Donna Field
Quality Engineer at Valley Services Electronics- Claim this Profile
Click to upgrade to our gold package
for the full feature experience.
Topline Score
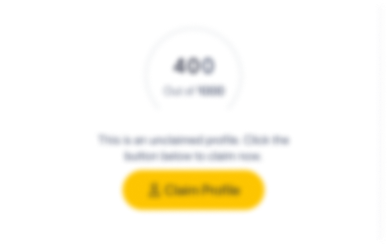
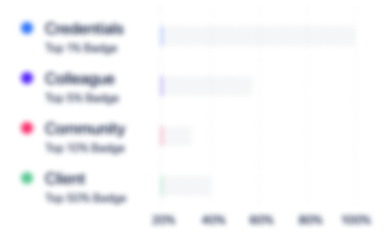
Bio

Aqeel Ahmed
Donna is very detailed oriented person. She manages her priorities in timely manner. She is a good team player and uses problem solving techniques effectively.

Diane Graham
- Follows procedures and is well versed in company documentation - Shows up and is prepared - Willing to learn new skills, tackle new tasks - Personable, well groomed and punctual

Aqeel Ahmed
Donna is very detailed oriented person. She manages her priorities in timely manner. She is a good team player and uses problem solving techniques effectively.

Diane Graham
- Follows procedures and is well versed in company documentation - Shows up and is prepared - Willing to learn new skills, tackle new tasks - Personable, well groomed and punctual

Aqeel Ahmed
Donna is very detailed oriented person. She manages her priorities in timely manner. She is a good team player and uses problem solving techniques effectively.

Diane Graham
- Follows procedures and is well versed in company documentation - Shows up and is prepared - Willing to learn new skills, tackle new tasks - Personable, well groomed and punctual

Aqeel Ahmed
Donna is very detailed oriented person. She manages her priorities in timely manner. She is a good team player and uses problem solving techniques effectively.

Diane Graham
- Follows procedures and is well versed in company documentation - Shows up and is prepared - Willing to learn new skills, tackle new tasks - Personable, well groomed and punctual

