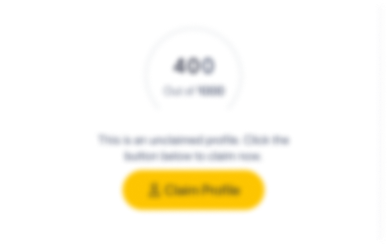
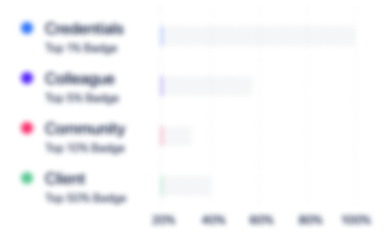
Bio


Experience
-
Invincible Boats
-
United States
-
Shipbuilding
-
1 - 100 Employee
-
Vice President Business Transformation
-
Jul 2020 - Present
Responsible for value creation driven by strategic and operational change across the organization. Design and implementation of innovative initiatives through process reengineering, development of technology and institution of cost reduction and resource optimization organizational philosophy. Particularly focused on supporting company's growth through cross functional scope, including various levels of the organization and multiple sites, Complex project management, long term… Show more Responsible for value creation driven by strategic and operational change across the organization. Design and implementation of innovative initiatives through process reengineering, development of technology and institution of cost reduction and resource optimization organizational philosophy. Particularly focused on supporting company's growth through cross functional scope, including various levels of the organization and multiple sites, Complex project management, long term plan creation and resources administration, based on identification of high impact opportunities at low cost execution in alignment with company vision. Culture enhancement and development focused on operational excellence, forming collaboration, effective communication and value capturing based on key performance indicators in accordance with overall company goals. Show less Responsible for value creation driven by strategic and operational change across the organization. Design and implementation of innovative initiatives through process reengineering, development of technology and institution of cost reduction and resource optimization organizational philosophy. Particularly focused on supporting company's growth through cross functional scope, including various levels of the organization and multiple sites, Complex project management, long term… Show more Responsible for value creation driven by strategic and operational change across the organization. Design and implementation of innovative initiatives through process reengineering, development of technology and institution of cost reduction and resource optimization organizational philosophy. Particularly focused on supporting company's growth through cross functional scope, including various levels of the organization and multiple sites, Complex project management, long term plan creation and resources administration, based on identification of high impact opportunities at low cost execution in alignment with company vision. Culture enhancement and development focused on operational excellence, forming collaboration, effective communication and value capturing based on key performance indicators in accordance with overall company goals. Show less
-
-
-
ICON Aircraft
-
United States
-
Aviation and Aerospace Component Manufacturing
-
100 - 200 Employee
-
Chief Of Staff to President
-
Jun 2019 - Jul 2020
*Direct support to President coordinating executive team, providing strategic counsel to leaders in the organization *Create and maintain cross departmental relationship to enable company and leadership success *Overseeing large, cross functional organization-wide projects
-
-
Senior Manufacturing and Engineering Manager
-
Oct 2018 - Jun 2019
*Manufacturing standardization across facilities, Manufacturing Engineering managers coaching and alignment *Bring design for manufacturability into Design Engineering. *Manage Capex budget (18.5 million USD) for tooling and equipment from composite to final assembly operations. *Model year 20 A5 implementation and Cost optimization project lead
-
-
Plant Manager
-
Jan 2018 - Oct 2018
* In charge a 700 employees composite manufacturing facility, 9 direct report managers * Support the organization creating process for the new composite operation in MX, plan and set up tooling and equipment to be used in a 300,000 sf facility. * People hiring and training, production ramp up and processes debugging. Show more * In charge a 700 employees composite manufacturing facility, 9 direct report managers * Support the organization creating process for the new composite operation in MX, plan and set up tooling and equipment to be used in a 300,000 sf facility. * People hiring and training, production ramp up and processes debugging.
-
-
Manufacturing and Engineering Manager
-
Jan 2016 - Jan 2018
*Manage and develop a mature ME team in two production sites (Vacaville,CA and Tijuana,BC), 19 employees. *Incorporate design engineering into production process, work instructions development, MBOM, engineering changes implementation process. *Influence the team creating continuous improvement culture, balancing review, problem solving methodology, tooling improvement program.
