Douglas Miller
Operations Manager at William Barnet and Son, LLC- Claim this Profile
Click to upgrade to our gold package
for the full feature experience.
Topline Score
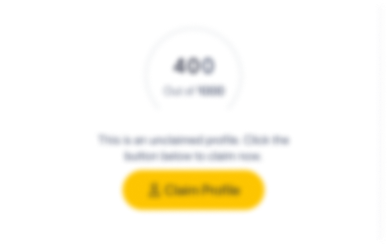
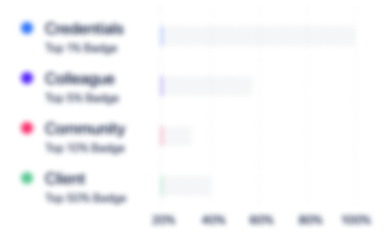
Bio

Jeff Stone
Douglas is an intelligent, high-energy leader with an enthusiasm that is contagious to anyone who has the pleasure of working with, or for him. His deep understanding of plant operations brought significant improvements to our company. He's truly a pleasure to work for. I would highly recommend Douglas to anyone.

Dave Harold
Working with Douglas since his tenure has been an absolute pleasure. His knowledge of production environments has help implement many of our key improvements.He is a true leader amongst men, being able to manage a rag tag bunch and turn us into a fine tuned line with true potential was fear unto itself. His mentoring qualities came at a critical time, where a lot of self doubt was evident in my life which was appreciated.Douglas has led with a true direction in his plan of attack.He was tough yet fair and would recommend him as an asset to any company that wants to surround themselves with the best talent available. Thank you Dave Harold Oven Supervisor at Kraus flooring

Jeff Stone
Douglas is an intelligent, high-energy leader with an enthusiasm that is contagious to anyone who has the pleasure of working with, or for him. His deep understanding of plant operations brought significant improvements to our company. He's truly a pleasure to work for. I would highly recommend Douglas to anyone.

Dave Harold
Working with Douglas since his tenure has been an absolute pleasure. His knowledge of production environments has help implement many of our key improvements.He is a true leader amongst men, being able to manage a rag tag bunch and turn us into a fine tuned line with true potential was fear unto itself. His mentoring qualities came at a critical time, where a lot of self doubt was evident in my life which was appreciated.Douglas has led with a true direction in his plan of attack.He was tough yet fair and would recommend him as an asset to any company that wants to surround themselves with the best talent available. Thank you Dave Harold Oven Supervisor at Kraus flooring

Jeff Stone
Douglas is an intelligent, high-energy leader with an enthusiasm that is contagious to anyone who has the pleasure of working with, or for him. His deep understanding of plant operations brought significant improvements to our company. He's truly a pleasure to work for. I would highly recommend Douglas to anyone.

Dave Harold
Working with Douglas since his tenure has been an absolute pleasure. His knowledge of production environments has help implement many of our key improvements.He is a true leader amongst men, being able to manage a rag tag bunch and turn us into a fine tuned line with true potential was fear unto itself. His mentoring qualities came at a critical time, where a lot of self doubt was evident in my life which was appreciated.Douglas has led with a true direction in his plan of attack.He was tough yet fair and would recommend him as an asset to any company that wants to surround themselves with the best talent available. Thank you Dave Harold Oven Supervisor at Kraus flooring

Jeff Stone
Douglas is an intelligent, high-energy leader with an enthusiasm that is contagious to anyone who has the pleasure of working with, or for him. His deep understanding of plant operations brought significant improvements to our company. He's truly a pleasure to work for. I would highly recommend Douglas to anyone.

Dave Harold
Working with Douglas since his tenure has been an absolute pleasure. His knowledge of production environments has help implement many of our key improvements.He is a true leader amongst men, being able to manage a rag tag bunch and turn us into a fine tuned line with true potential was fear unto itself. His mentoring qualities came at a critical time, where a lot of self doubt was evident in my life which was appreciated.Douglas has led with a true direction in his plan of attack.He was tough yet fair and would recommend him as an asset to any company that wants to surround themselves with the best talent available. Thank you Dave Harold Oven Supervisor at Kraus flooring

Experience
-
William Barnet and Son, LLC
-
United States
-
Textile Manufacturing
-
1 - 100 Employee
-
Operations Manager
-
Mar 2022 - Present
-
-
-
Guilford Textiles, Lear Corporation
-
Kenansville, NC
-
Operations Manager
-
Jun 2021 - Jan 2022
Led the Guilford manufacturing team during the post COVID labor and materials challenges. Worked to reestablish a stable work force and, with the materials team, juggled production schedules around various materials shortages and demand fluctuations while continuing to meet the needs of our customers. Led the Guilford manufacturing team during the post COVID labor and materials challenges. Worked to reestablish a stable work force and, with the materials team, juggled production schedules around various materials shortages and demand fluctuations while continuing to meet the needs of our customers.
