Ed Milford III, MSML CMPIC
Logistician V at Command Decisions Systems and Solutions (CDS2)- Claim this Profile
Click to upgrade to our gold package
for the full feature experience.
Topline Score
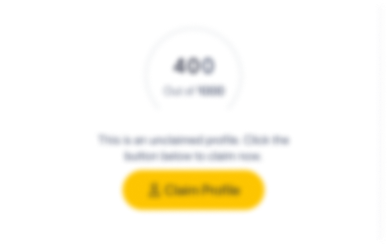
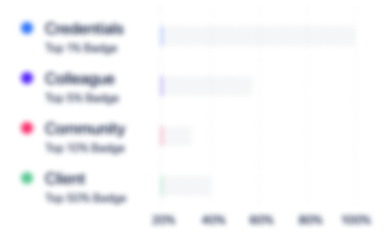
Bio

Richard Washington
Highly motivated individual

Richard Washington
Hire this man, thank me later.

Richard Washington
Highly motivated individual

Richard Washington
Hire this man, thank me later.

Richard Washington
Highly motivated individual

Richard Washington
Hire this man, thank me later.

Richard Washington
Highly motivated individual

Richard Washington
Hire this man, thank me later.

Experience
-
Command Decisions Systems and Solutions (CDS2)
-
United States
-
IT Services and IT Consulting
-
1 - 100 Employee
-
Logistician V
-
Jan 2016 - Present
Responsible for writing and implementing a comprehensive and detailed Life Cycle Support Plan for a critical and highly visible program. Applied experience in Reliability, Availability, and Maintainability (RAM), Mean Time Between Failures (MTBF), and Failure Rate Analysis using a manual and automated analytical tool, RAPTOR. • Assist with material management, which included receiving, managing material inventory, issuing material, and warranty tracking (CDRL A011 & A012). • Procure materials for successful integration of cables, connectors, hardware, brackets per design. • Conduct market research for cost estimate supporting procurements. • Assist with warranty repair processing and update all failures in a monthly RMA report. • Record and analyze applicable data into a warranty matric and Failure Reporting, Analysis and Corrective Action System (FRACAS). • Input, update, and manage the items in CMPro (part numbers, serial numbers, documents, drawings, software configuration, parts list, and Build of Material (BOM)). • Verify part numbers and sources of supply in engineering drawing package. • Complete DD-1149 forms for the transfer of materials. • Conduct monthly CMPro audits to ensure integrity of data entered in CMPro. • Revise and maintain a comprehensive and detailed Life-Cycle Support Plan. Show less
-
-
-
Skylla Engineering
-
United States
-
Defense and Space Manufacturing
-
100 - 200 Employee
-
Configuration Management Analyst I
-
Sep 2014 - Jan 2016
Responsible for establishing, documenting, adhering to, improving and communicating Configuration Management processes for software, hardware and related systems. Also responsible for monitoring Configuration Management processes across the product life cycle. Worked with project management to ensure the Configuration Management processes are implemented and followed by all project team members. Major responsibilities: • Monitor processes and procedures to guard against breakdowns in the Configuration Management project lifecycle. • Interface with and brief project management to maintain visibility of project configuration status. • Maintain Configuration Management database (CMPRO) and ensure proper Configuration Management methods are applied to all project documentation. • Research, Write, Evaluate and Implement plans, charters, and process documents for Configuration Management. • Maintain the change control process and baselines. • Participate in Local Configuration Control Boards (LCRB) and support Configuration Control Boards (CCB) for projects. • Produce reports indicating status of configuration items and communicate to team members. • Conduct Configuration Management project audits. • Analyze processes and schedules and identify areas of risk or conflict. • Participate in periodic audits and reviews and communicates results to management. • Manage software builds and changes to build lists and releases for project. Show less
-
-
-
Centurum
-
United States
-
Defense & Space
-
100 - 200 Employee
-
Logistics and Configuration Manager
-
Mar 2011 - May 2014
