Drew Dunderman
Systems Engineer I at RoviSys Building Technologies- Claim this Profile
Click to upgrade to our gold package
for the full feature experience.
Topline Score
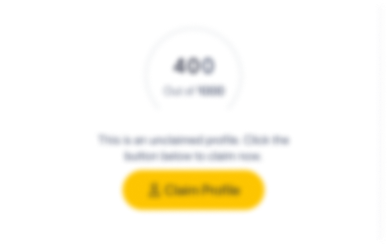
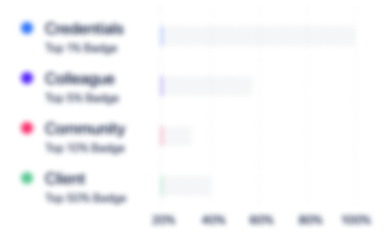
Bio


Experience
-
RoviSys Building Technologies
-
United States
-
Facilities Services
-
100 - 200 Employee
-
Systems Engineer I
-
Sep 2022 - Present
-
-
-
PepsiCo
-
United States
-
Food and Beverage Services
-
700 & Above Employee
-
Supply Chain Associate (Gatorade Division)
-
Jul 2021 - Present
• Currently providing supervisory leadership to two night-shift production line teams, prioritizing safety and quality standards as well as operator development to maximize production outputs; collaborating with cross-functional teams to investigate and resolve root causes of downtime issues • Managed a water conservation project involving sanitation requirements for process tanks on two production lines, yielding an estimated annual water savings of… Show more • Currently providing supervisory leadership to two night-shift production line teams, prioritizing safety and quality standards as well as operator development to maximize production outputs; collaborating with cross-functional teams to investigate and resolve root causes of downtime issues • Managed a water conservation project involving sanitation requirements for process tanks on two production lines, yielding an estimated annual water savings of 641,000 gallons o Lean Six Sigma (LSS) Yellow Belt (Kaizen) certification project, assisting with plant-wide re- application to four other production lines • Planned and gathered resources for an operator monitoring system for filler valves incorrectly filling, with the goal of lowering yield loss below its periodic target of 6% Show less • Currently providing supervisory leadership to two night-shift production line teams, prioritizing safety and quality standards as well as operator development to maximize production outputs; collaborating with cross-functional teams to investigate and resolve root causes of downtime issues • Managed a water conservation project involving sanitation requirements for process tanks on two production lines, yielding an estimated annual water savings of… Show more • Currently providing supervisory leadership to two night-shift production line teams, prioritizing safety and quality standards as well as operator development to maximize production outputs; collaborating with cross-functional teams to investigate and resolve root causes of downtime issues • Managed a water conservation project involving sanitation requirements for process tanks on two production lines, yielding an estimated annual water savings of 641,000 gallons o Lean Six Sigma (LSS) Yellow Belt (Kaizen) certification project, assisting with plant-wide re- application to four other production lines • Planned and gathered resources for an operator monitoring system for filler valves incorrectly filling, with the goal of lowering yield loss below its periodic target of 6% Show less
-
-
-
Marathon Petroleum Corporation
-
Oil and Gas
-
700 & Above Employee
-
Refining Operations Research Engineer
-
Jun 2020 - Aug 2020
• Analyzed and resolved mass balance closure rate from 108% to 101% for a butamer unit in its respective Unit Performance Monitor (UPM) model (acceptable closure rate ranges are from 98% - 102%) • Implemented a diesel mode mass balance analysis for a hydrotreater unit in its respective UPM model. Allowed for automated transfer between diesel mode and gas oil mode, based on what the unit was currently running in real time. Resolved the average… Show more • Analyzed and resolved mass balance closure rate from 108% to 101% for a butamer unit in its respective Unit Performance Monitor (UPM) model (acceptable closure rate ranges are from 98% - 102%) • Implemented a diesel mode mass balance analysis for a hydrotreater unit in its respective UPM model. Allowed for automated transfer between diesel mode and gas oil mode, based on what the unit was currently running in real time. Resolved the average mass balance closure rate from 11% to 100% • Developed a PI Asset Framework element structure for exporting production data to a hydrotreater catalyst vendor, including potential catalyst change alerts to