Don Petty
Director of Production at AHT COOLING SYSTEMS GMBH- Claim this Profile
Click to upgrade to our gold package
for the full feature experience.
Topline Score
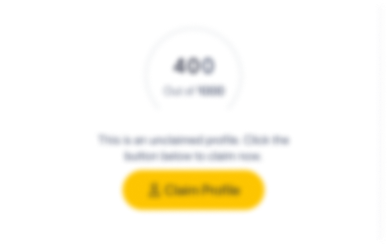
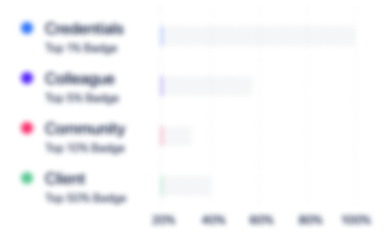
Bio


Experience
-
AHT Cooling Systems GmbH
-
Austria
-
Appliances, Electrical, and Electronics Manufacturing
-
200 - 300 Employee
-
Director of Production
-
Feb 2017 - Present
As the Director of Operations at AHT Cooling I am responsible for designing, directing, and implementing streamlined process, procedures, local R&D, facilities and product transfer plans for the company while building a strong team applying appropriate standards to maintain compliance with ETL / UL, OSHA, and ISO standards. Responsible for the development and implementation of first AHT North American production system. Establishing the production / logistic strategy to support company growth, the development of a strong empowered team, and expected performance results. AHT Cooling Systems is a Member of the Daikin Group and a leading global manufacturer of industrial refrigeration and deep freezers. The primary areas of business are refrigeration and deep freezers for supermarkets, ice cream freezers, and drink cooling. AHT takes quality seriously with ISO 9001 and ISO 14001 standards as the cornerstone of the quality system, this ensures superior quality of all products. Show less
-
-
-
Stryker
-
United States
-
Medical Equipment Manufacturing
-
700 & Above Employee
-
Sr. Manager, Continuous Improvement and Operations
-
Jan 2014 - Feb 2017
Site lead for acquisition integration, manufacturing transfer and site consolidation project . Reduced costs >3% annually while the top line grew >11% annually and maintained high quality levels. Coordinated continuous improvement and best practice initiatives involving US and international (Germany) sites on global and domestic process improvements and harmonization for both products and processes. Maintain appropriate product availability levels and first pass yields while increasing capacity, thus ensuring no customer interruption during the integration and transfer projects. Develop and present communication and engagement plans to all levels of the organization. Set overall operations strategy and targets for the Charleston manufacturing site to attain alignment with other sites in the network on corporate goals and strategies. Show less
-
-
Production Manager
-
Oct 2003 - Jan 2014
• Developed, implemented, and monitored management operations systems.• Transferred or established numerous products and assembly lines for domestic NPD or transfers from Europe.• Established an agile, cost effective approach to support a high mix / low volume assembly process for customer configured products with quality and safety as foundational principals.• Streamlined assembly process by utilizing Lean Manufacturing and Visual Management tools, while improving throughput and quality by establishing standard process and redeploying the quality team.• Coordinated various continuous improvement actives at all levels of the business involving varying skilled levels (Operations, Sales, Service, Project Mgt, Executives, etc...). • Operations lead in the implantation of a new ERP system (SAP), which allowed me to become a power user of the system.• Responsible for all facilities actives including maintenance, safety, and security. • Responsible for an annual operations budget >$32 million, and $1 million facilities budget. Show less
-
-
Field Service Technician
-
Jan 2001 - Oct 2003
• Project managed and completed various hospital installation, renovations, PM and repair schedules.• Operated as an independent agent under corporate guidelines and direction for a territory ≈ 300-mile radius.• Responsible for a regional budget, managing all fixed costs at job sites.• Sold product upgrades and service contracts to drive increased revenue in region.• Serviced, trouble shoot, repaired, and installed electromechanical capital medical equipment at customer facility. • Maintained a superior customer service rating• Assist other regions as required to solve complex service issue and support large installation projects Show less
-
-
Shop Supervisor
-
Jan 1992 - Jan 2001
• Supervised up to 18 employees in the assembly of electrical / mechanical medical equipment.• Worked in an integral role with IT on an ERP system implementation (Mapics software) by setting up material master information, BOMs and establishing a physical kanban inventory control system based on the Toyota just-in-time technique.• Oversaw the construction of the first USA based operations and two site expansions, each budget >$1.5 million.• Increased production capabilities to support and average growth rate of 19% annually.• Played a key role in transferring an acquired product line from Sweden to the USA and Germany sites. Show less
-
-
-
IDEA OF CHARLESTON, INC.
-
North Charleston SC
-
Machinist Apprentice
-
Aug 1990 - Jan 1992
• Setup and operated milling, turning, and grinding machines per engineering drawings • Preformed welding and cutting tasks on a limited basics • Read various drawings to layout material for machining and fabrication work • Setup and operated milling, turning, and grinding machines per engineering drawings • Preformed welding and cutting tasks on a limited basics • Read various drawings to layout material for machining and fabrication work
-
-
Education
-
Charleston Southern University
Bachelor of Science (BS), Organizational Management -
Trident Technical College
Machine Tool Program, Machine Tool Technology/Machinist
Community
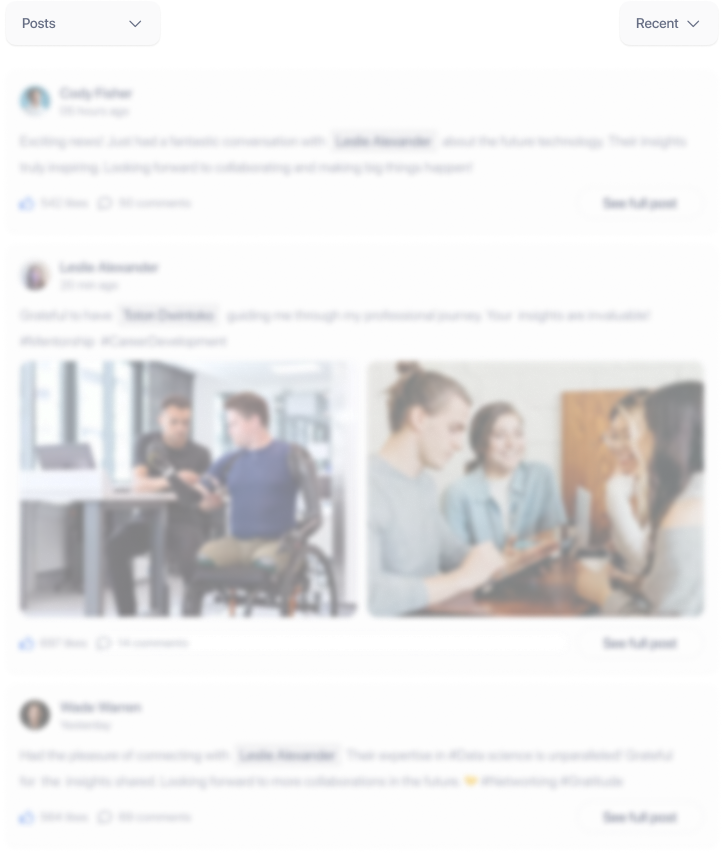