Doreen Herriman
Real Estate Agent at Platinum Real Estate Florida- Claim this Profile
Click to upgrade to our gold package
for the full feature experience.
Topline Score
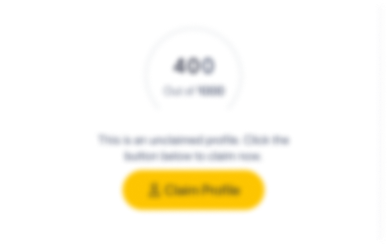
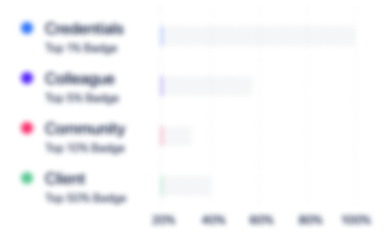
Bio


Experience
-
Platinum Real Estate Florida
-
United States
-
Real Estate
-
1 - 100 Employee
-
Real Estate Agent
-
Sep 2021 - Present
-
-
Real Estate Agent
-
Sep 2021 - Present
Marco Island, Florida
-
-
-
Mary Kay Cosmetics
-
Personal Care Product Manufacturing
-
700 & Above Employee
-
Sales Associate
-
Oct 2021 - Present
Marco Island, Florida
-
-
-
Premiere Plus Realty, Co.
-
United States
-
Real Estate
-
500 - 600 Employee
-
Real Estate Agent
-
Feb 2019 - Sep 2021
Marco Island, FL
-
-
-
Real Living John Burt Realty
-
Real Estate
-
1 - 100 Employee
-
Real Estate Agent
-
Jan 2017 - Sep 2021
Oxford, MI
-
-
-
-
Consultant
-
Aug 2016 - Dec 2020
-
-
-
Keller Williams Realty, Inc.
-
United States
-
Real Estate
-
700 & Above Employee
-
Real Estate Agent
-
Apr 2017 - Feb 2019
Marco Island, Florida
-
-
-
MPI PRODUCTS LLC
-
United States
-
Motor Vehicle Manufacturing
-
100 - 200 Employee
-
Senior Cost Estimator
-
Jan 2015 - Aug 2017
Rochester Hills, MI
-
-
-
Takata
-
United States
-
Motor Vehicle Manufacturing
-
700 & Above Employee
-
Senior Financial Analyst - Global Product Costing
-
Sep 2013 - Dec 2014
Auburn Hills, MI • Working in two person Product Costing Department, reduced past due quotes by 65%. • Participated in the development and roll-out of a new process flow for Product Costing Department that will remove ‘bottlenecks’ and increase productivity. • Develop quotes using data received from various departments including Purchasing and Plant. • Reviewed and analyzed quote data received from all departments to ensure their accuracy. • Support engineers when analysis of developed product cost… Show more • Working in two person Product Costing Department, reduced past due quotes by 65%. • Participated in the development and roll-out of a new process flow for Product Costing Department that will remove ‘bottlenecks’ and increase productivity. • Develop quotes using data received from various departments including Purchasing and Plant. • Reviewed and analyzed quote data received from all departments to ensure their accuracy. • Support engineers when analysis of developed product cost is required. • Proficient in understanding drawings and bill of materials received for each project. • Travel to manufacturing facilities to learn the manufacturing process and apply to costing. • Working with management and estimators at German headquarters to develop and roll-out a new cost estimating template. Show less
-
-
-
Alvarez & Marsal
-
United States
-
Business Consulting and Services
-
700 & Above Employee
-
Consultant
-
Oct 2009 - Sep 2013
• Work with counsel to prepare exhibits for objections to be filed with the court. • Prepare Preference reports • Triage claims to determine validity and when valid; categorize • Work with counsel, upper management and team to complete projects by deadlines set forth by the courts. • Participated in month long preparation of approximately $14 billion distribution. • Instrumental in developing new processes within our specialized database to improve process flow and accuracy.
-
-
-
-
Independent Contractor
-
Dec 2008 - Oct 2009
Worked with various corporations applying my skills as an administrative assistant, cost estimator and quality analyst to meet their needs and requirements. • Designed, developed and implemented a cost estimating program. • Cost estimating and cost analysis responsibilities. • Various accounting and administrative duties.
