Douglas Nelson
Head Mechanic at Progressive Food Solutions Llc- Claim this Profile
Click to upgrade to our gold package
for the full feature experience.
-
English Native or bilingual proficiency
-
Spanish Limited working proficiency
Topline Score
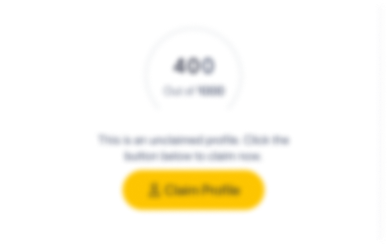
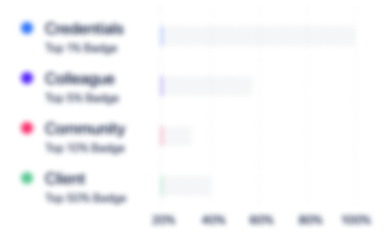
Bio


Experience
-
Progressive Food Solutions Llc
-
United States
-
Restaurants
-
1 - 100 Employee
-
Head Mechanic
-
Apr 2021 - Present
-
-
-
Thermo Fisher Scientific
-
United States
-
Biotechnology Research
-
700 & Above Employee
-
Manufacturing Engineer, Shift Production Supervisor
-
Feb 2014 - Mar 2021
o Initiated modernization of production equipment and procedures, aligning with customer requirements.o Identified areas where inadequate, malfunctioning or equipment shortages inhibited maximum utilization of assets; Strategized solutions to increase efficiency and accuracy.o Create production schedules with dual goal of reducing backorders and increasing throughput.o Develop operating procedures and train operators in the proper set-up, running and troubleshoot of semi- automatic filling stations. Reduced down-time by a minimum of 50%.o Improvements to existing and creating training procedures where none existed, decreased instruction period and improved initial performance of new team members.o Leadership of Emergency response Team raised awareness standards and performance of team in crisis situations.o Work closely with Quality Assurance department to find root causes and solutions to quality issues.o Develop and implement solutions to production issues, maintaining high levels of output.
-
-
Logistics Specialist/Head Trainer/Emergency Response Team, Asst. Captain
-
Jul 2010 - Jan 2014
- Created a system of arranging products on pallets meeting railroad requirements, enabling freight shipment by Intermodal Rail Freight for Practical Process Improvement project. Currently results in an annual savings in excess of $500,000. - Participant in Refrigerated Flammable Storage Restructuring. Ideas brought to project increased capacity 33%, raised efficiency of operations and eliminated risky storage practices. Eliminated situations resulting in day long shut downs of 50% of facility. - Able to reduce the training period of new employees on the team from 6-8 weeks to 2 weeks. Practices are currently in use. - Member of the Emergency Response Team. OSHA HAZWOPER & Thermo-Fisher hazardous contaminate identification & cleanup trained. Versed in OSHA PPE guidelines, New Jersey DEP procedures, trained in First Aid, CPR & SCBA. - Authored/revised official Departmental Operating Procedure to properly describe job functions and procedures
-
-
-
Pfizer
-
Events Services
-
1 - 100 Employee
-
Assistant Supervisor of Operations
-
May 2010 - Jul 2010
(Through Volt Services Group, Whippany, NJ)- Supervise and direct twelve person team when supervisor was absent; direct and supervise special projects.- Cataloged, recorded and shipped sensitive files for a major pharmaceutical company; lead role on critical project positions for the purpose of continuity during a myriad of personnel changes.- Obtained from Pfizer security clearance handling sensitive documentation, facilitated team compliance with process guidelines. - Lead various teams in the batching, handling and shipping of materials to ensure proper order and security integrity.
-
-
-
LG Electronics
-
South Korea
-
Computers and Electronics Manufacturing
-
700 & Above Employee
-
Assistant Test Engineer
-
Mar 2010 - May 2010
(For LG Mobilcomm Through Volt Services Group, Whippany, NJ)- Qualify new cellular products for Verizon, T-Mobile & AT&T via testing and performance measurement; testing criteria include: 1X, 2G, 3G voice and data performance. Identified & reported specific performance modifications.- Analyzed and modified test routes that resulted in unit-wide reduction in fuel consumption and miles traveled for more efficient use of time and diminution of man hours required for product testing. (For LG Mobilcomm Through Volt Services Group, Whippany, NJ)- Qualify new cellular products for Verizon, T-Mobile & AT&T via testing and performance measurement; testing criteria include: 1X, 2G, 3G voice and data performance. Identified & reported specific performance modifications.- Analyzed and modified test routes that resulted in unit-wide reduction in fuel consumption and miles traveled for more efficient use of time and diminution of man hours required for product testing.
-
-
-
-
Project Manager
-
Jan 2009 - Jan 2010
- Evaluated conditions of a residential property; determined the types of work to be performed for implementation of green technologies and maximization of return on investment. Obtained proper work permits; ensured all work was code compliant. - Supervised contractors' performance and work quality. Acted as liaison between all contractors on the job.- Performed various construction trade tasks during project. - Evaluated conditions of a residential property; determined the types of work to be performed for implementation of green technologies and maximization of return on investment. Obtained proper work permits; ensured all work was code compliant. - Supervised contractors' performance and work quality. Acted as liaison between all contractors on the job.- Performed various construction trade tasks during project.
