Donald Lockhart
Maintenance Leader at AGY- Claim this Profile
Click to upgrade to our gold package
for the full feature experience.
Topline Score
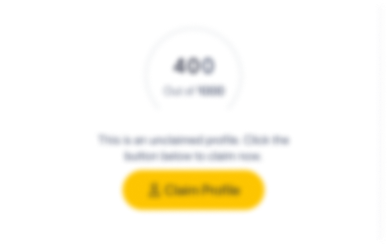
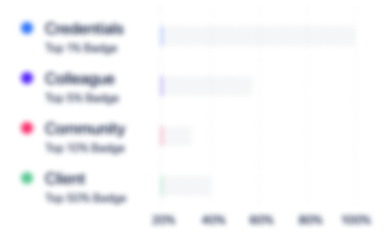
Bio

David Coleman
Don is a highly effective, and detail oriented manager. During my time working for him, I can safely say that he always had his plate double full, but still managed to give 110% attention to each and every issue that faced him. Additionally, his office door was always open to his employees, and he never failed to give any employee consideration in personal matters when it really was important. I have worked for many people since my time with TI, but I would like to say that of all my managers, Don was not just my boss, but also a good friend, and I miss working for him daily.

Susan Tinkham, SPHR
I worked with Don at Allied Air Enterprises, and I highly recommend him for an Operations Manager/Plant Manager role. Don and I worked together on a variety of team-based projects regarding involving front line supervison and hourly employees. Don is outstanding at balancing the needs of the company with the needs of the individuals. One of Don's strong points is the ability to quickly gain the trust and respect of those working for him. People are eager to share ideas, opinions and information with him. This allows him to effectively utilize people based on their skills, abilities and interests. If you're looking for a strong leader that can quickly motivate a culture change in your organization, Don is exceptionally suited for the challenge! Susan Tinkham, SPHR

David Coleman
Don is a highly effective, and detail oriented manager. During my time working for him, I can safely say that he always had his plate double full, but still managed to give 110% attention to each and every issue that faced him. Additionally, his office door was always open to his employees, and he never failed to give any employee consideration in personal matters when it really was important. I have worked for many people since my time with TI, but I would like to say that of all my managers, Don was not just my boss, but also a good friend, and I miss working for him daily.

Susan Tinkham, SPHR
I worked with Don at Allied Air Enterprises, and I highly recommend him for an Operations Manager/Plant Manager role. Don and I worked together on a variety of team-based projects regarding involving front line supervison and hourly employees. Don is outstanding at balancing the needs of the company with the needs of the individuals. One of Don's strong points is the ability to quickly gain the trust and respect of those working for him. People are eager to share ideas, opinions and information with him. This allows him to effectively utilize people based on their skills, abilities and interests. If you're looking for a strong leader that can quickly motivate a culture change in your organization, Don is exceptionally suited for the challenge! Susan Tinkham, SPHR

David Coleman
Don is a highly effective, and detail oriented manager. During my time working for him, I can safely say that he always had his plate double full, but still managed to give 110% attention to each and every issue that faced him. Additionally, his office door was always open to his employees, and he never failed to give any employee consideration in personal matters when it really was important. I have worked for many people since my time with TI, but I would like to say that of all my managers, Don was not just my boss, but also a good friend, and I miss working for him daily.

Susan Tinkham, SPHR
I worked with Don at Allied Air Enterprises, and I highly recommend him for an Operations Manager/Plant Manager role. Don and I worked together on a variety of team-based projects regarding involving front line supervison and hourly employees. Don is outstanding at balancing the needs of the company with the needs of the individuals. One of Don's strong points is the ability to quickly gain the trust and respect of those working for him. People are eager to share ideas, opinions and information with him. This allows him to effectively utilize people based on their skills, abilities and interests. If you're looking for a strong leader that can quickly motivate a culture change in your organization, Don is exceptionally suited for the challenge! Susan Tinkham, SPHR

David Coleman
Don is a highly effective, and detail oriented manager. During my time working for him, I can safely say that he always had his plate double full, but still managed to give 110% attention to each and every issue that faced him. Additionally, his office door was always open to his employees, and he never failed to give any employee consideration in personal matters when it really was important. I have worked for many people since my time with TI, but I would like to say that of all my managers, Don was not just my boss, but also a good friend, and I miss working for him daily.