-
-
-
-
Cost Estimator
-
Oct 2007 - Dec 2008
Edscha is a Tier 1 supplier of door hinges, door checks, and hood hinges to the automotive industry. My role as part of the cost estimating team was to develop costs based on accurate data obtained from supplier and manufacturing divisions. Responsibilities: • Organize the cost estimating process to ensure customer requirements are met. • Collaborate with purchasing, engineering, sales, manufacturing facilities and management to develop accurate cost estimates. • Travel… Show more Edscha is a Tier 1 supplier of door hinges, door checks, and hood hinges to the automotive industry. My role as part of the cost estimating team was to develop costs based on accurate data obtained from supplier and manufacturing divisions. Responsibilities: • Organize the cost estimating process to ensure customer requirements are met. • Collaborate with purchasing, engineering, sales, manufacturing facilities and management to develop accurate cost estimates. • Travel to Edscha manufacturing facilities and suppliers to learn their capabilities and restrictions. • Review and analyze supplier quotes. Choose supplier based on criteria such as price, quality history, and meeting all print and customer requirements. • Manufacturing capacity analysis of each manufacturing facility and available equipment. • Review cost breakdown and present to management. Show less
-
-
-
-
Cost Estimator / TS Management Rep
-
1990 - 2007
MPI International, Inc. is the largest fineblanking organization in North America. They are a Tier 1 supplier of transmission parts, latches, core plates and other fineblanked parts. Cost Estimating Responsibilities: • Use AutoCAD to develop the optimal strip layout for estimating purposes. • Successfully handled and organized the cost estimating process from receipt of customer RFQ, developing manufacturing process, developing cost estimate and submitting completed quotation to… Show more MPI International, Inc. is the largest fineblanking organization in North America. They are a Tier 1 supplier of transmission parts, latches, core plates and other fineblanked parts. Cost Estimating Responsibilities: • Use AutoCAD to develop the optimal strip layout for estimating purposes. • Successfully handled and organized the cost estimating process from receipt of customer RFQ, developing manufacturing process, developing cost estimate and submitting completed quotation to the customer. • Conferred with engineers and management to develop manufacturing process. • Submitted customer quotes using customer specific internet websites and customer specific breakdown forms. • Assisted in the design and implementation of in-house cot estimating program. • Developed training manuals and travel to divisions to train users on the use of the cost estimating program. • Trained on customer specific websites, including Chrysler and Ford Motor Company. • Traveled to Switzerland for extensive Fineblanking training. Quality Management Representative Responsibilities: • Responsible for obtaining and maintaining TS 16949 Quality Certification and Corporate Headquarters. • Traveled to manufacturing divisions as the Corporate Management Representative to audit their quality system and participate in their third party audits. • Developed and implemented a quality system at a ‘start-up’ division, including procedures, work instructions, training and audit preparation. • Studied methods of improving work measurements and performance standards. • Studied management methods in order to improve workflow, simplify reporting procedures and implement cost reductions. • Aided executive and sales staff by coordinating office services using all Microsoft applications. • Instrumental in the development and completion of special projects. Show less
-
-
Education
-
GE Corporate
Six Sigma Green Belt Trained -
QAI
ISO/TS 16949:2002 Quality Lead Auditor Training -
Davenport University
Bachelors, Business Administration -
Walsh College of Accountancy and Business Administration
Masters Program, Finance
Community
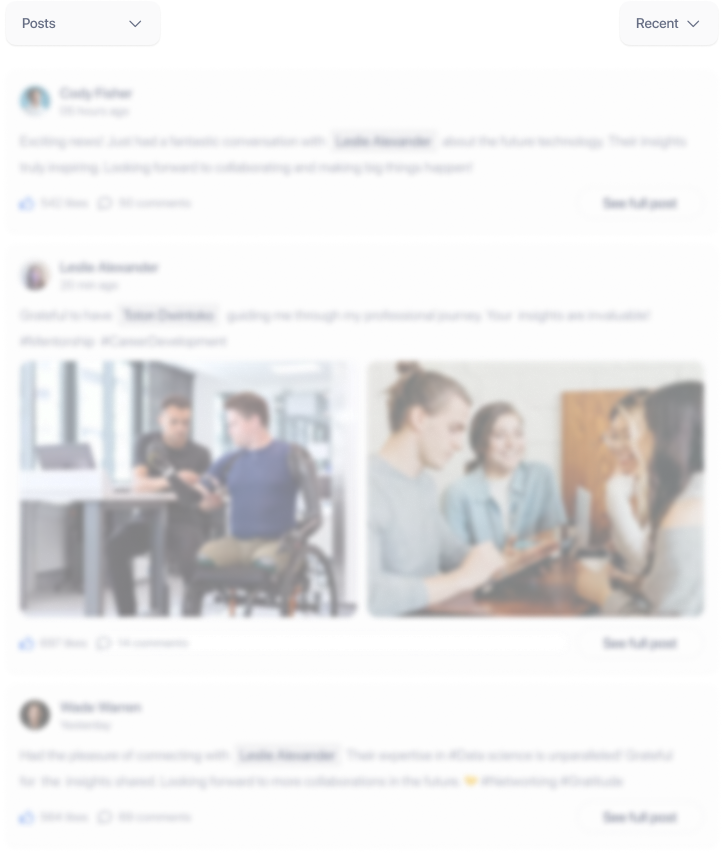