-
-
-
LVH Electric
-
United States
-
Operations and Project Manager
-
Aug 2006 - Dec 2009
Oversee metal fabrication shop and fifteen person road crew comprised of riggers, electricians and helpers at multiple job sites; project manage contracts to completion; participate in proposal, design and bid activities; participate in on site work as required. - Was challenged with installing permanent lighting technology in Mission Basilica San Juan Capistrano, a project worth $500,000. Discovered specified installation equipment was inadequate. Worked locally with contractors on a related project to extend their scaffolding work so that the lighting project could be completed on time and under budget.-Worked closely with state and local inspectors: California Dept. of Architects; Underwriters Labratories; National Electrical Code . - Project managed a facility move transposing the company's warehouse and workshop spaces, keeping cost and downtime at a minimum.
-
-
-
DeSisti Lighting
-
Movies, Videos, and Sound
-
1 - 100 Employee
-
Manager of Engineering Services/DeSisti Rigging & Automation
-
Jan 2005 - Apr 2006
Manage Production and design of electric theatrical hoists & lifts. Assist contractors in installation of systems. Commission systems. Provide sales quotes and proposals based on client's needs. Creat & provide submittal drawings, cut sheets, and specifications for contracts. Manage projects internationally, designing custom modifications to basic product to comply with local regulations. Include Japan, Canada and Carribean Islands.-Created a new standardized CAD architectural drawing process whereby electrical engineers & general contractors in the US and Italian production facilities could understand cross-country drawings. The overhauled process reduced response time from 2+ months, to 1-week, minimized difficulties in understanding drawings, saving time and reduced manpower significantly. -Devised a repurposed facility to accommodate newly self-designed equipment to aid in the process of assembling products in the USA instead of Italy. Utilized never used before light weight fiber tubing that significantly reduced packaging costs over crating; saved money when products were shipped domestically and internationally. -Devised and implemented a 100% ‘Hands-Off” distribution and shipping system. Materials received from factory in Rome, Italy were received, broken down and shipped nationally by 3rd party contractors, eliminating need for investment in facilities. Resultant savings estimated to be $70,000/yr in shipping alone, eliminated losses due to disruption of operations to process shipments.
-
-
-
-
Energy and Efficiency Analyst; Team Leader
-
Jan 2003 - 2004
- Supervise Industrial Assessment Centers throughout the US for the US Department Of Energy. - Recommended conservation methods based on the viable solution techniques available. Recommendations included the use of compressed air, HVAC, building envelope, process heating, steam, lighting, solar & co-generation. o Conveyer belt found faulty - 40% of the parts that traveled down the conveyer were destroyed. Strongly recommended and received by-in by the client to install magnetic conveyer belts as a solution to save on the amount of materials scrapped (down to 5%) which also saved the company money on production costs.
-
-
-
O.Berk Company
-
United States
-
Packaging and Containers Manufacturing
-
1 - 100 Employee
-
Account manager/Sales Service
-
Jun 1994 - Sep 2000
- Managed daily activities; oversaw multiple account activities, provided research and development for new products, monitored inventory, performed evaluations, addressed compatibility and failure issues. Headed telemarketing team. - Inside sales of containers, closure products and accessory treatments to multiple industries. - Managed daily activities; oversaw multiple account activities, provided research and development for new products, monitored inventory, performed evaluations, addressed compatibility and failure issues. Headed telemarketing team. - Inside sales of containers, closure products and accessory treatments to multiple industries.
-
-
Education
-
Rutgers, The State University of New Jersey-New Brunswick
Bachelor's Degree, Indusrtrial & Systems Engineering
Community
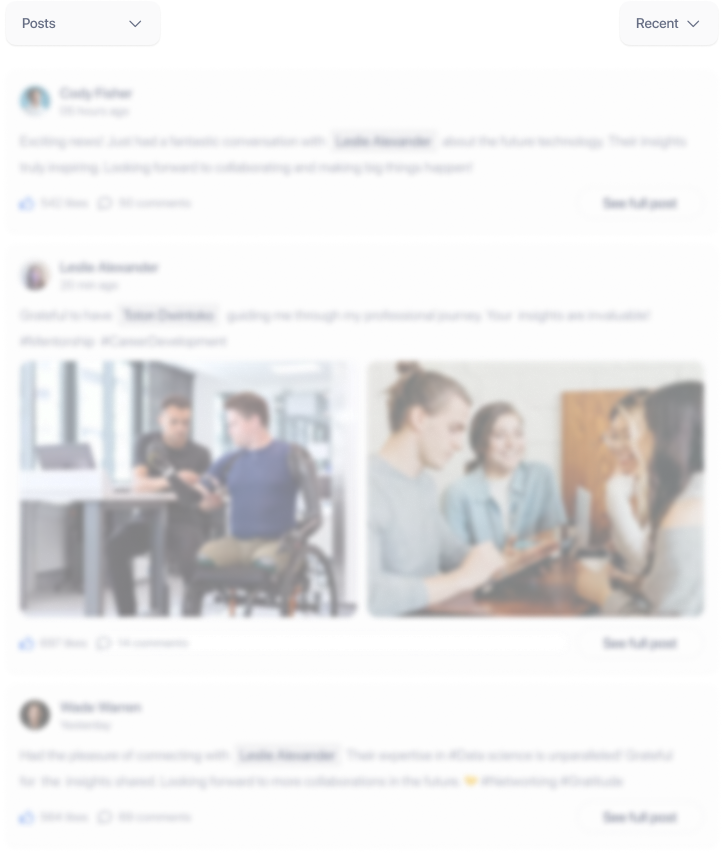