Doug Gordon
Senior Project Manager at Conveyco Technologies- Claim this Profile
Click to upgrade to our gold package
for the full feature experience.
Topline Score
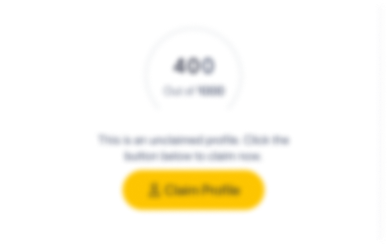
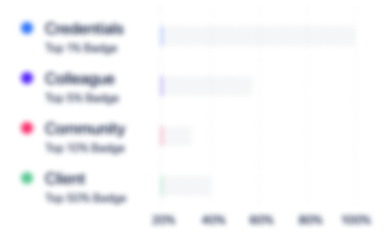
Bio


Experience
-
Conveyco Technologies
-
United States
-
Transportation, Logistics, Supply Chain and Storage
-
1 - 100 Employee
-
Senior Project Manager
-
Jan 2022 - Present
Senior Project Manager launching new innovative solutions for Automotive client and consumer goods client. Senior Project Manager launching new innovative solutions for Automotive client and consumer goods client.
-
-
-
Dematic
-
United States
-
Transportation, Logistics, Supply Chain and Storage
-
700 & Above Employee
-
Senior Professional Project Manager
-
Jun 2016 - Present
Responsible for various projects for Dematic which supports Amazon Fulfillment Centers throughout the United States. Responsible for various projects for Dematic which supports Amazon Fulfillment Centers throughout the United States.
-
-
-
Visteon Corporation
-
United States
-
Motor Vehicle Manufacturing
-
700 & Above Employee
-
Resident Manufacturing Engineer-Americas
-
Jul 2014 - Sep 2015
Responsibility is evolving from an Advanced Manufacturing Engineer (JCI role) to more of a Senior Resident Engineer. Main responsibly will to support new business quoting activities and designs with the Design for Manufacturing in mind. Be the liaison between the Product Engineering and the Plants during the design phases. Responsibility is evolving from an Advanced Manufacturing Engineer (JCI role) to more of a Senior Resident Engineer. Main responsibly will to support new business quoting activities and designs with the Design for Manufacturing in mind. Be the liaison between the Product Engineering and the Plants during the design phases.
-
-
-
Johnson Controls
-
Ireland
-
Industrial Machinery Manufacturing
-
700 & Above Employee
-
Advanced Manufacturing Engineer-Electronics
-
Jun 2012 - Jun 2014
Provide design for manufacturability to Product Design Groups and support to the Launch Engineering Teams for various Instrument Cluster and Center Console Displays. Key interface and the voice of the manufacturing plant during the internal design and development phases of the program. • Utilized Design for Manufacturing Analysis software (DFMA) to create the most efficient methods to assemble Instrument Clusters and Display assemblies • Successfully launched several of B4 (GM) Instrument Clusters all on the same line utilizing a similar DFMA concepts • Acquired and successfully launched Ford MFD4 center display from a fellow AME and smoothly continued the multiple bracket launches plus new business launches to the excess of 750K units a year production. • Professionally ended the Ford U502 Instrument Cluster Line that was in the build phase due to Ford change in sourcing direction after the Visteon Acquisition • Successfully launched BMW, Ford, GM and Volvo Automotive Electronic components with each meeting and exceeding customer satisfaction within the manufacturing environment Attended weekly design reviews for various products as the voice of manufacturing and feasibility. Utilizing templates and lessons learned from previous teams, allowed my team to launch several products very successfully and all under budget. Show less
-
-
-
Saint-Gobain India Private Limited - Glass Business
-
Glass Product Manufacturing
-
700 & Above Employee
-
Senior Manufacturing Engineer/ Cold End Project Manager
-
May 2007 - Jun 2012
Routinely manage manufacturing projects and demonstrate the vision and ability to complete these efforts on time and at cost; successfully apply a solid technical expertise to support, troubleshoot and ensure internal process effectiveness; and work closely with the operations team to propagate the principals of Flow and Lean Manufacturing. • As project manager, have been able to cover all the mechanical, electrical and project management duties on projects up to $5,300,000. The results allow for other projects to be covered by fellow engineers. • As Cold End Engineer created budgets, WBS and executed projects at Saint Gobain Containers Glass Manufacturing Facilities. • Cold End Engineers are responsible from the end of the Lehr to the shipping dock within a glass plant. Areas covered are mass flow conveyors, single