Experience
-
Valley Services Electronics (VSE)
-
United States
-
Appliances, Electrical, and Electronics Manufacturing
-
1 - 100 Employee
-
Quality Engineer
-
Aug 2020 - Present
• Provide QA Engineering support activities of inspection and quality assurance; including receiving inspection, cabling, components, and electro-mechanical assembly in an IPC-A-610 environment • Facilitation and monitoring of activities in areas related to Product defects, Supplier returns, Supplier Corrective Action Requests, First Articles, FAIR, NCMR, MRB, Calibration, and Customer Clarification Requests • Provide QA Engineering support activities of inspection and quality assurance; including receiving inspection, cabling, components, and electro-mechanical assembly in an IPC-A-610 environment • Facilitation and monitoring of activities in areas related to Product defects, Supplier returns, Supplier Corrective Action Requests, First Articles, FAIR, NCMR, MRB, Calibration, and Customer Clarification Requests
-
-
-
General Electronics Assembly
-
United States
-
Appliances, Electrical, and Electronics Manufacturing
-
Quality Manager
-
Dec 2010 - Jun 2020
Maintain certifications for ISO 9001 as Management Representative and Conduct ISO audits Certified to IPC-A-610, IPC-A-620 & J-STD-001 Provide customer support for different quality aspects as well as provide monthly reports to measure Customer's satisfaction, On Time Delivery, Vendor Performance, and Acceptance rate. Analyze and recommend corrective actions, using CAPA system for customer complaints, process control and continual improvement programs Manage tool calibration, equipment preventive maintenance, ESD, environmental health & safety, hazardous materials, employee training, and document control programs Provide value add process improvements in the workplace, strengthening the entire organization QMS Manager Responsibilities: -Conduct QMS process audits and training throughout the company. -Manage and prepare for internal and external audits including interface with registrar. -Identify systemic issues, risks and negative trends. -Manage and drive Corrective and Preventive action process -Prepare for annual ISO management review meetings and track actions to closure. -Manage ISO9001 compliance projects. -Generate or update written business process and procedures to support the QMS. -Lead process re-engineering where needed. -Assist with implementation and maintenance of QMS
-
-
-
Optitech Solutions
-
Santa Clara CA
-
Quality Systems Manager-ISO Implementation -Part Time
-
Dec 2013 - Mar 2014
Part time position while working current full time job at General Electronics Assembly. Work with QAS International to obtain ISO9001:2008 Certification Help to Implement Quality Management System into the Business Process Set up Quality System documentation and implement internal processes for a small company in preparation for ISO Part time position while working current full time job at General Electronics Assembly. Work with QAS International to obtain ISO9001:2008 Certification Help to Implement Quality Management System into the Business Process Set up Quality System documentation and implement internal processes for a small company in preparation for ISO
-
-
-
Samax Precision Inc.
-
United States
-
Machinery Manufacturing
-
1 - 100 Employee
-
Quality Coordinator
-
Sep 2010 - Nov 2010
• Assist the Quality Manager with record Keeping • Conduct Internal Audits per quality system assessment schedule • AS 9100B, ISO 13485 and ISO 9001:2008 • Coordinate Supplier Assessment Surveys, Non Disclosure Agreements and ensure timely closure • Supplier Performance reporting on Acceptance rate and on-time delivery • Assist the Quality Manager with record Keeping • Conduct Internal Audits per quality system assessment schedule • AS 9100B, ISO 13485 and ISO 9001:2008 • Coordinate Supplier Assessment Surveys, Non Disclosure Agreements and ensure timely closure • Supplier Performance reporting on Acceptance rate and on-time delivery
-
-
-
i2a Technologies
-
Fremont CA
-
QA Manager (Contractor)
-
May 2010 - Sep 2010
• Develop, implement, communicate, and maintain the company’s quality systems, policies and procedures • Led the ISO 9001:2008 recertification efforts including but not limited to; review, revise, and implementation of document control procedures, and maintenance of existing specifications • Customer Complaints, Surveys, Preventive Maintenance, Calibration, Corrective Actions, and RMA • Conduct internal audits within determined time-line • Develop, implement, communicate, and maintain the company’s quality systems, policies and procedures • Led the ISO 9001:2008 recertification efforts including but not limited to; review, revise, and implementation of document control procedures, and maintenance of existing specifications • Customer Complaints, Surveys, Preventive Maintenance, Calibration, Corrective Actions, and RMA • Conduct internal audits within determined time-line
