
Doug Ochis
Site Operations Manager at Quality Tech Services- Claim this Profile
Click to upgrade to our gold package
for the full feature experience.
Topline Score
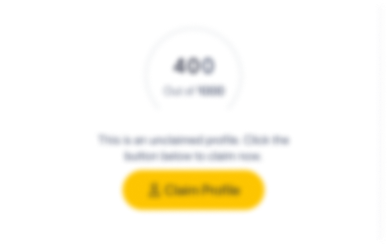
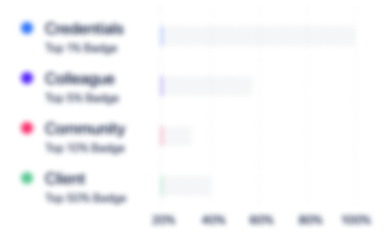
Bio

Donald Birnie
I had the pleasure to work with Doug over a period spanning almost 5 years and in that time I had the opportunity to support his engaging and professional approach in problem solving and culture change. Whatever challenges were presented, Doug would logically and methodically approach the task at hand in a way that fostered engagement and accommodated varying opinion to assure success, even spanning cultural differences. Doug is the consummate professional and will be a tremendous asset to any organisation who seeks a level head in the turbulent waters of Operations today and he will settle for nothing short of the desired outcome.

Scott Larson
Doug is a focused professional that is an effective leader, manager and technical asset. He has the ability to facilitate and lead groups though any type of discussion, brainstorming or problem solving process, while achieving operational symmetry that’s proven to keep a supply chain moving and production lines up and running. Doug’s attention to detail, compassion for his direct reports, concern for quality and team focused approach makes these difficult tasks seem natural and effortless. I highly recommend Doug for any position or endeavor that he may seek to pursue. He will be a valuable asset for any organization.

Donald Birnie
I had the pleasure to work with Doug over a period spanning almost 5 years and in that time I had the opportunity to support his engaging and professional approach in problem solving and culture change. Whatever challenges were presented, Doug would logically and methodically approach the task at hand in a way that fostered engagement and accommodated varying opinion to assure success, even spanning cultural differences. Doug is the consummate professional and will be a tremendous asset to any organisation who seeks a level head in the turbulent waters of Operations today and he will settle for nothing short of the desired outcome.

Scott Larson
Doug is a focused professional that is an effective leader, manager and technical asset. He has the ability to facilitate and lead groups though any type of discussion, brainstorming or problem solving process, while achieving operational symmetry that’s proven to keep a supply chain moving and production lines up and running. Doug’s attention to detail, compassion for his direct reports, concern for quality and team focused approach makes these difficult tasks seem natural and effortless. I highly recommend Doug for any position or endeavor that he may seek to pursue. He will be a valuable asset for any organization.

Donald Birnie
I had the pleasure to work with Doug over a period spanning almost 5 years and in that time I had the opportunity to support his engaging and professional approach in problem solving and culture change. Whatever challenges were presented, Doug would logically and methodically approach the task at hand in a way that fostered engagement and accommodated varying opinion to assure success, even spanning cultural differences. Doug is the consummate professional and will be a tremendous asset to any organisation who seeks a level head in the turbulent waters of Operations today and he will settle for nothing short of the desired outcome.

Scott Larson
Doug is a focused professional that is an effective leader, manager and technical asset. He has the ability to facilitate and lead groups though any type of discussion, brainstorming or problem solving process, while achieving operational symmetry that’s proven to keep a supply chain moving and production lines up and running. Doug’s attention to detail, compassion for his direct reports, concern for quality and team focused approach makes these difficult tasks seem natural and effortless. I highly recommend Doug for any position or endeavor that he may seek to pursue. He will be a valuable asset for any organization.

Donald Birnie
I had the pleasure to work with Doug over a period spanning almost 5 years and in that time I had the opportunity to support his engaging and professional approach in problem solving and culture change. Whatever challenges were presented, Doug would logically and methodically approach the task at hand in a way that fostered engagement and accommodated varying opinion to assure success, even spanning cultural differences. Doug is the consummate professional and will be a tremendous asset to any organisation who seeks a level head in the turbulent waters of Operations today and he will settle for nothing short of the desired outcome.

Scott Larson
Doug is a focused professional that is an effective leader, manager and technical asset. He has the ability to facilitate and lead groups though any type of discussion, brainstorming or problem solving process, while achieving operational symmetry that’s proven to keep a supply chain moving and production lines up and running. Doug’s attention to detail, compassion for his direct reports, concern for quality and team focused approach makes these difficult tasks seem natural and effortless. I highly recommend Doug for any position or endeavor that he may seek to pursue. He will be a valuable asset for any organization.