-
-
-
Textile Management Associates
-
Textile Manufacturing
-
1 - 100 Employee
-
Research And Development Manager
-
Feb 2020 - May 2021
-
-
-
CTS Corporation
-
Manufacturing
-
700 & Above Employee
-
Plant Manager
-
Nov 2018 - Oct 2019
Responsible for the site cost, staffing, performance, quality, and profitability, full P&L responsibility. CTS specializes in designing and producing piezo ceramics and ceramic RF filters for civilian and military applications. Operation is all custom parts in both high and low volume production cells. The site maintains a workforce of 200 Direct labor employees and 100 indirect employees including engineers, supervisory and corporate personnel. • Lead plant through materials and economic… Show more Responsible for the site cost, staffing, performance, quality, and profitability, full P&L responsibility. CTS specializes in designing and producing piezo ceramics and ceramic RF filters for civilian and military applications. Operation is all custom parts in both high and low volume production cells. The site maintains a workforce of 200 Direct labor employees and 100 indirect employees including engineers, supervisory and corporate personnel. • Lead plant through materials and economic crisis, improving the gross margins by 25 points, through cost improvements, Negotiations with suppliers, and strategic cost management. Approximately a $750K monthly swing. • Improved yields by approximately $250K annually. • Improved the safety rates by 70% with 0 lost time accidents during my tenure and reducing Osha recordables to two during 2019. • Implemented a plan to improve OTJ that includes practical and online testing to insure employee certification to multiple functions. • Hired or replaced Quality manger, Manufacturing manager, Buyer, Materials manager, 3 supervisors, and an HR manager Show less Responsible for the site cost, staffing, performance, quality, and profitability, full P&L responsibility. CTS specializes in designing and producing piezo ceramics and ceramic RF filters for civilian and military applications. Operation is all custom parts in both high and low volume production cells. The site maintains a workforce of 200 Direct labor employees and 100 indirect employees including engineers, supervisory and corporate personnel. • Lead plant through materials and economic… Show more Responsible for the site cost, staffing, performance, quality, and profitability, full P&L responsibility. CTS specializes in designing and producing piezo ceramics and ceramic RF filters for civilian and military applications. Operation is all custom parts in both high and low volume production cells. The site maintains a workforce of 200 Direct labor employees and 100 indirect employees including engineers, supervisory and corporate personnel. • Lead plant through materials and economic crisis, improving the gross margins by 25 points, through cost improvements, Negotiations with suppliers, and strategic cost management. Approximately a $750K monthly swing. • Improved yields by approximately $250K annually. • Improved the safety rates by 70% with 0 lost time accidents during my tenure and reducing Osha recordables to two during 2019. • Implemented a plan to improve OTJ that includes practical and online testing to insure employee certification to multiple functions. • Hired or replaced Quality manger, Manufacturing manager, Buyer, Materials manager, 3 supervisors, and an HR manager Show less
-
-
-
Kraus Flooring
-
Waterloo, Ontario, Canada
-
Manager Operations
-
Apr 2013 - Oct 2018
Responsible for all cost, performance, quality, and functioning of warehousing distribution operations for Kraus Manufacturing in Waterloo, Canada. Canadian operations include yarn processing, tufting, dyeing, finishing, warehouse and distribution operations. Operation has over 200 union employees with two distinct bargaining units and 25 salaried managers. Establish lean type CAPEX projects with financial paybacks to upgrade old equipment in all manufacturing areas and infrastructure to… Show more Responsible for all cost, performance, quality, and functioning of warehousing distribution operations for Kraus Manufacturing in Waterloo, Canada. Canadian operations include yarn processing, tufting, dyeing, finishing, warehouse and distribution operations. Operation has over 200 union employees with two distinct bargaining units and 25 salaried managers. Establish lean type CAPEX projects with financial paybacks to upgrade old equipment in all manufacturing areas and infrastructure to improve Costs, throughput, quality, and legal requirements. Reduced beck re-dyes from 4 per week to 4 per year. Dye operation went from 20% first-time pass to 90% first-time pass. Increased dye house capacity by 50+% while reducing department off quality from 0.75% to 0.2%. Reduced Coating off quality from 0.75% in 2014 to .011% in 2017. Completed Six Sigma project increasing tuftbind and delamination properties and consistency while lowering the overall materials cost and increasing throughput for the finishing