Doug Imbrogna
Plant Engineer at Ajinomoto Cambrooke, Inc.- Claim this Profile
Click to upgrade to our gold package
for the full feature experience.
Topline Score
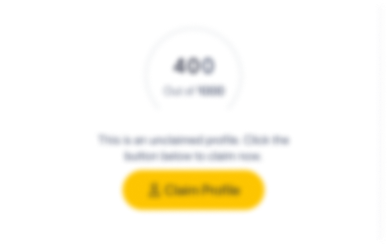
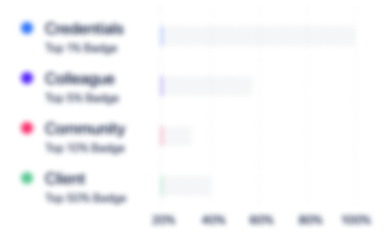
Bio


Experience
-
Ajinomoto Cambrooke, Inc.
-
United States
-
Pharmaceutical Manufacturing
-
1 - 100 Employee
-
Plant Engineer
-
Oct 2022 - Present
-
-
-
Superior Nut Co Inc
-
United States
-
Food and Beverage Services
-
1 - 100 Employee
-
Plant Engineer
-
Feb 2020 - Oct 2022
Oversee operation of 112-year-old 65,000+ sq. ft. facility with 6 floors, 3 elevators, and over 200 unique pieces of machinery and equipment. Oversaw $1M “Can Line” upgrade during the pandemic: • Prepared the plan and site for 2-day line shut down • Upgraded the primary production (packaging) line to incorporate new key pieces of equipment including a new Fully Automated Bosch Wraparound Case Packer • Programmed the machine to run 10 additional formats for $50,000 less than the OEM bid and ultimately exceeded OEM specifications Project manager for $1M “Continuous Dry Roaster” CAPEX upgrade: • Coordinated installation and commissioning with OEM • Successfully planned and integrated a through-building multi-floor exhaust duct • Added two high-capacity make-up air units to the 3rd-floor production area. This supplied the air necessary for proper combustion and improved air quality throughout the plant
-
-
-
Canobie Seafoods INC
-
United States
-
1 - 100 Employee
-
Fleet Technology Consultant & Maintanance Tchnician
-
Sep 2017 - Apr 2021
Provided electrical, mechanical, and plumbing services for 5000 sq. ft. live seafood/saltwater facility Implemented an Electronic Logging Device (ELD) system to meet the Federal Motor Carrier (FMCSA) deadline. • Created and managed database with ELD service provider • Coordinated with each of the 10 Semi-tractors to find a window of time for installation • Installed ELD tracking devices on all fleet vehicles Created and integrated a cellular temperature monitoring system for live freight so that users could log-in and see the temperature and location of their shipment when they had concerns it was being shipped warm. Provided training and technical support for the CDL drivers.
-
-
-
Portsmouth Naval Shipyard
-
United States
-
Defense & Space
-
700 & Above Employee
-
Mechanical Engineer
-
Oct 2018 - Feb 2020
Analyzed existing submarine components allowing for a 50% increase in structural capacity (details classified). This allowed for a more efficient and safer overhaul procedure. Designed a complex fixture for the Rigging Department that allowed them to train for situations they would see inside the submarines. Subject Matter Expert (SME) for torque wrench usage. Re-wrote the technical documentation procedures for how to use, read, and care-for equipment used for fastener torquing. Appointed project manager for a $2.5M overhaul on a key piece of lifting equipment.
-
-
-
InnovativeFoto
-
Salem, New Hampshire, United States
-
Mechanical Design Engineer
-
Aug 2015 - Sep 2017
Created an articulating camera for special purpose use at Walt Disney World that required ADA (Americans with Disabilities Act) compliance. This new assembly allowed for aiming at standing customers as well as customers sitting in wheelchairs. Created three ADA compliant kiosk assemblies for Walt Disney World Speedway to print 'driver's license' badges. Oversaw a two-person Printer Repair Department. Created an articulating camera for special purpose use at Walt Disney World that required ADA (Americans with Disabilities Act) compliance. This new assembly allowed for aiming at standing customers as well as customers sitting in wheelchairs. Created three ADA compliant kiosk assemblies for Walt Disney World Speedway to print 'driver's license' badges. Oversaw a two-person Printer Repair Department.
-
-
-
State Gardens LLC
-
United States
-
Food Production
-
1 - 100 Employee
-
Mechanical Engineer
-
Sep 2010 - Aug 2015
Using hygienic design, invented a proprietary Autopaddle machine that eliminated one operator from each of our 14 production lines.Decommissioned our old celery production facility and designed all new proprietary equipment for the new celery production location. This featured a hygienic design for food production and ease of washing. Designed proprietary check-weigher equipment for use on all production lines. These were mounted onto existing machinery to fit with the spatial constraints of production lines. Developed standard operating procedures (SOP) and step-by-step instructions for assembly and use of all equipment.Designed custom manhole covers strong enough to support forklifts.
-
-
Maintanance Technician
-
Dec 2008 - Aug 2010
-
-
Education
-
Boston University
Bachelor of Applied Science (BASc), Mechanical Engineering -
Duxbury High School
Community
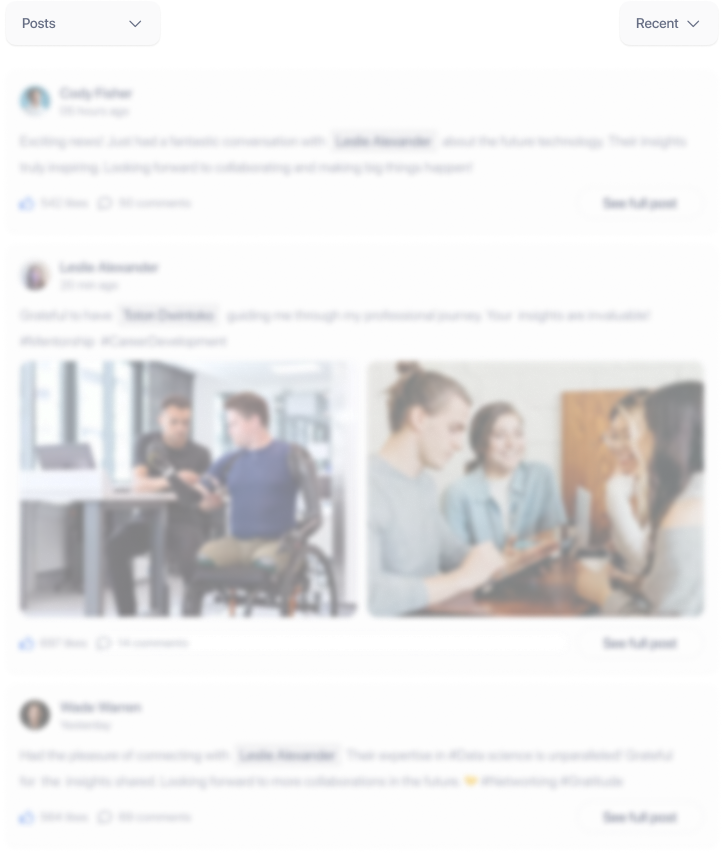