-
-
-
Faurecia
-
France
-
Motor Vehicle Manufacturing
-
700 & Above Employee
-
Acquisition Manufacturing Leader
-
Dec 2015 - Jan 2016
-
-
-
BRP
-
Canada
-
Manufacturing
-
700 & Above Employee
-
General Supervisor
-
May 2014 - Dec 2015
• Launch of the Moon Project (new product), in charge of 350 production operators and 7 production supervisors. • Plan and install 2 principal assembly conveyors and subassembly cells under the established manufacturing system. • Start up of second shift to fulfill demand achieving productivity, quality and safety targets, tracking KPIs for continuous improvement. • Plan for the next 4 years production, capacity increase and seasonal demand, ramp up and hiring plan. • Create… Show more • Launch of the Moon Project (new product), in charge of 350 production operators and 7 production supervisors. • Plan and install 2 principal assembly conveyors and subassembly cells under the established manufacturing system. • Start up of second shift to fulfill demand achieving productivity, quality and safety targets, tracking KPIs for continuous improvement. • Plan for the next 4 years production, capacity increase and seasonal demand, ramp up and hiring plan. • Create development plan for employees at different levels, Supervisors, Engineers and Team Leaders. • Strategic plan for cost reduction, scrap and crib material KPIs, improvement over 8 months
-
-
Production Supervisor
-
Feb 2014 - May 2014
• Launch of the Seadoo Spark 2014, in charge of 110 production operators, achieving productivity, quality and safety targets. • Reducing the Concerns Per Unit from 92% to 20%, continuous improvement with problem solving process. • Develop training plan for 110 operators more and 24 Team leaders total. • Plant reconstruction and set up for new product lunching with speed increase and more complexity, 190 Operators. • Coordinating 3 production supervisors, coaching them to develop… Show more • Launch of the Seadoo Spark 2014, in charge of 110 production operators, achieving productivity, quality and safety targets. • Reducing the Concerns Per Unit from 92% to 20%, continuous improvement with problem solving process. • Develop training plan for 110 operators more and 24 Team leaders total. • Plant reconstruction and set up for new product lunching with speed increase and more complexity, 190 Operators. • Coordinating 3 production supervisors, coaching them to develop skills to achieve the targets. • Creating links with support areas having a net focused on solving issues.
-
-
-
Ford Motor Company
-
United States
-
Motor Vehicle Manufacturing
-
700 & Above Employee
-
Manufacturing Engineer Final Assembly
-
Feb 2013 - Feb 2014
• Change management to be implemented in production without risk of affecting safety, quality and delivery. • Workloads using MODAPTS methodology trained and certified using this tool. • Linked engineering changes and costumer claims to production and get continuous improvement. • Implementation of error proofing systems (tools, pick lights, scanners) • Responsible of buyoff of new equipment, documenting by protag fulfilling safety, quality, delivery and cost… Show more • Change management to be implemented in production without risk of affecting safety, quality and delivery. • Workloads using MODAPTS methodology trained and certified using this tool. • Linked engineering changes and costumer claims to production and get continuous improvement. • Implementation of error proofing systems (tools, pick lights, scanners) • Responsible of buyoff of new equipment, documenting by protag fulfilling safety, quality, delivery and cost requirements. • Launching of 2014 and 2014.5 model of the new Ford Fiesta Planning for training, tooling and assembly process.
-
-
Process Coach Engineer
-
May 2011 - Feb 2013