operation. Created and quoted a plan to reestablish manufacturing operations from Canada to Dalton GA. Took the manufacturing interruptions into account and developed suppliers to cover those until manufacturing was back on line. Developed relationships with key city and state agencies to take advantage of grants to aid the relocation. Led Six-Sigma Teams to address the top quality issues. Reduced Off Quality production from approximately 3% in 2012 to under 0.5% in 2017. After Kraus was acquired by an investment firm, the new owners placed me over the corporate variable cost reductions focusing on quality, waste, raw materials, labor, and utilization efficiency. Led Waste reduction effort that has reduced overall plant waste by over $500,000, annualized. Show less Responsible for all cost, performance, quality, and functioning of warehousing distribution operations for Kraus Manufacturing in Waterloo, Canada. Canadian operations include yarn processing, tufting, dyeing, finishing, warehouse and distribution operations. Operation has over 200 union employees with two distinct bargaining units and 25 salaried managers. Establish lean type CAPEX projects with financial paybacks to upgrade old equipment in all manufacturing areas and infrastructure to… Show more Responsible for all cost, performance, quality, and functioning of warehousing distribution operations for Kraus Manufacturing in Waterloo, Canada. Canadian operations include yarn processing, tufting, dyeing, finishing, warehouse and distribution operations. Operation has over 200 union employees with two distinct bargaining units and 25 salaried managers. Establish lean type CAPEX projects with financial paybacks to upgrade old equipment in all manufacturing areas and infrastructure to improve Costs, throughput, quality, and legal requirements. Reduced beck re-dyes from 4 per week to 4 per year. Dye operation went from 20% first-time pass to 90% first-time pass. Increased dye house capacity by 50+% while reducing department off quality from 0.75% to 0.2%. Reduced Coating off quality from 0.75% in 2014 to .011% in 2017. Completed Six Sigma project increasing tuftbind and delamination properties and consistency while lowering the overall materials cost and increasing throughput for the finishing operation. Created and quoted a plan to reestablish manufacturing operations from Canada to Dalton GA. Took the manufacturing interruptions into account and developed suppliers to cover those until manufacturing was back on line. Developed relationships with key city and state agencies to take advantage of grants to aid the relocation. Led Six-Sigma Teams to address the top quality issues. Reduced Off Quality production from approximately 3% in 2012 to under 0.5% in 2017. After Kraus was acquired by an investment firm, the new owners placed me over the corporate variable cost reductions focusing on quality, waste, raw materials, labor, and utilization efficiency. Led Waste reduction effort that has reduced overall plant waste by over $500,000, annualized. Show less
-
-
-
Kraus Flooring
-
United States
-
Wholesale Building Materials
-
100 - 200 Employee
-
Site Manager
-
Sep 2011 - Apr 2013
Responsible for distribution and manufacturing operations for the Kraus Flooring Dalton facility. Managed the manufacture and distribution of sample displays oversite of international shipping from the Dalton facility. Simultaneously established and led the process improvement teams in Waterloo, Ontario. Organized training and consulted with our Waterloo production operation to improve quality and throughput. Shared best manufacturing practices between the US and Canadian… Show more Responsible for distribution and manufacturing operations for the Kraus Flooring Dalton facility. Managed the manufacture and distribution of sample displays oversite of international shipping from the Dalton facility. Simultaneously established and led the process improvement teams in Waterloo, Ontario. Organized training and consulted with our Waterloo production operation to improve quality and throughput. Shared best manufacturing practices between the US and Canadian manufacturing centers to raise our quality and improve Kraus Flooring’s competitive position in the industry. Regularly flew between Ontario and Georgia to lead the process improvement process in Canada. Show less Responsible for distribution and manufacturing operations for the Kraus Flooring Dalton facility. Managed the manufacture and distribution of sample displays oversite of international shipping from the Dalton facility. Simultaneously established and led the process improvement teams in Waterloo, Ontario. Organized training and consulted with our Waterloo production operation to improve quality and throughput. Shared best manufacturing practices between the US and Canadian… Show more Responsible for distribution and manufacturing operations for the Kraus Flooring Dalton facility. Managed the manufacture and distribution of sample displays oversite of international shipping from the Dalton facility. Simultaneously established and led the process improvement teams in Waterloo, Ontario. Organized training and consulted with our Waterloo production operation to improve quality and throughput. Shared best manufacturing practices between the US and Canadian manufacturing centers to raise our quality and improve Kraus Flooring’s competitive position in the industry. Regularly flew between Ontario and Georgia to lead the process improvement process in Canada. Show less