Susan Tinkham, SPHR
I worked with Don at Allied Air Enterprises, and I highly recommend him for an Operations Manager/Plant Manager role. Don and I worked together on a variety of team-based projects regarding involving front line supervison and hourly employees. Don is outstanding at balancing the needs of the company with the needs of the individuals. One of Don's strong points is the ability to quickly gain the trust and respect of those working for him. People are eager to share ideas, opinions and information with him. This allows him to effectively utilize people based on their skills, abilities and interests. If you're looking for a strong leader that can quickly motivate a culture change in your organization, Don is exceptionally suited for the challenge! Susan Tinkham, SPHR

Experience
-
AGY
-
United States
-
Glass, Ceramics and Concrete Manufacturing
-
100 - 200 Employee
-
Maintenance Leader
-
Jul 2016 - Present
-
-
-
-
Maintenance Manager
-
Aug 2015 - Jul 2016
-
-
-
Owens Corning
-
United States
-
Wholesale Building Materials
-
700 & Above Employee
-
Operations Leader, Maintenace Leader, Engineer, Production Supervisor
-
Aug 2010 - Jul 2015
Manage the plant operations across three major production areas, responsible for meeting all KPI’s to include safety, quality, schedule attainment, first pass yield, machine operating efficiencies, manufacturing gain loss and employee engagement. This is a 24/7 continuous flow process, primary product produced is a fiberglass mat that is used in the building materials and carpet manufacturing sector. • Fostered a “Safety First" culture, by establishing and enforcing expectations for a safe and clean working environment, developing safe work procedures and task risk analysis. • Implemented a business unit model in each of the 3 production lines, utilizing a managing for daily improvement concept with the metric’s that has driven all deliverables in a positive direction. • Lead a critical line capacity increase team to meet the challenges of a 67% increase in customer demand, which pushed the line to be over sold by 30% of it demonstrated capacity. Used many lean tools to identified and eliminate bottlenecks, determined cause, implement change to line operation, scheduling, and make process improvements. Within eight months the line was capable of supplying the increased demand. • Supported the very successful launch of three new products, gaining new markets and customers. • Developed strategic plans with meaningful goals and metrics that engages and maximizes team performance. • Established a work environment characterized by mutual trust and respect, open and honest communications, and teamwork. • Maximized the effectiveness of maintenance systems through the implementation of Reliability Work Process (RWP). • Administered the plant's capital plan and built the long term capital strategy. • Developed and maintained outstanding employee relations in a union environment. • Continually improving reliability centered maintenance systems. • Introduced “Plant Floor Basic Equipment Care” and Single Minute Exchange of Dies (SMED). Show less
-
-
-
-
Operations/Production Manager
-
Jul 2003 - Jan 2010
Report to the plant manager. Responsible for all production, and maintenance departments. Responsibilities include overall plant performance, employee relations, capital and expense budgeting. Allied Air is a division of Lennox International a leading manufacturer of residential and commercial HVAC system. Increased the focus on root cause analysis through data collection making improvements in downtime reduction through predictive and preventative maintenance of critical assembly and facilities equipment. Developed and implemented a continuous training plan for supervisory and lead personnel providing the business with a professional staff capable and willing to implement the needed improvements. Through the use of a Lean team and Production Support teams began the lean journey using many lean tools, including value stream mapping, Kanban, visual factory, supermarkets, major Kaizen events and Point Kaizens. Continuously improved key production indicators like: delivery, scrap, 1st pass yield, and production output and absorption levels through the use of Managing for Daily Improvement (MDI) boards Show less