ensure data confidentiality Show less • Analyzed and resolved mass balance closure rate from 108% to 101% for a butamer unit in its respective Unit Performance Monitor (UPM) model (acceptable closure rate ranges are from 98% - 102%) • Implemented a diesel mode mass balance analysis for a hydrotreater unit in its respective UPM model. Allowed for automated transfer between diesel mode and gas oil mode, based on what the unit was currently running in real time. Resolved the average… Show more • Analyzed and resolved mass balance closure rate from 108% to 101% for a butamer unit in its respective Unit Performance Monitor (UPM) model (acceptable closure rate ranges are from 98% - 102%) • Implemented a diesel mode mass balance analysis for a hydrotreater unit in its respective UPM model. Allowed for automated transfer between diesel mode and gas oil mode, based on what the unit was currently running in real time. Resolved the average mass balance closure rate from 11% to 100% • Developed a PI Asset Framework element structure for exporting production data to a hydrotreater catalyst vendor, including potential catalyst change alerts to ensure data confidentiality Show less
-
-
-
Marathon Petroleum Corporation
-
Oil and Gas
-
700 & Above Employee
-
Technical Services Engineer
-
Aug 2019 - Dec 2019
• Designed a slurry flow reduction strategy for the fluid catalytic cracking fractionator, with an annual target value of $803,000 in increased light cycle oil output • Analyzed the alleviation of hydraulic constraints for light cycle oil rundown, with an annual target value of $5,840,000 in optimized light cycle oil output • Designed a slurry flow reduction strategy for the fluid catalytic cracking fractionator, with an annual target value of $803,000 in increased light cycle oil output • Analyzed the alleviation of hydraulic constraints for light cycle oil rundown, with an annual target value of $5,840,000 in optimized light cycle oil output
-
-
-
Braskem America
-
United States
-
Plastics Manufacturing
-
200 - 300 Employee
-
Process Engineer
-
May 2019 - Aug 2019
• Implemented mechanical, electrical, and thermal designs of ANSI approved safety shower • Designed and implemented trolly-and-chain lid removal system for continuous blender maintenance • Consolidated Process Hazard Review (PHA) action items from all company reports into an overall location • Implemented mechanical, electrical, and thermal designs of ANSI approved safety shower • Designed and implemented trolly-and-chain lid removal system for continuous blender maintenance • Consolidated Process Hazard Review (PHA) action items from all company reports into an overall location
-
-
-
Buckeye Food Alliance
-
United States
-
Civic and Social Organizations
-
1 - 100 Employee
-
President of the Executive Board and Advisory Board Chairman
-
May 2017 - May 2019
• Oversaw Executive Board and organization operations, coordinated projects contributing to BFA’s growth • Established relations with donors, securing ~$300,000 during time as President • Led negotiations with St. Stevens Episcopal Church to open a satellite pantry in their space • Strategized BFA short-term and long-term developments with Ohio State alumni-based Advisory Board • Oversaw Executive Board and organization operations, coordinated projects contributing to BFA’s growth • Established relations with donors, securing ~$300,000 during time as President • Led negotiations with St. Stevens Episcopal Church to open a satellite pantry in their space • Strategized BFA short-term and long-term developments with Ohio State alumni-based Advisory Board
-
-
-
Cremer North America, LP
-
United States
-
Chemical Manufacturing
-
1 - 100 Employee
-
Process Engineer
-
May 2018 - Aug 2018
• Managed implementation of product cooling belt modifications yielding an estimated annual product savings of $216,000 • Input and used daily production data to run analyses for troubleshooting and deviation reports • Managed implementation of product cooling belt modifications yielding an estimated annual product savings of $216,000 • Input and used daily production data to run analyses for troubleshooting and deviation reports
-
-
Education
-
The Ohio State University
Bachelor of Science - BS, Chemical Engineering
Community
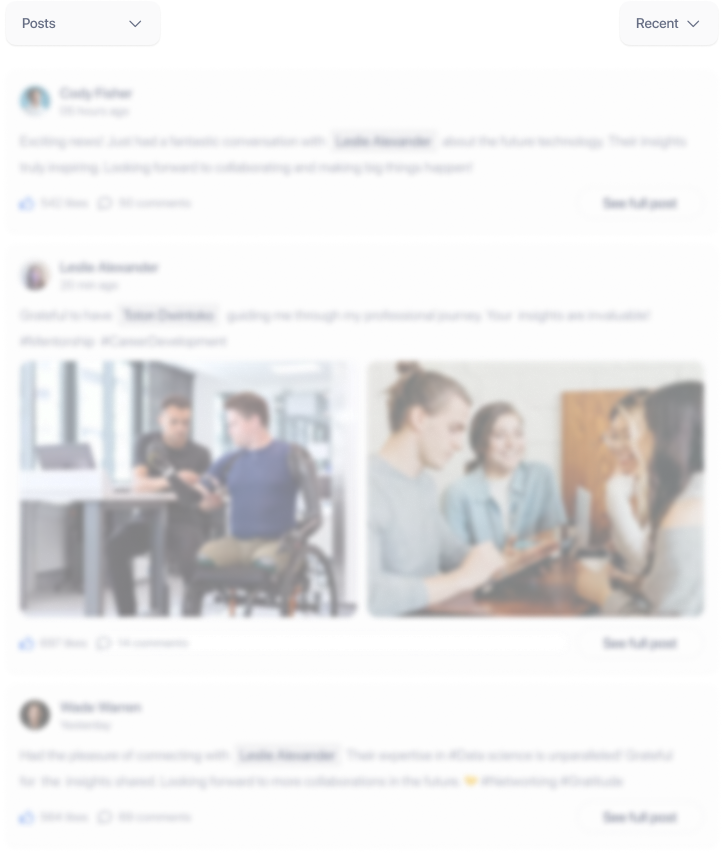