
Dustin Hird
Production Manager (Group Leader) at The HON Company- Claim this Profile
Click to upgrade to our gold package
for the full feature experience.
Topline Score
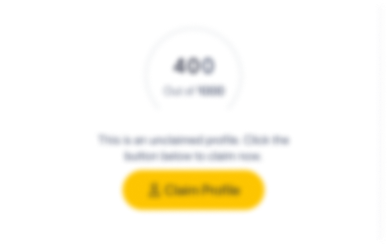
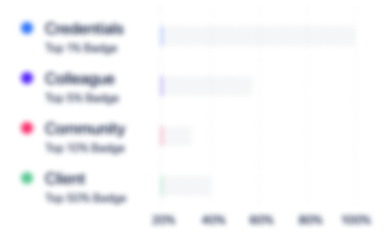
Bio

John Hannon, CSP
Dustin always went above and beyond to play his role in the safety management system. There was never an attitude indicating

Scott Stout
Dustin is a great manager, who makes time for his employees and is very good with time management, delegation and fosters a culture of team work.

John Hannon, CSP
Dustin always went above and beyond to play his role in the safety management system. There was never an attitude indicating

Scott Stout
Dustin is a great manager, who makes time for his employees and is very good with time management, delegation and fosters a culture of team work.

John Hannon, CSP
Dustin always went above and beyond to play his role in the safety management system. There was never an attitude indicating

Scott Stout
Dustin is a great manager, who makes time for his employees and is very good with time management, delegation and fosters a culture of team work.

John Hannon, CSP
Dustin always went above and beyond to play his role in the safety management system. There was never an attitude indicating

Scott Stout
Dustin is a great manager, who makes time for his employees and is very good with time management, delegation and fosters a culture of team work.

Credentials
-
Body Language for Leaders
LinkedInFeb, 2018- Nov, 2024 -
Employee Engagement
LinkedInFeb, 2018- Nov, 2024 -
Lean Foundations
LinkedInFeb, 2018- Nov, 2024 -
Operations Management Foundations
LinkedInFeb, 2018- Nov, 2024 -
Process Improvement Foundations
LinkedInFeb, 2018- Nov, 2024 -
Strategic Thinking
LinkedInFeb, 2018- Nov, 2024
Experience
-
The HON Company
-
United States
-
Furniture and Home Furnishings Manufacturing
-
300 - 400 Employee
-
Production Manager (Group Leader)
-
Apr 2018 - Present
As an Group Leader at HON Oak Laminate I am responsible for daily operations of the Fabrication Factory. I am over four team leaders and 40 hourly members. I am responsible for daily fabrication of material (pressed laminate wood) for the final assembly process. I investigate, analyze and resolve various system, part, and people issues to correct deficiencies, reduce costs, improve processes/performance using root cause analysis and problem solving skills. I drive my team to meet daily, monthly and quarterly performance metrics including safety, quality, efficiency and cost goals. I provide daily leadership to my team including administering company policies and procedures. I lead and develop my team through conducting performance evaluations and providing performance feedback, conducting interviews and managing staffing for specific area. I review production capacities within the department to manage, impact, and improve processes. I coach members on issues, provide conflict resolution and productive team management. I coordinate vacation schedules, perform accurate member record keeping in relation to time keeping (Kronos), attendance, performance, safety and quality. I review engineering prints and make sure parts are being produced to most updated prints. I make sure production equipment has data to be able to operate.
-
-
-
Walmart
-
United States
-
Retail
-
700 & Above Employee
-
Assistant Manager
-
May 2015 - Apr 2018
As an Assistant Manager at Wal-Mart I managed day to day operations of the store. I was directly responsible for 30 associates on three different shifts. On any given day I supervised 100 plus associates. My day was spent following up on associates to make sure they were following company issued policies and processes to ensure proper in-stock of merchandise to help drive sales. I followed up with associates by conducting performance evaluations including verbal and written coaching regarding disciplinary action. I made sure we got the best talent by Interviewing job candidates and hiring the best for the job. I was also responsible for ensuring my facility was in compliance with all federal and state specific laws and regulations. With my fellow Assistant Managers I helped manage day to day freight flow and helped strategically plan merchandise displays and merchandise sets for the different seasons. When customers have questions or concerns, I gave great customer service so they have a great shopping experience and want to come back in the future.
-
-
-
Hy-Vee, Inc.
-
Retail
-
700 & Above Employee
-
Assistant Manager
-
Oct 2011 - May 2015
After working for Hy-Vee for five years, I was promoted to Assistant Manager. As an Assistant Manager at Hy-Vee, I worked with a team of Assistant Managers to ensure proper in stock of merchandise, delegate tasks to employees, and provide a fast, clean, and safe shopping experience to customers. I would help out in the areas of the store that needed the most help and my job would change day to day based on what was going on. Most days I would be in charge of front end operations and ensure steady flow of customers through the check out lanes. On any given day I would be directly responsible for 10 to 15 employees. Other days I would be in charge of backroom operations, which involves backroom organization of merchandise, coordinating merchandise shipments and overall backroom cleanliness.
-
-
Education
-
Iowa Wesleyan University
Bachelor’s Degree, Business Administration, Management and Operations -
Southeastern Community College
Associate's Degree, General Studies
Community
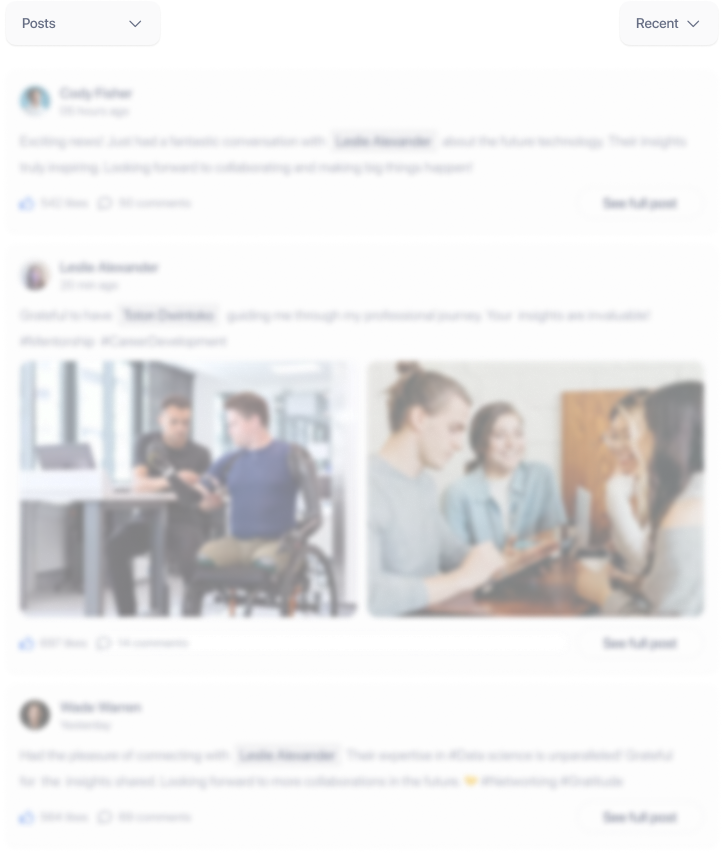