Work with key project stakeholders to formulate and communicate business requirements and scope of project. Work with project stakeholders to translate their requirements into specifications technical staff can understand and also translate questions that technical staff has into a format the stakeholders can understand. Work with stakeholders to validate their requirements. Write use cases as part of the requirements document. Unit tests upon development to ensure requirements have been met. Identify potential areas of automation and aid in re-engineering the underlying business processes. Responsible for coordination of production turnover of all configuration work upon user sign off. Work with business areas to understand and implement all contract configurations and benefit configurations. Coordinate multiple simultaneous projects and initiatives. As required, facilitates and leads meetings and selected workgroups. • Issue transfer work orders to aid the technicians. • Create DD1149s and work orders to transfer, DRMO, or ship complete systems. • Assist with inventory of systems. • Upload Documents and associate Platform, ECR, ECO, System/Subsystem, Shipalts, and other documents to CMPro. o Fleet Advisory Messages (FAM). o Mandatory System Updates (MSU) o Ship Check Guides o RMMCO Install Completion Sheet o Liaison Action Records (LAR) o Reverse Liaison Action Records (RLAR) o Ship Configuration Drawings (SCD) • Upload Drawings and associate Platform, ECR, ECO, System/Subsystem, Shipalts, and other documents to CMPro. • Aide in Physical Configuration Audit (PCA). • Assist in the Engineer Change Requests (ECR). • Assist in the Engineer Change Orders (ECO). • Revise the Configuration Management Plan (CMP). • Create records for Software Repository. • Create Part Trees/PDM. • Create As-Built Baselines. • Order, procure, and track spares for RED Falcon • Provisioning in ICAPS Show less
-
-
-
SAIC
-
United States
-
IT Services and IT Consulting
-
700 & Above Employee
-
Logistician III
-
Dec 2006 - Mar 2011
Provide a full spectrum of logistics support for planning, Integrated Logistics Support (ILS) development and life-cycle planning in support of SPAWAR C4I/COMSEC systems. Responsibilities include analyzing system acquisition requirements and budgets, as well as performing cost analysis and control. Develop and maintain all necessary documentation in support of selected projects for cradle to grave Life-Cycle support. Access information from lab, maintains regular interaction with clients, and attends weekly meetings conducted by the client. Participate in Integrated Product Teams program reviews and logistics support meetings. Developed a better spreadsheet that was more in depth to track all TacMobile’s spares. Provide Spares market research for all of TacMobile’s platforms. Purchaser of all TacMobile Spares. Responsible for all Spares and integration data front loaded into CMPro for TacMobile including SAIC and ManTech’s purchase request. Research every part number to ensure the correct information is enter into CMPro by manufacture number and link them to the retailer part number to ensure an accurate count in inventory. Issue transfer work orders to aid the technicians. Researched and tracked GPETE for all of TacMobile’s platforms. Coordinate all logistics entering and exiting the secured area know as the Swing Space, aide technicians in locating, transferring, ordering, and issuing parts to DRMO or sites. Create DD1149s and work orders to transfer or ship complete systems. Assist with inventory of systems and CDMD-OA research. Interact with logistic program manager for special projects. Show less
-
-
-
EG&G Technical Services (now part of URS Corporation)
-
Defense and Space Manufacturing
-
200 - 300 Employee
-
SARSS Operator
-
Dec 2005 - Aug 2006
Provide full logistic support per the clients’ standard operating procedures while “in theater.” Provided guidance and performed of all inventory research for unmarked/defective material requiring identification, as well as supply inspection/examination procedures for materials. Mastered all work areas of receiving, storage, turn-Ins, issue, stock control and client requirements. Completed start-up, back-up, and close out, along with Transin, Process, and Tranout every hour to keep our information in the system current (SARSS). Processed ISS’s with a diskette and keyed them in manually and supported the Customer Issue Section. Coached, trained and supported new employees and cross trained any employee who qualified and assigned in stock control and customer issue section. Conducted shelf life and COSIS actions as necessary and conduct material coordination duties for special programs as required. Provided cost estimates for preparation of kits, and provided daily work assignment to other personnel assigned to work center. Show less
-
-
Education
-
Webster University
Master of Arts (M.A.), Management and Leadership -
South Carolina State University
Bachelor of Science (BS), Business, Management, Marketing, and Related Support Services
Community
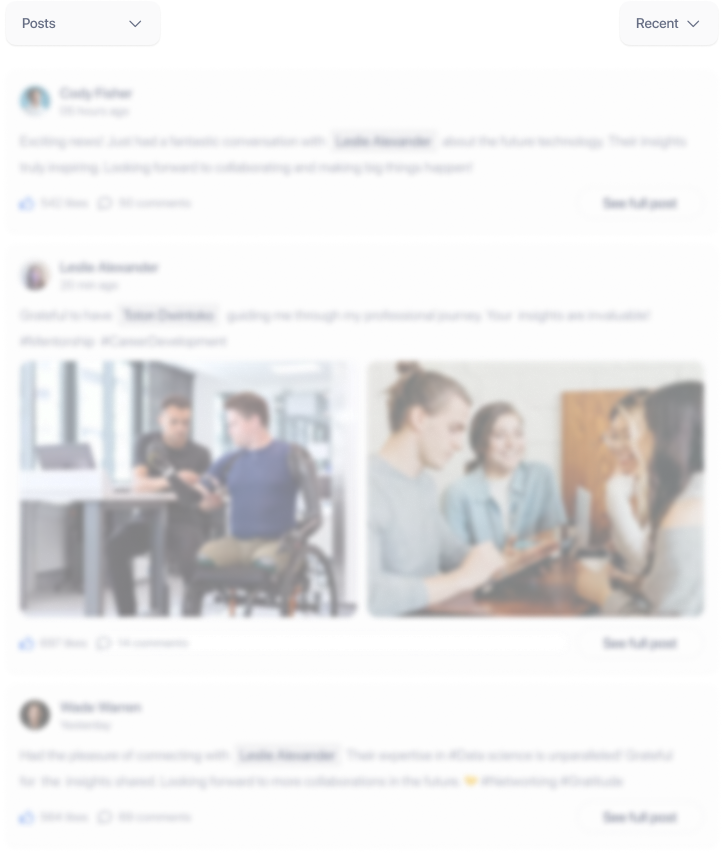