-
-
-
Mohawk Industries
-
Lyerly, GA
-
Site Manager
-
Jul 2010 - Aug 2011
Held responsibility for multiple aspects of 960,000 SF high-end residential carpet manufacturing plant, with floor staff of 500 people and 31 salaried personnel. Headed departments, including scheduling, shipping and receiving, tufting, two dye operations, finishing, maintenance, quality assurance, process engineering, and one water treatment facility. Completed Six Sigma project to increase constrained pattern machines capacity by 39.5%, which eliminated constrained status of machine… Show more Held responsibility for multiple aspects of 960,000 SF high-end residential carpet manufacturing plant, with floor staff of 500 people and 31 salaried personnel. Headed departments, including scheduling, shipping and receiving, tufting, two dye operations, finishing, maintenance, quality assurance, process engineering, and one water treatment facility. Completed Six Sigma project to increase constrained pattern machines capacity by 39.5%, which eliminated constrained status of machine group and reduced expected labor cost for group of machines by $950,000 annually. Led team to redesign floor plan and to reduce non-active gauge groups. Redrew plant layout and implemented plan to increase greige capacity by 25% and achieve targeted yarn capacity. Involved in restart of coating line, overcoming numerous and chronic quality issues and implementing over 117 action items to improve coating operation. Promoted to site manager in 2011 in midst of numerous quality and cost issues. Oversaw changes to machine maintenance program and allocated money to restore critical machines to improve quality and productivity. Enlisted services of Mohawk training division to design comprehensive training program for operators and fixers, which will include classroom training as well as video and PowerPoint instruction. Show less Held responsibility for multiple aspects of 960,000 SF high-end residential carpet manufacturing plant, with floor staff of 500 people and 31 salaried personnel. Headed departments, including scheduling, shipping and receiving, tufting, two dye operations, finishing, maintenance, quality assurance, process engineering, and one water treatment facility. Completed Six Sigma project to increase constrained pattern machines capacity by 39.5%, which eliminated constrained status of machine… Show more Held responsibility for multiple aspects of 960,000 SF high-end residential carpet manufacturing plant, with floor staff of 500 people and 31 salaried personnel. Headed departments, including scheduling, shipping and receiving, tufting, two dye operations, finishing, maintenance, quality assurance, process engineering, and one water treatment facility. Completed Six Sigma project to increase constrained pattern machines capacity by 39.5%, which eliminated constrained status of machine group and reduced expected labor cost for group of machines by $950,000 annually. Led team to redesign floor plan and to reduce non-active gauge groups. Redrew plant layout and implemented plan to increase greige capacity by 25% and achieve targeted yarn capacity. Involved in restart of coating line, overcoming numerous and chronic quality issues and implementing over 117 action items to improve coating operation. Promoted to site manager in 2011 in midst of numerous quality and cost issues. Oversaw changes to machine maintenance program and allocated money to restore critical machines to improve quality and productivity. Enlisted services of Mohawk training division to design comprehensive training program for operators and fixers, which will include classroom training as well as video and PowerPoint instruction. Show less
-
-
-
Tiger Turf
-
Austin, TX
-
Plant Manager
-
Jan 2010 - Jul 2010
Hired by the CEO to bring leadership and direction to the artificial turf manufacturing facility. Responsibilities included all aspects of tufting and urethane coating of landscape and athletic field turf products as well as shipping, receiving, warehousing, quality, P & L, and operating budget. The scope of the operations included approximately 100 hourly and salaried employees on a four shift 24/7 configuration. The plant produced landscape and athletic turf to be sold in North America and… Show more Hired by the CEO to bring leadership and direction to the artificial turf manufacturing facility. Responsibilities included all aspects of tufting and urethane coating of landscape and athletic field turf products as well as shipping, receiving, warehousing, quality, P & L, and