-
-
-
Jabil
-
United States
-
Appliances, Electrical, and Electronics Manufacturing
-
700 & Above Employee
-
Project Quality / Supplier Quality Engineer
-
Jun 2006 - Oct 2008
• Coordinated customer failure analysis with responsible product and factory engineering groups • Maintained Quality System requirements such as CAPAs, Supplier Audits, Failure Analysis, and quality metrics • Worked with Process Engineering for corrective action of customer compliance issues and provided follow up • Conducted investigative work to solve, resolve and proactively disposition quality related problems • Developed supplier evaluation calendar and conduct quarterly supplier surveys/follow up/ verification audits • Issued, reviewed, and analyzed corrective action reports in an effort to reduce and eliminate defects • Drove timely updates of corrective action reports from supply base • Followed ISO 9001 processes and ensured internal compliance of processes. • Reviewed and evaluated monthly site metrics of receiving inspection, MRB and SCAR database • Managed PCN Notification process, work with component engineers, buyers, and provide timely customer feedback
-
-
-
Brocade
-
United States
-
Computer Networking Products
-
700 & Above Employee
-
Data Integrity Analyst / Environmental Compliance (Contractor)
-
Jul 2005 - Jun 2006
• Scrubbed sustaining and new product introduction BOM to meet RoHS requirements • Managed the implementation process, coordinated RoHS transition activities and interaction between component manufacturer, Subcontractor, and Supplier • Teamed with component engineer, supply base managers to drive gap closure on Certificates of Compliance • Validated manufacturer identity on components; worked with Component Eng and Doc Services to create ECO and MCO as needed • Scrubbed sustaining and new product introduction BOM to meet RoHS requirements • Managed the implementation process, coordinated RoHS transition activities and interaction between component manufacturer, Subcontractor, and Supplier • Teamed with component engineer, supply base managers to drive gap closure on Certificates of Compliance • Validated manufacturer identity on components; worked with Component Eng and Doc Services to create ECO and MCO as needed
-
-
-
Cisco
-
United States
-
Software Development
-
700 & Above Employee
-
Program Manager- Supply Chain Architecture (Contractor)
-
Jan 2005 - Jul 2005
• Managed and reviewed supply chain business continuity and disaster recovery plans that span multiple suppliers, locations, and cross functional teams • Managed manufacturing risk assessments for all CM, CS, CSO, and SLC impacting production, Teamed with Commodity Managers and Suppliers to drive completion of plans • Managed and reviewed supply chain business continuity and disaster recovery plans that span multiple suppliers, locations, and cross functional teams • Managed manufacturing risk assessments for all CM, CS, CSO, and SLC impacting production, Teamed with Commodity Managers and Suppliers to drive completion of plans
-
-
-
National Semiconductor
-
Semiconductor Manufacturing
-
400 - 500 Employee
-
Quality Assurance Program Manager (Contractor)
-
Jan 2004 - Jan 2005
• Managed Subcontractor certification and assessments process via (ASL) Approved Supplier List; Support Test and Package processing at local subcontractor; present data at monthly meetings and drove completion of action items • Teamed with Reliability Engineering to develop RoHS Database (Restrictions on Hazardous Substance) to display compliance on the Web • Diligently work with suppliers and subcontractors to collect ICP data, ensured integrity and closed all gaps in process. Helped ensure suppliers ISO certifications are all up to date and provided follow through
-
-
-
Maxtor
-
Computer Hardware Manufacturing
-
1 - 100 Employee
-
Program Coordinator - Supplier Quality Engineering
-
Jan 2000 - Jan 2002