• Coached trim process of the new fiesta since launching. • Managed 2 principal final assembly lines (Trim 1 and Trim 2) and 2 subassembly lines, Instrument Panel and doors line. • A total of 148 labor union technicians on the area per shift, divided in a total of 16 work teams. • Responsible for achieving Safety, Quality, Delivery and Cost goals • Reported to the top plant management • Developed and trained to put in place FPS (Ford Production System) strategy, set as a… Show more • Coached trim process of the new fiesta since launching. • Managed 2 principal final assembly lines (Trim 1 and Trim 2) and 2 subassembly lines, Instrument Panel and doors line. • A total of 148 labor union technicians on the area per shift, divided in a total of 16 work teams. • Responsible for achieving Safety, Quality, Delivery and Cost goals • Reported to the top plant management • Developed and trained to put in place FPS (Ford Production System) strategy, set as a global standard • Improved quality from 33R/1000 to 21R/1000 • Achieved 90% efficiency on the production line with a continuous improvement system, first Ford plant that reach this efficiency
-
-
-
SEGLO Logistics / Schnellecke Logistics
-
Mexico
-
Truck Transportation
-
500 - 600 Employee
-
Material Planning and Logistics
-
Nov 2009 - Apr 2011
• Planed and launched the material sequencing strategy for the new fiesta at Cuatitlan plant • Set the requirements for manpower, facilities and systems • Developed the Sequencing and Kitting System (SKS) that after became standard for all North America Ford Plants • Made Cuautitlan the plant with the highest level of material sequencing in plant with a total of 823 parts out of 1133 • Part of the launching team for new models, responsible for parts engineering changes supplied… Show more • Planed and launched the material sequencing strategy for the new fiesta at Cuatitlan plant • Set the requirements for manpower, facilities and systems • Developed the Sequencing and Kitting System (SKS) that after became standard for all North America Ford Plants • Made Cuautitlan the plant with the highest level of material sequencing in plant with a total of 823 parts out of 1133 • Part of the launching team for new models, responsible for parts engineering changes supplied to the line Show less • Planed and launched the material sequencing strategy for the new fiesta at Cuatitlan plant • Set the requirements for manpower, facilities and systems • Developed the Sequencing and Kitting System (SKS) that after became standard for all North America Ford Plants • Made Cuautitlan the plant with the highest level of material sequencing in plant with a total of 823 parts out of 1133 • Part of the launching team for new models, responsible for parts engineering changes supplied… Show more • Planed and launched the material sequencing strategy for the new fiesta at Cuatitlan plant • Set the requirements for manpower, facilities and systems • Developed the Sequencing and Kitting System (SKS) that after became standard for all North America Ford Plants • Made Cuautitlan the plant with the highest level of material sequencing in plant with a total of 823 parts out of 1133 • Part of the launching team for new models, responsible for parts engineering changes supplied to the line Show less
-
-
-
LUGARTH S.A. de C.V.
-
Pachuca Hidalgo
-
Junior Production Supervisor
-
Jul 2007 - Oct 2009
• Production control of the entire manufacturing process of metal mechanical products for material handling • Material requirements and production scheduling • Participated on winning bids for PEMEX (Petróleos Mexicanos), Airports and for the Mexican Army • Linked Lugarth and a Canadian Company on a project to produce trash compactors in Mexico with the Canadian brand • Production control of the entire manufacturing process of metal mechanical products for material handling • Material requirements and production scheduling • Participated on winning bids for PEMEX (Petróleos Mexicanos), Airports and for the Mexican Army • Linked Lugarth and a Canadian Company on a project to produce trash compactors in Mexico with the Canadian brand
-
-
Education
-
Stanford University Graduate School of Business
Graduate School of Business, Stanford LEAD Professional Certificate -
Thunderbird School of Global Management
Master of Business Administration (MBA), Global Master Business Administration for Latin American Managers -
TECNOL��GICO DE MONTERREY
Bachelor's degree, Bachelor of Industrial Engineer and Systems (IIS)
Community
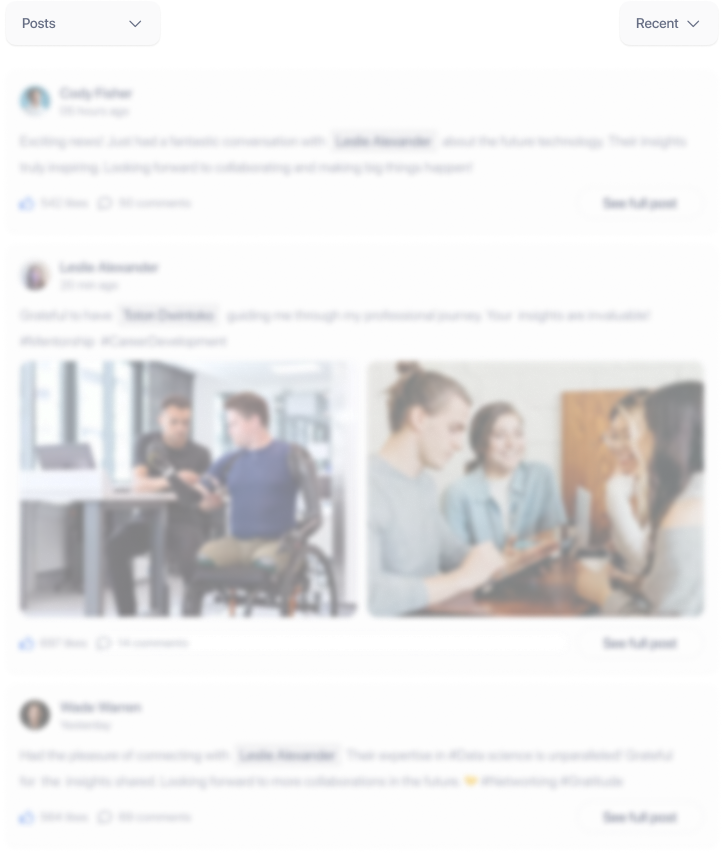