operating budget. The scope of the operations included approximately 100 hourly and salaried employees on a four shift 24/7 configuration. The plant produced landscape and athletic turf to be sold in North America and Mexico. Achievements: • Assessed internal quality issues and began rebuilding the aging machinery. • Established perfomance metrics for quality and productivity. • Developed an action plan to prioritize and attack the toughest issues first. • Sought local computer support for the highly technical urethane coating line. • Hired quality manager and supervisors from out of state to build experience base. • Serious issues with external claims predating my tenure required focusing on replacement orders. Show less Hired by the CEO to bring leadership and direction to the artificial turf manufacturing facility. Responsibilities included all aspects of tufting and urethane coating of landscape and athletic field turf products as well as shipping, receiving, warehousing, quality, P & L, and operating budget. The scope of the operations included approximately 100 hourly and salaried employees on a four shift 24/7 configuration. The plant produced landscape and athletic turf to be sold in North America and… Show more Hired by the CEO to bring leadership and direction to the artificial turf manufacturing facility. Responsibilities included all aspects of tufting and urethane coating of landscape and athletic field turf products as well as shipping, receiving, warehousing, quality, P & L, and operating budget. The scope of the operations included approximately 100 hourly and salaried employees on a four shift 24/7 configuration. The plant produced landscape and athletic turf to be sold in North America and Mexico. Achievements: • Assessed internal quality issues and began rebuilding the aging machinery. • Established perfomance metrics for quality and productivity. • Developed an action plan to prioritize and attack the toughest issues first. • Sought local computer support for the highly technical urethane coating line. • Hired quality manager and supervisors from out of state to build experience base. • Serious issues with external claims predating my tenure required focusing on replacement orders. Show less
-
-
-
-
Plant Manager
-
Sep 2003 - Aug 2009
Recruited by company owner and COO to bring order, quality, productivity, and profitability to its manufacturing operation producing 80% to 90% of the industry's marine carpet, as well as carpet for RV's, athletic turf, manufactured housing, and hospitality rugs. Scope of operations included over 150 employees operating 24/7 in four shifts and six salaried personnel. Produced over 450,000 square yards of carpet weekly. Managed P & L, Operating budget, capital expenditure budget and… Show more Recruited by company owner and COO to bring order, quality, productivity, and profitability to its manufacturing operation producing 80% to 90% of the industry's marine carpet, as well as carpet for RV's, athletic turf, manufactured housing, and hospitality rugs. Scope of operations included over 150 employees operating 24/7 in four shifts and six salaried personnel. Produced over 450,000 square yards of carpet weekly. Managed P & L, Operating budget, capital expenditure budget and purchases. Achievements: Turned plant annual bottom line loss of over $300,000 to a profit of $100,000 verses a revenue neutral budget. Implemented Statistical Process Controls to monitor and focus improvement of plant leading to a reduction of over $200,000 in quality claims annually. Led the plant through ISO 9000 certification and maintained the certification in subsequent audits. Installed modern high speed/ High tech equipment thus expanding production capabilities and design complexity allowing for new styles and product lines. Received multiple safety awards from GTMA and maintained an accident free plant for over a year while practically eliminating employee turnover. Show less Recruited by company owner and COO to bring order, quality, productivity, and profitability to its manufacturing operation producing 80% to 90% of the industry's marine carpet, as well as carpet for RV's, athletic turf, manufactured housing, and hospitality rugs. Scope of operations included over 150 employees operating 24/7 in four shifts and six salaried personnel. Produced over 450,000 square yards of carpet weekly. Managed P & L, Operating budget, capital expenditure budget and… Show more Recruited by company owner and COO to bring order, quality, productivity, and profitability to its manufacturing operation producing 80% to 90% of the industry's marine carpet, as well as carpet for RV's, athletic turf, manufactured housing, and hospitality rugs. Scope of operations included over 150 employees operating 24/7 in four shifts and six salaried personnel. Produced over 450,000 square yards of carpet weekly. Managed P & L, Operating budget, capital expenditure budget and purchases. Achievements: Turned plant annual bottom line loss of over $300,000 to a profit of $100,000 verses a revenue neutral budget. Implemented Statistical Process Controls to monitor and focus improvement of plant leading to a reduction of over $200,000 in quality claims annually. Led the plant through ISO 9000 certification and maintained the certification in subsequent audits. Installed modern high speed/ High tech equipment thus expanding production capabilities and design complexity allowing for new styles and product lines. Received multiple safety awards from GTMA and maintained an accident free plant for over a year while practically eliminating employee turnover. Show less