-
-
-
TI Automotive
-
United States
-
Motor Vehicle Manufacturing
-
700 & Above Employee
-
Technical Services Manager
-
Jan 1999 - Jul 2004
Responsible for Equipment/ Facilities maintenance and Controls Engineering departments. Responsibilities included downtime reduction, supporting Lean improvement efforts, development of cross-functional teams to maximize responsiveness and utilization of the production capabilities.
-
-
Technical/Maintenance Manager, Area Manager, Production Supervisor
-
Jan 1999 - Jan 2003
Reported to the plant manager. Responsible for Equipment maintenance, Facilities maintenance and Controls Engineering departments. Responsibilities included downtime reduction, production performance improvement, employee relations, capital and expense budgeting. TI Automotive is a tier 1 and 2 supplier of fuel delivery systems to the automotive industry. Successfully managed diverse departments with five distinct skill sets. Gaining a thorough knowledge and understanding of manufacturing techniques, facility management, controls engineering and human relations in a UAW environment. Lead a team of managers through the plant consolidation eliminating the need for an 115,000-sq. ft. building while maintaining full production for the customers and minimizing the impact on the work force.Trained the work force and lead Total Productive Maintenance (TPM) implementation throughout the plant. Developed and headed the implementation of an Environmental Management System (ISO 14001), achieving certification within eight months. Reduced equipment downtime 65% with the use of data collection, root cause analysis, aggressive preventative and predictive maintenance systems, training and team building. As a production supervisor increased the quality and output of product with the use of lean principles and various tools. Show less
-
-
-
US Navy
-
United States
-
Armed Forces
-
700 & Above Employee
-
Senior Chief Sonar Technician Submarines
-
Nov 1976 - Jan 1999
Manager, leader, instructor, supervisor, technician, student, operator
-
-
Manager, Supervisor, Technician, Instructor
-
Jan 1976 - Jan 1999
The U.S. Submarine Force is an elite group of dedicated, highly trained individuals that understand and embrace the concept of teamwork, with limited resources each member of the team must be able to perform multiple tasks in order for the mission/goal to be accomplished. Management & Supervisory Oversaw the operation of 200 personnel in the daily instruction and training of the operation, maintenance, repair, calibration, of electronic equipment for four years. Directed the maintenance and operation of submarine sonar systems and associated subsystems for 7 years with minimal system downtime and optimal system performance. Trained and experienced in the operation, maintenance and repair of three major sonar systems, including but not limited to processors, analog displays, high speed data converters, power supplies and system communication networks. Qualified "Master Groom Specialist", technical expert on AN/BQQ-5 and AN/BSY-1 systems. Coordinated all facets of a sonar system calibration on eleven submarines: logistic support, troubleshooting, repair, data gathering, report publication and system certification. Designed a preventive maintenance schedule used as the baseline for all submarines with that installed system. Instructor / Curriculum Developer Taught two electronic maintenance courses and four operator / supervisory courses of instruction. U.S. Navy's representative to Interactive Courseware Design Board; made positive changes that were incorporated into both shore based and fleet-wide training programs. Conducted successful pilot course of the AN/BQQ-5E Maintenance Conversion Course as CourseMonitor/Chairperson, meeting or exceeding the requirements as set by higher authority.Developed mode flow diagrams for sonar employment used by maintenance technicians on all AN/BSY-1 equipped submarines. Show less
-
-
Education
-
US Navy
Technical, Electronics -
Bacon Academy
High School -
Aiken Technical College
Electrical and Electronics Engineering, 3.8 -
Ford's training institute. US Military
Community
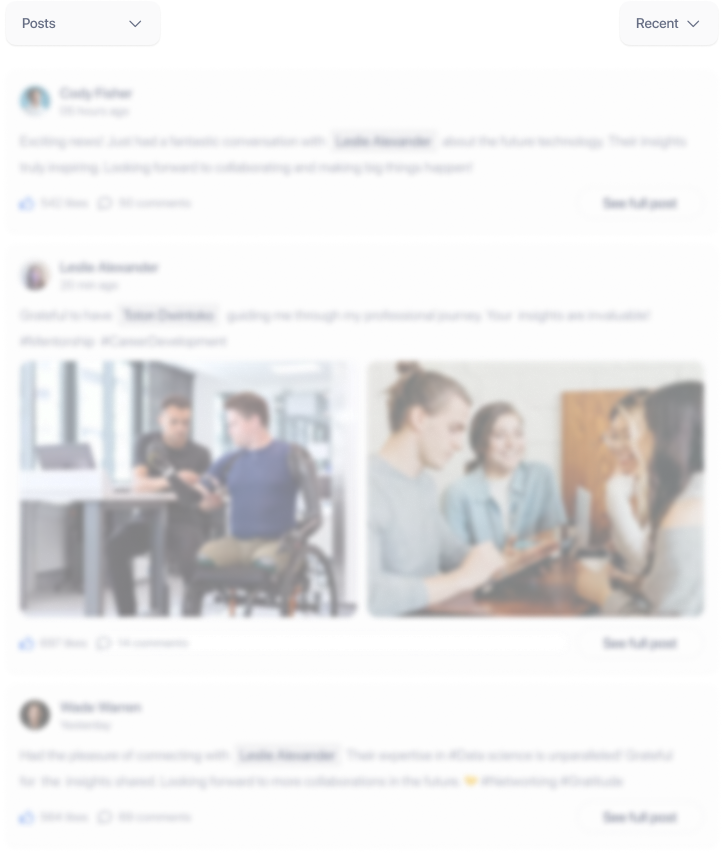