Experience
-
QTS Medical Device Outsourcing
-
United States
-
Medical Device
-
1 - 100 Employee
-
Site Operations Manager
-
2012 - Present
QTS provides a wide variety of outsourcing solutions focused on satisfying the needs of medical device manufacturers around the world. By specializing in sterile barrier package design, process validation, clean room assembly & packaging, as well as, component sourcing, QTS brings high quality products to market quickly and efficiently.Direct responsibility for the plants manufacturing activities across 3 Business Units each with an ISO class 7 clean room. Identified KPI’s for the Manufacturing department. Initiated the process of implementing Lean Manufacturing methodologies to drive ongoing improvements in key performance areas. In addition to overseeing daily scheduling and manufacturing activities; I am accountable for identifying, and bringing in house, leading technologies, developing improved manufacturing processes, a Lean Manufacturing Implementation program, departmental budgeting, training requirements and staffing plans.
-
-
-
Olympus Corporation of the Americas
-
United States
-
Medical Equipment Manufacturing
-
700 & Above Employee
-
Value Stream Manager
-
Jan 2006 - Feb 2012
Directly responsible for coordinating the efforts of all cross functional teams (Scheduling, Supply Chain, Quality, Engineering) to support manufacturing, in a build to demand environment, of over 170 finished goods for worldwide distribution. Familiar with the needs for producing Class II & III Disposable devices in an ISO Class 8 clean room setting as well as Capital goods . Work with Leadership team to identify, and then achieve, key business goals in the areas of Manufacturing Efficiencies, Cost Reductions, Product Availability and Quality. Staffing responsibilities, including hiring/firing and employee development, for 50+ direct and indirect reports.
-
-
Operations | Manufacturing | Value Stream Manager Skilled in Lean Manufacturing Implementation | Ope
-
2006 - 2012
Driving operational excellence through identifying needs and implementing the right Lean Manufacturing tools for operations of any size including ISO and FDA certified facilities. Increase production throughput, reduce manufacturing waste and achieve on time delivery while ensuring quality and customer service goals are met/exceeded.
-
-
-
ACMI
-
Medical Device
-
100 - 200 Employee
-
Production Supervisor
-
Feb 2002 - Jan 2006
Effectively communicated daily goals and priorities to multiple production lines consisting of 50 to 60 direct reports. Monitoring production output, quality and training through a variety of key metrics. Implementing continuous improvements through Lean Manufacturing techniques. Working with support groups to ensure documentation and process improvements are incorporated in a timely manner. Effectively communicated daily goals and priorities to multiple production lines consisting of 50 to 60 direct reports. Monitoring production output, quality and training through a variety of key metrics. Implementing continuous improvements through Lean Manufacturing techniques. Working with support groups to ensure documentation and process improvements are incorporated in a timely manner.
-
-
-
Northwest Airlines
-
Airlines and Aviation
-
700 & Above Employee
-
Production Support Manager
-
Mar 1990 - Oct 2001
Prioritizing and scheduling requirements and personnel to support Maintenance and Inspection operations in aircraft heavy maintenance hangers. Ensuring all documentation was maintained per FAA requirements. Prioritizing and scheduling requirements and personnel to support Maintenance and Inspection operations in aircraft heavy maintenance hangers. Ensuring all documentation was maintained per FAA requirements.
-
-
-
Unisys
-
United States
-
IT Services and IT Consulting
-
700 & Above Employee
-
Asset Recovery Lead Technician
-
1982 - 1989
Hands on training of 30+ personnel in the disassembly and sorting of precious metal bearing computer components. Heavy equipment maintenance, record keeping, scheduling and planning of sort line and shipping and receiving areas. Hands on training of 30+ personnel in the disassembly and sorting of precious metal bearing computer components. Heavy equipment maintenance, record keeping, scheduling and planning of sort line and shipping and receiving areas.
-
-
Education
-
University of St. Thomas
-
Augsburg College
B.A., Business Administration, Minor in Economics
Community
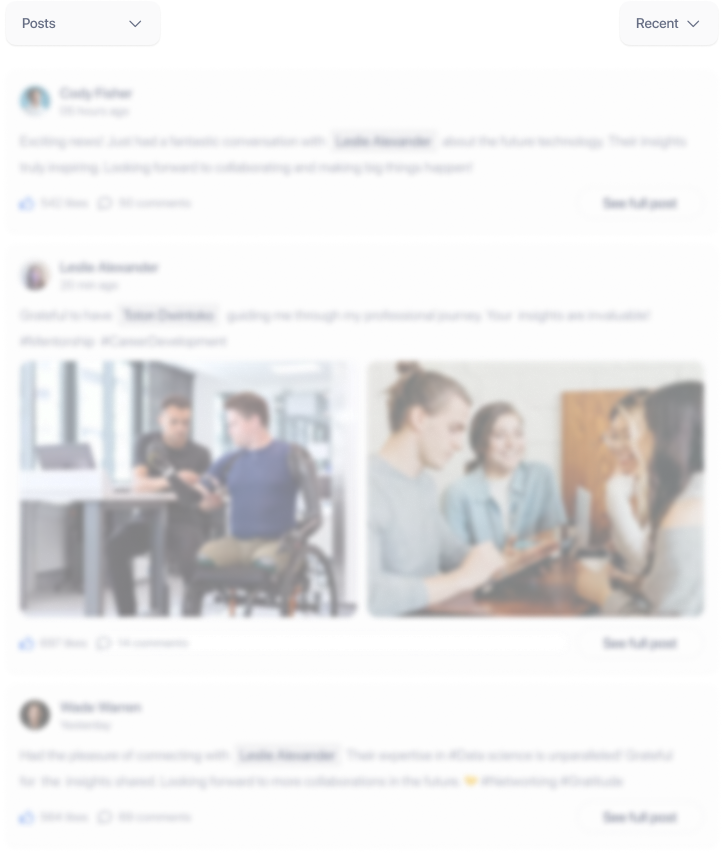