-
-
-
-
Technical Sales Representative
-
Jun 2002 - Sep 2003
Sought by company owner to develop new customers and markets for designer chemicals targeted at the textiles industry. Used contacts and industry connections to pursue new customers for the company's custom fiber lubricant capability. Achievements: Established numerous customer accounts and maintained a sales region including Georgia, Alabama, North and South Carolina. Led trials with customers to develop, modify, and redesign the chemicals necessary to process industrial… Show more Sought by company owner to develop new customers and markets for designer chemicals targeted at the textiles industry. Used contacts and industry connections to pursue new customers for the company's custom fiber lubricant capability. Achievements: Established numerous customer accounts and maintained a sales region including Georgia, Alabama, North and South Carolina. Led trials with customers to develop, modify, and redesign the chemicals necessary to process industrial fibers. Established plant safety protocols, and necessary safety barriers. Show less Sought by company owner to develop new customers and markets for designer chemicals targeted at the textiles industry. Used contacts and industry connections to pursue new customers for the company's custom fiber lubricant capability. Achievements: Established numerous customer accounts and maintained a sales region including Georgia, Alabama, North and South Carolina. Led trials with customers to develop, modify, and redesign the chemicals necessary to process industrial… Show more Sought by company owner to develop new customers and markets for designer chemicals targeted at the textiles industry. Used contacts and industry connections to pursue new customers for the company's custom fiber lubricant capability. Achievements: Established numerous customer accounts and maintained a sales region including Georgia, Alabama, North and South Carolina. Led trials with customers to develop, modify, and redesign the chemicals necessary to process industrial fibers. Established plant safety protocols, and necessary safety barriers. Show less
-
-
-
-
Plant Manager
-
Nov 1999 - Apr 2002
Promoted to define changes and improvements in quality, productivity and costs for the only residential berber plant in the company. Responsible for the scope of operations including over 600 employees and 16 salaried managers operating 24/7 with a weekly capacity of over 800,000 square yards of finished carpet weekly. Controlled P & L, Operating budget, capital expenditure budget and purchases. Achievements: Reduced off quality carpet by over 83% using statistical methods… Show more Promoted to define changes and improvements in quality, productivity and costs for the only residential berber plant in the company. Responsible for the scope of operations including over 600 employees and 16 salaried managers operating 24/7 with a weekly capacity of over 800,000 square yards of finished carpet weekly. Controlled P & L, Operating budget, capital expenditure budget and purchases. Achievements: Reduced off quality carpet by over 83% using statistical methods, appropriate training policies, team building, and strong consistent leadership. Improved productivity and reduced operating cost variances by over $40,000 per week while reducing turnover and increasing safety awareness. Redesigned the floor plan and upgraded machinery to include computerized high speed scroll machines and enhanced graphic equipment thus advancing our design capabilities and facilitating the development of new product lines. Increased productivity to allow for the elimination of the weekend shifts and reducing overall labor and operating costs. Instilled management skills in my supervisory personnel. Subsequently, two of my department managers were promoted to plant management positions at other locations. Led plant through ISO 9002 certification and maintained the certification throughout my tenure. Show less Promoted to define changes and improvements in quality, productivity and costs for the only residential berber plant in the company. Responsible for the scope of operations including over 600 employees and 16 salaried managers operating 24/7 with a weekly capacity of over 800,000 square yards of finished carpet weekly. Controlled P & L, Operating budget, capital expenditure budget and purchases. Achievements: Reduced off quality carpet by over 83% using statistical methods… Show