bottle conveyors, inspection equipment, bulk handling equipment, case packing and inserting equipment, stretch wrapping and bagging of pallets, Warehouse Management Systems (WMS) and Pallet labeling systems. • Worked closely with the various plant resources (Operations, Scheduling, Engineering, Maintenance and Warehouse to reduce any downtime caused by project installations. In one case was successful in doing an install with zero downtime for the plant. • Successfully purchased and launched equipment from global resources (Germany, Italy, France, US, Mexico) on multiple projects. • Successfully budgeted, specified, purchased and launched 3 new Cold End upgrades during major furnace rebuilds. • Worked outside area of expertise on various projects to improve plant facilities for conveyor installations. Example Seattle projects had to remove and pour new floor for equipment. Installed new roofing in refurbished furnace area and upgraded incoming service for Fairfield Warehouse. Show less
-
-
-
General Motors
-
United States
-
Motor Vehicle Manufacturing
-
700 & Above Employee
-
Senior Manufacturing Engineer
-
May 1997 - May 2007
Established common approaches for processes to conform into corporate controls standards. Was responsible for the design and testing of tooling, equipment and planning the manufacturing processes. Developed and installed tools, equipment and established a course of action to accomplish completion of each project. Analyzed product designs for best manufacturing methods; proposed and evaluated the processes for equipment in assigned area. Directed the design, development and improvement of manufacturing processes. Provided technical support for specific plant operations. Coordinated input from internal/external customers to better understand customer needs and/or perceptions. Remained abreast of current product developments and trends in areas of expertise. Actively identified new areas for learning and took advantage of learning opportunities. Directed the design, development and improvement of manufacturing process for an assigned area. Supported the purchase and installation of new equipment. Evaluated expenditures for processes and equipment. Provided technical assistance and training for assigned plant operations. Ensured lessons learned were analyzed and documented. Coordinated activities with other department's divisional offices and our customers. Ensured manufacturing had accurate and detailed information on specifications for production. Also successfully mentored interns and new hires. Show less
-
-
-
Ford Motor Company
-
United States
-
Motor Vehicle Manufacturing
-
700 & Above Employee
-
Summer Intern
-
May 1994 - Aug 1996
As a summer Intern I was exposed to multiple areas within the headliner manufacturing operation. From Engineering of new and CIP processes, to first line production and maintenance supervision. Witnesses firsthand what happens when a facility closes (Mt Clemens) as well as how to build relationships with unionized labor force. As a summer Intern I was exposed to multiple areas within the headliner manufacturing operation. From Engineering of new and CIP processes, to first line production and maintenance supervision. Witnesses firsthand what happens when a facility closes (Mt Clemens) as well as how to build relationships with unionized labor force.
-
-
-
US Navy
-
United States
-
Armed Forces
-
700 & Above Employee
-
AT 3 Aviation Electronics Technician
-
Aug 1987 - May 1993
As an AT3 I worked Intermediate Maintenance Level (AIMD) as a Sea Operations Detachment (SEAOPDET) where I was assigned to the USS Carl Vinson and USS Kitty Hawk. My role was to troubleshoot and repair offensive and defensive Electronic Countermeasure devices utilizing the Hybrid Test Station (HTS). I participated in Operation Desert Storm, and Somalia I was exposed to multiple areas within the headliner manufacturing operation. From Engineering of new and CIP processes, to first line production and maintenance supervision. Witnesses firsthand what happens when a facility closes (Mt Clemens) as well as how to build relationships with unionized labor force. Show less
-
-
Education
-
New York Institute of Technology
MBA, Management -
Purdue University
BS, Electrical Engineering Technology -
Blackford High School
Community
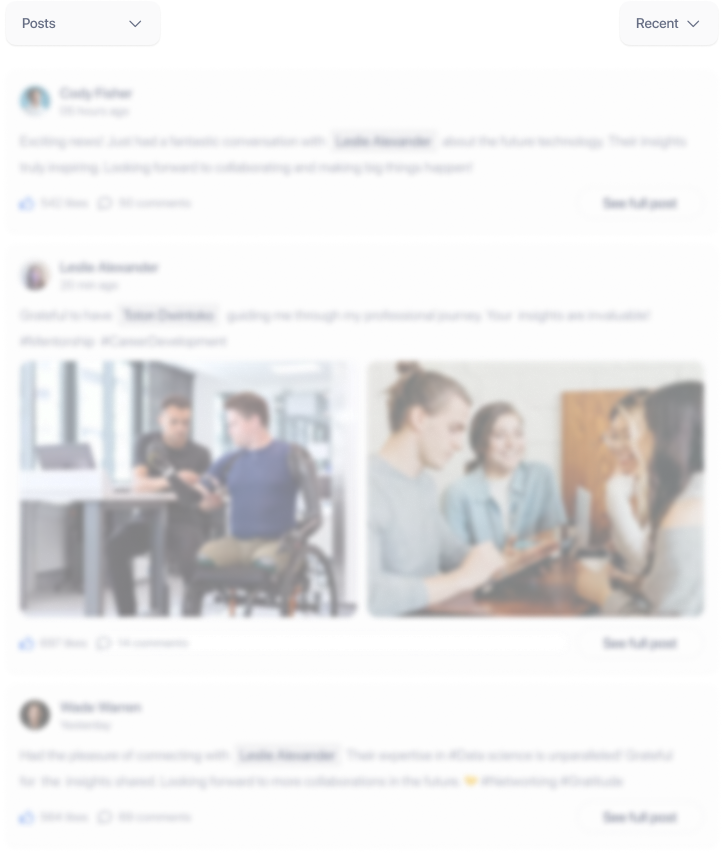