• Reduced new product launch time by working closely with internal / external commodity teams • Revised design and development plans, and provided top level exposure reports to ensure consistency between locations • Reduced new product launch time by working closely with internal / external commodity teams • Revised design and development plans, and provided top level exposure reports to ensure consistency between locations
-
-
-
Seagate Technology
-
United States
-
Computer Hardware Manufacturing
-
700 & Above Employee
-
Quality System Admin/ Quality & Reliability Engineering
-
Jan 1998 - Jan 2000
• Managed the Quality System by performing and supporting the following activities: • Developed a new quality system that increased efficiency by 50% and reduced corrective tracking from 365 to 90 days • Maintained CAPA Corrective / Preventive Action system and tracked issues to closure with persistence using root cause analysis • Worked with our vendor Agilent, for calibration of equipment to verify accuracy of calibration • Led ISO Steering Committee meetings, provided a mechanism to communicate issues to management for clarification and actions, which led to an improved quality system, coordinated and facilitated internal and • external audit system; led internal auditors, demonstrated strong leadership skills and ability to communicate in a team setting • Implemented ISO and QSR system into the organization by developing a systematic way of using resources and orchestrating 20 people; summarized monthly quality system data through graphs, and charts for senior level management review meetings • Consistently promoted quality awareness throughout the organization
-
-
-
SSL
-
United States
-
Defense and Space Manufacturing
-
700 & Above Employee
-
Audit Coordinator/ Inspector/ Quality Assurance Auditor/ Engineer
-
Jan 1991 - Jan 1998
• Coordinated and scheduled Quality Assurance Audit activities in preparation for ISO 9001 implementation similar to ISO13485 • Perform Particle Counts in the clean room and maintain clean room to standards • Documented protocols, processes and clean room certifications • Conducted Internal Audits throughout all phases of the manufacturing process, ensuring compliance to policies and procedures and assisting in implementation and closure of corrective actions • ISO 9001 Internal Auditor, Operations level statistical process control, hazardous materials • Performed in-depth audits and prepared reports for all major spacecraft and space systems programs/document results for management reviews and customer awareness (Intelsat VII, GOES, Space Station) Interface and work with DCMA staff • Provided in process, final and audit inspection tasks, including floor surveillance of in process assembly / test requirements for satellite subsystems and ground support equipment • Provided close proactive support to spacecraft manufacturing / test areas in order to rapidly recognize Quality problems, identified their causes and assisted in the implementation of appropriate corrective actions • Surveillance, verification, and monitoring of equipment calibrations, clean room environments, vibration, thermal test, hardware torque, crimp, bond pull, flatness, weight, humidity, area classifications, solder bath, freezer & oven temperature, and material mix • Certified in NASA hand soldering, cable crimp & harness, Electro Static Discharge (ESD) and Contamination Control As an Inspector / Auditor in the Aerospace industry, I covered tasks associated in multiple departments such as MUX (RF), Digital, Solar Arrays, Power Assemblies, Thermal, Propulsion, vibration, Machine shop, composites, and Hi-Bay final Assembly (final spacecraft installation and testing). This included inspection of components at the microscopic level, including soldering installation
-
-
-
KLA
-
United States
-
Semiconductor Manufacturing
-
700 & Above Employee
-
Quality Control Inspector/ Mechanical Assembler
-
Jan 1982 - Jan 1990
• Assembled, soldered, inspected, and verified all in-process and final assemblies. • Source inspection off site at vendors – cables, paint and mechanical cabinets. • Developed procedures and checklists to improve processes and product. Use of schematics, drawings, calipers, micrometers, test fixtures, and a variety of different hand tools. • Assembled, soldered, inspected, and verified all in-process and final assemblies. • Source inspection off site at vendors – cables, paint and mechanical cabinets. • Developed procedures and checklists to improve processes and product. Use of schematics, drawings, calipers, micrometers, test fixtures, and a variety of different hand tools.
-
-
Education
-
Foothill College
Community
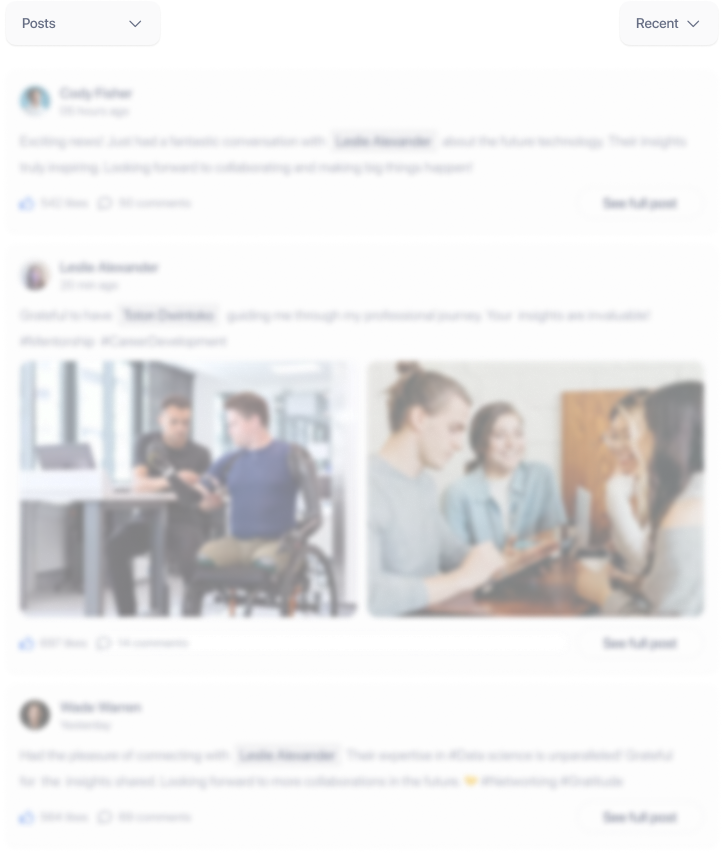