more Promoted to define changes and improvements in quality, productivity and costs for the only residential berber plant in the company. Responsible for the scope of operations including over 600 employees and 16 salaried managers operating 24/7 with a weekly capacity of over 800,000 square yards of finished carpet weekly. Controlled P & L, Operating budget, capital expenditure budget and purchases. Achievements: Reduced off quality carpet by over 83% using statistical methods, appropriate training policies, team building, and strong consistent leadership. Improved productivity and reduced operating cost variances by over $40,000 per week while reducing turnover and increasing safety awareness. Redesigned the floor plan and upgraded machinery to include computerized high speed scroll machines and enhanced graphic equipment thus advancing our design capabilities and facilitating the development of new product lines. Increased productivity to allow for the elimination of the weekend shifts and reducing overall labor and operating costs. Instilled management skills in my supervisory personnel. Subsequently, two of my department managers were promoted to plant management positions at other locations. Led plant through ISO 9002 certification and maintained the certification throughout my tenure. Show less
-
-
-
-
Plant Manager
-
Nov 1996 - Nov 1999
Selected to lead the company's high capacity commodity carpet facility. Responsible for four carpet coating operations in two locations and over 900,000 square yards of weekly carpet tufting capacity in 24/5 operations. Managed P&L, Operating Budget, Capital Budget, and plant purchases. Achievements: Implemented Statistical Process Control Systems throughout operations and lowered total off quality by 68%, from 0.8% of production to under 0.25% of production. Established… Show more Selected to lead the company's high capacity commodity carpet facility. Responsible for four carpet coating operations in two locations and over 900,000 square yards of weekly carpet tufting capacity in 24/5 operations. Managed P&L, Operating Budget, Capital Budget, and plant purchases. Achievements: Implemented Statistical Process Control Systems throughout operations and lowered total off quality by 68%, from 0.8% of production to under 0.25% of production. Established comprehensive employee training plans to improve quality, safety, employee satisfaction, and productivity. Replaced aging tufting equipment with high speed machinery and redesigned the floor plan to optimize production flow. Proposed and implemented a corporate plan to consolidate similar machinery in various plants to create a more specialized workforce within each operation. Became the first carpet tufting plant to be ISO 9002 certified. Led plant into a standardized cost program and regularly surpassed the engineered costs standards. Show less Selected to lead the company's high capacity commodity carpet facility. Responsible for four carpet coating operations in two locations and over 900,000 square yards of weekly carpet tufting capacity in 24/5 operations. Managed P&L, Operating Budget, Capital Budget, and plant purchases. Achievements: Implemented Statistical Process Control Systems throughout operations and lowered total off quality by 68%, from 0.8% of production to under 0.25% of production. Established… Show more Selected to lead the company's high capacity commodity carpet facility. Responsible for four carpet coating operations in two locations and over 900,000 square yards of weekly carpet tufting capacity in 24/5 operations. Managed P&L, Operating Budget, Capital Budget, and plant purchases. Achievements: Implemented Statistical Process Control Systems throughout operations and lowered total off quality by 68%, from 0.8% of production to under 0.25% of production. Established comprehensive employee training plans to improve quality, safety, employee satisfaction, and productivity. Replaced aging tufting equipment with high speed machinery and redesigned the floor plan to optimize production flow. Proposed and implemented a corporate plan to consolidate similar machinery in various plants to create a more specialized workforce within each operation. Became the first carpet tufting plant to be ISO 9002 certified. Led plant into a standardized cost program and regularly surpassed the engineered costs standards. Show less
-
-
-
-
Plant Manager
-
Oct 1995 - Nov 1996
Promoted to be the first Beaulieu plant manager of a new company acquisition. Managed all aspects of plant function including, P&L, budget, payroll, product development, quality, raw material purchases and vendor selection. Operations included over 150 employees and six salaried personnel with a 24/5 schedule. Promoted to be the first Beaulieu plant manager of a new company acquisition. Managed all aspects of plant function including, P&L, budget, payroll, product development, quality, raw material purchases and vendor selection. Operations included over 150 employees and six salaried personnel with a 24/5 schedule.
-
-
-
-
Production Manager
-
Feb 1993 - Oct 1995
Successfully integrated the new acquisition into the Beaulieu Group. Developed new products and specialty products to utilize distressed yarns, earning the plant $1 Million in sales over a three month period. Implemented employee training program improving on safety, production and quality. Restored machinery and renovated plant appearance.; Managed production, quality, machine scheduling, supervisors, and employees over a new extrusion department with over 250,000 lbs of daily… Show more Successfully integrated the new acquisition into the Beaulieu Group. Developed new products and specialty products to utilize distressed yarns, earning the plant $1 Million in sales over a three month period. Implemented employee training program improving on safety, production and quality. Restored machinery and renovated plant appearance.; Managed production, quality, machine scheduling, supervisors, and employees over a new extrusion department with over 250,000 lbs of daily production capacity processing both nylon and polypropylene material. Managed 29 extrusion lines on 4 shifts 24/7. Maintained raw material inventories, custom colors and packing supplies reordering as required. Directed new trials, yarn quality initiatives and insured shade consistency. Achievements: Key team member in the design and installation of new extrusion department. Established key measures, goals, and Statistical Process Control Methods to operate under. Used multivariable testing to statistically identify and correct various startup issues in the new processes. Helped to write all of the new training books and quality policies. Took plant from startup to successful high production high quality operation. Show less Successfully integrated the new acquisition into the Beaulieu Group. Developed new products and specialty products to utilize distressed yarns, earning the plant $1 Million in sales over a three month period. Implemented employee training program improving on safety, production and quality. Restored machinery and renovated plant appearance.; Managed production, quality, machine scheduling, supervisors, and employees over a new extrusion department with over 250,000 lbs of daily… Show more Successfully integrated the new acquisition into the Beaulieu Group. Developed new products and specialty products to utilize distressed yarns, earning the plant $1 Million in sales over a three month period. Implemented employee training program improving on safety, production and quality. Restored machinery and renovated plant appearance.; Managed production, quality, machine scheduling, supervisors, and employees over a new extrusion department with over 250,000 lbs of daily production capacity processing both nylon and polypropylene material. Managed 29 extrusion lines on 4 shifts 24/7. Maintained raw material inventories, custom colors and packing supplies reordering as required. Directed new trials, yarn quality initiatives and insured shade consistency. Achievements: Key team member in the design and installation of new extrusion department. Established key measures, goals, and Statistical Process Control Methods to operate under. Used multivariable testing to statistically identify and correct various startup issues in the new processes. Helped to write all of the new training books and quality policies. Took plant from startup to successful high production high quality operation. Show less
-
-
-
-
Various Supervisory Positions
-
Jun 1990 - Feb 1993
Promoted rapidly through a series of increasingly responsible operating management and leadership positions. Achievements: Designed and implemented an operating plan and floor plan for a new quarter million square foot warehouse. Increased extruded yarn productivity and quality exceeding all other shifts. Promoted rapidly through a series of increasingly responsible operating management and leadership positions. Achievements: Designed and implemented an operating plan and floor plan for a new quarter million square foot warehouse. Increased extruded yarn productivity and quality exceeding all other shifts.
-
-
Education
-
The University of Tennessee at Chattanooga
Bachelor of Science (BS), Business Administration, Marketing
Community
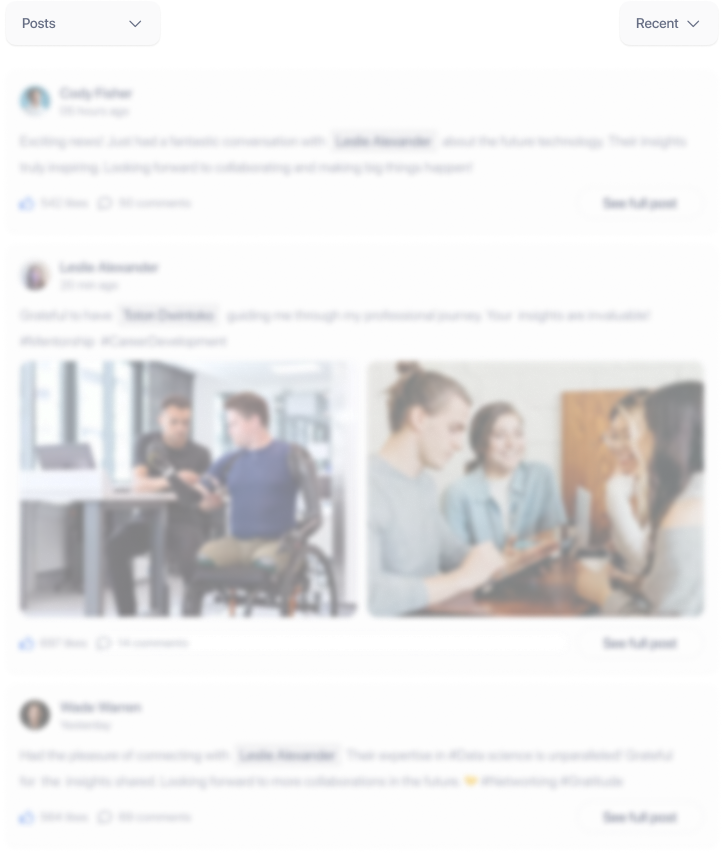